Basalt insulation for walls outside the house: features of using stone wool

Using basalt insulation for external insulation of a house is a simple and effective way to increase its effectiveness. In addition to thermal insulation, when using this material, it will be possible to increase the sound insulation of the building. Other technical characteristics include fire resistance, environmental friendliness and durability of the insulation.

What it is?
Heaters made from the finest fibers of mineral origin are called mineral wool. Depending on the basis of the composition, it has several varieties. The highest heat and sound insulation qualities, as well as environmental friendliness and fire safety are demonstrated by stone wool insulation.
Basalt wool is a type of mineral wool insulation, which significantly surpasses its main types in its technical properties. Basalt insulation consists of fibers melted and stretched into threads. Mixing in a chaotic manner, they form an airy, but durable and warm material.
A huge amount of air bubbles accumulate between the fibers, which provide a thermal insulation effect, and also demonstrate the ability to reflect and absorb sound. The insulation got its name due to the fact that the fibers of the material are obtained by processing rocks. Stone wool is also called "basalt" and "mineral" wool.


The varieties of basalt insulation can be determined by its density and the diameter of the fibers used. Based on the density, soft, semi-hard and hard cotton wool is distinguished. The thickness of the wool fiber ranges from 1 micron (micro-thin) to 500 microns (coarse fibers).
The form of material release is facade slabs, produced in 2 dimensional options: 0.5 by 1.0 m and 0.6 by 1.2 m. The thickness is 5-15 cm. Slabs 10 cm thick are considered the most popular for outdoor insulation of a country house. The analogue in rolls is less common: it is less dense and at the same time is subject to deformation.
The material has a wide range of applications. If we talk about thermal insulation of external walls, then it is suitable for both "wet" and "dry" types of facades.

How is it produced?
The progenitor of modern insulation was the threads found in Hawaii near a volcano after its eruption. Locals have found that these lightweight fibers, when stacked together, improve the thermal efficiency of homes, are water-resistant and do not burst. Technically, the first basalt wool was obtained in 1897 in the United States. However, at that time it was produced in open workshops, so the smallest particles of basalt raw materials penetrated the respiratory tract of workers. This almost became a rejection of the production of the material.
After a while, a way was found for a different organization of the production process and the protection of employees. Today, basalt wool is produced from rocks that are heated in furnaces up to 1500 C. After that, threads are drawn from the molten raw materials. Then fibers are formed, which are impregnated with special compounds to improve the technical properties of the insulation and are stacked in a chaotic manner.

Advantages and disadvantages
Stone wool insulation has many positive properties.
- Durability... Long service life (up to 50 years, according to the manufacturer) allows you to forget about the need to insulate the facade for a long time.If the installation rules are observed, the operating period can be extended for another 10-15 years.
- Heat efficiency... The porous structure of the material ensures its high thermal insulation performance. Its use allows you to maintain a favorable microclimate in the house: warmth in the cold season, pleasant coolness in the summer heat. The material has a low thermal conductivity, which is 0.032–0.048 W per meter-kelvin. Polystyrene foam, cork, foamed rubber have a similar value of thermal conductivity. Ten centimeters of basalt insulation with a density of 100 kg / m3 can replace a brick wall with a thickness of 117–160 cm (depending on the type of brick used) or wood, which is almost 26 cm thick.
- High performance of sound insulation. In addition to high thermal efficiency, the material has increased sound insulation characteristics. This is also due to the peculiarities of the composition and structure of the material.

- Fire resistance... The material is considered non-combustible, since it can withstand temperatures up to 800-1000 C.
- Vapor permeability... The vapor permeability of the material ensures condensate drainage. This, in turn, guarantees the preservation of the technical properties of the insulation, the absence of high humidity in the room, protection from mold and mildew both inside the building and on the surface of the facade. Vapor permeability indicators - 0.3 mg / (m · h · Pa).
- Chemical inertness, biostability. Stone wool is characterized by chemical passivity. When applied over metal products, you can be sure that they will not be exposed to rust, and mold and mildew will not appear on the surface. In addition, stone fibers are too tough for rodents.
- Ease of use. Several options for sheet dimensions, as well as the ability to cut the material, greatly simplify its installation. Unlike glass wool, basalt fibers do not prick and do not have the ability to penetrate the skin.


- Moisture resistance. Due to this property, moisture droplets do not settle inside the material, but pass through it. In addition, cotton wool has a special hydrophobic impregnation, so it literally repels moisture. The moisture absorption of the material is at least 2%, which makes it the optimal insulation not only for the facade of the house, but also for the walls of a sauna, bathhouse and other objects characterized by high humidity.
- No deformation. The material does not deform and does not shrink, which is a guarantee of maintaining the technical characteristics throughout the entire period of operation.
- Environmental friendliness. Due to the natural composition, the material is non-toxic. However, the buyer should be careful: sometimes manufacturers add slags and additives to the composition of the basalt insulation to reduce the cost of the material.
It should be remembered that they burn at a temperature of 400 C, and the material with such additives has the worst performance.


The disadvantage of insulation can be called the high cost. However, if you insulate the facade of the building with it, in the future you can save on heating it. Like all mineral wool materials, stone wool, when cutting and during installation, forms the smallest dust that irritates the mucous membranes of the upper respiratory tract. This can be avoided by using a protective mask.
Finally, due to its high vapor permeability, basalt insulation is not recommended for finishing the basement and basement of a house.
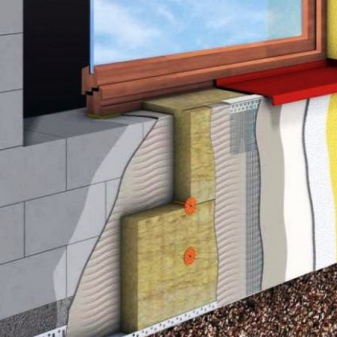

How to choose?
For the walls of a country house, medium-density basalt wool (semi-rigid material with a density of at least 80 kg / m3) with a thickness of 8-10 cm is sufficient. Pay attention to the location of the fibers. Randomly spaced filaments provide better sound and thermal insulation properties than horizontally or vertically oriented filaments.
In order to increase the thermal insulation properties, you can purchase a foil analogue.On one side, it has a foil, which not only reflects thermal energy, but also has a more reliable waterproofing, allows you to reduce the thickness of the insulation used. In addition, the foil version of the insulation is suitable for regions with high levels of humidity, for houses located near water bodies, as well as for brick walls, since it is characterized by improved hydrophobicity.
The latter property is especially valuable for a wet facade, since a too thick layer of insulation may not be firmly fixed to the walls, creating an excessive load.

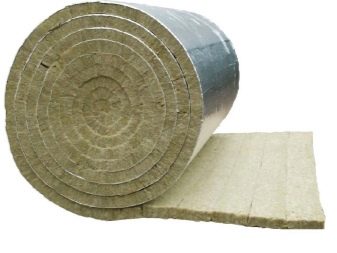
For a frame house, in the walls of which the presence of a layer of insulation is already assumed, you can use cotton wool of a lower density - 50 kg / m3. For northern regions, as well as for use in extreme conditions, it is recommended to use a solid stone wool mat. It has a wider operating temperature range.
When buying stone wool, preference should be given to well-known manufacturers who have received a positive assessment from buyers. Among them: products of the domestic company "TechnoNIKOL", as well as products manufactured under the French brand Isover and the Finnish brand Paroc. Pay attention to how the product is stored: it must be in its original packaging and wrapped in shrink wrap. The packaging must be free of holes and damage. It is unacceptable to store products in the open sun - only under a canopy.


When buying insulation in a cardboard box, make sure that it has not got wet. Dirty stains on the packaging, different density of cardboard - all this can indicate moisture ingress. The purchase should be abandoned, since there is a high probability that the material will lose its technical properties.
An important point: the glue used to connect the stone wool and the foil layer reduces the fire resistance of the finished product. This can be avoided by purchasing pierced basalt materials.


Subtleties of application
Stone wool is usually used for external insulation, which is due not only to the high thermal efficiency and moisture resistance of the material, but also the ability to avoid reducing the area of the room, which is inevitable when cladding walls from the inside.
To insulate the material outside, you should choose a dry, warm day. The air temperature should be + 5… +25 С, the humidity level should be no more than 80%. It is desirable that the sun's rays do not fall on the surface to be treated.
Regardless of whether basalt wool is fixed under plaster or a curtain facade, it is correct to start laying with preparatory work.

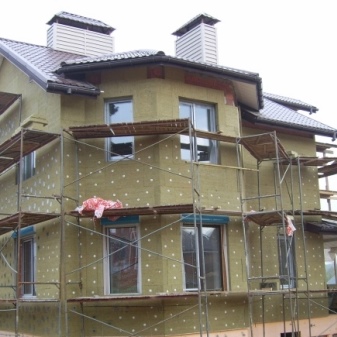
Preparation
At this stage, the facade should be freed from cement drips, protruding elements, pins. It is necessary to remove all communication: pipes, wires. It is imperative to eliminate gaps and cracks with cement mortar.
After you manage to achieve evenness and smoothness of the surface, you can start priming the facade. It should be applied in 2-3 layers, letting the previous one dry before applying the next one.
After the primed surfaces are completely dry, proceed to the installation of the frame. It consists of metal profiles that are attached to the wall with dowels.

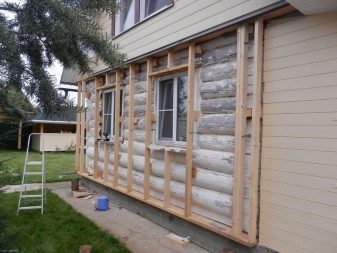
Mounting
The technology of laying basalt insulation depends on the type of facade. If the facade is finished with plaster, then the plates are attached to a special adhesive. The latter is preliminarily diluted with water in the proportions indicated on the package, after which it is thoroughly mixed.
The glue is applied to the surface of the insulation, after which the material is firmly pressed against the wall. It is important to install and smooth it before the adhesive fully adheres to the wall and cotton wool surfaces. After the previous product is fixed, the next plate is laid.



For additional reinforcement, holes are made in the center and on the sides of each insulation plate into which dowels are inserted.After the cotton wool is laid and fixed on the surface, it is covered with a thick layer of adhesive, and then the reinforcing mesh is pressed into it. Laying the latter starts from the corners, for which special reinforcing corners are used. After the corners are reinforced, after about a day, you can fix the mesh along the rest of the facade.


After another day, you can begin to plaster the walls. A rough finish is applied first, which is not perfectly smooth. However, gradually, layer by layer, the facade becomes smoother. When organizing hinged material with your own hands, after installing the frame, a waterproof film is attached to the wall, and on top of it - layers of stone wool. They do not need to be glued - they are immediately fixed with dowels.
To protect the insulation from wind and precipitation, a windproof membrane is used, it is laid on stone wool. It is important to fix 3 layers at once with one dowel: windproof, insulation and waterproof. The thickness of stone wool is selected based on climatic conditions and structural features of the building.

Finishing
Finishing for a "wet" facade begins with painting the plastered walls. For this, primer paint is used. For better adhesion to the surface of the walls, the latter are processed with fine emery paper. The finishing has 2 functions: protective and decorative. Plastered facades made by the "wet" method are widespread. The dry plaster mixture is diluted with water and applied to the prepared walls.
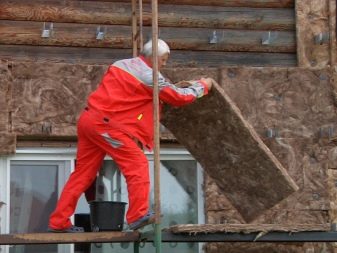


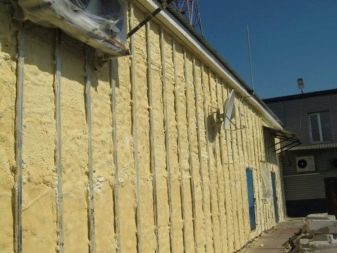
Corners, window and door openings and architectural elements are designed using additional structures. In order to increase the thermal efficiency of the building, they resort to organizing a ventilated facade, which can be hinged or made with the use of building mixtures. A feature of the ventilated facade is the air gap between the finish and the insulation.
Most curtain walls have such gaps, the general principles of their organization are described above. To organize a "wet" ventilated facade, the insulation after installation is also covered with a windproof vapor-vapor-proof material. A crate is stuffed to the walls, on which plasterboard sheets are fixed. It is important that an air gap of 25–30 cm remains between the layers of stone wool and the drywall sheets. Then the surface of the drywall is primed, the joints are carefully sealed, compared with the rest of the sheet. After the primer has dried, plaster is applied or the surface is painted.
In addition, facades plastered and painted with a primer can be painted with acrylic-based facade paints.



Suspended structures involve the use of vinyl siding, porcelain stoneware, artificial or natural stone slabs. They are attached to a frame made of a metal profile and secured with dowels. The presence of a locking mechanism on panels or finishing plates allows to provide increased reliability of the curtain wall, its wind resistance and the absence of gaps between individual elements.
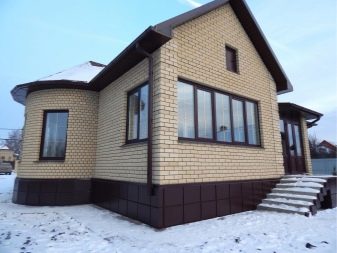
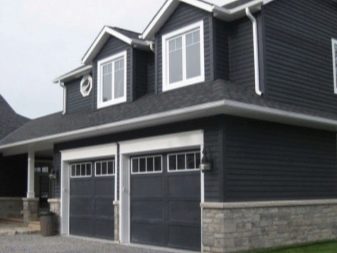
In the next video, you can learn more about the process of insulating the walls of the house from the outside.
The comment was sent successfully.