Cleavers: features and types
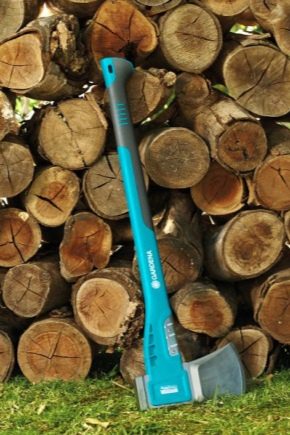
In Europe, spike-shaped axes appeared during the time of the Roman emperor Octavian Augustus. In the Middle Ages, their distribution became widespread. Their difference was that their width was only one third of the height, and there were also additional side details. Over time, the Slavic peoples "adopted" other products, but the Finno-Ugric tribes used this type of ax for a long time, up to the 15th century.
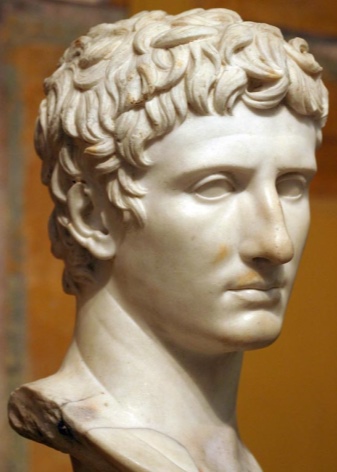
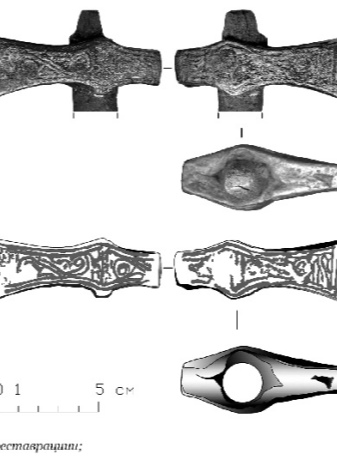
Specifications
Nowadays, cleavers are distinguished by a powerful prismatic blade with a blunt blade, the angle of inclination is approximately 32 degrees. The weight of the products can vary from 1.5 kg to 6 kg. Usually in everyday life you can find an ax that weighs 3.5 kg, and the size of the tool may fluctuate. The ax can be up to one meter long - such a long lever is necessary when you have to handle sticky wood with a high moisture content.
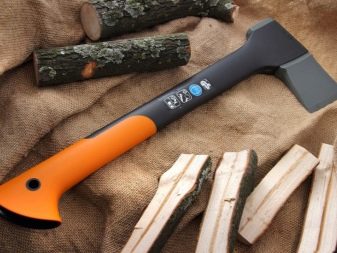
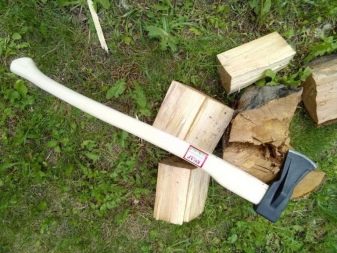
Design
Choppers for chopping firewood are:
- screw (conical);
- hydraulic;
- electrical.
The first type is the most common, used by 80% of consumers. The tapered steel ingot has a strong thread and can be immersed in the material using an electric motor. Cone cleavers are used to harvest firewood. On the trading floors, you can find prepared kits that allow you to assemble such a tool in a few minutes.
The handle is made from durable woods, and the handle can be made from oak, ash or birch. Sharpening is usually carried out at an angle of 40-50 degrees.
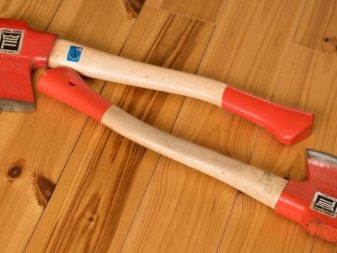
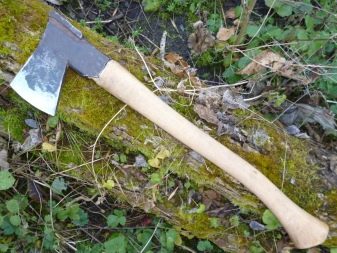
Cleavers are differentiated into the following types:
- massive;
- spicy.
The first type is often confused with a sledgehammer - they are so similar, the second type has a sharper blade. Also, cleavers can be cast and forged. There are no fundamental differences between them.
The cleaver blade can be:
- sharpened by a wedge;
- "Lop-eared".
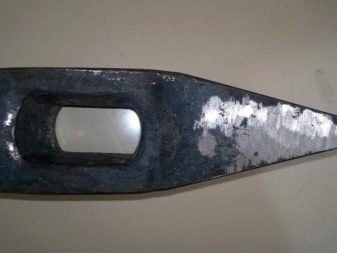
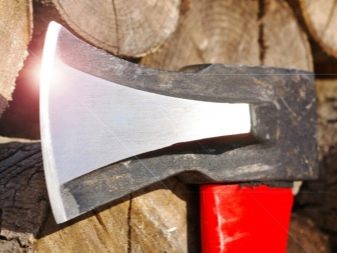
The latter type can be considered a novelty, workers with great practical experience treat it with distrust, express critical remarks. Manufacturers in the instructions claim that this tool can only be used with dry wood. It is recommended to take this fact into account when choosing a tool.
The wooden parts of the cleaver have disadvantages - they can spontaneously split. In recent years, pens have been produced from a new material - fiberglass. This composite material is durable and lightweight. Its advantage is that the recoil to the hand is noticeably less than that of a wooden handle, the material is able to actively absorb vibration. Also, from fiberglass, you can make the ax very long, which has a positive effect on the force of the blow.
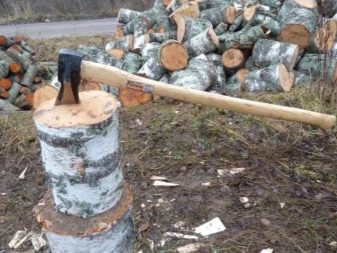
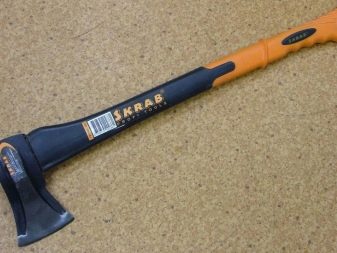
What is it needed for?
There is a wide variety of models of cleavers, which greatly facilitate physical labor, helping to chop wood in a short period of time. A cleaver is noticeably different from an ax - this tool is intended exclusively for chopping wood. Outwardly, there are also noticeable differences. The cleaver looks like a sharpened metal ingot weighing at least 3-4 kg. It has a long, sturdy handle that allows the tool to be removed even from very tough wood. Almost any tree can be chopped with such a tool, and an alternative to the cleaver has not yet been invented.Its design is simple and functional, which explains why this tool has been popular for many hundreds of years.

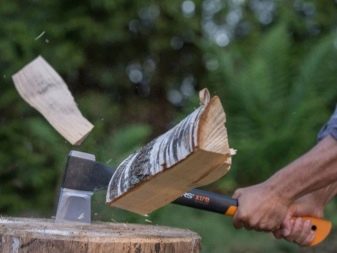
Views
Modern technologies and materials make it possible to improve the traditional design of the cleaver. In our time, cleavers of various types have appeared, among which there are the following:
- with a displaced center;
- manual conical;
- rack and spacer;
- heavy forged;
- with electric or gasoline engine (automatic).
Finnish company Vipukirves, which offers a wide variety of models, which have a "floating" center of gravity, works well for modern developments.
Usually, additional accessories to the main product are not cheap, sometimes their design is quite complex.
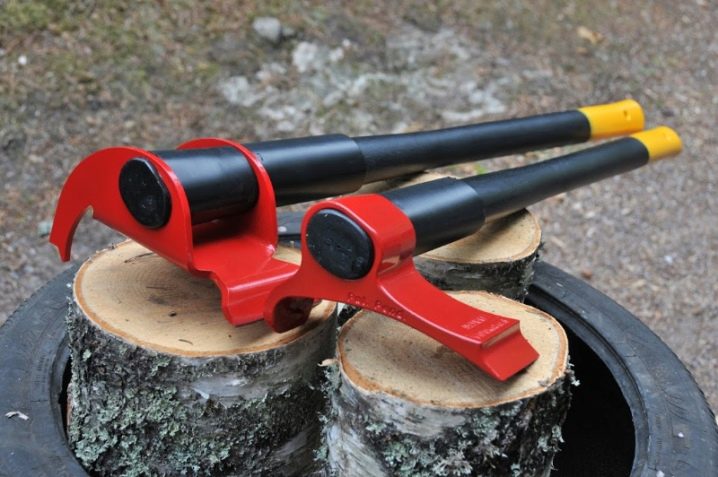
Consider several types of cleavers that are especially popular.
Screw wood splitter
It has become widespread among farmers; it is not very difficult to make such a tool on your own. To make a screw cleaver with an electric drive, you will need:
- an engine with a power of at least 1.8 kW;
- roller with fitted bearing;
- pulley;
- threaded cone;
- metal sheet 5 mm thick;
- corners "4";
- pipes 40 mm;
- bearing.
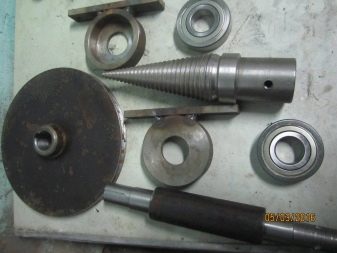
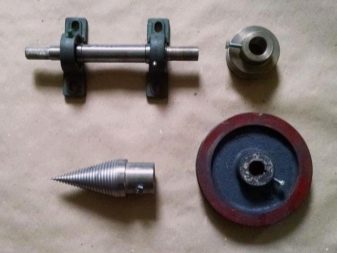
If you put the engine at 450 rpm, then there will be no need to mount the pulley, then it is permissible to simply attach the cone to the shaft. The optimal choice is therefore a speed of 400 rpm or more. The cone can be ordered from a turner or made by yourself according to a pre-drawn drawing. The material from which the cleaver is made is steel with a high carbon content. The threads should be in 7 mm increments, and the threads can be up to 2 mm. Pulleys are machined from regular steel. The size of the groove is determined by the parameters of the pulley.
To assemble a cleaver that works according to the screw principle, you first need to make a base, put a plate under the tabletop on which the engine will be held, and on it, in turn, the shaft. Alternatively, you can secure the cone and pulley and then position and tighten the belt. After that, you can proceed to the tests.
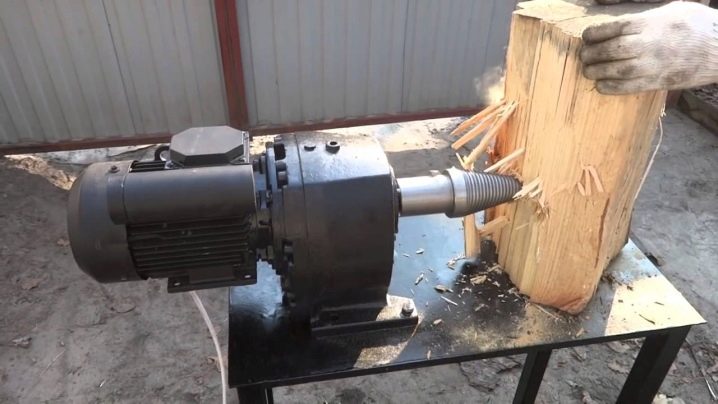
Hydraulic wood splitter
Has good power and performance. The stationary tool is massive, it works using a cylinder in which the working pressure is provided by a pump. It is placed on the same shaft with an electric motor; it is also important to take into account that the unit can be placed even at the other end of the room (not necessarily on the bed). The connection can be made using special hoses.
After the drawings are selected and the necessary nodes are purchased, you should think about how to make a cleaver shape. Welding from metal is the simplest solution. The dimensions can be any. The power of the cylinder is of decisive importance here. It should be enough to split massive wooden ingots, which are fairly saturated with moisture. Such a material has the highest viscosity index, and it is especially difficult to work with it.
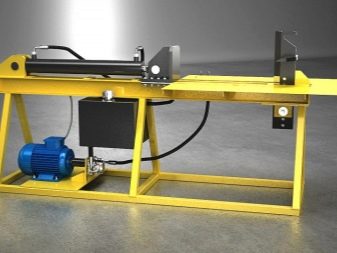
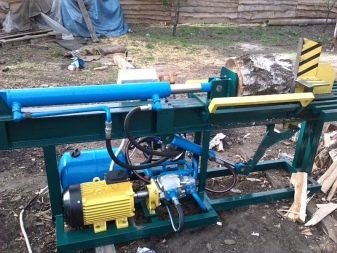
Cleaver in the form of a cross
The mold is mounted on a bed so that the transverse axis coincides with the shaft, which is attached to the hydraulic cylinder, connected to the pump by means of hoses.
You can also mechanize the cleaver by attaching wheels to it.
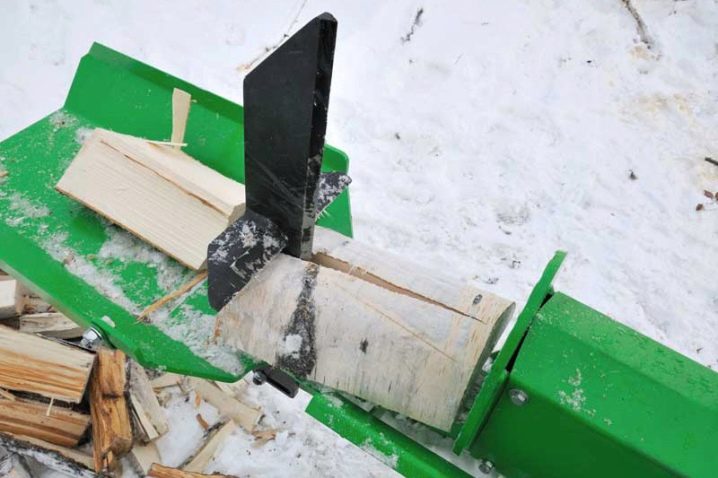
How is it different from an ax?
The cleaver is a type of ax. This tool is intended primarily for splitting large-sized ingots. The cleaver blade also differs from the ax blade: it is wedge-shaped and weighs at least 3.5 kg. The cleaver does not cut like an ax - it splits the material. This is the fundamental difference. When working with a cleaver, the power of the blow is important, and when working with an ax, it is important how sharply the tool is sharpened.
The cleaver can be compared to a sledgehammer, its blade is sharpened at an angle of 45 degrees, which allows you to split even massive logs with a lot of knots.
Cleavers are:
- forged;
- all-metal (cast).
For a middle-aged man with standard physical capabilities, a cleaver with a blade weight of up to 3 kg is suitable.
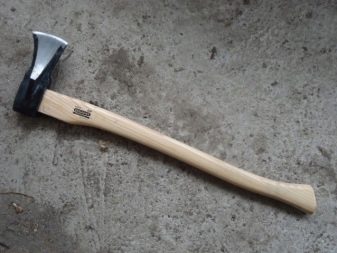
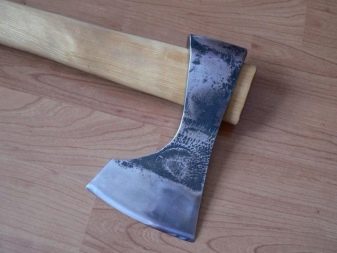
Rating of the best models
Let's conduct a small overview of the most popular models, among which there are samples from American, German and Russian manufacturers.
- Cleaver Ax Matrix weighing 3 kg with fiberglass handle. The product is made of steel grade 66G, the hardness factor is 50 HRc. In order to accurately and effectively split even massive wooden fragments, the head is equipped with a small anvil from the rear. The fiberglass handle is made of the most modern material, never gets wet, does not dry out or swell.
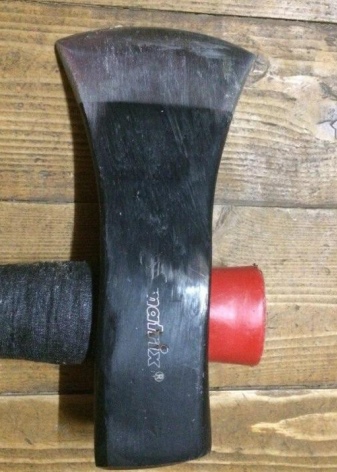
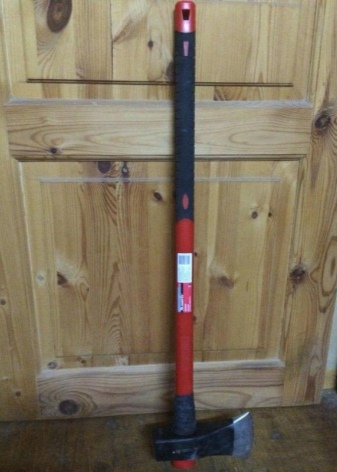
- Cleaver "Bars" from Nylon has a weight of 750 grams, can work with all types of wood. The working part of the cleaver is made of U14 steel, the hardness of the cutting edge at a height of up to 2.5 cm is 47-53 HRc on the Rockwell scale, the sharpening angle is about 28 degrees. There are nubs on the sides - this helps to effectively split the wood. In the lower part of the ax there are special rubber "dampers" of mechanical impulses. The strength of the material is above average. The product is sold in a durable PVC case.
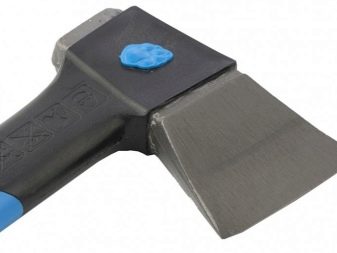
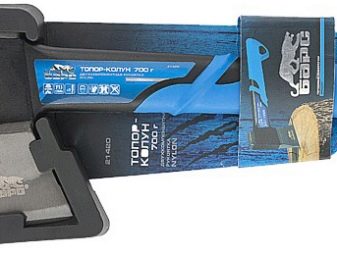
- Cleaver Inforce (3.65 kilograms). The 910 mm long handle is designed for splitting large ingots, ideal for fuel preparation. The product is lightweight and durable.
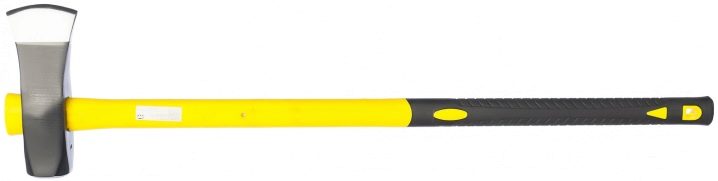
- Cleaver The Great Divider weighing 4 kg with fiberglass handle. The tool is made of steel grade 65G, the hardness factor is 55 HRc. This device can split any fragments, the handle is made of fiberglass material, withstands significant loads and protects from unnecessary vibration.
- Russian-made cleaver "Whirlwind" weighs 3 kg. It has a wooden handle covered with a layer of damper rubber. The length reaches 80 cm.
The tool is effective for splitting solid pieces of wood.
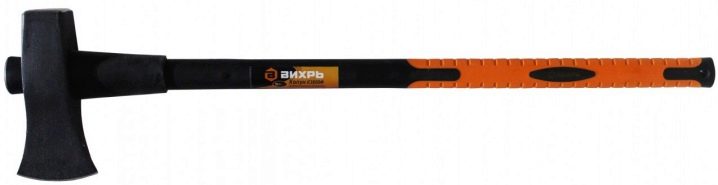
- The German cleaver Stihl 8812008 is also very popular now (weight - 3 kg, length of the ax - 80 cm). There are rubberized pads. The model weighs a little, it is effective in the work of harvesting firewood.
- One of the oldest companies producing axes and cleavers is Fiskars... The company appeared in the 17th century in Sweden. Cleavers from "Fiskars" are a combination of modern design, strength, comfortable grip of the handle and special strength steel. During operation, the clever design guarantees a harmonious combination of impact power and ease of use. The softening elements on the handle are made of modern FiberComp material. This innovative fiberglass is stronger than Damascus steel and is lightweight. All elements of the product are not subject to corrosion or rust. The most popular model is the Fiskars X17.
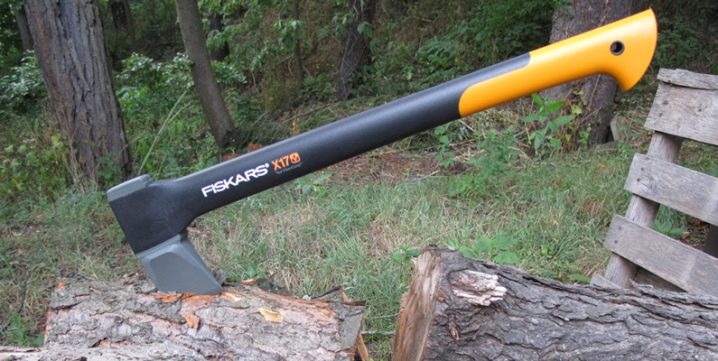
How to choose?
The choice of instrument is dictated by the following criteria:
- the weight;
- material;
- the size of the hatchet;
- sharpening form.
Finding a tool that matches the physical characteristics of an employee is not an easy task. If the cleaver is too light, it will be difficult to split massive fragments, and when working with a heavy tool, more physical effort will be spent, but at the same time it will be much easier to split heavy ingots.
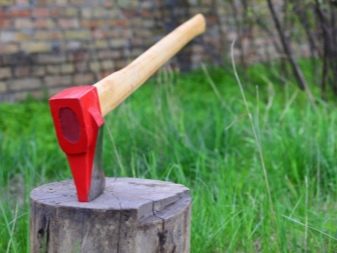
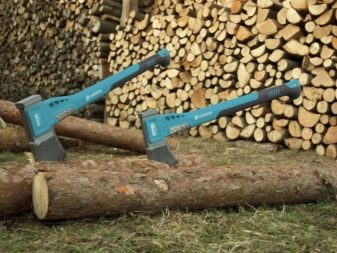
It is also important that the handle is made of solid wood that has "knitting" properties. The handle experiences a significant load, so it must have the above qualities. The short handle also does not fit - it is difficult to work with. Handles that are made of PVC or steel are not the best choice. Such axes are expensive, but it is inconvenient to work with such a tool. Such a tool will not be able to trim the trunks saturated with moisture, the diameter of which is more than 25 cm. The ax gets stuck in such material quite often.
Zealous owners, as a rule, use one of two types of ax: classic or wedge-shaped. The first type is convenient to handle freshly cut wood, in which there is a lot of moisture. The second type is convenient to chop dry logs.
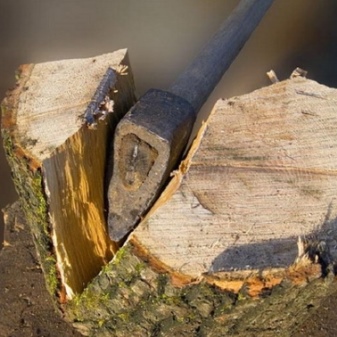
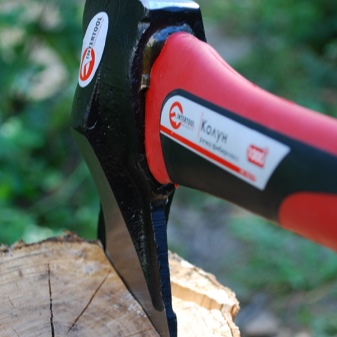
Cone axes are easy to use and quite effective (especially when working with solid wood). The ingot is installed perpendicularly, a screw is driven into it, then it splits. The work is just mechanical.
The hydraulic drive helps in solving production problems - it makes it possible to separate the logs immediately.
It makes sense to use such a device if the work with massive wood blanks occurs constantly, because the hydraulic splitter is quite expensive.
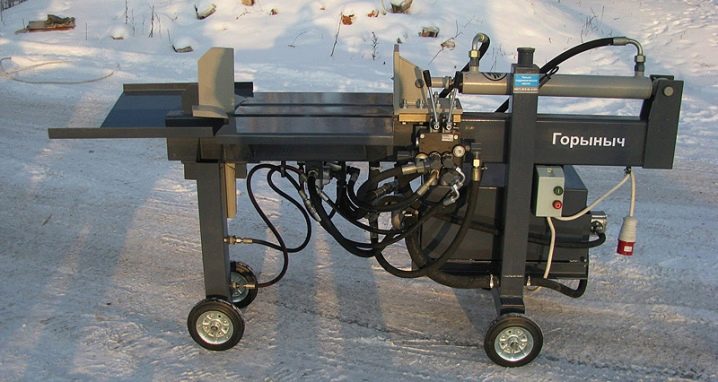
Operating tips
A cleaver, like an ax, is a tool of increased injury risk, so it should be sharpened correctly and used with precautions.
Many questions arise when choosing a product - the tool must ideally match the physical data of the employee. Finding the ideal option is only possible when the cleaver is tested in practice. Even experienced woodcutters do not always "guess" which cleaver is ideal for them.
It is important to choose the right deck - it should be of medium diameter, its height should be 5 centimeters above the knee.
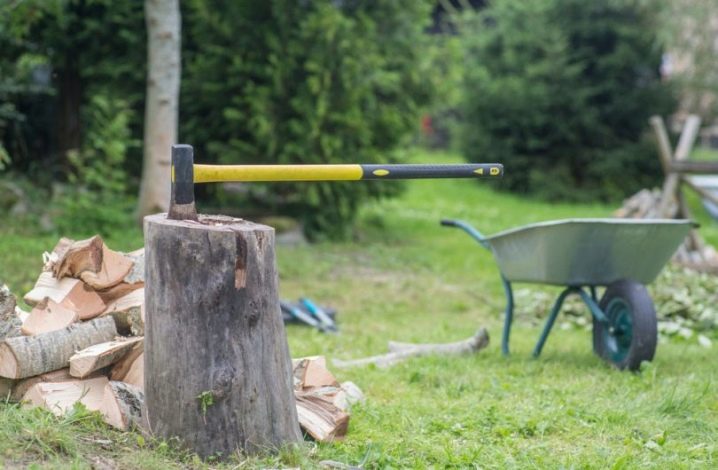
When starting work, you should take care of gloves and glasses. Also, clothing should be loose enough, it should not hinder movement. During operation, there should be no people or animals within a radius of 2 meters - chips can fly off at a significant speed and injure others.
From standard medium-sized chocks, 4-5 logs are obtained. Larger lumps can produce 10 logs. When working, it makes no sense to split a massive piece of wood at once. It is much more reasonable to cut the tree from different sides, chopping off fragments.
It is better to keep the logs in the open air in winter - then the wood will not be soggy and loose. When working with wood, it is recommended to start work from those places where cracks are present. Often, cleavers are inserted into such recesses and hit on them with sledgehammers.
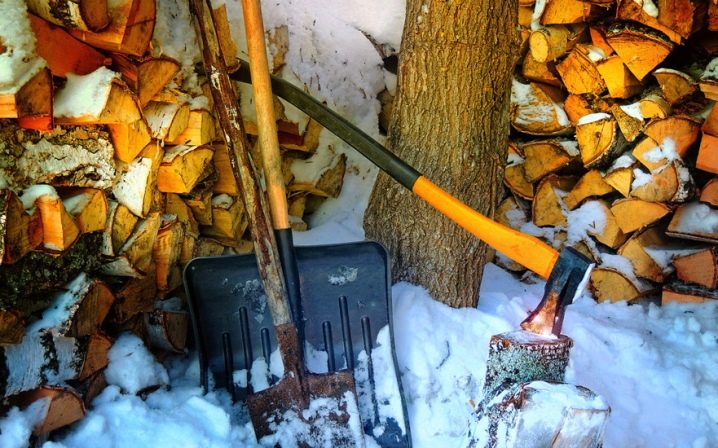
For information on how to make a cleaver from an ax with your own hands, see the next video.
The comment was sent successfully.