All About Duct Flange
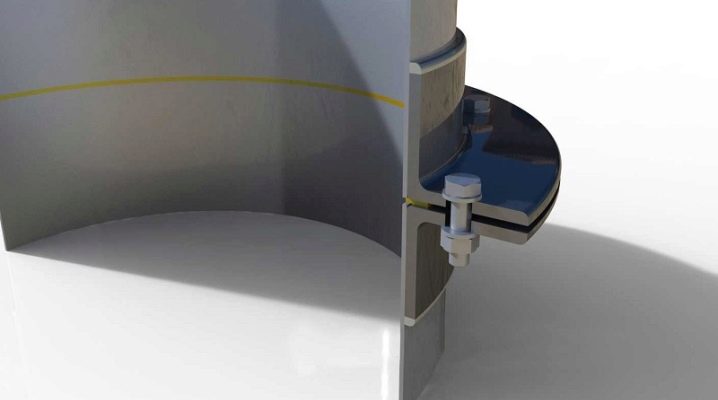
The ventilation system is a prefabricated structure consisting of several elements. Normal air circulation in the system is ensured by tightness, which also prevents the occurrence of extraneous noise. The desired result will be achieved with a duct flange.
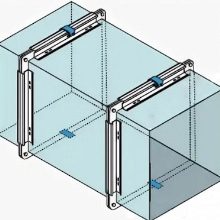
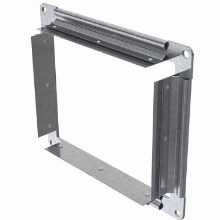
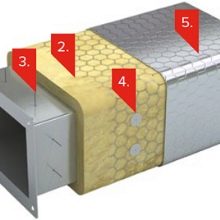
What it is?
A flange - or a tie-in - is one of the forms of shaped products, with the help of which it is possible to organize a reliable installation of air ducts and ventilation ducts, to perform a tight connection of elements in almost any plane. Products of this type are applicable in finished structures, as well as when performing pipe routing.
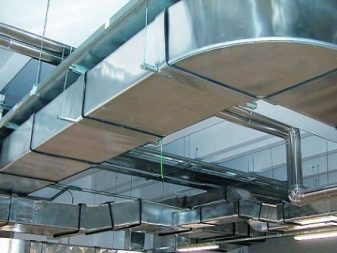
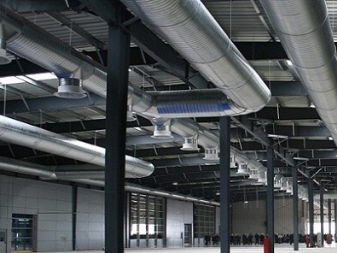
Manufacturers produce different types of flanges, relying on a variety of fittings for air ducts. Regardless of the type, the fittings are equipped with a flange on one side, which ensures a sealed joint. On the other side of the part there is a straight edge, which provides for the possibility of flange connection of the elements.
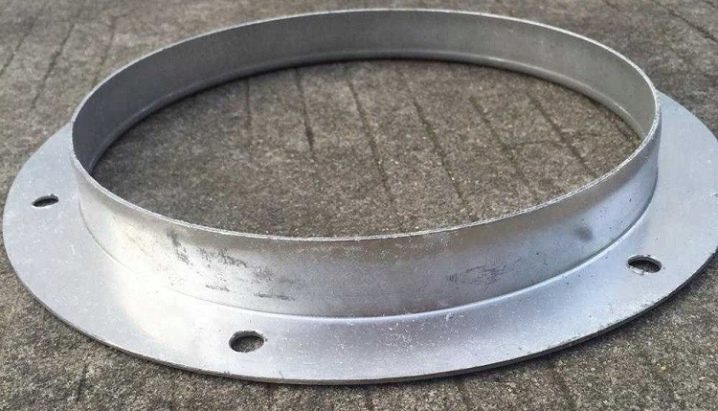
In addition to flanges, other components are also used in the ventilation system.
- Nipples... They are simple parts that are suitable for organizing quick connection of structural elements. Fixing of fittings takes place by using small steel pipes, the joints are sealed.
- Bandage... In this case, the ends of the pipes are pre-flanged, and then a bandage with a provided recess is put on from above. The tightness of the structure is ensured by the mastic, which is used to fill the bandage.
- Trumpet... Provides for the possibility of inserting ventilation system elements into each other due to narrowing or expansion at the end of the part.
And you can also connect the elements of the duct using a euro bus. The galvanized L-shaped section guarantees a secure connection. The insert differs from the listed parts and resembles a tee in its functionality. However, it is generally accepted that the use of such a connection option is cheaper and simpler.
Thanks to the use of flanges, it is possible to shorten the work time and also save on materials.
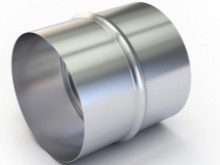
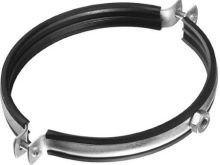
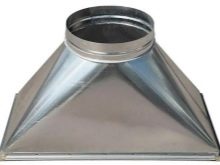
Features of production
Flanges are manufactured using special equipment. For the production of parts, factories use lightweight and durable material that can be easily processed and acquire the desired properties in a short time. Among the main ones:
- Cink Steelthe thickness of which does not exceed 1.2 mm;
- stainless steel, produced in sheets or rolls.
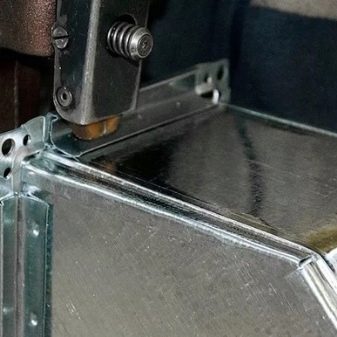
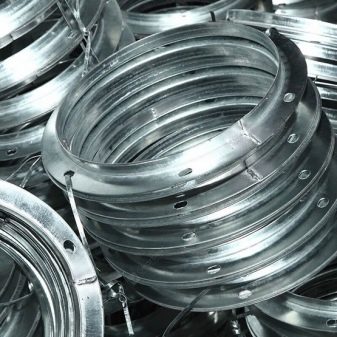
The flange manufacturing procedure begins with preliminary marking and cutting of blanks, from which the future product will subsequently be formed. The process is based on the blank stamping method, which produces durable parts with a long service life. The connection of a straight sheet and the creation of the required cut-in shape is ensured by the counter-type grooves, which are pressed in the process using a press.
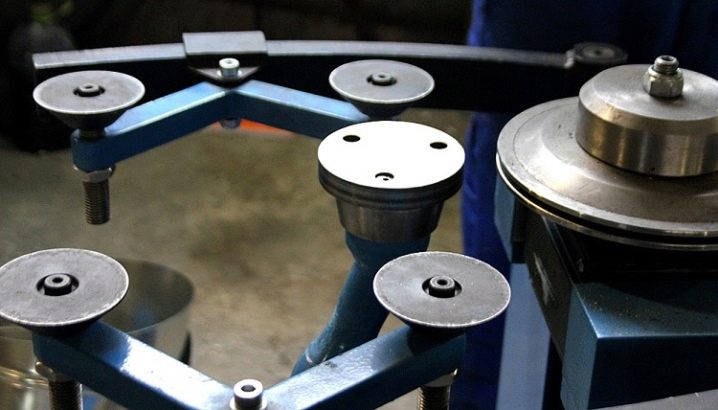
After the flanges are made, a small amount of steel and other material remains, which is used for the production of corners, fittings and other small parts. The production of tie-ins requires compliance with certain norms stipulated by state standards.
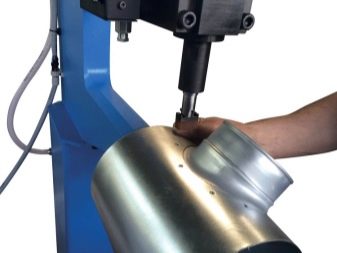
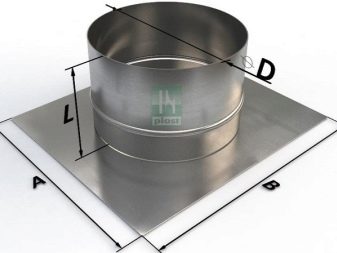
Regulatory documents regulate not only the production methodology, but also the characteristics of the materials used. Therefore, when choosing fittings, it is recommended to give preference to elements produced by trusted manufacturers.
Otherwise, the likelihood of premature destruction of the system increases due to the use of poor quality connection elements.
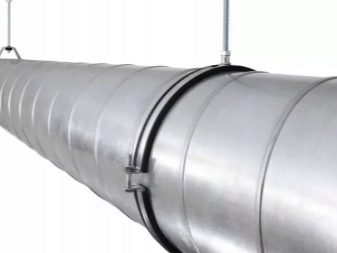
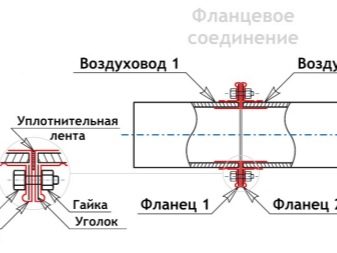
Specifications
Tubes for connecting duct elements are distinguished by the type of cross-section, diameter and size. These can be parts with a diameter of 560 or 115 mm, or a section with dimensions of 120, 110 or 200 mm. The main characteristics are regulated by regulatory documents. Popular flange sizes are shown in the table.
Length, mm |
Inset diameter, mm |
Maximum product area, m2 |
Maximum weight, kg |
100 to 200 |
40 |
0,6 |
0,3 |
250 to 600 |
60 |
0,18 |
1 |
630 to 900 |
80 |
0,33 |
2,6 |
1000 to 1250 |
100 |
0,5 |
4 |
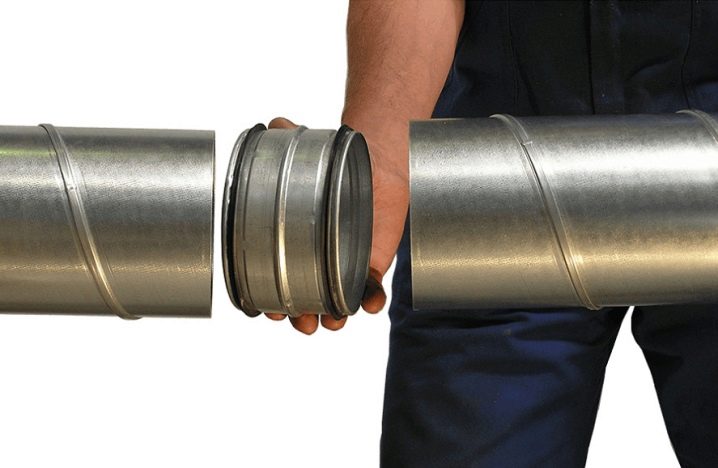
And also tie-ins can have a size of 150, 160 and even 315 mm, regardless of the shape of the section. When choosing, it is worth paying attention to the diameter of the pipe or the dimensions of the rectangular duct in order to select the appropriate connecting element. For example, for a 100x150 fittings, a flange of the same dimensions or slightly smaller dimensions is suitable.
Each flange is equipped with a flange, by means of which it is possible to securely fasten the element and ensure a tight connection of the air duct parts. And also in the design of the tie-in there is a nipple necessary to connect the air duct with the central pipe of the ventilation line.
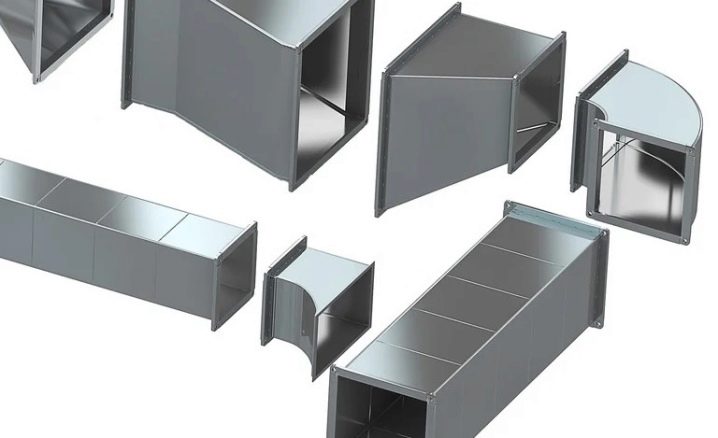
Air ducts, as a rule, are produced by the same manufacturers that produce fittings for ventilation systems. Therefore, it will be easy to find a part of the right size for installing the system.
When studying the characteristics of the flanges, you should additionally pay attention to the rigidity of the elements of the ventilation system, which must be achieved during installation. If the tie-ins are incorrectly installed, there is a risk of destruction of the line.
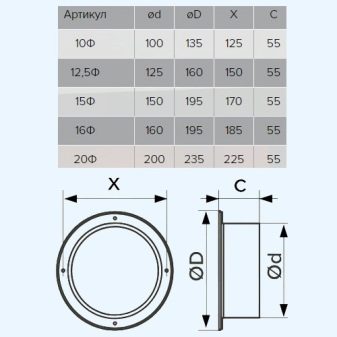
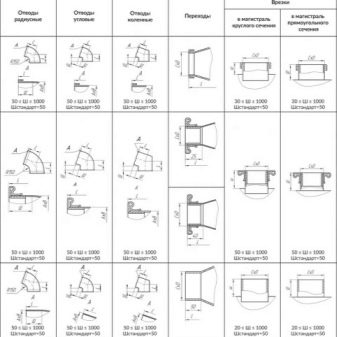
Views
The dimensions and type of flange are determined based on the dimensions and section of the part to which the element is connected. Manufacturers produce different variations of frames, which can be roughly divided into two main groups.
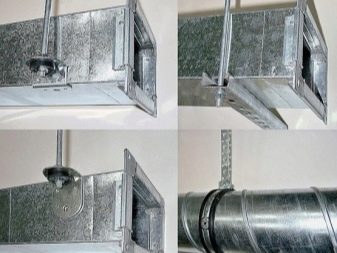
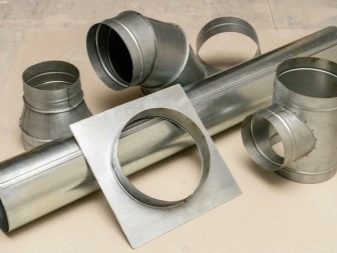
Round
Designed for installation of branching round duct systems. They are used for reliable and tight connection of round pipes of different diameters. Flange selection is carried out depending on the diameter of the pipe, the assortment is represented by a large selection of elements of different sizes. This type of flange is lightweight, easy to install and has a long service life.
A flange is provided in round inserts, which makes it possible to achieve a hermetically sealed connection of the duct elements. The diameter of such elements ranges from 10 to 125 cm and is selected depending on the fittings that will be connected to each other. The length of the round inset is 6-10 cm. On the body of most elements there are special protrusions that allow you to fix the pipe in the desired position. This category has a subspecies - straight round cuts, which are used to connect round ducts with rectangular systems.
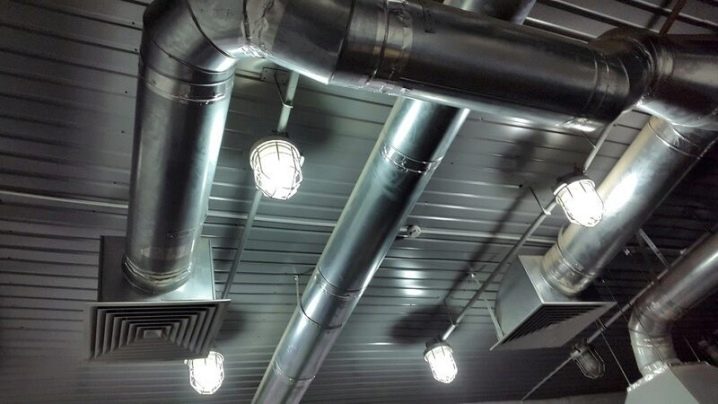
Rectangular
Rectangular cut-outs are used to fasten the central pipe using self-tapping screws or rivets. Among the differences of this type of elements, a layer of silicone sealant is distinguished, which provides an increased tightness of the connection. A special feature of rectangular flanges is the presence of a flange on one side and a connecting strip on the other. And also the design provides a persistent protrusion.
The average size of the inset is 10-250 cm and is selected depending on the cross-section of the rectangular duct. Fasteners are installed in 5 cm increments. Corner flanges for a circular duct are a separate category. Such elements are used when it becomes necessary to branch the system and form a new branch or lattice at an angle.Such fittings are distinguished by a straight flanged side, therefore, such flanges are not suitable for mounting a round line.
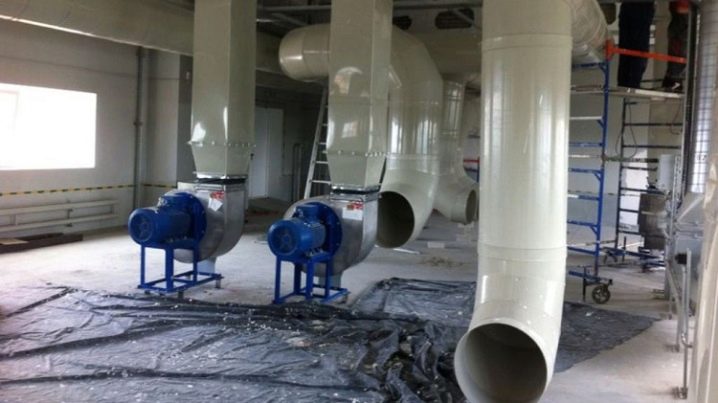
Mounting
The ventilation structure is a complex system of several elements, the installation of which must be approached responsibly. Regardless of where the air ducts will be located, the scheme will remain the same. There are two ways to mount a structure using inserts.
- Into the plane. This method is used mainly for fixing round air ducts going into a rectangular pipeline. To ensure a reliable connection of the elements, a hole is preliminarily made in the structure so that the transverse dimension of the wall is greater than the diameter of the hole by a maximum of 5 cm.
- Into the pipe. The method of mounting a round air duct into the wall provides for the presence of a connecting pipe. For reliable fixation of the device, a hole of a pre-calculated diameter is made, and a layer of insulation is applied, which contains silicone. Only after that, a flange is installed, which will ensure the connection of the structural elements.
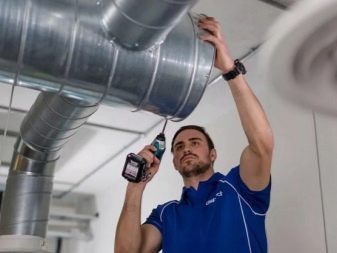

The corner insert should not be considered separately, since the installation is carried out according to the standard scheme. The only difference is that the finished mechanism is fixed using spot welding or rivets, and then the installation is mounted to the wall or ceiling.
The correct approach to the installation of tie-ins will not only ensure reliable sealing of the joints, but also:
- relieve excess heat and harmful substances;
- eliminate combustion products;
- will reduce the risk of smoke entering the system;
- keep moisture readings normal;
- removes excess dust and harmful gases from the system;
- normalizes temperature indicators.
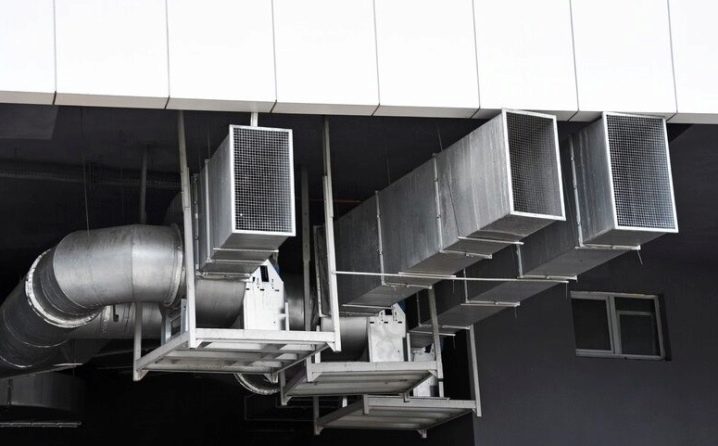
Now it is worth taking a closer look at the installation scheme of the flanges themselves. Main steps.
- Preparation... Before installing the flange into the ventilation system, it is necessary to purchase the elements of the required dimensions. In order not to be mistaken in the choice, it is recommended to draw a figure at the place of the future exit of the new channel branch, depending on the type of air duct. When the drawing is ready, an understanding will come about which shaped product is needed.
- Calculation of dimensions and diameter. To determine the dimensions of the flange, and to clarify its cross-section, it is necessary to measure 5 cm from the upper and lower corners of the shaft.If a round line is planned, then it is worth measuring the diameter of the main line, and choosing a part with a lower value.
- Selection of tools... The third stage involves the preparation of tools with which the part will be inserted. For work, you will need metal scissors, a screwdriver or screwdriver, as well as rivets, a marker and a pencil. Additionally, it is worth stocking up on silicone sealant.
- Hole cutting... First of all, they start cutting a hole, which in its dimensions will correspond to the internal dimensions of the inset. Only in this case it is possible to organize a tight fit of the flange to the surface. It is not worth reducing the output too much, so as not to disrupt the functionality of the system.
- Mounting... When the hole is ready, the edges of the flange are covered with a layer of sealant to achieve a tight seal, and then the part is installed in place. The element is fixed with rivets, in rare cases self-tapping screws are used.
At the end, the silicone is allowed to dry, and only after that they begin to install the branch.
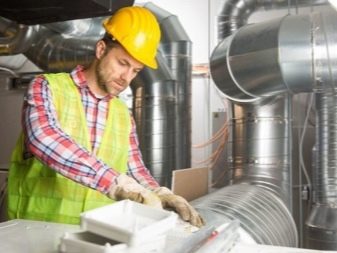
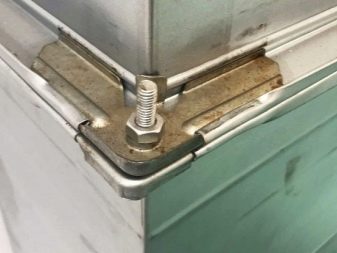
The comment was sent successfully.