We make a vibrating plate with our own hands

During construction work, it is often necessary to compact concrete tiles, backfill or soil. In this case, you cannot do without specialized equipment. If we consider private construction, it is often associated with problems regarding subsidence and deformation of the laid foundation.
Not everyone can buy a ready-made unit due to the rather high cost. If you have minimal skills in working with welding inverters, various locksmith tools, you can create a self-propelled vibrating plate yourself. This significantly saves money, and the result will certainly be positive. The description of this process is just given in our material.


Features of homemade models
Self-made units are equipped with a power device, through which the main work is carried out. In practice, 2 types of engines are used.
- Soil compaction machines, complemented by a diesel engine. They will become appropriate when it is necessary to exert a lot of effort, but they are rarely used in everyday life. Nevertheless, you can find vibrating plates in personal plots, in which there is a two-stroke motor from a walk-behind tractor.
- Gasoline-powered devices are autonomous, but they make a lot of noise during operation. It is recommended to select the "heart" of the unit with low power and economical.



In general, the recommended power is 1.5 to 2 W at 5000 rpm. At a lower value, it is impossible to achieve the required speed, therefore, the output vibration force will not be normal.
The best solution may be an electric model, which is easy to assemble on your own. To use such a unit, electricity is supplied to the place of compaction of the soil.

The indisputable advantage is the absence of emission of harmful gases. There is a generally accepted classification by weight:
- lightweight structures - no more than 70 kg;
- heavy products - over 140 kg;
- medium in severity - in the range from 90 to 140 kg;
- universal products - within 90 kg.


As for the first category, it is suitable for work in the local area, when the pressing layer does not exceed 15 cm. Universal installations are suitable for compacting a layer of 25 cm. Weighted models cope with layers of 50-60 cm. It is important to correctly determine the type of electric motor. A weak specimen on a massive slab will simply sink into the soil. The best option is 3.7 kW (no more than 100 kg of the processed substance).


Manufacturing
The main part of the vibrating plate, which is created by hand, is the base made of durable metal. There are samples based on cast iron or steel, but their use in everyday life is not justified. If we consider cast iron, it is rather brittle, it can crack, and it is difficult to weld. Most often, a sheet of steel is used, the thickness of which starts from 8 mm. In order to increase the mass, heavy parts are mounted on the prepared base. These include the shaft on two strong bearings, on which the load is fixed in the longitudinal plane. While rotating, this part exerts a compelling force under the action of inertial force and its own weight. This creates short-term, but frequent loads on the soil.



It is important to create a drawing of the vibroblock before designing it.The efficiency of the device depends on the speed of the rotating shaft, the area of the entire base, and the mass.
If the stove is very large, do not rely on increased pressure. The fact is that the weight is evenly distributed over the entire surface with minimization of specific pressure.
A base of small size shows increased efficiency, but its action will become point or selective. Such work will not provide uniform compaction over the entire treated area. If we consider the eccentric shaft, during its rotation there is a significant load on the existing structural elements for compaction of the soil. The increased vibration will destroy the vibrating plate, which you managed to make yourself. As a result, a negative effect is transmitted to the motor, the employee's well-being.


Tools and materials
First of all, you should consider the installation and pre-selection of the engine. It is usually installed at the rear of the unit, on the base. As already mentioned, gasoline, diesel, and electrical devices are used. When choosing the right option, the following factors are taken into account:
- financial opportunities;
- the specificity of the use of the plate;
- the ability to supply electricity to the work area.



A kind of gasoline vibrators for solid substrates are characterized by independence from electricity. Their convenience is determined by the ability to operate in remote areas, in the steppe, on a vacant lot.
The peculiarity lies in the constant availability of spare fuel. Its consumption depends on the power of the motor used and the duration of operation.


If we consider, for example, an electrical installation made independently on the basis of a motor from a washing machine, it is limited in movement by the existing connecting cable.
Among the main disadvantages of the motor, a regular rotational speed stands out, as a result, the network is overloaded due to the increased starting torque. This problem can be eliminated by using the controller for soft start. It is designed to avoid electrical or mechanical overload.


During self-assembly of the vibrating plate, damping pads are often installed under the engine. This significantly reduces vibration, prevents premature destruction of the unit from mechanical stress. The option of using ready-made motors from a walk-behind tractor or a perforator, a cultivator is possible.
As for the work plate, it is usually represented by a metal sheet, the thickness of which also affects the rigidity of the product. As a standard, a surface from 8 mm in thickness is used, the average dimensions of which are 60 * 40 cm, but other variations are often used. The back and front areas on the slab are slightly raised for easy movement.



If we talk about the frame, it acts as a reliable support for the eccentric vibration shaft and the engine, often made from a channel. Such a part is at the same time an additional load, providing increased efficiency in the performance of the assigned tasks.
The frame also enhances the strength and rigidity of the entire base, capable of absorbing mechanical loads transmitted by the rotor shaft.

Such a do-it-yourself detail may be different. She (to give more weight) is often made from a rail. At the same time, it should be understood that the vibrating plate will periodically have to be manually moved to the storage room, which creates additional difficulties.
An important functional element is the vibration mechanism. Structurally, it can be of two types:
- unbalanced is characterized by imbalance in relation to the axis of movement of the rotor;
- planetary, in which energy from moving parts moving along given paths of a closed type is used.
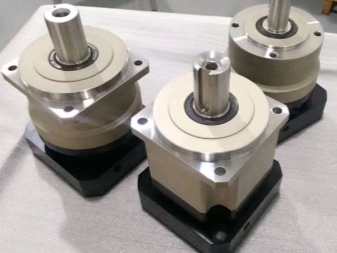

Considering the last mechanism, one can understand that its creation at home is not advisable. This procedure, like follow-up care, is challenging. The choice in this case remains with the unbalanced device. A drive belt connects the motor to the eccentric rotor. For this purpose, these parts are equipped with pulleys that occupy one vertical plane. They are able to adjust gear ratios, vibration frequency.

Of the additional details, three more can be distinguished.
- The carrier or the handle that controls the installation in the working process. The handle is made in the form of an elongated tube bracket. It is attached to the plate by means of a hinge joint, compensates for some of the vibrations and provides protection to the worker.
- Trolley for moving the unit. The trolley is a separate device, it can be made in the form of a structure with rigid fasteners. It is neatly placed under the plate, which is slightly tilted by the handle, then transported to the designated place.
- Tensioning mechanism. It is necessary to create tight contact between the pulleys and the drive belt. The roller should be supplemented with a groove with a mat, identical to the same groove on the pulleys. This prolongs the life of the belt. When the roller is positioned on the outside of the vibratory plate, it should be sized to fit the back of the belt. The tension is carried out with a special screw, which helps to tighten the belt for work or to release it when servicing or replacing.
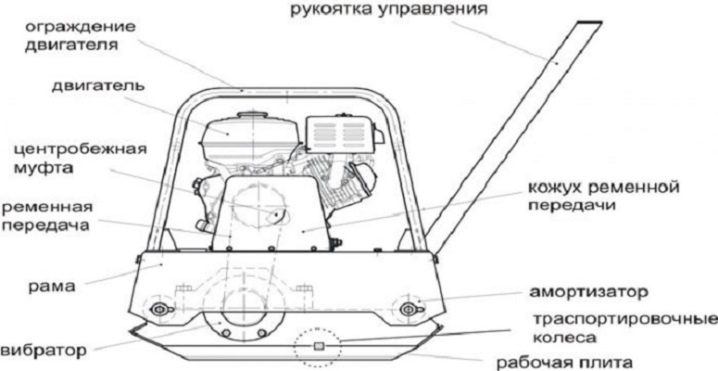
Assembly stages
A homemade vibratory plate is not so difficult to assemble. The main thing is to adhere to the sequence of stages.
- The slab is cut with a grinder. Its parameters are selected individually, taking into account the planned work. The average is 60 * 40 cm.
- At the front edge, incisions are made every 7 cm, at the back - every 5 cm with a depth of 5 mm. Along these incisions, the edges are tucked up 25 degrees. This will prevent the surface from sticking in the ground.
- Two sections of the channel are attached to the upper part, which only strengthens the edges and the base itself. It is important to keep them in the same plane.
- Holes are made in the rear of the channel through which the motor is fastened. If the case requires it, a metal platform with already existing holes is welded onto the proposed place.
- Installation of the engine involves the use of rubber cushions.
- For the purpose of fixing the handle, lugs are mounted.
- A rotor with an eccentric is produced separately, after which it is placed in a finished form on a plate. Structurally, it is represented by a shaft, which is located in the through and blind hubs. The pulleys must be on the same level, otherwise the drive belts will often fly off.
- As for the tension piece, it should be located in an easy-to-use area on the frame. This is most often the area between the pulleys where the belt sags most. The idler pulley must be in the same plane as the pulleys.
- A protective cover must be placed on the rotating rotor to prevent injury.
- The handle is mounted, after which a test run is carried out to determine the quality of performance. The identified problems are eliminated, corrections are made.



When the plate compactor is completely assembled, it can be used. The first time you try, you may not get the expected result. But when the detected shortcomings are corrected, the unit starts to function in standard mode. The main setting is to find the optimal values of the eccentric and speed mode.
A homemade stove will in any case show a better result than if the backfill was tamped manually.
In the process of application, the resulting design can be improved, in this form it will be worthy to compete with an industrial design.
The main feature of self-made units is the possibility of changing them, transforming the design, adding new accessories. This will not work with ready-made installations, they are made in such a way that there is no possibility of making adjustments.

Operating tips
The vibroblock, related to technologically complex units, must undergo a thorough inspection before use. It is imperative to comply with safety regulations. Industrial devices usually come with instructions. But in the case of a homemade installation, you need to take into account some features during application.
- Immediately before switching on, a person must make sure that all fasteners are strong, that the working parts are correctly installed. A particularly thorough inspection is carried out when the cooker is first started up.
- The spark plugs in the gasoline engine should be cleaned periodically. They must always be checked and the resulting deposits removed. This prolongs the "life" of the engine, and the vibrating plate will function for many years.
- The oil in the engine is periodically changed, and its level is checked before each start and at the end of work, when all the parts are still very hot.
- The motor filter must also be periodically cleaned. In general, all parts of the structure should be kept clean, which ensures its continued use.
- Refueling of the described device is carried out only when the engine is off. Otherwise, the person puts himself in great danger.
- It is highly discouraged to use a self-made installation in relation to hard soils, it can be concrete or asphalt. Damage may occur due to increased vibrations.

Fast and high-quality implementation of labor-intensive measures for the processing of bulk substances is possible only when using reliable vibrating plates. The effort expended on the manufacture of such an installation will pay off in the process of its use.
How to make a vibrating plate with your own hands, see below.
The comment was sent successfully.