The subtleties of insulating wooden houses outside
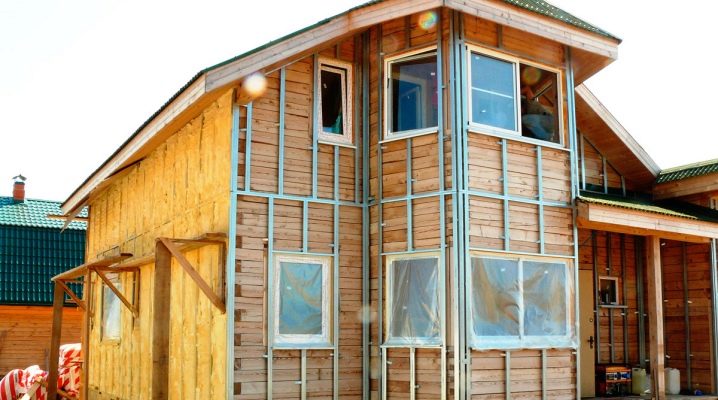
Wooden houses are considered one of the most popular types of buildings, especially if we are talking about the countryside and the buildings of the beginning and middle of this century, where many more have rubble. Not everyone can change housing, and it is not always possible to do this. But nevertheless, the issues of energy saving and energy efficiency in our time of high tariffs for resources and utilities worries everyone. And today we will talk about how to insulate wooden houses from the outside.
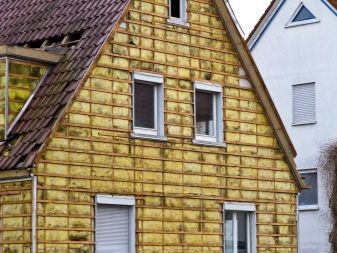
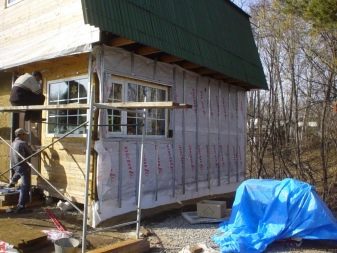
Features of thermal insulation of wood
Any wood has a property that allows it to absorb moisture. With the help of various impregnations, it is possible to reduce the hygroscopicity of such a material, but it is not possible to completely eliminate this property. If there is an effective ventilation system, then moisture can evaporate quite quickly and efficiently and it will not have time to have any negative effect on wood, which will allow maintaining a good microclimate in a village or city house.
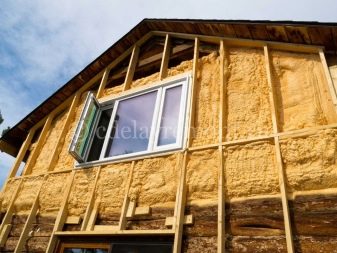
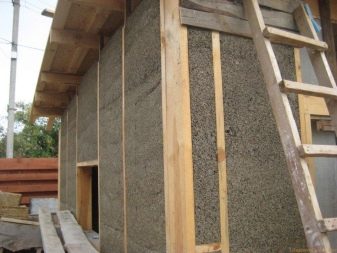
But the violation of the movement of air masses leads to the fact that condensation begins to accumulate and the tree begins to swell, which is why fungus and rot begin to appear on it, and the air begins to smell characteristic. In order to avoid such problems, it is recommended to follow these tips:
- use only insulation with good vapor-permeable characteristics;
- it is better to insulate dry walls, but not wet and damp;
- cover the thermal insulation with a waterproofing membrane on both sides;
- leave a small air gap between the finish and the insulation.
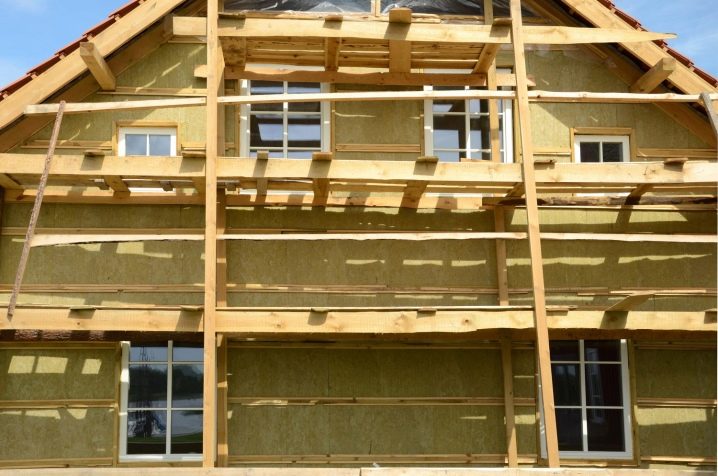
If you plan to paint the walls of a wooden house, or you just need to insulate the seams, then paint with a sealant must also be vapor-permeable.
As a rule, these are those made on an acrylic base. And of course, the surface must be prepared as much as possible before insulation. In addition, the logs themselves or the surface of the outer boards should not be damaged by pests such as bark beetles.
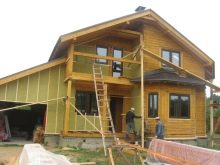
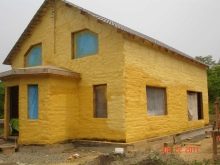
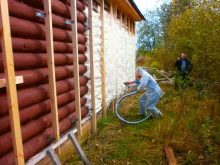
Facade insulation methods
It should be said that to insulate a wooden house from the outside, there are two external insulation technologies:
- ventilated facade;
- wet facade.
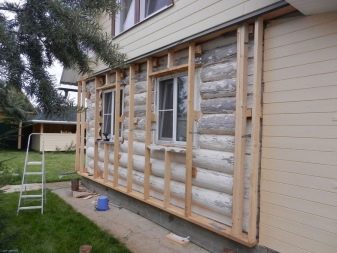
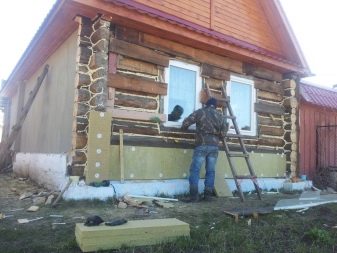
The first technology is suitable for frame houses. The frame is mounted on the walls, after which it is sheathed with siding, clapboard or some other finishing material. In this case, the insulation is placed between the finishing material and the wall. This technology is very good in that it excludes carrying out wet works, and the facade itself in this case will be stronger and more durable.
In the second case, the walls of the house are simply pasted over with insulation, after which they are plastered using a technology specially developed for this.
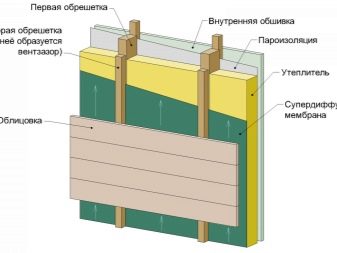
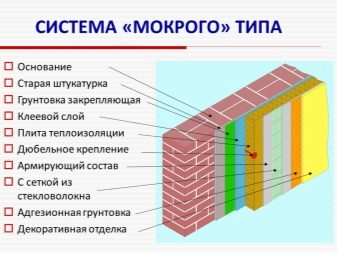
Now let's tell you more about the features of each of the methods.
Ventilated facade technology
The process of creating a so-called ventilated (or hinged) facade includes several parts:
- preparation of the facade;
- arrangement of the ventilation gap and installation of the frame;
- frame sheathing.
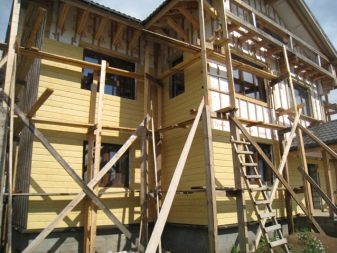
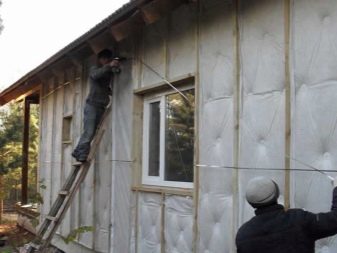
If we talk about insulation that can be used with this method, then it should be said that the best solution would be mineral wool.Many people want to carry out insulation with foam.
And, in principle, with this method, its use is also allowed. It is only necessary to remember that foam resists very poorly to the effects of fire, and also does not allow steam and moisture to pass through. And this can negatively affect the microclimate inside the house. Therefore, in this case, it is better to give preference to mineral wool.
If we talk about racks for the frame, then either bars or boards are used for it. They can be attached to the walls using brackets or metal corners. By the way, as an option, you can apply a profile that is used to install drywall. In addition, you will need a vapor barrier film, which will protect the insulation from getting wet, the material that will be used for finishing: siding, wall paneling, block house or some kind of facade material.
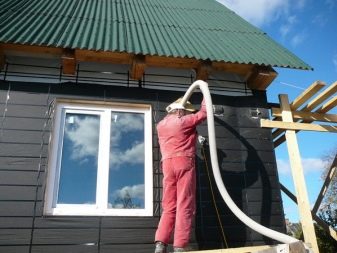
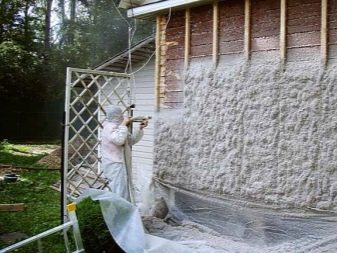
Also, to implement this method, you will need a mezhventsovy heater. Usually, jute tow is used in this capacity, which acts as an excellent protection for the seams, but you can use special foam or any other materials that are suitable. You will also need a wood preservative so that it can resist moisture. It is usually applied under plaster.
Now let's talk about the features of another method.
Wet facade technology
It consists of the following parts:
- preparation of the facade;
- installation of insulation;
- reinforcement;
- painting.
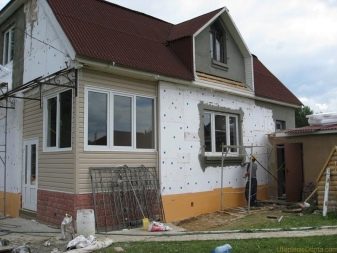
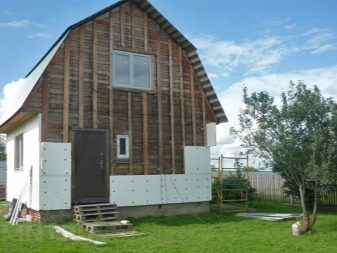
In a little more detail, in this case it is also better to give preference to such material as mineral wool. In addition to insulation, in this case, it will also be necessary to purchase a special glue for mineral wool, an umbrella-shaped dowel, a special reinforcing mesh made of fiberglass, perforated corners, a primer, paint for the facade, as well as decorative plaster. After all these materials are purchased, you can start work.
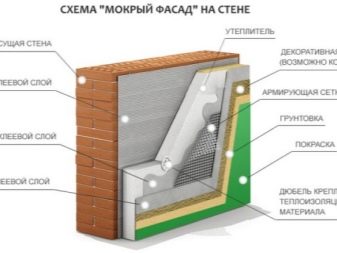
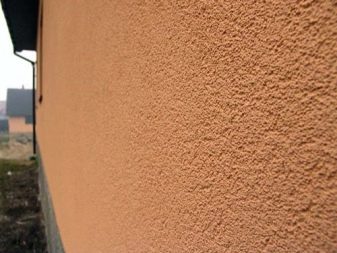
Material characteristics
The decision to insulate a wooden house must be made with an eye to the quality of its construction. If the thickness of the walls is selected correctly, then it may not be necessary to additionally make thermal insulation. But it is necessary to insulate a wooden house if it is cold in it. And if it is also old, then, most likely, you simply cannot do without it.
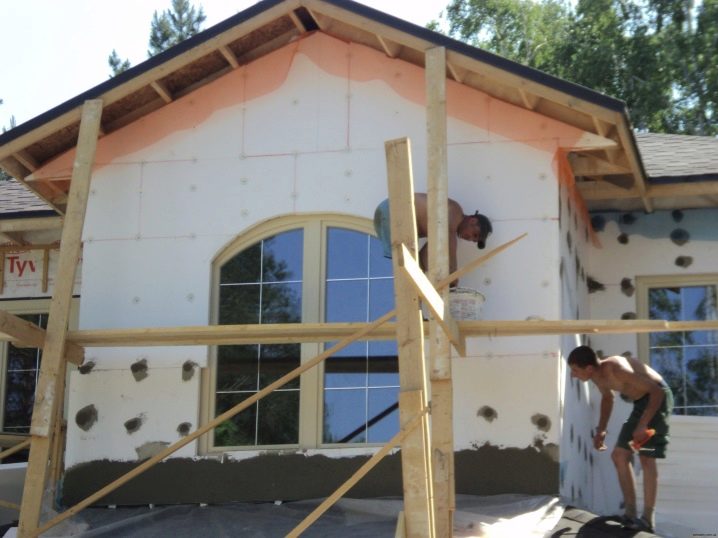
But at the same time, it is important to select materials for this so that their effectiveness is maximized. Not all heaters are recommended to be used to insulate houses of this type from the outside.
It is important to understand here that heaters can be of two categories:
- natural;
- artificial.
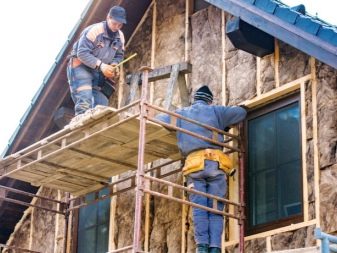
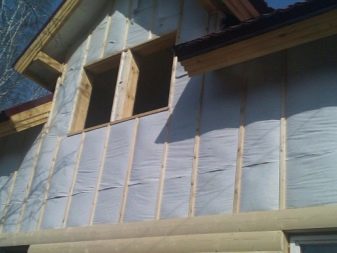
The first category does not violate the microclimate at home, as it allows it to breathe. The second category of materials will be more affordable in terms of price, but the use of such materials may not always be safe for health. But the question of what is the best way to insulate a wooden house is really very important. Those who prefer natural materials most often use algae mats, adobe or hemp fiber. Sometimes home owners also resort to wood and sawdust insulation. But this is, say, not a very ecological way of warming.
And those who believe that artificial thermal insulation is not the worst solution can insulate houses with extruded polystyrene foam, basalt slabs, isopink, isover, penoplex and even expanded clay.

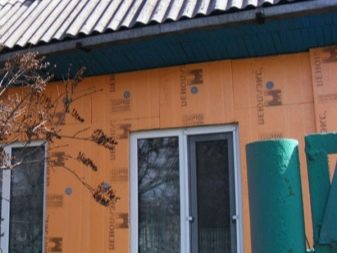
You should also give the following list of artificial insulation for the house:
- mineral insulation, which includes various types of wool: stone, glass wool and basalt;
- penoizol;
- ecowool;
- Styrofoam;
- polyurethane foam.
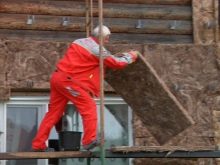
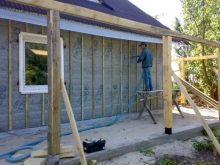
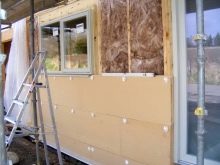
In general, as you can see, the choice of heaters for creating thermal insulation of a wooden house is very large. But how do you choose the best solution? You can try to study the technical characteristics of heaters, which will be discussed below.
Stone wool
This type of insulation is most often made from basalt or from melts of other rocks. Typically, this material contains three components:
- stone fibers;
- binders (urea, formaldehyde resins);
- hydrophobic additives.
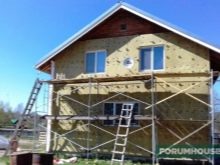
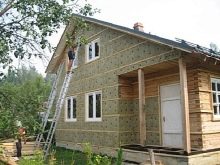
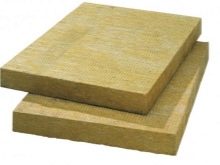
This material is classified as non-combustible, since it can easily withstand heating up to 600 degrees and does not change its physical properties and characteristics under the influence of such a temperature. Also, stone wool has good vapor permeability and low thermal conductivity. Most often, this material is presented in the form of plates or mats, and is covered with kraft paper, fiberglass or foil. Basalt slabs are quite dense, which allows them, with properly performed thermal insulation, not only not to shrink, but also to keep their shape well throughout the entire period of use.
In addition, this material is excellent against the appearance of microorganisms. It is very easy to install such a plate due to its low weight and dimensions.
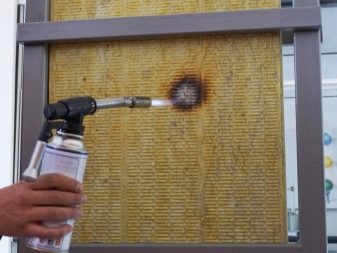
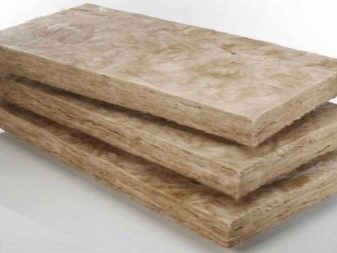
If we talk about the shortcomings, then there are not so many of them in such a stove. The main thing is the low strength of the fibers: if the material is squeezed or cut, then dust quickly forms, which is very easy to inhale. For this reason, it is best to work with the material after wearing a respirator. Another disadvantage of this material will be the rather high price, therefore, if the budget is small, it is better to look for alternatives.
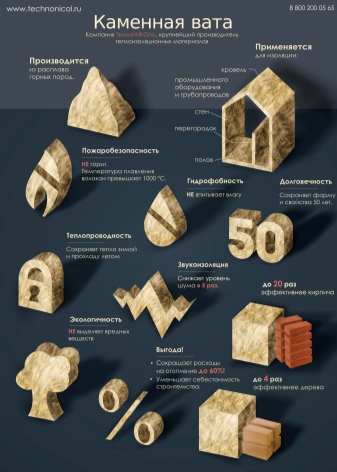
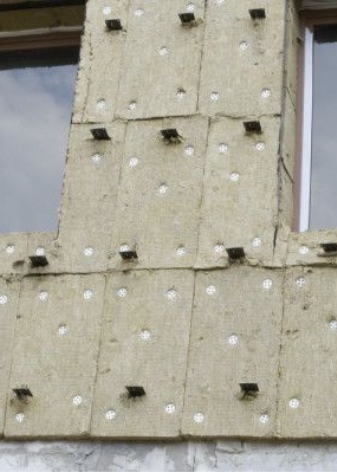
Ecowool
Ecowool production is carried out from the waste of the cardboard and paper industry. For this reason, this type of insulation is 80 percent cellulose. In order to improve the characteristics of cellulose, its fibers are mixed with fire retardants and antiseptics. Such material can absorb and release water without losing its thermal insulation properties. If you make a choice in favor of such a heater, then condensation will never appear. In addition, it has excellent sound insulating properties and does not emit any harmful substances. By the way, insects or rodents do not start in such insulation due to the presence of special additives in its composition.
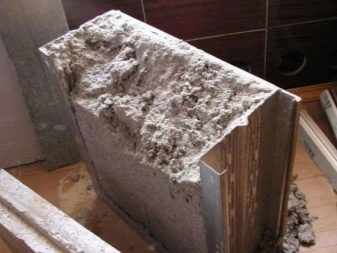
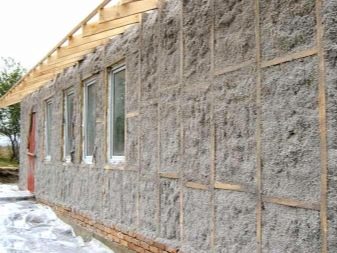
This type of insulation is a loose light gray mass, which is tightly packed in bags of 15 kilograms. Before warming, the mass is poured out of the bag, loosened with a mixer, and then laid. The effectiveness of such a material depends on the density of the layer. If the material is tamped too weakly, then it shrinks very quickly and forms cold bridges. But if such cotton wool is laid tightly, then it will not change its characteristics during the entire service life.
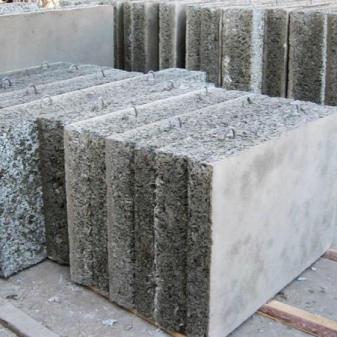
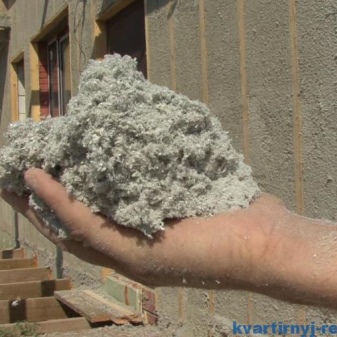
If we talk about the shortcomings of ecowool, then first of all we should mention the technology of its laying. This requires a special pneumatic unit, which is expensive and requires special knowledge. That is, in this case, it is also necessary to spend money on the search for certain specialists.
Glass wool
Glass wool is made from broken glass melts, to which borax, limestone and other components are added. The connecting link in this case will be either bitumen or synthetic polymers. Glass wool has long fibers, which allows it to surpass analogs on a different basis in terms of elasticity, and also have a high mechanical density, despite its low density.
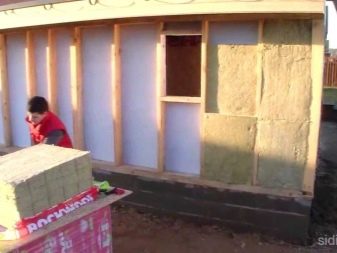
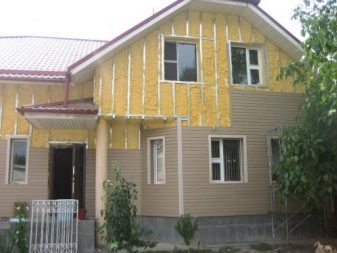
It should be noted that glass wool is vapor-permeable, perfectly retains heat and is not afraid of the effects of substances that are chemically aggressive. It does not burn and calmly withstands heating up to 450 degrees without changing its physical properties. And also it perfectly resists sudden changes in temperature.
Glass wool is produced in the form of mats, plates and rolls, including those with a foil coating. Its greatest disadvantage can be called the prickly fibers, which cause severe irritation of the human skin and easily get into the eyes and lungs.In addition, it is quite fragile, which is why it is quite difficult to work with it - before laying it you need to wear good and tight clothes, as well as gloves.
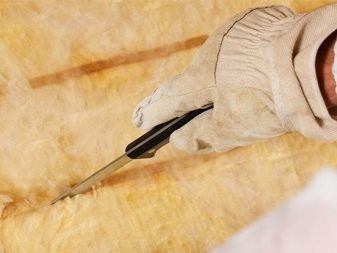
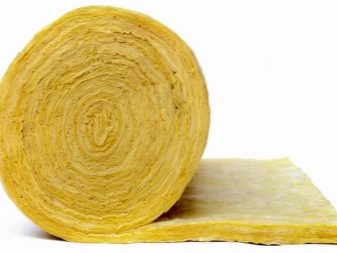
Styrofoam
This material is the most affordable in terms of cost. It has excellent performance characteristics, which allows using it to significantly save on heating. This material is made in the form of panels of various sizes and thicknesses. For carrying out insulation work of an external nature, material with an average density is used. It is important to understand here that the greater the density of the insulation, the worse its thermal insulation qualities will be. True, the resistance to stress will be higher. Too dense material is usually used for floor insulation.
This material has a small mass and is a good barrier not only for cold air masses, but also for sound. It has a low thermal conductivity, due to which it retains the accumulated heat in the room for a long time. It is easy to cut and fasten to the wall.
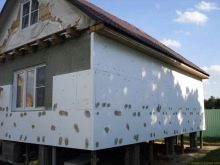
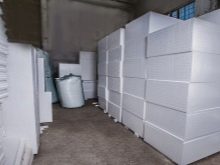
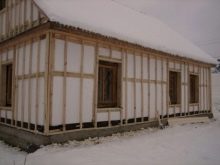
In addition, it is resistant to temperature extremes and ultraviolet radiation, does not absorb moisture and has a considerable service life. At the same time, this material also has a number of disadvantages. Its mechanical strength is extremely low: the material is very easy to break and crumble. For this reason, once attached to the wall, it will require protection with reinforcement and decorative coating. By the way, they can also do interior decoration by placing it, for example, under drywall.
The disadvantage of the material can also be called its poor fire resistance. Moreover, when exposed to high temperatures, it can release substances hazardous to health. By the way, if you intend to use glue to fix the material, then you need to find out whether this or that particular brand of glue is suitable, since some types can destroy the material.
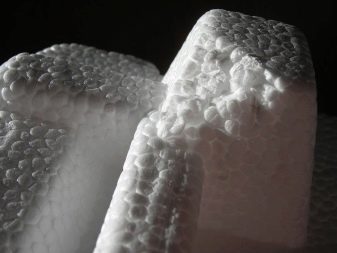
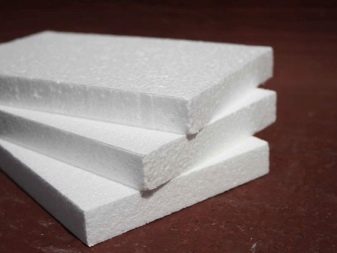
Slag
To create this type of mineral wool, blast furnace slags are used, that is, waste from the metallurgical industry. This determines the availability of this type of material. Slag wool has a slightly higher thermal conductivity than basalt insulation. The material can be heated up to 300 degrees Celsius without any problems. If the temperature is higher, then it begins to deform and loses its characteristics. As a rule, slag wool is produced in rolls and slabs, often coated with foil. It has low rigidity, which is why it is excellent for thermal insulation of uneven surfaces, as well as excellent thermal insulation and sound insulation characteristics. Also, mold cannot develop in it.
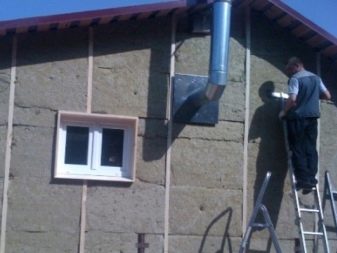
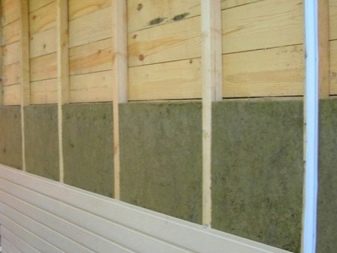
But slag also has a number of disadvantages:
- hygroscopic;
- does not like temperature changes;
- releases acids when exposed to moisture;
- in contact with the skin, it causes extremely severe irritation.
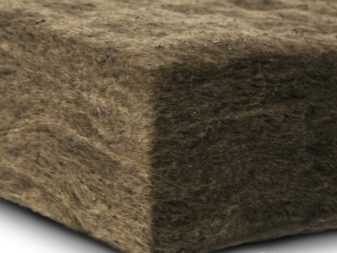
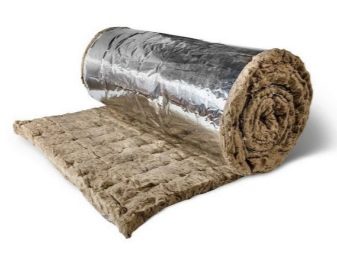
Polyurethane foam
Polyurethane foam is considered a new generation material. It is a spray-on heat insulator. It absorbs moisture minimally and also has minimal thermal conductivity. The most interesting thing is that the higher the density of the polyurethane foam, the higher its thermal conductivity. In fact, this material, as it were, envelops the building and does not allow cold air masses or moisture to pass inside.
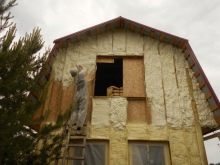
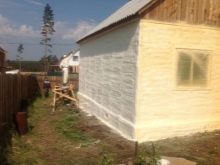
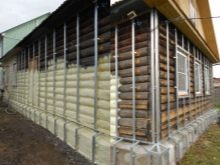
This material is an excellent solution for buildings in an arctic climate, as its characteristics are extremely effective for such natural conditions.
True, experts are rather ambiguous in assessing the need to use this material as insulation. According to some, it is not worth using polyurethane foam for wooden buildings, since the tree simply does not breathe, which is why its slow destruction begins.According to others, if you correctly calculate the thickness of the polyurethane foam coating for wooden walls, then the surface will always be dry and perfectly protected from decay, and the moisture exchange that wood needs will be carried out inside the room, and not outside.
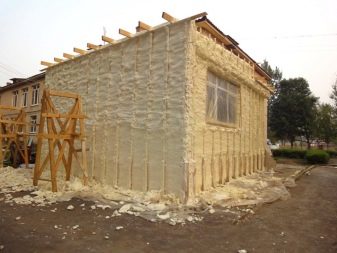
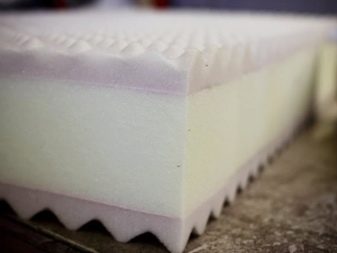
Natural heat insulants
As mentioned above, in addition to artificial ones, there are also so-called natural heat insulators. These include slabs made from sawdust of the type Steico Flex, straw. And you can also use clay insulation, which is also considered insulation. In general, this category of insulation from the point of view of environmental friendliness is an excellent solution. Moreover, they are inexpensive. But their main drawback is the complexity of creation. Also, flax fiber is used as a natural insulation, which has excellent antiseptic properties and prevents the appearance of mold and mildew. This material is easy to cut, install, and easy to work with.
Separately, it is necessary to talk about the material Steico Flex. This material is made of wood fiber mats that are easy to install and handle, even without the use of tools.
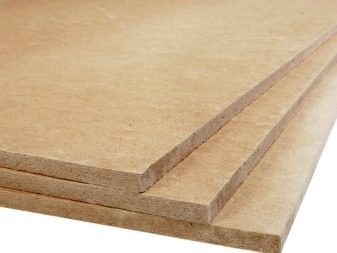
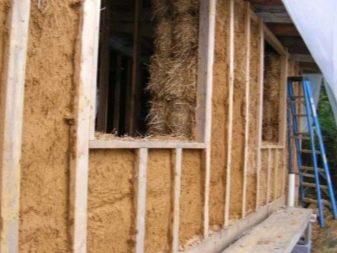
With this material, you can not only insulate the walls, but also the floor, as well as the ceiling. In addition, such insulation will be an excellent solution not only for a wooden house, but also for a house made of chopped timber or lined with bricks. It also has excellent sound insulation characteristics and responds well to temperature extremes.
Its use allows you to make the microclimate in the house as comfortable as possible for its residents.
Thickness calculation
An important point is the calculation of the thickness of the insulation. It should be noted that the thickness of the thermal insulation layer depends on the thickness of the walls of the house, as well as climatic features. But to know how thick the insulation should have is simply necessary. If there is too much of it, then this can adversely affect the house, and an insufficient amount will cause the low efficiency of the insulation process as a whole.
In addition, this parameter significantly affects the structure of the frame, since it is very important to know at what distance from the walls the guides should be taken out under the outer skin. It is not difficult to make such calculations yourself, especially if you apply a certain calculation method. Its essence is that the total heat transfer resistance of a wall from several layers of the structure R should not be less than the calculated one for a certain climatic region.
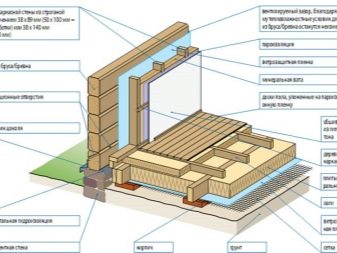
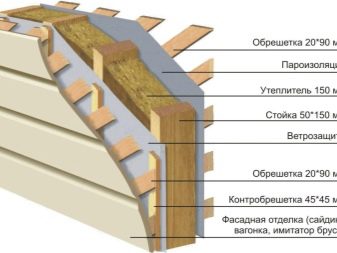
It should be noted that the wall is not only the log house itself, but also the entire interior decoration, thermal insulation layer, as well as the external decoration of the facade. Each layer has its own thermal resistance index, which must also be calculated.
To determine the specifically required thickness of the insulation, it is necessary to know the coefficient of thermal conductivity of each layer, as well as their thickness. The calculation will be carried out according to the formula: Rn = Hn / λn, where:
- Hn is the thickness of a particular layer;
- λn is the coefficient of thermal conductivity of the material from which this or that layer is made.
As a result, the calculation formula will look like this: Hу = (R– H1 / λ1 - H2 / λ2 - H3 / λ3 ...) × λу, where
- λу - coefficient of thermal conductivity of the specified thermal insulator;
- Well - the thickness of the insulation.
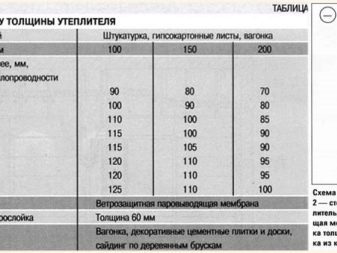
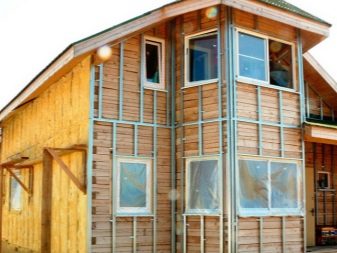
Finding such coefficients is quite simple. Sometimes manufacturers even indicate them on the packaging. Measuring the thickness of the layers is also not difficult. If you do not want to calculate everything manually, then you can use an online calculator. It already has all the necessary basic and frequently used construction, insulation and finishing materials.
Preparatory work
If we talk about preparatory work before insulating a house, then they should be performed in a dry and warm season, so that the walls are not frozen or damp. The surface of the walls must be cleaned as efficiently as possible from dirt, dust, moss, fungi.It is imperative to conduct a careful examination of the inter-crown seams. If you find any voids, then they must be repaired with a sealant, and then sealed with a sealant. The same method can be used if you find deep cracks in the tree of a log house.
After that, priming is carried out. The primer is applied with a brush, carefully treating all the grooves, irregularities, and end cuts of the logs.
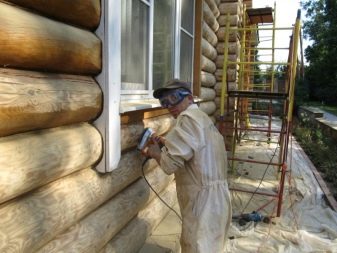
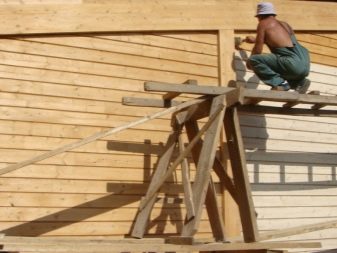
Note that if the wood absorbs the primer too quickly, then it is applied in two layers. After that, it is necessary to wait until the surface is completely dry and only then proceed to the very process of warming.
If the work is carried out using the technology of the curtain facade, it is required to carry out its preparation, which consists of the following stages:
- dismantling all hinged-type elements that can interfere with the work (antennas, visors, window sills and ebb tides);
- treatment of walls with antiseptic impregnation;
- closure of the gaps between the joints with a heater, if any.
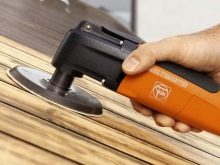
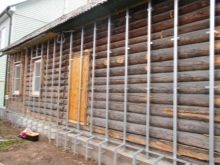
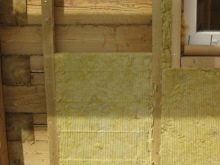
In general, this is a rough list of preparatory work. But it may differ depending on the type and structure of the house, the chosen insulation technology, as well as the characteristics of the building itself.
Installation steps
Consider an approximate algorithm for insulation, both in the case of the ventilated facade technology, and in the case of the wet technology, which are done by hand.
So, if the preparatory work on the creation of the curtain facade is done correctly and the technology is followed, then after that the installation of the frame for insulation begins.
At the first stage, it is necessary to equip the ventilation gap. For this, boards with a thickness of 2 centimeters should be attached to the walls. You can arrange them as you like. The main thing is that later you can attach racks to them.
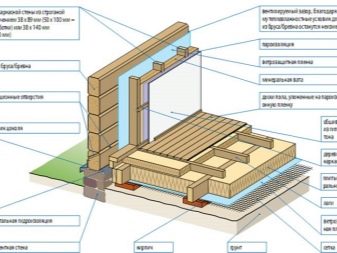
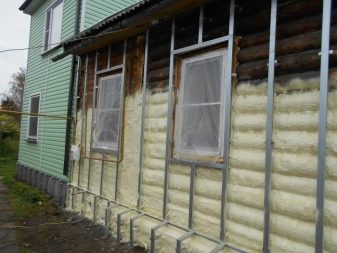
After that, we attach a vapor barrier film to the boards with a stapler. It is imperative that it be placed tightly and overlapped so that there is space between it and the wall. Places where there will be joints should be glued with tape. It should be noted that the insulation of the ventilation gap is important, since if this is not done, then moisture can begin to accumulate between the insulation and the wall, which will lead to bad consequences. After that, the racks are installed. First, two extreme posts are mounted, between which the ropes should be pulled. These will be a kind of beacons for intermediate rails. Installation of the end posts is carried out at the same distance from the wall and only vertically.
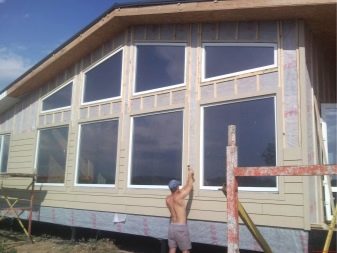
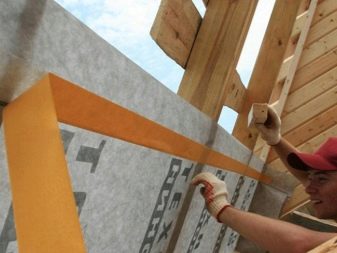
If the boards are used as drains, then they should be strengthened with metal corners and self-tapping screws. After that, the installation of intermediate rails is carried out, which are located at a distance of 1-2 centimeters from the mineral wool slabs.
Now it is necessary to lay the heat-insulating material in the space between the racks. As a rule, in this case it is better to use mineral wool. The mats should adhere as closely as possible to each other and to the uprights so that there are no gaps in the insulation. After that, a vapor barrier film is attached to the frame. It should also overlap. It is fixed with horizontal slats, which will also hold the insulation. This completes the insulation of the facade in this way.
After that, the frame should be plated, which will be the final stage. The finish can be different. If you do not have any pronounced preferences, then focus primarily on the price and quality of the material.
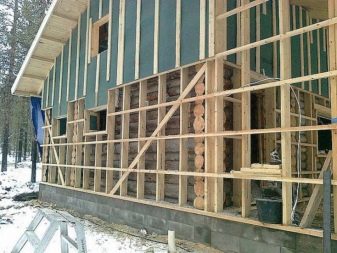
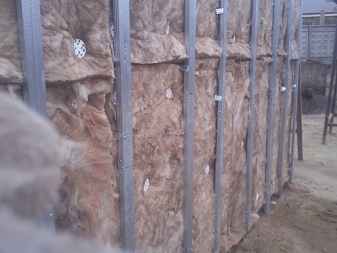
For example, lining is an environmentally friendly material that allows you to maintain an attractive appearance of the house. And if you take vinyl siding, then such a material is easy to clean and does not require any special care.
If you still decide to apply siding, then the sequence of actions will be as follows:
- it is necessary to install the starting profile, which should be placed horizontally around the perimeter of the house (it will not be superfluous to leave the distance from the ground or blind area to the profile of about ten centimeters);
- corresponding profiles are mounted in the corners of the house;
- the first row of panels is installed: from below the siding is inserted into the starting profile, and from above it and the crate are connected using self-tapping screws;
- according to this mechanism, the whole house is sheathed with siding;
- before installing the last panel, you need to fix the final profile;
- at the end, the installation of the remaining elements is carried out: ebb, slopes and so on.
This is where the siding ends. It should be said that according to the same scheme, the house is sheathed with clapboard, thermal panels or other materials.
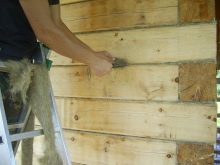
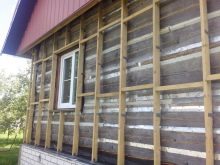
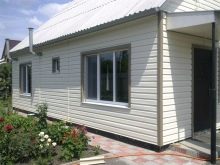
If we are talking about a wet facade, then after preparation, the walls of the house are immediately pasted over with mineral wool under the plaster. First, we prepare the glue, after which we apply it to the mineral mats using a notched trowel. It will not be superfluous to use the building level, as well as stretch the beacons so that all the plates are located in the same plane. After all the walls of the house are pasted over, the mineral wool should be fixed to the wall with dowels-umbrellas.
Now window openings, including gables, are pasted over with mineral wool. It is not necessary to install dowels on window slopes, but on door slopes it is necessary. After that, we apply the rule to various sections of the walls and check if there are any bumps. After that, glue the perforated corners to the outer corners with glue. At the end, we glue the dowel caps with glue so that the facade is smooth.
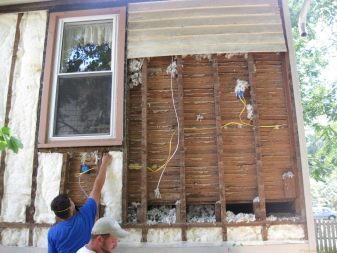
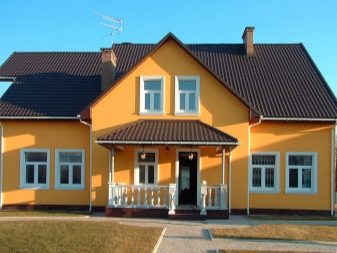
Now we carry out the process of reinforcement, which is also called rough plastering. First, we prepare the mesh by cutting it into pieces of the required size. Then we cut into pieces for the slopes. Now we glue the mesh on the slopes, after which we do the same steps with the walls. When everything is dry, then apply the glue again with a thin layer and remove the irregularities. Now all that remains is to apply decorative plaster. This process will be easier than reinforcement, and is carried out in the following sequence:
- the walls of the house are treated with a primer (it is best to apply it in two layers);
- the solution is prepared according to the instructions on the pack;
- decorative plaster is applied to the walls with a spatula, while the layer should be as thin as possible;
- when the plaster begins to set on the walls, then it is necessary to wipe it with a small one, which will create a pattern;
- all that remains is to paint the house and everything will be ready.
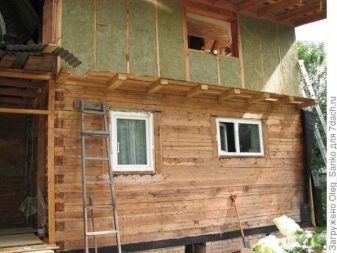
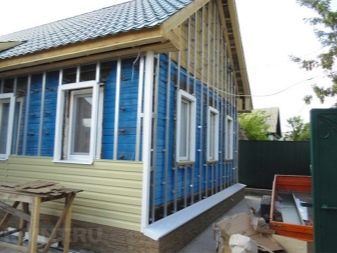
In general, as you can see, it is possible to insulate a wooden house from the outside on your own. But it is important to observe the technology of this process as much as possible, to have a clear idea of the nuances of work and to determine exactly what method of insulation and what material is suitable for this.
Knowing all this, as well as having certain knowledge, you will be able to insulate your house with high quality and well without any problems in a fairly short time, which will significantly increase and improve its operational and thermal insulation characteristics.
For information on how to insulate a house from a bar outside, see the video below.
The comment was sent successfully.