How to make a lining with your own hands?
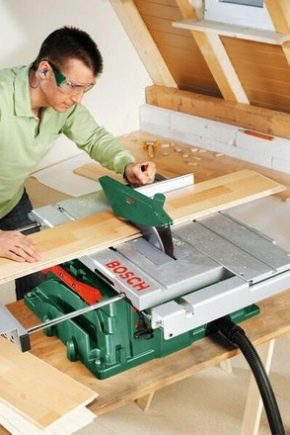
Making lining at home is suitable exclusively for those who have a lot of free time at their disposal, have patience and perseverance. From this article, you will find out the smallest details of its manufacture with your own hands, while significantly saving your budget, since the discrepancy in price between the clapboard and the unedged board is significant. The positive aspects of using lining are visible to the naked eye: this is, first of all, the low cost of the material itself, and since the installation process is extremely simple, there is no need to hire a work team, you can cope with your own efforts.
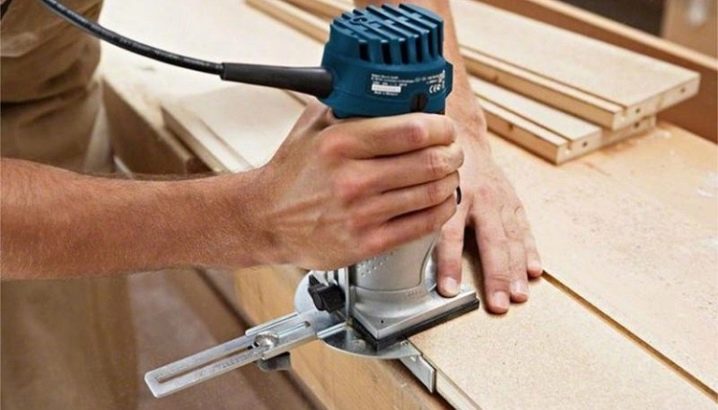
About the material
Before you start making lining, it is recommended to understand what material you are dealing with. This knowledge will be useful for making the best decisions on your own while working at home.
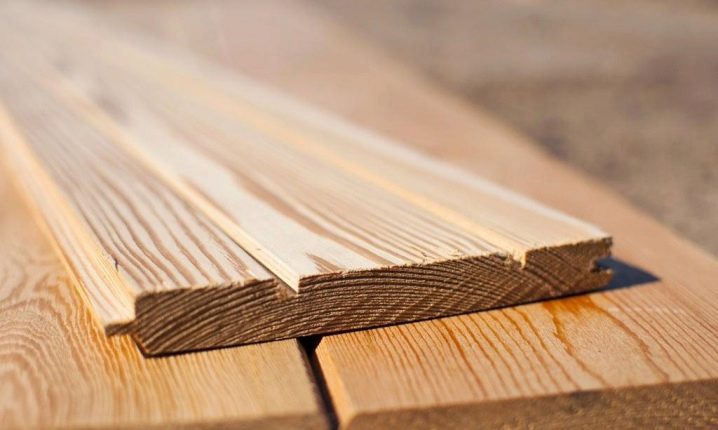
The process itself takes place in several stages.
- Board production. The whip is taken as a basis - the trunk, which has already been cleaned of the root part and knots. With the help of a band or disk sawmill, the whip is cut according to the specified parameters. An approximate value is taken for the thickness of the board within fifteen millimeters, and for the width one hundred millimeters.
- Drying of lumber. Fresh wood has a lot of moisture. During transportation, sawing or storage, it can consume or accumulate moisture in its composition to a greater or lesser extent. In addition, wood is a hygroscopic material, that is, it is capable of absorbing water vapor from the air. For construction applications, maximum dry wood material is required. In order to reduce the amount of waste, moisture and minimize the risk of board cracking, this step is extremely important.
It takes place in a specialized chamber drying.
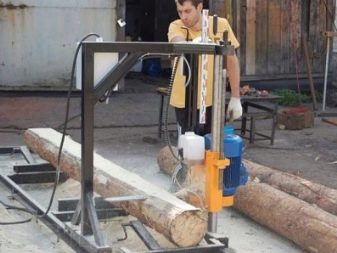
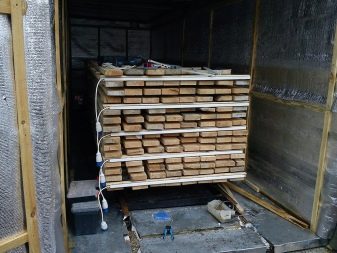
- Sorting. The lumber is sorted according to quality. For the production of lining, a board is selected with a quality not lower than class B (second grade). The grade difference is based on the external defects of the board, their presence or absence.
- Lining production. At this stage, a powerful four-side planer is involved. Thanks to various cutters and knives, up to four planes are processed at a time, that is, the desired profiles are obtained in two minutes.
- Quality control, placement and storage. This completes the process of obtaining lining in production. This is a routine job and does not imply complexity if you have the necessary equipment. To preserve the qualities of the lining, the correct creation of a place for storing this material is required. A dry, level room with an installed canopy, it is possible to use a regular film covered over the boards. It is important to provide systematic ventilation.
It is advisable to pre-install pallets.
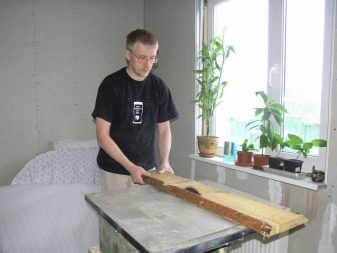
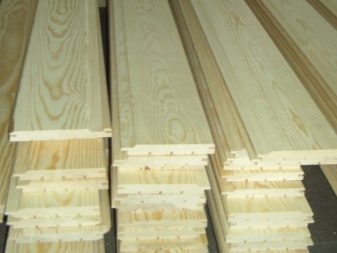
Where is lining used?
There is no need to list all the positive aspects of the lining. In building materials stores, it is the most demanded material for decorative and finishing work with walls and ceilings, it is used both inside and outside. The lining is made from different types of wood, which is why its further use is connected. For example, linden or alder is used in the wall cladding of saunas due to its moisture-proof properties and resistance to sudden temperature fluctuations.
Spruce and pine lining is used mainly for interior decoration due to low humidity and stable temperatures from two to thirty degrees.
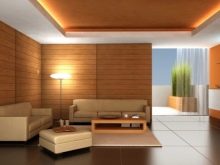
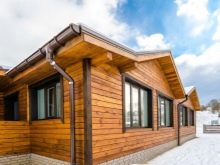
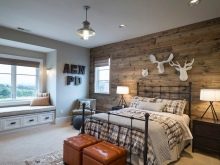
Necessary equipment
First you need to select and prepare for work a large and powerful machine. The second machine will be a practical purchase. Due to the fact that even the most powerful machine after a certain period of time will begin to overheat, allowing it to rest and cool down will be a mandatory working moment. The required characteristic of the machine is a power not lower than one kilowatt. It is required to perform two main functions - this is sawing and jointing, that is, leveling the wooden surface.
When giving preference to any model, draw attention to the presence of backlash - clearance, in places where parts are adjusted. A high-quality woodworking machine, for example, an American, does not exceed a width of fifteen to twenty centimeters. But also the rulers and the cooling system should be of high quality.
Do not give preference to a machine with an aluminum table and ruler.
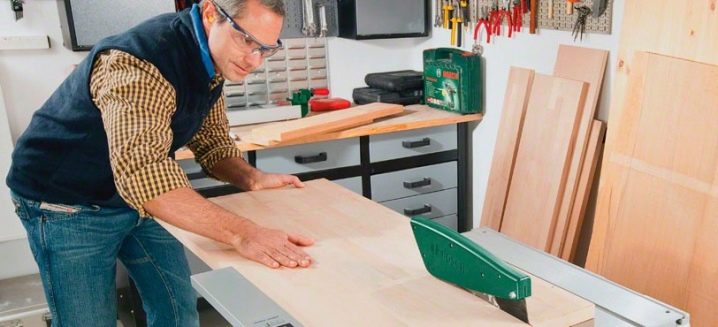
Aluminum tends to leave black marks on wood. It is possible to apply stripes to the finished product with a jigsaw. As a result, defects adversely affect the appearance of the material after processing, and the finished lining must be painted when colorless varnish could be dispensed with. For the operation of the saw, a specialized cover is intended, which is put on the base of the saw in order not to stain the wood, when both the table and the ruler do not have protective devices.
You can make alder lining by hand, for example, with a milling cutter or on a circular. The milling method is of higher quality.
The homemade material made in this way has good technical indicators.
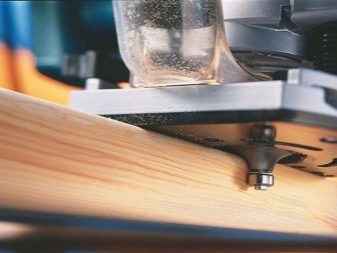
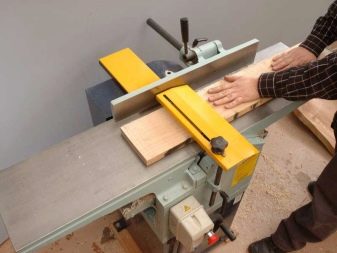
Lining dimensions
First of all, you need to choose the right size for an uncut board. The required length is set based on the average length of the boards at your disposal and on the required length. Lining more than two meters long is extremely difficult to process, and therefore this kind of length is economically unprofitable. But by and large, any length can be used effectively.
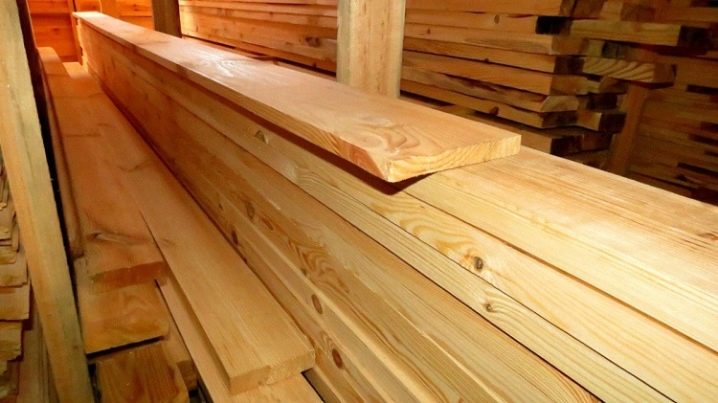
The most unpretentious-looking board, which sometimes goes straight to the trash, can be transformed into a beautiful DIY parquet. It will save your pocket from unnecessary costs and will delight your eye no worse than purchased in the store. Then you need to determine the width of the lining. With a narrow board, the lining will come out wide, that is, one lining - one board. With a wide board - two narrow lining.
Many experts argue that the use of a lining with a width of seven to ten centimeters is many times more practical. Do not forget that the lining you are using must be the same width.
Quality material is produced, for example, by this method. like brushing.
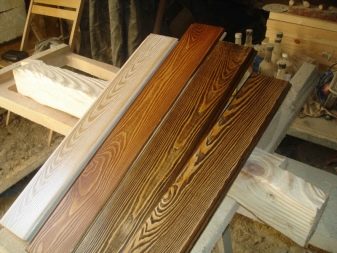
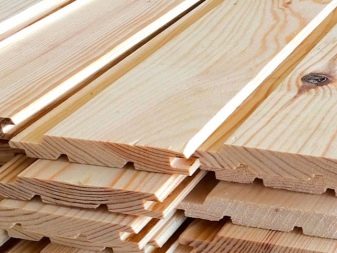
Making lining with your own hands
Safety is the first thing worth mentioning. In no case is it recommended to wear clothing with decorative details. A comfortable simple robe without unnecessary elements is the best option. Wear safety goggles if possible. The saw should be in a special cover with a riving knife, which will make it easier for you to cut and at the same time protect you when using the machine. Monotonous work often lulls the vigilance of the worker, and in this case there is a possibility of accidentally sawing something that was not required. Therefore, watch out for overheating of the motor.
To do this, cut the boards in batches first on one side, and only then grab the other.
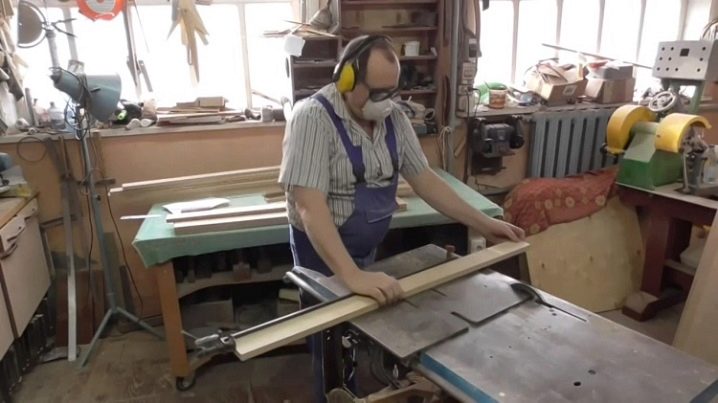
The process itself begins with drawing straight lines., along which the sides of the boards will be sawn later.It is recommended to use pencils of green or blue color, this is necessary so that the lines are clearly visible, in case the wood is damp and starts to turn blue. To cut the board, we lay it on the table top of the machine so that the lines marked earlier are even. Place an emphasis on the end of the board with your body and push it straight onto the saw blade. Many people buy a saw blade in order to simplify the cutting process, preferring circles with a large diameter.
At the same time, it is important to keep an eye on the board, it should not pinch the circle.
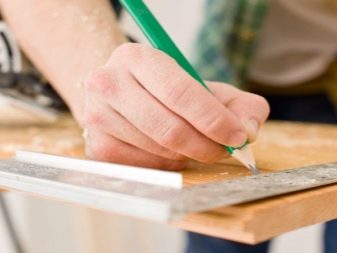
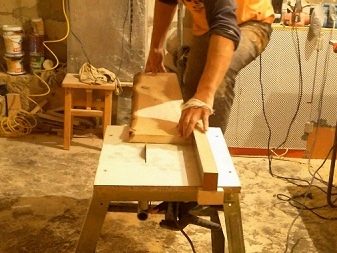
To cut the other side of the board, the machine must be reconfigured. To do this, set the ruler to the required width. It is common practice to use two clamps to hold it in place during processing. Then the second side of the board is cut along the adjusted ruler, when the side is cut without using the ruler, the sawn under the ruler will appear at the exit. Put them in a separate place, they will come in handy for the slats.
For those who are interested in how to determine the width of the slats, the answer is simple; for this, a sawn-off lining is placed, which will be used instead of a ruler.
It makes no sense to find out the width to a millimeter, since this will not affect the quality of the lining.
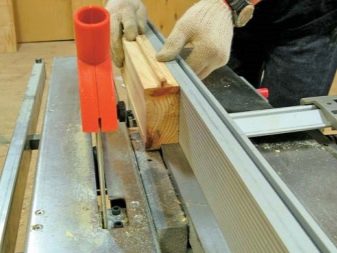
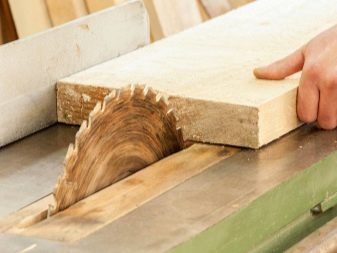
Jointing boards
The board becomes even and smooth after the jointing procedure. This is an extremely important stage and requires equal attention and concentration. To do this, the machine must be reconfigured again. Planks are planed one after the other, strictly from one side. Boards that have curled up in the process of planing into a spiral are immediately thrown away, because they are no longer subject to further use. To get even and equal boards in width, count how many times it took you to slide over the machine and repeat the same number with each new board, applying the same force.
When working on the other side, slight differences in thickness will not be noticeable.
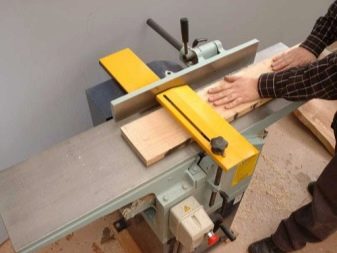
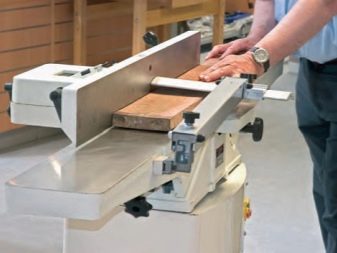
At the end of the processing of the board, it is required to make grooves. They are obtained using cutters or a small-diameter saw blade, but it is necessary to install it obliquely. It is worth using it only if you do not have cutters available, since the method is quite laborious, additional equipment adjustment is required.
The first thing to do is set up the ruler., to do this, raise and lower the table until you set the required depth for the groove. After that, cut out the grooves on both sides of the board. There is no need to cut grooves strictly in the middle of the board, making the groove a little closer to the surface - visually there is a feeling of a thinner lining than it really is.
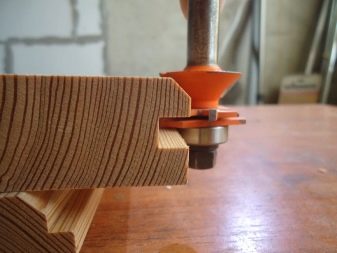
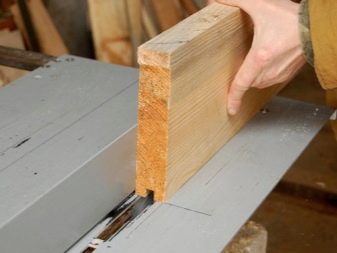
Implementation of residuals in reiki
The previously unrealized boards, which were put aside, will be transformed into slats, which will be used to fix the lining during its installation. As a joint material, the batten does not have to be the same length as the lining. The length in this case does not matter, since the joint is hidden behind the clapboard. But the rail should be smaller than the groove.
Due to the curvature of the rail, it will be perfectly fixed in the grooves, in this regard, it is not planed, with a high-quality saw, the rail turns out to be quite smooth.
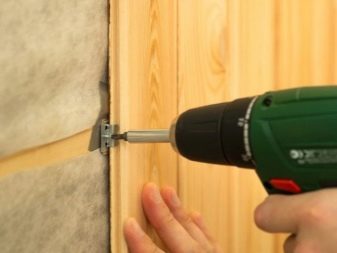
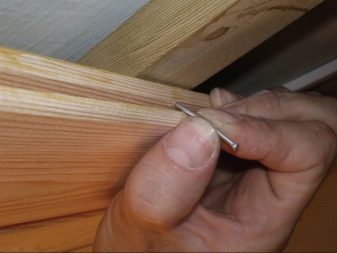
If appearance is your top priority, remove small chamfers on both sides of the board. It will take a lot of time. But by doing this, the result will immediately be striking. The service life of the lining is approximately fifteen to twenty years. Provided that it is treated with a specialized protective agent against fungus, rot and insects, the durability of the lining increases significantly.
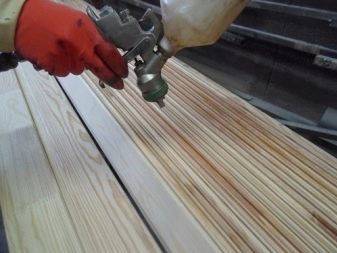
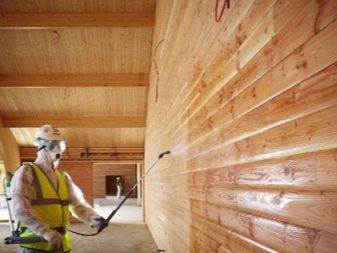
The lining made at home will save your pocket from unnecessary expenses, will give the room a more aesthetic and attractive look. Do not forget that the lining is a material with a high thermal conductivity and is an environmentally friendly material, which means that it will not emit harmful toxic substances at high temperature jumps.
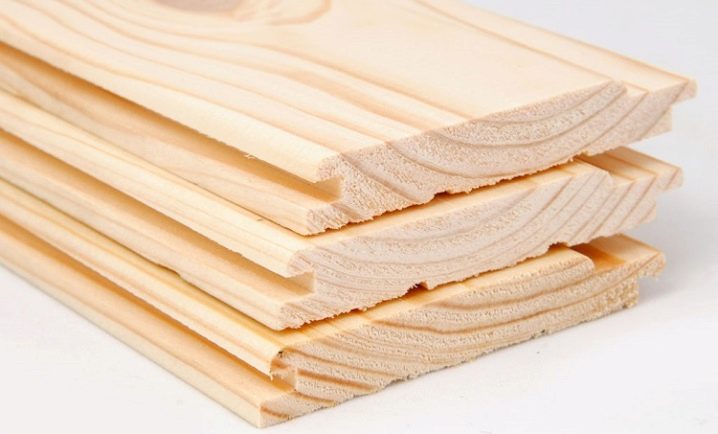
You can find out more information on this issue by watching the video below.
The comment was sent successfully.