Characteristics, varieties and applications of blind rivets
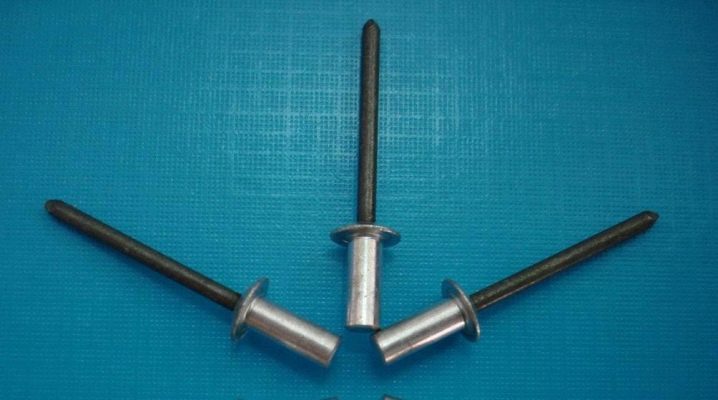
Blind rivets are a fairly common fastening material and are widely used in many areas of human activity. Details have replaced outdated riveting methods and have become a part of everyday life.
Appointment
Blind rivets are used to connect sheet material and require access to the working surface only from one side. This is one of their main differences from traditional "hammer" models. Mounting of rivets is carried out in a drilled hole using a special tool, which can be either manual or pneumo-electric. Connections made with blind rivets are very strong and durable. In addition, the parts are easy to install and are highly resistant to aggressive chemicals, high temperatures and humidity.
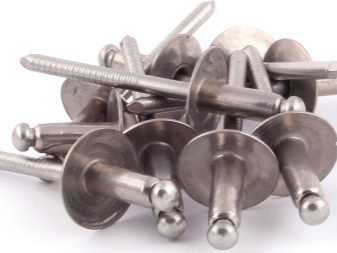
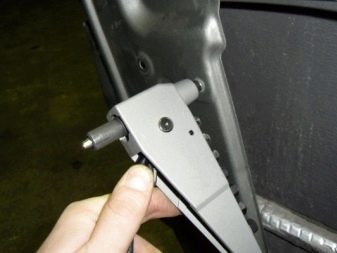
Due to their versatility and reliability, the scope of application of blind rivets is quite extensive. Parts are actively used in shipbuilding, aircraft and mechanical engineering, textile industry and construction. When working on hazardous objects, rivets act as an alternative to welding joints. In addition, rivets are widely used in the repair of parts and mechanisms in hard-to-reach places and at fire-hazardous facilities. In addition to joining elements made of ferrous and non-ferrous metals, blind rivets are capable of joining plastic and textiles in any combination. This allows them to be widely used in electrical work and actively used in the manufacture of clothing, textile consumer goods and tanks.




Advantages and disadvantages
High consumer demand for blind rivets is due to a number of indisputable advantages of these hardware.
- The ease of installation is due to the need to access the connection only from the front side. This favorably distinguishes these hardware from threaded nuts, for the installation of which access is required from both sides. In addition, threaded fasteners tend to loosen and loosen over time.
- The low cost of blind rivets makes it possible to form a reliable and durable fastener without saving on material.


- A wide range of standard sizes greatly facilitates the choice of fasteners.
- The ability to combine materials of different structure and properties greatly expands the scope of hardware.
- High strength and durability of the connection. Subject to the rules of installation and careful operation, the service life of the rivets is equal, and sometimes even exceeds the service life of the fastened parts.
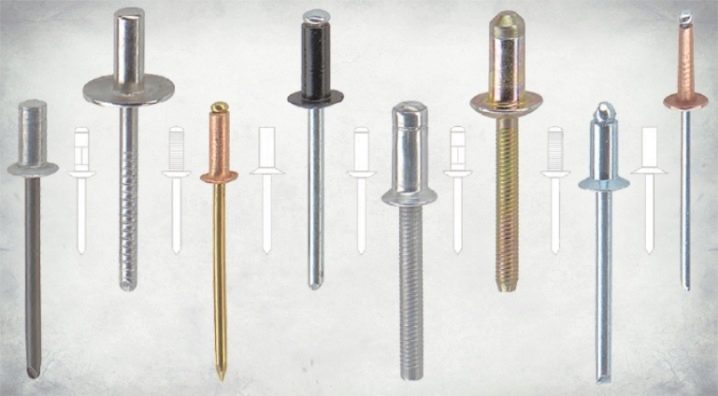
The disadvantages include the need for pre-drilling, non-separable connection and the application of significant efforts when riveting by hand. In addition, the models are disposable and cannot be reused.
Manufacturing materials
A wide variety of materials are used as a raw material for blind rivets. This allows the use of hardware in almost all types of repair and construction work. For the manufacture of rivets, a number of materials are used, each of which has its own strengths and weaknesses and determines the place of installation of future products.


Aluminum
Its anodized or varnished modification is often used. Aluminum rivets are lightweight and low cost, however, in terms of strength, they are somewhat inferior to steel models. Products are used for bonding light metals, plastics and are widely used in electrical engineering.
Stainless steel
Also used in several modifications. So, grade A-2 is considered one of the most resistant to rust and is used for mounting parts when performing outdoor work. While A-4 is unmatched in acid resistance and is widely used in chemical industries.

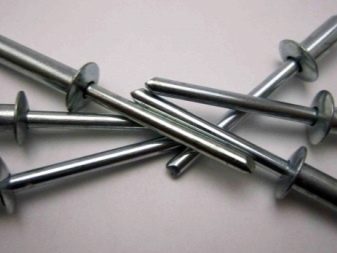


Cink Steel
Possesses high anti-corrosion properties and provides a reliable connection. However, if one of the connected elements is mobile, the galvanized parts wear out quickly.
Copper alloys
They are widely used in the production of rivets. The most popular is Monel, an alloy composed of 30% copper and 70% nickel. Sometimes bronze is used as a rod in copper models. The disadvantage of copper elements is their high cost and the risk of a green coating during oxidation.




Polyamide
They are used for making rivets used in light industry and for sewing clothes. The material is not particularly durable, but it can be painted in any color and looks good on products.
Optimally, all rivet elements should be made of the same material. Otherwise, the risk of galvanic processes increases, during which the more active metal destroys the weaker one. The principle of compatibility must also be followed when selecting hardware for certain materials. For example, a bond of copper and aluminum is extremely undesirable, while copper behaves quite friendly with other metals.



Views
The type of hardware is selected in accordance with the requirements for the connection. Due to the fact that the modern market of fasteners presents a wide range of blind rivets, it will not be difficult to choose the right element. Depending on the performance characteristics, the hardware is divided into several types.
- Combined models are considered the most common species. Hardware is capable of providing a permanent connection of particularly hard parts that are exposed to mechanical, weight and vibration loads.



- Sealed models have a rather narrow specialization and are widely used in shipbuilding industries. A feature of the design of blind models is the sealed end of the rod. Products can be made of stainless steel, copper and aluminum.
- Multi-clamp models have several riveting sections and are installed in movable structures if it is necessary to connect three or more elements. Such a section is located between two adjacent elements, and the installation is carried out using a pneumatic gun.
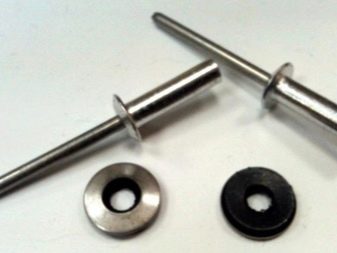


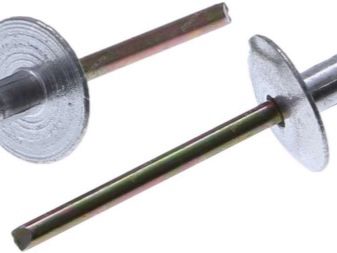
In addition to traditional models, there are reinforced rivet options, in the manufacture of which a stronger material with thicker walls is used.
Typical dimensions
According to GOST 10299 80, the shape, dimensions and diameters of the heads and shanks of blind rivets are strictly regulated. This allows you to systematize the use of hardware, as well as to simplify the calculation of the parameters of parts and to accurately determine their number. The reliability and durability of the connection depends on how correct the calculations are. One of the main parameters of rivets is their length, which can be calculated using the following formula: L = S + 1,2d, where S is the sum of the thickness of the elements to be joined, d is the rivet diameter, and L is the required length of the hardware.


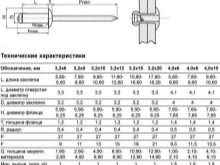
The rivet diameter is chosen 0.1-0.2 mm less than the drilled hole. This allows the part to be freely positioned in the hole, and, having adjusted its position, riveted. Typical blind rivet diameters are 6, 6.4, 5, 4.8, 4, 3.2, 3 and 2.4 mm.The length of the rivets varies from 6 to 45 mm, which is quite enough for joining materials with a total thickness of 1.3 to 17.3 mm.
Design and principle of operation
Blind rivets are produced in strict accordance with the DIN7337 standard and are regulated by GOST R ICO 15973. Structurally, the parts are composed of two elements: a body and a rod. The body consists of a head, a sleeve, a cylinder and is considered the main element of the rivet, which performs the fastening function. For some hardware, the cylindrical base is sealed tightly. The head of the body can be equipped with a high, wide or secret side.


The first two provide the most reliable connection, however, they will be clearly visible from the front side. The secret is not distinguished by such high reliability rates as high and wide, but it is also widely used in construction and repair. This is due to the fact that the height of the head of the countersunk side does not exceed 1 mm, which makes the hardware almost invisible on the surfaces to be fastened. The rod (core) is an equally important part of the rivet and looks like a nail. On the upper part of the element there is a head and a retainer with a separation zone located between them, along which the rod breaks off during installation.


Blind rivets are available in different sizes. The numerical value of the hardware marking means the diameter of the cylinder and its length. Therefore, its dimensions are decisive when choosing fasteners. Both values are indicated through the sign "x", and in front of them it is written from which alloy the cylinder is made. So, marking AlMg 2.5 4x8 will mean that the hardware is made of magnesium-aluminum alloy, the outer diameter of the cylinder is 4 mm, and the length is 8 mm. The rivet shank is made of steel and is used for riveting the connection; during installation it is pulled out and broken off using a pneumatic rivet or pliers.


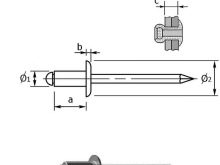
The blind rivet works quite simply: hardware is inserted into the through hole, pre-drilled in both sheets. After that, the sponges of the pneumatic gun rest against the side of the rivet, clamp the rod and begin to pull it through the body. In this case, the rod head deforms the body and tightens the materials to be joined. At the moment of reaching the maximum tightening value, the rod breaks off and is removed. The product can be used immediately after installation.
Mounting
Installation of blind rivets is so easy that it is not difficult even for beginners.

A prerequisite for installation is only the availability of a riveting tool and adherence to the sequence of work.
- The first step will be to mark the front side of the top of the parts to be joined. The distance between two adjacent rivets should not be less than five diameters of their heads.
- The holes must be drilled with a small allowance.
- Deburring is performed on both sides of each part. If access to the closed side is restricted, deburring on the closed side is negligible.


- The installation of the blind rivet must be done in such a way that the shank is on the face side.
- Gripping the rod with a rivet and working with a pneumatic gun must be done smoothly and with sufficient force at the same time.
- The remaining part of the rod, if necessary, is cut off or cut off with nippers. In the case of an inaccurately executed break of the rod, it is allowed to file the head with a file.
Useful Tips
In addition to the general algorithm for performing work, each individual material has its own small subtleties of installation. So, when connecting materials of different thickness, the rivet should be installed from the thin side. This will allow the reverse head to form a thicker flattening and improve the reliability of the connection. In the absence of the possibility of such an arrangement on the side of a thin material, you can put a washer of the required diameter.Such a gasket will not allow a thin layer to be pushed through and will not allow the surface to deform.


When joining hard and soft materials, it is recommended to use hardware with a high sidem, while the reverse head is better placed on the side of the solid material. If this is not possible, then from the side of the soft layer, you can put a washer or use a petal rivet. It is better to connect fragile and thin parts with plastic blind rivets or use spacer and petal options. To obtain a smooth surface on both sides, it is recommended to use rivets equipped with countersunk heads on both sides.


To form a sealed waterproof connection, it is necessary to use closed "blind" hardware that can effectively prevent the ingress of dust and prevent the ingress of water and vapors. When installing a rivet in a hard-to-reach place, along with a rivet gun, it is necessary to use additional equipment in the form of extension nozzles to help get to the rod.

In addition, when installing hardware, it should be borne in mind that the distance from the axis of the element to the edge of the parts to be joined must be greater than or equal to two diameters of the head. The connection of loose materials must be accompanied by the installation of an additional sleeve, into which the rivet will be installed. When joining pipes with flat surfaces, it is not recommended to pass hardware through the pipe. The connection will be stronger if only one side of the tube is involved in the docking.


Thus, blind rivets are a universal fastening element. They allow you to form a strong and reliable connection in hard-to-reach areas. Also, the parts easily bond surfaces with limited access from the back side.
A detailed story about the use of blind rivets is in the video below.
The comment was sent successfully.