All about shale shakers
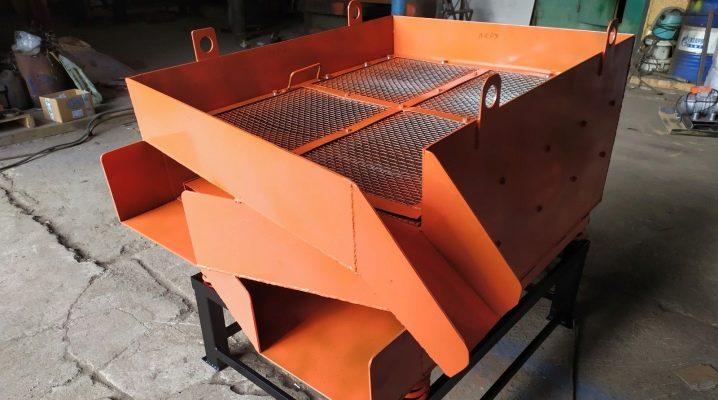
The vibrating screen is a device that is in demand in many industrial sectors. It can be used to sift, clean and separate various materials into fractions. Sieves can differ in shape, type of mesh, number of cleaning levels. Depending on the production goals, you can select a device with suitable characteristics.

What it is?
The device is known as a "vibrating sieve" or "shaker". The first option is more often used to describe equipment for the oil industry, the second name is typical for the mining industry. Although the devices may differ in design, the general principle of cleaning remains the same.
The raw materials that need to be processed are poured onto a panel set at a certain degree. Then the vibration mechanism is started. Under its influence, as well as due to the natural force of gravity, the material is gradually sieved and enters the next pallet, designed to collect the processed raw materials.

Particles that have not passed the screening can be easily removed from the top panel by turning it over to the other side.
The shaker is best suited for dry or semi-dry material. It is recommended to sift wet raw materials using a drum installation, which operates on the principle of a centrifuge.
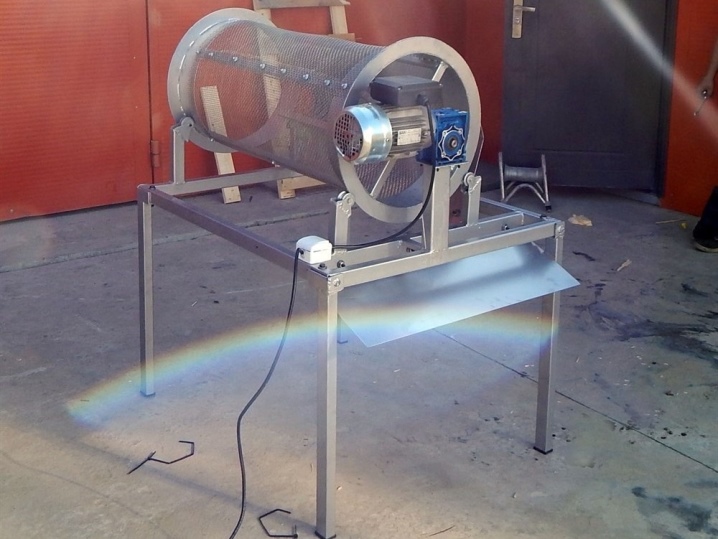
Views
The vibrating sieve can be round or rectangular, and there are different types of sizes. Some sifters have a more complex layout and allow for multilevel cleaning - for this, additional sieve panels are used. The main parameters that are taken into account when choosing a device are:
-
overflow height - the distance from the base of the structure to the place where the substance falls on the pallet;
-
sieve area;
-
the strength of vibrational vibrations.


Despite the fact that the principle of operation of the devices is similar, there are several varieties of these devices.
By the type of grids to be installed
There are two types of sieves:
-
under the tension mesh - the owner must mount it himself;
-
with wireframe or pre-installed - it is installed at the factory, the device comes to the user completely ready for use.

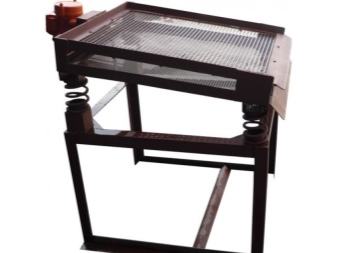
After the 2000s, most manufacturers make devices with wireframe meshes. They have several advantages:
-
material is distributed more evenly on the pallet, accordingly, the sifting capacity increases, which allows you to optimize and speed up the work process;
-
factory setting guarantees tension quality, while an inexperienced user can out-pull or under-pull the network;
-
the device is ready for use, it does not require additional configuration.

Options for a stretch mesh can also be found on sale, but there are not so many of these models, so the choice will be limited.
By the number of cleaning levels
The design can include a different number of panels, usually from 1 to 3 pieces.
-
Sibling sifters are the most common. They have a simple yet reliable design. Since there is only one panel and is visible, the user can control the screening process, as well as monitor the state of the mesh - appearing defects are easy to notice.
-
Two-tier devices help to save floor space in the workshop. They allow you to process more raw materials, while taking up less space.
-
Three-tier devices can be different.Some are used to save space, by analogy with two-tier ones, only in this case one more tier is added. And there are also models with a more complex design, providing several stages of cleaning - from coarse to finer.



Three-level sieves make it possible to carry out the main screening at the first stage, and then add clogging additives. Such components are used in the manufacture of concrete mortar - these substances help to avoid the appearance of pores in which moisture can accumulate. After enrichment, the mixture undergoes a finer purification at the third level. Various mesh sizes are used at all stages to ensure high-quality screening.

By type of vibration
Vibration can be applied to the device in a variety of ways. Depending on the method used, the screening rate and quality will vary, as well as the level of load and wear on the mesh. There are several types of vibration waves.
-
Unbalanced elliptical. These vibrations can be obtained with a single engine located outside the frame's center of gravity.
-
Circular... The engine is located exactly in the center of the vibration frame, which allows for more uniform and smooth vibrations.
-
Linear... In this case, two motors are used, rotating in different directions during operation. They can be on the sides or on top.
-
Balanced elliptical. Two or three motors are involved, depending on the applied circuit.

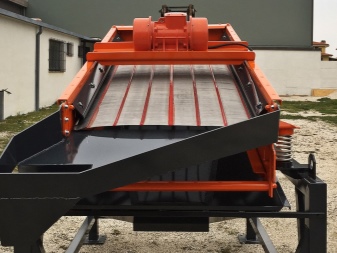
The best option is selected in accordance with the production goals and the characteristics of the sifted materials. Each method has its own advantages, for example, linear oscillation allows for increased throughput, and when using balanced elliptical, the working network will last longer.
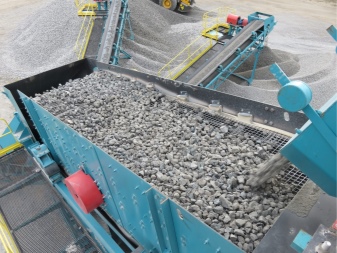

Applications
Sieves are used for sifting components and cleaning bulk materials - sand, silicon, cement and others. Vibrating devices are indispensable during the preparation of the drilling fluid required for cleaning wells while drilling. And also the devices are in demand at factories engaged in the production of PVC products - with the help of a sieve, a mixture for powder painting is obtained.



The variety of industrial and laboratory models allows you to process all kinds of substances - from chemical mixtures to food.
Food
Depending on the specifics of production, vibration installations are used:
-
for sifting spices, cleaning them from debris and large particles, obtaining a homogeneous mixture;
-
in the manufacture of egg powder Is a common ingredient found in various foods;
-
during milk powder productionto get a homogeneous mass;
-
for sorting nuts, seeds and cereals in fractions in accordance with standard sizes;
-
for sifting coffee - in powder or granular form.

And also vibrating sieves can be found in factories producing dairy and cheese products, chocolate products, sugar. Sifting not only helps to get rid of large particles or debris, but also helps to remove excess moisture.

Pharmaceutical
The industries in this industry usually have high hygienic requirements, therefore the equipment must meet the required standards. Vibrating screens can carry out sterile filtration, including under pressure, sieving, separation. With the help of these devices, various vitamins and food additives are made, protein substances, silicon dioxide and other components necessary for the creation of medicines are obtained.
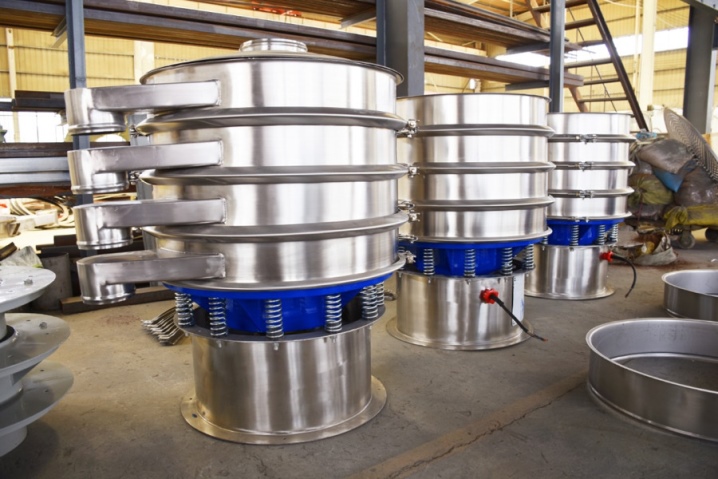
Chemical
Various fertilizers are often produced in powder form - they are obtained by sifting through a vibrating sieve. These can be compositions based on potassium or phosphorus compounds, as well as nitrogen.In addition, in the chemical industry, devices are involved in the production of carbon black, silicon, in the manufacture of various types of PVC.

Mining
Minerals extracted from the bowels of the earth require processing - it is necessary to sift them, divide them into fractions, and reject waste rock. For these purposes, vibrating sieves are used. They clean coal, bentonite, gypsum, limestone, sand and other loose substances.
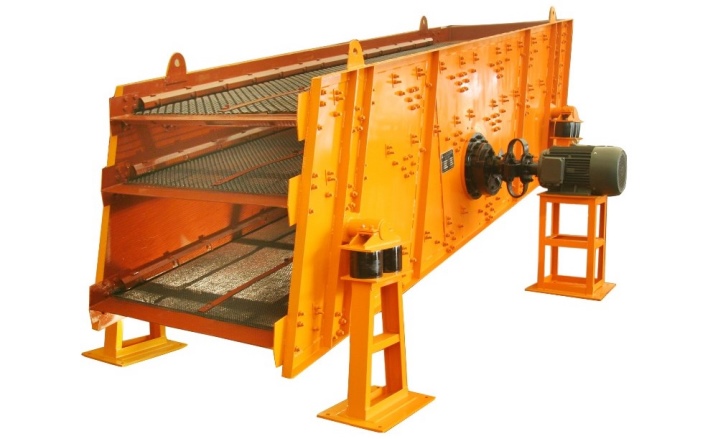
Oil producing
Screens play an important role in the separation of oil sludge - this is industrial waste containing various impurities that should not get into a clean product. In addition, devices are needed for the production and purification of drilling fluids.

Paper
Screeners are in demand in the pulp industry - they can be used to divide chips into fractions, remove excess impurities, clean and prepare reagents. Vibrating screens are used for the production of wood and technical cellulose.

Ceramic
There are many bulk materials used in this industry that are difficult to obtain without the use of a vibrating sieve. It is used to process:
-
sand;
-
gypsum;
-
cement;
-
quartz;
-
alumina.

The vibrating sieve is a wide-ranging tool. An extensive classification allows you to select a model for the intended purpose, depending on the needs of a particular industrial sector and the specifics of production.
The comment was sent successfully.