Spiral wound air ducts
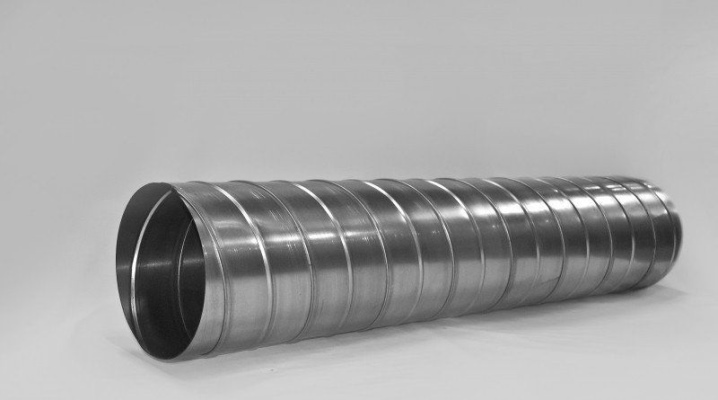
Spiral wound air ducts are of high quality. Allocate according to GOST models 100-125 mm and 160-200 mm, 250-315 mm and other sizes. It is also necessary to analyze the machines for the production of round spiral-wound air ducts.
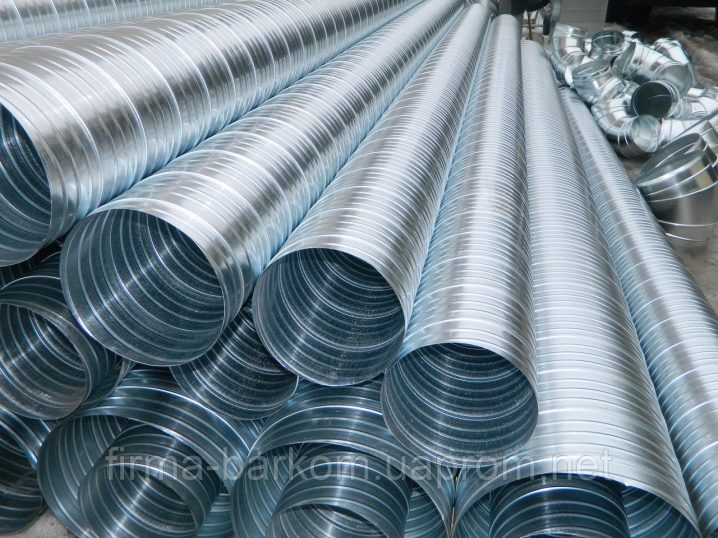
Description
A typical spiral wound air duct is a full-fledged analogue of rectangular models. Compared to them, it is faster and easier to assemble. The standard material is zinc coated steel. Welded and flat corners are used as flanges. The thickness of the material is not less than 0.05 and not more than 0.1 cm.
Spiral-wound models can have non-standard lengths. In some cases, this is very practical. The air is evenly distributed inside the round pipe.
The sound volume with this performance will be lower than in rectangular analogs. Compared to rectangular structures, the connection will be tighter.
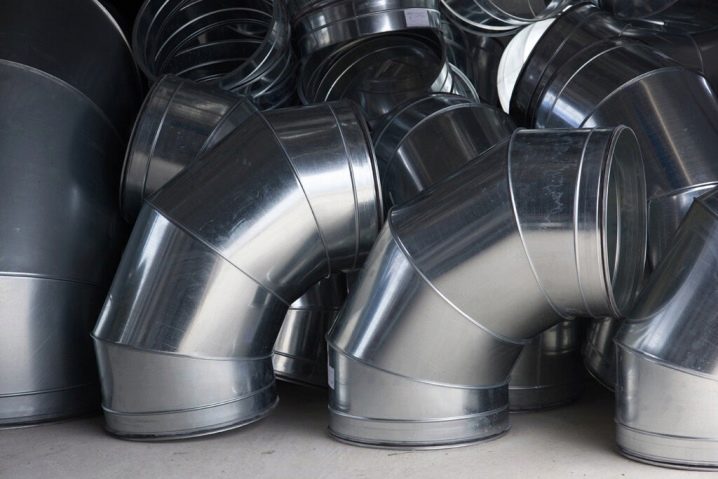
Features of production
Such air ducts are made of stainless steel, or rather, of galvanized strip metal. The manufacturing technique has been worked out very well. It provides strength and rigidity to the resulting product. The strips are attached with a special lock. Such a lock is located strictly along the entire length of the duct, which guarantees a reliable and rigid performance.
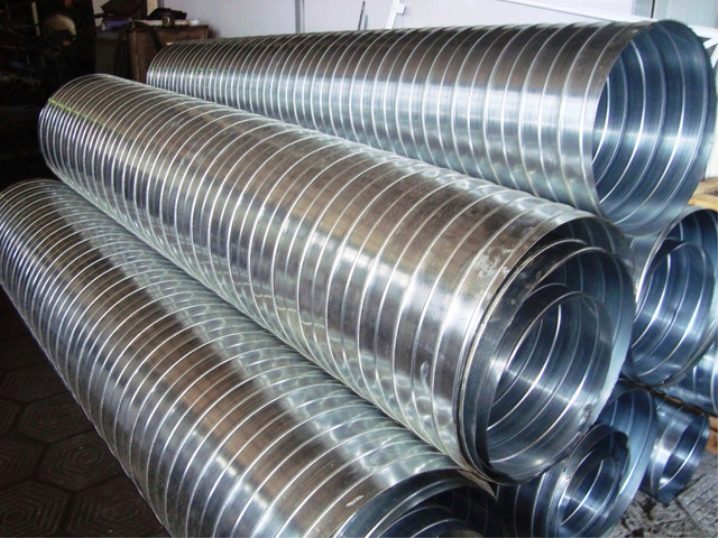
Straight sections of a typical length are 3 m.However, as needed, duct segments up to 12 m long are produced. Machines for the manufacture of round ducts successfully work with ferrous, galvanized, and stainless steel. The length of the blanks is from 50 to 600 cm. Their diameter can vary from 10 to 160 cm; in some models, the diameter can reach 120 or 150 cm.
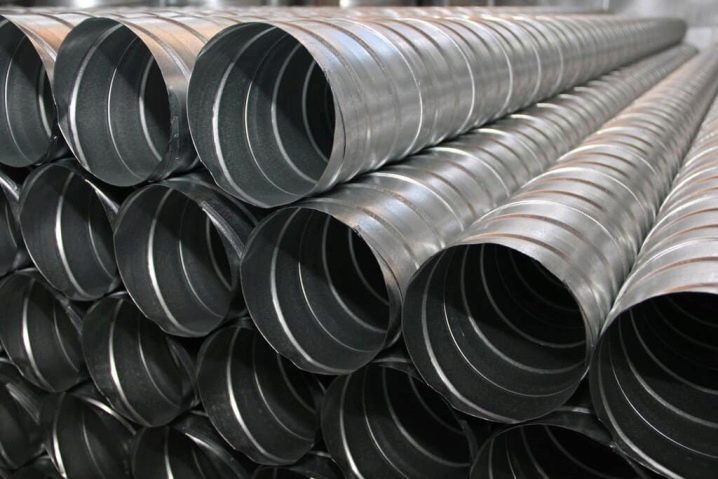
Spiral-wound machines of special power are used for the production of air ducts for industrial facilities... In this case, the pipe diameter can reach 300 cm. The wall thickness in special situations is up to 0.2 cm. Numerical control guarantees complete automation of the process.
The employees will only need to set the key settings, and then the software shell will draw up the algorithm and work it out with high accuracy.
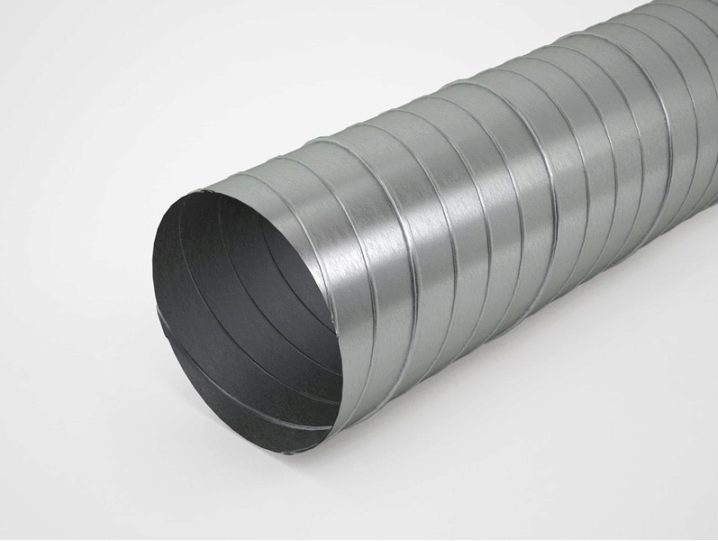
The interface of a modern machine tool is pretty simple. It does not require a thorough study of the features of the technique. Cutting and winding are very efficient. Automatic accounting of sheet metal costs is guaranteed. The technique is approximately as follows:
- on the front consoles, coils with metal are placed, having a given width;
- the grips of the machine fix the edges of the material;
- then the same grippers begin to unwind the roll;
- the steel tape is straightened using cylindrical devices;
- the straightened metal is fed to the rotary apparatus, which provides the arrangement of the locking edge;
- the tape is bent;
- the workpiece is folded, getting the lock itself;
- the resulting pipes are dumped into a tray for acceptance, sent to the workshop warehouse, and from there to the main warehouse or directly for sale.
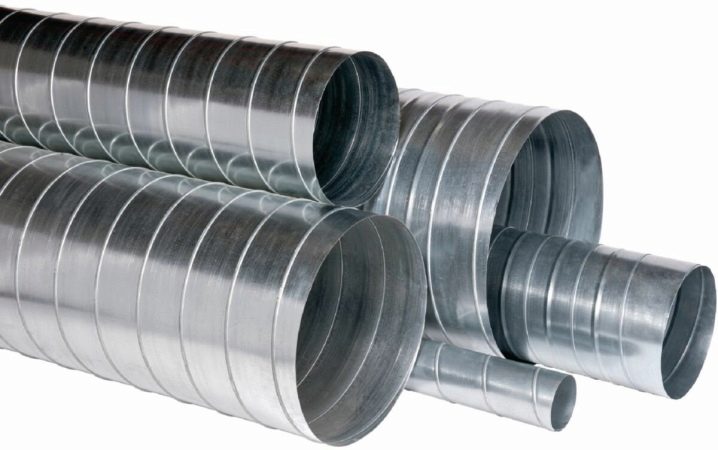
Dimensions (edit)
The main dimensions of round air ducts, the steel of which corresponds to GOST 14918 of 1980, are most often set on the basis of practical nuances. The usual diameter can be:
- 100 mm;
- 125 mm;
- 140 mm.
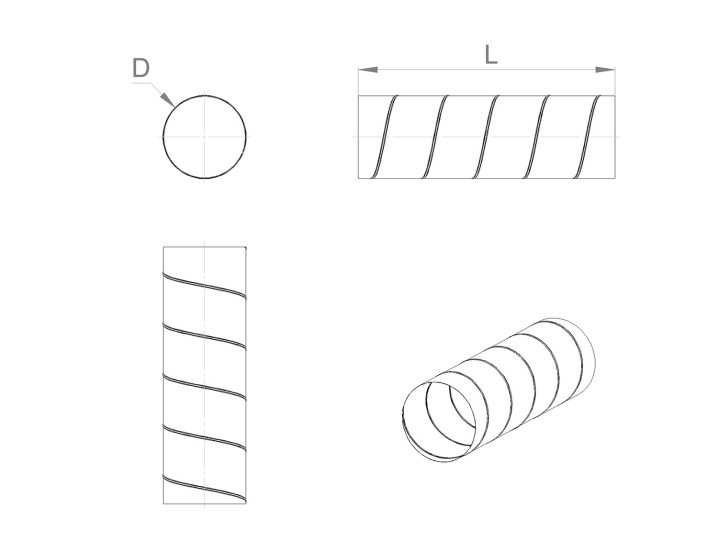
There are also products with a cross section of 150 mm or 160 mm. If desired, you can order larger ones - 180 and 200 mm, as well as 250 mm, 280, 315 mm. But even this is not the limit - there are also models with a diameter:
- 355;
- 400;
- 450;
- 500;
- 560;
- 630;
- 710;
- 800 mm;
- the largest known size is 1120 mm.
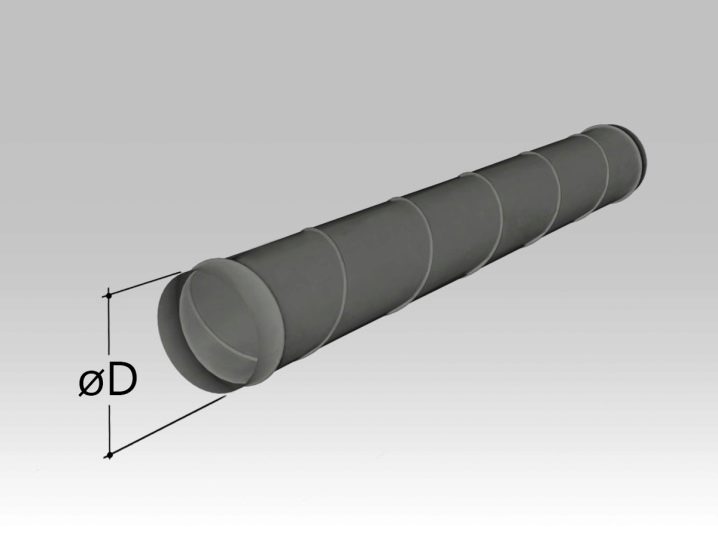
The thickness can be equal to:
- 0,45;
- 0,5;
- 0,55;
- 0,7;
- 0,9;
- 1 mm.
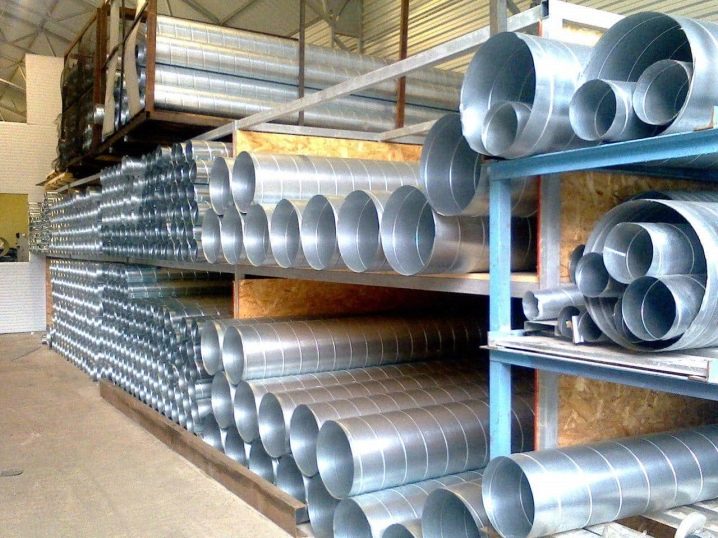
Installation tips
Spiral-wound air ducts are needed mainly for arranging ventilation and air conditioning systems. Be sure to take into account the features associated with the calculation of the required parameters. Such pipelines cannot be used for pneumatic mail and in aspiration complexes. Nipple connections are usually taken as a basis. It is much more compact than when using flange or bandage systems.
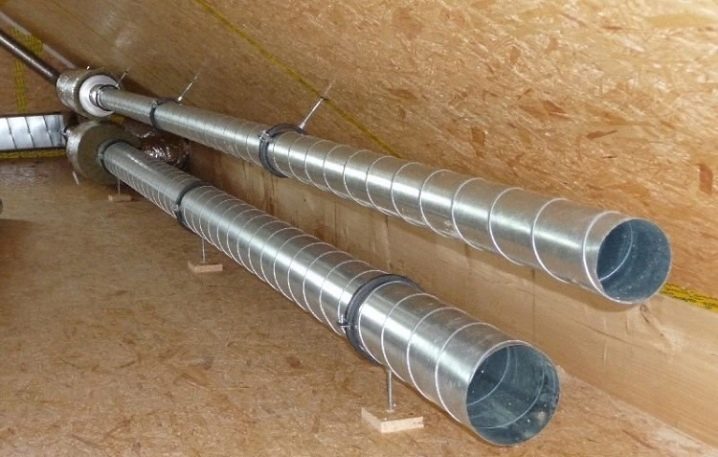
The gasket scheme is selected individually. According to it, the required number of elements and the consumption of connecting parts are determined. Having put the fasteners, they ensure the fixation of the pipes during further work. The air ducts themselves must be assembled as tightly as possible. When installation and assembly is complete, the system is tested.
Straight sections are collected only by the nipple method... Each nipple is covered with a layer of silicone-based sealant, and the fittings are fixed using specialized couplings. The pipe must not be allowed to sag by more than 4% along its entire length.
Do not make turns with a radius exceeding 55% of the channel section. Such solutions maximize aerodynamic performance.
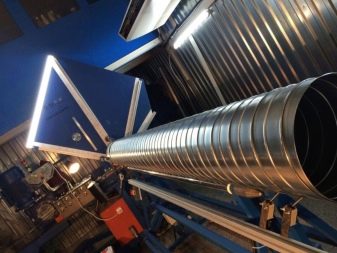
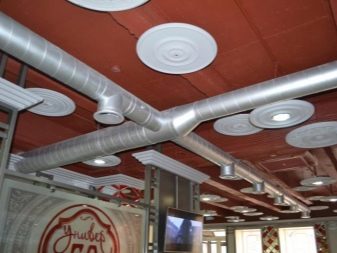
Shaped elements are installed not only with the help of couplings, but also with the use of clamps... Each clamp must be fitted with an elastic gasket. The step between the suspension mountings should be kept as strictly as possible.
There are also other subtleties:
- the bandage connection is performed quickly, but does not allow achieving full-fledged tightness;
- the most professional connection by a combination of stud and profile;
- air ducts insulated with heat-insulating or sound-insulating materials must be fixed on a hairpin and a traverse;
- all attachment points are fitted with rubber seals to reduce noise and vibration.
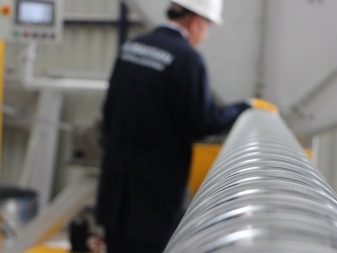
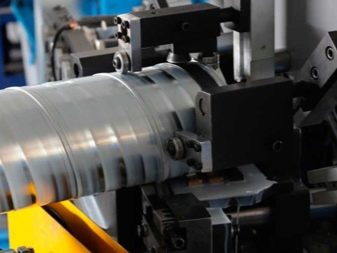
The comment was sent successfully.