How to make a vibrating table for paving slabs with your own hands?

For the manufacture of paving slabs, it is very convenient to use a vibrating table. This unit can be made independently and made at home. This helps to reduce costs for creating not only blocks for paths, but also for other finishing elements. When making a do-it-yourself vibration casting table, you can use inexpensive improvised means.


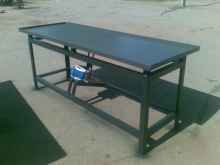
Tools and materials
Before you start creating a vibrating table for the manufacture of concrete and other products, it is worth considering in advance what materials to use for this and what tools you may need.
-
Metal - This is the main material for a table designed for vibration casting. A sheet version with a thickness of 0.3 cm or more is best suited. It is advisable to take into account that the larger the countertop area, the greater the thickness should be preferred.
-
Angles or channels for the bed. It is important to remember that for the table, all the basic elements must be metal, as this is called for by the specifics of its work.
-
Metal springs that provide mobility of the vibrating table. The size of these elements must be selected so that they correspond to the mass of the finished device and the load from the cast molds.
-
Welding machine will be needed to connect all metal parts.
-
Electric drill and drill setdesigned for metal to make holes of the required diameter.
-
Grinder with disc for cutting metal products and a grinding disc.
-
Measuring tape or ruler will allow you to quickly and accurately make all the necessary measurements.
-
Spanners for bolting.
-
Bolts for fixing the electric motor to the table.
-
Primer, paint-enamel or other anti-rust agent to prevent rust.
-
Marker for marks.
-
There are several options for fixing to the floor. Firstly, using cement mortar and special depressions. In this case, sheets of metal are welded to the ends, and then deepened by 100 mm. Secondly, using anchors that are poured into the floor. It is to them that the table is attached. This option is convenient because, if desired, you can easily disconnect the unit and move it to the desired location. The third method is fastening to tires, which implies their installation on top of each other. To make such a structure made of tires stronger, you can connect them inside with bolts. Moreover, even the motor can be installed in the tire, if you place it on the bottom of the working surface on the channels.
-
The vibration motor is most often selected for domestic use with low power. The simplest option would be a 220 W washing machine motor. It is quite enough to ensure the normal operation of a table with dimensions of 70 by 70 centimeters.
For larger installations with dimensions of 180 x 80 centimeters and for the production of a large number of products, it is necessary to look for other engines, for example, with a higher vibration frequency of the IV-99E type. Such an electric motor must be connected to a dedicated line using a wire of a special section. Typically, the power consumption will be 500 watts. You can also use single-phase models that differ in power, rated voltage, service life.




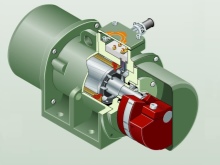

If desired, you can create a vibration drive from a conventional electric drill. It is taken as a source of vibration waves and attached to a piece of reinforcement, fixed in a vice.
-
Paint brush for painting.
-
Sandpaper for stripping before painting.
-
Springs or suspensions.
-
Metal tube for glasses for springs.



Step-by-step instruction
Before making a vibrating table for the production of paving slabs with your own hands, you should understand how it works and what is its principle of operation. The main surface, which is a working surface, is attached to the base using special springs. This is the case if the table is made with horizontal vibration. In the version with vertical springs are replaced by hangers.
When an electric motor of a suitable power with an eccentric on the shaft is turned on, the tabletop begins to vibrate. The required frequency of movements is achieved by shifting the center of gravity. To make it more convenient to work with the table, it is worth considering the height of the legs on which the base is placed.
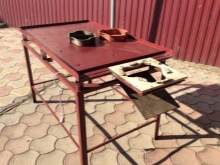
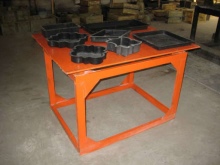

The first thing to start with before making a table is to draw up a complete drawing that takes into account all the nuances. It is important that the diagram includes the dimensions of each part. If a beginner will make the device, then it is better to choose a simple version of the vibration table, which is easy to assemble and maintain. The more complex design is for people with experience. As a rule, it is equipped with additional functions.
Before proceeding with cutting, it is worth measuring everything again so that all the elements fall into place exactly. Drawings usually start from the bed. It is important to take into account the height, how it will be attached to the floor, the size of the working surface. It must be understood that the springs will be located at the corners, as well as at the main points of the vibration device.
Think in advance where the engine will be located. It is desirable that it be as close to the center of mass of the vibrating table as possible. In this case, the eccentric must be located either on the shaft of the electric motor, or on the drive immediately in the center. Also, the number of forms for paving stones is immediately taken into account. You can get ready-made tiles at home simply by hand or using the molding version of the nozzle.



Slicing
The optimal size of each of the elements must be entered into the drawing, and it will be according to which the cutting will be carried out. The required production volume determines the size of the vibrating table. Its surface area will depend on the number of manufactured elements at a time.
The height of the bed should be determined by the height of the person who will work behind it. It is important here that it is comfortable. Usually 90-95 centimeters are taken for the average height. For blanks, it is advisable to use a pipe with a diameter of 6.5 cm and projections in the form of 4.5 cm corners.
The next point is cutting the countertop itself. It is better to make it from a sheet of metal, but it is also possible from a sheet of plywood with a thickness of 1.4 centimeters or more. Next, you should prepare the springs in the amount of 10 pieces. It is important to ensure that they are all the same length.
You should also prepare glasses. As them, you can use pipe sections, in which the diameter will be a couple of millimeters larger than the spring girth.
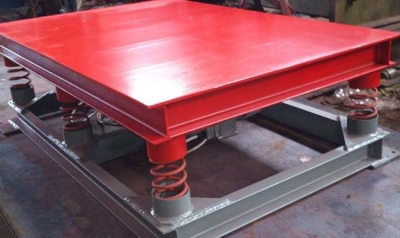
Connecting elements
Fastening of vibration table elements is carried out using welding equipment. The bolts should not be used, as they loosen over time under the influence of vibration waves, reducing the rigidity of the supporting structure. This type of connection is suitable only if the structure is collapsible. Of course, in this case, you will have to constantly monitor and, if necessary, tighten the attachment points.
In this case, it is important to control yourself in what position the table legs are. It is also worth monitoring the density of the support on the table and the presence of a plane. When the bed is ready, a rectangular strapping is welded around the perimeter. A corner is best suited for this, while you need to control the plane.
Next, you need to attach by welding the springs to the corners of the bed, in the middle of the short sides (one at a time) and at an equal distance from the corner along the long sides (two). On the underside, the glasses should be fixed so that they correspond to the location of all the springs. After that, the vibrating table top is welded.

Welding channel
A homemade vibrating table must be properly equipped with an electric motor. It is important that the motor mount is rigid. To do this, weld 4 corners from the bottom of the tabletop... The fastening is made very strong and exactly in the middle of the slab. With a poor connection, the vibration motor will be exposed to excessive vibrations and will quickly fail.
At this stage of work, care should be taken of the eccentricity of the engine, or rather, its violation. This can be done by drilling a hole in the motor shaft and tapping eight. Now you need to take the corresponding bolt, and then screw it into the motor shaft. In this case, the longer the bolt length, the better the vibration will be on the plate stripping table. This procedure is necessary, since the engine cannot simply create the desired vibration.

Spring fixing
In order for the springs to be firmly fixed and not transmit vibration to the bed, they must be additionally secured with rods. Such guides must pass through them and join to the bottom of the glasses by welding. You can additionally put a layer of thick rubber under both sides of the spring. This will further reduce vibration.
Long bolts can be made as guides. Thus, the springs will receive a stronger tension, as nuts and washers are screwed onto them. It turns out that the table is better fixed and the vibration amplitude is limited.

Finishing
When the vibrating table is fully assembled, all that remains is to install the electric motor and make sure that all the wiring is correctly connected. To automatically adjust the engine speed and, accordingly, the vibration frequency, it is worth additionally installing a potentiometer. The higher the current supplied to the motor, the stronger the vibration will be. It is very convenient when the table is made mobile, so the main part of the electrics is mounted on the base, and only an extension cord is supplied to the bed itself. Do not forget about mandatory grounding.
The final stage in the manufacture of a vibrating table is painting. You need to start with preliminary cleaning of metal surfaces. For this, a grinder is best suited, and then sandpaper. Particular attention should be paid to welds, as they are most vulnerable to corrosion.

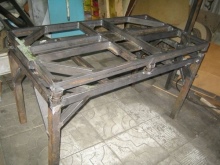

Painting is best done with special paints, for example, primer enamel. It is important that it is recommended for metal products and protects against rust. In this matter, you should not save money, but it is advisable to give preference to quality products from well-known companies. It is worth noting that both foreign and domestic manufacturers have good paints.
When painting, after applying the first layer, it must be allowed to dry completely. Only then is the second layer of paint applied. If desired, you can also apply a third one so that the vibrating table is as protected as possible.
Tile production tables can be supplemented with various devices. For example, they are often equipped with a sand sifting unit. In this case, a cover is made for the electric drive from a casing, which serves as a sheet material.



A funnel made of thick fabric or galvanized metal is placed below. As for the vibrating platform itself, it is replaced by a grid.
How to make a vibrating table for paving slabs with your own hands, see the video below.
The comment was sent successfully.