Insulation of a house from aerated concrete: types of insulation and installation stages

Buildings made of aerated concrete or foam blocks, built in temperate and northern climates, need additional insulation. Some believe that such a material itself is a good heat insulator, but this is not so. Therefore, it is worth considering in more detail the insulation of a house made of aerated concrete, the types of thermal materials and the stages of installation.


The need for insulation
The popularity of gas silicate blocks is due to a number of reasons: they are light, with a clear rectangular shape, do not require the construction of a powerful foundation under the house, and even a novice specialist can cope with their installation. Installation of a building made of such material does not require the same qualifications of a bricklayer as a brick house. Foam concrete blocks are cut easily - with an ordinary hacksaw.
The aerated concrete block includes a cement-lime mixture, a foaming agent, which is most often used as aluminum powder. To increase the strength of this cellular material, the finished blocks are kept under high pressure and temperature. Air bubbles inside give a certain level of thermal insulation, but you still have to insulate the building at least from the outside.
Many people believe that to protect the outer walls from cold and moisture, it is enough to simply plaster them. The plaster will perform not only a decorative, but also a protective function, it really retains heat a little. At the same time, in the future, many face problems.


In order to answer whether it is necessary to insulate buildings from foam concrete, you first need to take a closer look at the structure of the material. It contains cells filled with air, but their pores are open, that is, it is vapor-permeable and absorbs moisture. So for a comfortable home and efficient use of heating, you need to use heat, hydro and vapor barrier.
Builders recommend erecting such buildings with a wall thickness of 300–500 mm. But these are only norms for the stability of the building, we are not talking about thermal insulation here. For such a house, at least one layer of external protection from the cold is required. It should be borne in mind that according to their thermal insulation characteristics, stone wool or foam slabs with a thickness of 100 mm replace 300 mm of aerated concrete wall.
Another important point is the "dew point", that is, the place in the wall where the positive temperature turns into negative. Condensate accumulates in the zone where zero degrees, this is due to the fact that aerated concrete is hygroscopic, that is, it easily passes moisture. Over time, under the influence of temperatures, this liquid will destroy the structure of the block.
Therefore, due to external insulation, it is best to transfer the "dew point" to the outer insulating layer, especially since foam, mineral wool, expanded polystyrene and other materials are less susceptible to destruction.

Even if, under the influence of cold and moisture, the outer insulation collapses over time, it is much easier to replace it than destroyed and deformed blocks. By the way, that is why it is recommended to install the insulation outside, and not inside the building.
If you plan to build a cozy house in which the family can live comfortably all year round, and the walls of a relatively fragile material will not collapse, then you should definitely take care of thermal insulation. Moreover, the costs for it will not be so significant, several times less than the installation of the gas silicate walls themselves.


The ways
Aerated concrete houses are insulated on the outside on the facade, on the inside under a fine interior finish. Do not forget about floor and ceiling insulation. First, consider the ways to insulate the walls from the outside.
"Wet" facade
The so-called wet facade is a simple and cheap way to insulate a building from foam blocks, but it is also quite effective. The method consists in fixing mineral wool slabs with glue and plastic dowels. Instead of mineral wool, you can use foam or other similar materials. Outside, a reinforcing mesh is hung on the insulation, then the surface is plastered.
Before starting work, the surface of the walls is cleaned of dust and primed with a special compound for deep penetration foam blocks. After the primer is completely dry, glue is applied, for this it is best to use a notched trowel. There are many adhesives for installing insulation plates, they are produced in the form of dry mixtures, which are diluted with water and mixed with a mixer. An example is Ceresit CT83 outdoor adhesive.
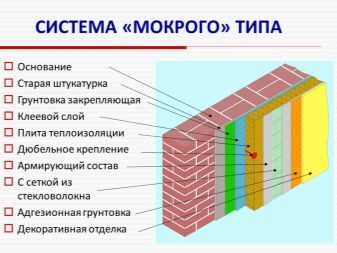

Until the glue has dried, a serpentine is applied to it so that it covers the entire wall without gaps. Then they start gluing the insulation boards, this work should not cause problems even for an amateur. The mineral wool is applied to the glue-coated surface and pressed firmly. In this case, it is necessary to ensure that the plates are located exactly, there are no gaps between them. It is optimal to lay each subsequent row with a shift of half the slab.
Installation of insulation boards goes from bottom to top. After laying each row, it is optimal to hammer in the dowels while the glue is still wet. For a "wet" facade, there are special plastic dowels-umbrellas 120-160 mm long, inside there is a metal screw. They are hammered into gas silicate blocks without much effort with an ordinary hammer. It is necessary to fasten them so that the cap is slightly recessed into the insulator.


When all the boards are installed and the umbrella plugs are clogged, you need to wait until the inner layer is completely dry, then apply a second layer of glue to the entire surface. After these procedures, when completely dry, you can apply decorative plaster. With a wall thickness of 300–375 mm, together with insulation, 400–500 mm is obtained.
Ventilated facade
This is a more complex version of wall insulation with gas blocks. It requires the installation of battens made of wooden beams or metal profiles. This method allows for a wider variety of finishes for siding, decorative stone or wood. The same insulating materials are used for the ventilated facade as for the "wet" one: mineral wool, polystyrene foam, polystyrene foam, expanded polystyrene.


Advantages and disadvantages
The following advantages of a ventilated facade can be noted:
- longer service life of insulating materials;
- effective protection against moisture;
- additional sound insulation;
- protection against deformation of walls made of aerated concrete blocks;
- fire safety.
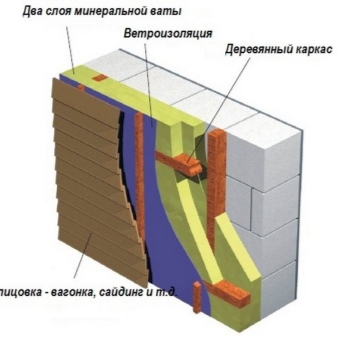
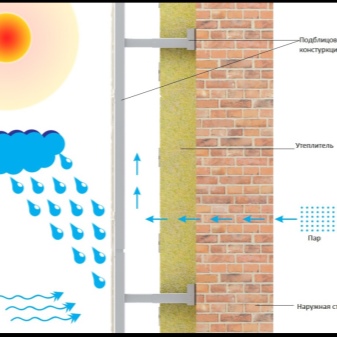
It is immediately worth noting its disadvantages:
- relatively short service life;
- great skill in installation is required, otherwise there will be no air cushion;
- Swelling may occur due to condensation entering and freezing in winter.


Installation steps
The process of installing a ventilated facade begins with the installation of an insulating layer. Here, as in the previous version, any tile insulating materials are used, for example, all the same mineral wool. The wall is cleaned, primed in 2-3 layers, after the primer has dried, glue for foam blocks is applied with a notched trowel. Then, as on the "wet facade", insulator sheets are laid on the serpyanka, the dowels-umbrellas are attached. The difference from the first method is that not glue is applied over the mineral wool, but a moisture-windproof membrane or a wind barrier is strengthened.
After the glue has dried, preparations begin for installing the lathing. For example, you can consider its construction of wood.It is best to take vertical beams 100 by 50 or 100 by 40 mm, and for horizontal jumpers - 30 x 30 or 30 x 40 mm.
Before work, they must be treated with an antiseptic. The bars are attached to the wall with anchors for aerated concrete, and between themselves with self-tapping screws for wood, preferably galvanized.


First, vertical beams are installed on top of the wind barrier along the entire length of the wall. The step should not be more than 500 mm. After that, the vertical jumpers are installed in the same way. It is worth remembering that the level for one plane must be observed everywhere. At the final stage, siding or other type of decorative trim is attached to the crate.
Less often, when arranging private houses, the difficult method of "wet facade" is used. For him, the foundation of the building expands, the insulation rests on it and is attached to powerful metal hooks. A reinforcing mesh is installed on top of the insulating layer and then plaster is applied, which can be covered with decorative stone.
Another option for external insulation of a house made of gas silicate blocks can be noted for finishing outside with facing bricks. A protective layer of air is formed between the brick wall and the aerated concrete. This method allows you to create a beautiful exterior of the facade of the building, but it is quite expensive, and the laying of facing bricks requires special professionalism.
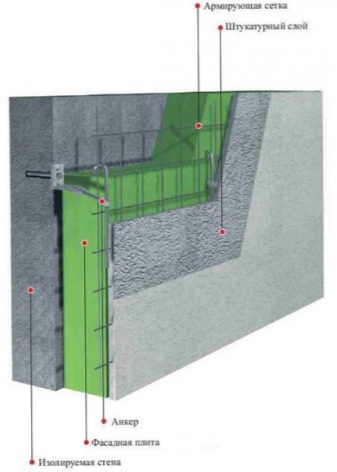

After external insulation of walls made of foam blocks, it is worth starting to install internal insulation. It is better not to use completely vapor-proof materials here, as the wall seems to be clogged up and the building does not breathe. It is best to use regular plaster for interior use. The dry mixture is diluted with water, mixed with a mixer and applied to a vertical surface, then leveled. Before plastering, do not forget about priming the walls and fixing the serpyanka.
Inside such a house, you should definitely insulate the floor, ceiling and roof. To do this, you can use various methods and materials, for example, mount a crate, inside which to place slabs of stone wool or foam, create a "warm floor" system with heating, use a screed with an additional protective layer, and cover roll heat-insulating materials in the attic.
When insulating the floor and ceiling in a private house, do not forget about their protection from moisture and steam.


Varieties of materials
To decide which insulation is better to choose for your home, you must not only take into account the cost of material and installation, but also know their properties.
Stone wool is traditionally used to insulate the walls of houses, floors and roofs, sewer pipes, water supply and heat supply pipes. For thermal insulation of buildings made of aerated concrete, it is widely used, it is the most popular material in the technology of "wet facade", ventilated facade. It is made from mineral raw materials, mainly basalt under the influence of high temperatures by pressing and extruding fibers.
It is possible to use stone wool for frost protection when constructing a building from scratch or in a house that has already been built for a long time. Due to its structure, it promotes good air circulation, so that, in conjunction with porous foam blocks, it will allow the house to "breathe". This material is not subject to combustion: at high temperatures and an open flame, its fibers will only melt and stick together, so this is a completely fireproof option.


The thermal conductivity coefficient of mineral wool is the highest among all materials. In addition, it is made on natural raw materials, without harmful impurities, it is an environmentally friendly material. It is categorically impossible to get it wet, it immediately becomes unusable, therefore, when installing it, it is necessary to use waterproofing correctly.
You can insulate the facade of a house made of aerated concrete with foam. In terms of its popularity, it is practically not inferior to mineral wool, while it has high thermal insulation characteristics and low cost.Consumption of material in comparison with mineral wool with the same layer is almost one and a half times less. It is easy to cut and attached to the foam block wall using plastic umbrella dowels. An important advantage of polystyrene is that its slabs have a flat surface, they are rigid and do not require lathing and guides during installation.


The density of the foam is from 8 to 35 kg per cubic meter. m, thermal conductivity 0.041-0.043 W per micron, fracture toughness 0.06-0.3 MPa. These characteristics depend on the selected material grade. The foam cells have no pores, so it practically does not allow moisture and steam to pass through, which is also a good indicator. It has good noise insulation, does not emit harmful substances and is resistant to the effects of various chemicals. Regular foam is a fairly flammable material, but with the addition of flame retardants, its fire hazard is reduced.
A good option would be to insulate a house made of aerated concrete with a basalt slab. This material is very similar to mineral wool, but harder, it can be installed without guides, simply glued in even rows to the wall. A basalt slab is made from rocks: basalt, dolomite, limestone, some types of clay by melting at temperatures above 1500 degrees and obtaining fibers. In terms of density, it is almost the same as polystyrene, it is easily cut into fragments, attached to the wall retains sufficient rigidity.


Modern varieties of basalt slabs are highly hydrophobic, that is, their surface practically does not absorb water. In addition, they are environmentally friendly, do not emit harmful substances when heated, they are vapor-permeable, and have excellent sound insulation.
Glass wool has been used for a long time, but recently it has been supplanted by other more practical and effective materials. Many people still consider its main disadvantage to be harmful to the skin and respiratory tract during work. Its small particles are easily separated and float in the air. An important advantage over all other common thermal insulators is the low cost of glass wool.
Glass wool is easy to transport as it folds into compact rolls. It is a non-combustible material with good sound insulation.
It is best to install glass wool thermal protection with the installation of the crate. Another advantage is that rodents are afraid of this material and do not create their own burrows in the thickness of the thermal insulation.

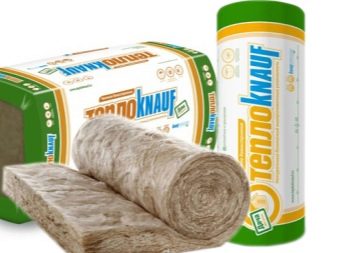
Ecowool is a fairly new heat-insulating material made from cellulose, various paper and cardboard residues. To protect against fire, a fire retardant is added to it, and antiseptics are added to prevent rotting. It is low cost, environmentally friendly and has low thermal conductivity. It is installed in a crate on the wall of the building. Among the shortcomings, it is worth noting that ecowool intensively absorbs moisture and decreases in volume over time.
Penoplex or expanded polystyrene is a fairly effective material for insulating walls from foam blocks. It is a fairly hard and rigid slab with grooves at the edges. It has durability, moisture protection, strength and low vapor permeability.

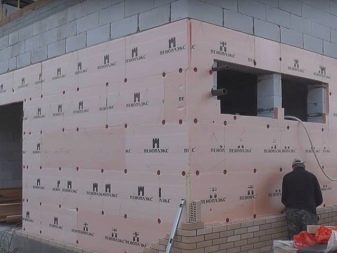
Polyurethane foam is applied to the surface by spraying from cans, this is its main advantage, it does not require any glue, or fasteners, or lathing. On top of that, if there are metal elements in the foam block wall, then he covers them with a protective anti-corrosion mesh.
A standard facing brick can serve not only as an excellent external finishing of the facade, but also be an external heat insulator, if you cover it with a wall of foam blocks. But it is best to use two layers to keep warm in the house, placing foam sheets between them.


To simplify all the work on thermal insulation and external decor of the building, you can sheathe its walls with thermal panels. It is a versatile material that combines insulating and decorative properties.The inner layer is made of various non-combustible heat insulators, and the outer one has many options for textures, patterns, colors. There is an imitation of brick, natural stone, quarrystone, wood. You can successfully combine thermal panels with clinker tiles.



Subtleties of installation
Installation of thermal insulation of a building made of aerated concrete and subsequent decorative finishing with your own hands have a number of subtleties. For convenience and safety, you should definitely use rigid, securely fixed to the wall scaffolding with platforms. You can fix them on the wire and anchors screwed into the facade. It is best to use lightweight and durable aluminum rather than heavy steel.
For any type of facade, the sequence of the cake must be correctly followed: first there is a layer of glue with a serpentine, then insulating panels, the next layer of glue or a windscreen with a crate. The decorative facade cladding in the "wet" version is applied only on a hard surface.
Above the foundation of the house made of gas silicate, you can fix a corner of a metal profile, which will additionally support the insulation layer, and at the same time separate the base from the wall. It is attached to ordinary metal dowels or aerated concrete anchors.

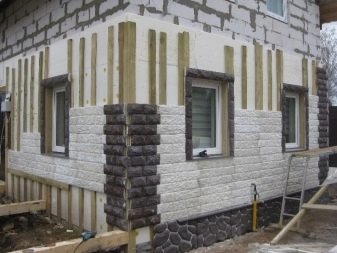
Foam plastic, with all its advantages, does not allow air circulation, that is, when it is fixed on both sides of a wall made of gas silicate blocks, it practically levels its remarkable properties. Therefore, many people prefer to use traditional mineral wool or more modern and efficient basalt slabs.
The ventilated or hinged façade can be installed on metal or wooden battens. The tree can deform under the influence of temperature, humidity, and therefore there is a possibility of deformation of the decorative facing of the building.
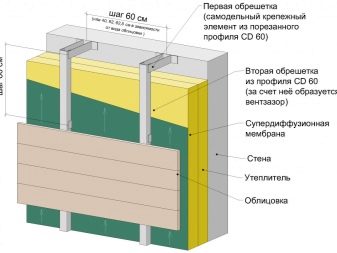

For information on how to insulate a house made of aerated concrete with mineral wool, see the next video.
The glue must be of high vapor permeability.
The comment was sent successfully.