Heaters: types and features of materials
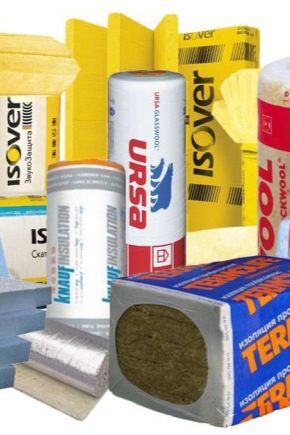
The issue of building insulation is especially relevant today. On the one hand, there are no big problems with the purchase of heat-insulating material - the construction market offers many options. On the other hand, it is this variety that gives rise to the problem - which insulation to choose?
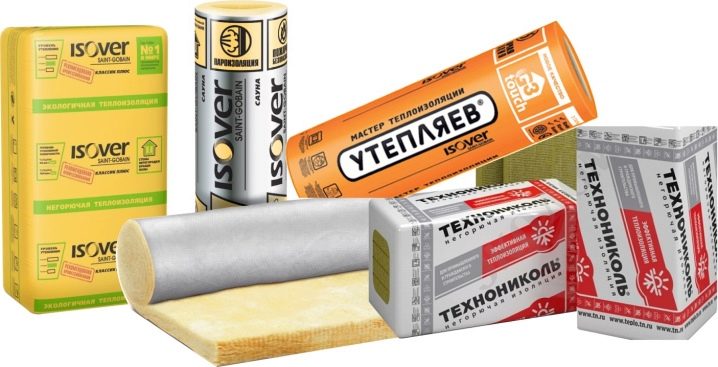
What it is?
The problem of thermal insulation of modern buildings (especially urban new buildings) is especially acute today. Thermal insulation is structural elements that reduce the heat transfer rates of materials and the structure (unit) as a whole.
Thermal insulation is also understood as a process that prevents the mixing of the thermal energy of the structure (refrigeration equipment, heating mains, etc.) and buildings with the external environment. In other words, the thermal insulation layer has a thermos effect.
Thermal insulation provides a comfortable indoor climate, keeping it warm during cold seasons and preventing excessive heat build-up on hot days.
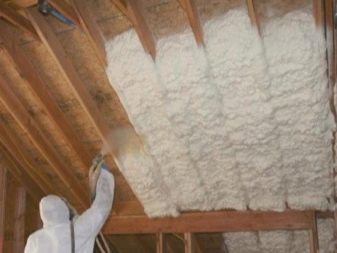
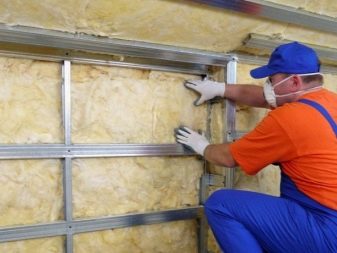
Using insulation can reduce electricity costs by up to 30-40%. In addition, most modern thermal insulation materials have sound insulation properties. A fairly common practice in the construction of a private house is the use of materials that are both insulating and structural element of walls and ceilings.
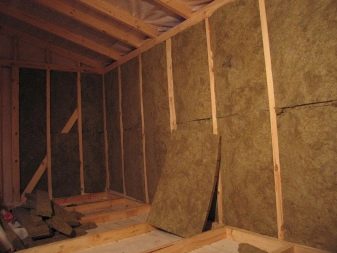
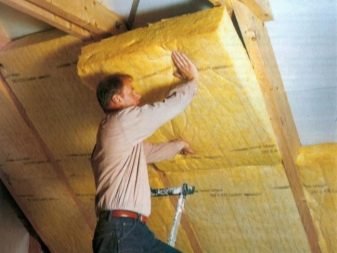
Depending on the thermal conductivity, the following classes of thermal insulation materials are distinguished:
- class A - materials with low thermal conductivity within 0.06 W / m kV. and below;
- class B - materials with an average thermal conductivity, the indicators of which are 0.06 - 0.115 W / m kV;
- class C - materials with high thermal conductivity equal to 0.115 -0.175 W / m kV.
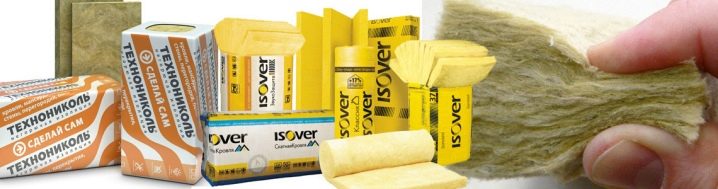
There are many ways to install insulation, but they all belong to one of these technologies:
- Monolithic wall - is a brick or wooden partition, the thickness of which for thermal efficiency must be at least 40 cm (depending on the region).
- Multilayer "pie" - a method in which the insulation is located inside the wall, between the outer and outer partitions. The implementation of this method is possible only at the construction stage or when facing the facade with brickwork (if the strength of the foundation allows or there is a separate base for the masonry).
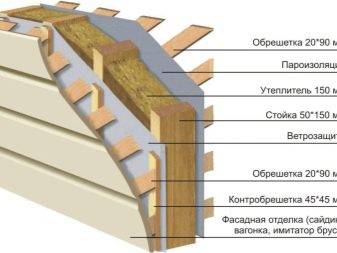
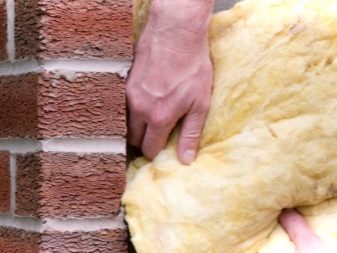
- External insulation - one of the most popular, due to its effectiveness, the method, which involves sheathing the outer walls with insulation, after which they are closed with facade materials. The organization of a ventilated facade allows to increase the thermal insulation performance, when an air gap remains between the wall with insulation and the facade finish. The method necessarily involves the use of vapor-permeable and waterproof coatings and films.
- Internal insulation - one of the most difficult and less effective in comparison with the external method of insulation. Provides insulation of surfaces from the inside of the building.
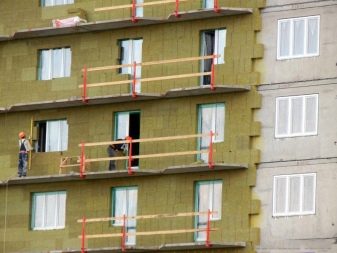
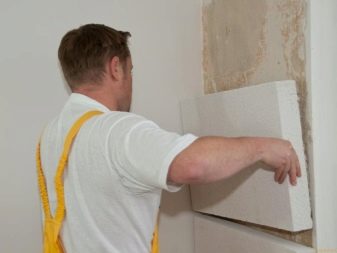
Specifications
All types of insulation are characterized by certain properties. The following are common:
- Low thermal conductivity. Thermal efficiency indicators are the main ones when choosing a heater.The lower the coefficient of thermal conductivity (measured in W / (m × K) shows the amount of thermal energy passing through 1 m3 of dry insulation at a temperature difference of 10C), the less heat loss the material has. The warmest is polyurethane foam, which has a thermal conductivity coefficient of 0.03. Average values are about 0.047 (thermal conductivity index of expanded polystyrene, mineral wool grade P-75).
- Hygroscopicity. That is, the ability of the insulation to absorb moisture. High-quality insulation does not absorb moisture or absorbs a minimum amount of it. Otherwise, it is impossible to avoid getting the material wet, which means the loss of the main property (thermal efficiency).
- Vapor barrier. The ability to pass water vapor, thereby ensuring an optimal level of humidity in the room and keeping walls or other work surfaces dry.
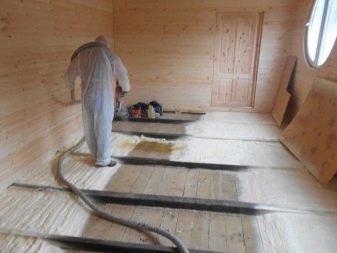
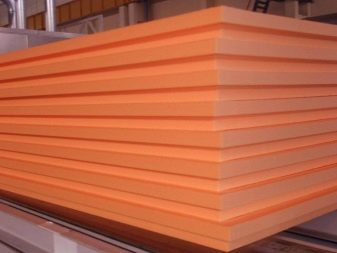
- Fire resistance. Another important characteristic of a heat-insulating material is its resistance to fire. Some materials have a high fire hazard, their combustion temperature can reach 1000 degrees (for example, basalt wool), while others are extremely unstable to high temperatures (expanded polystyrene). Most modern heaters are self-extinguishing materials. The appearance of open fire on their surface is almost impossible, and if it does occur, the burning time does not exceed 10 seconds. During combustion, no toxins are released, the mass of the material during combustion is reduced by at least 50%.
Combustion toxicity is usually mentioned when talking about fire resistance. The optimum is a material that, even when heated, does not emit hazardous toxic compounds.
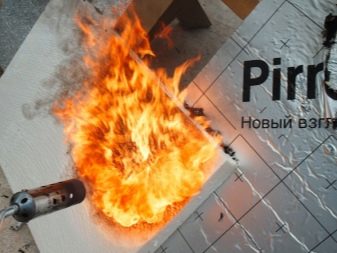
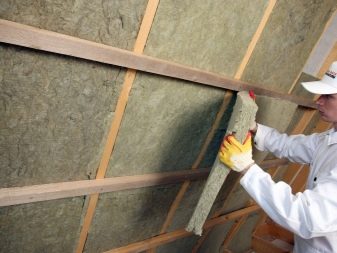
- Environmental friendliness. Environmental friendliness is especially important for indoor materials. The key to environmental friendliness is usually the naturalness of the composition. So, for example, basalt insulation, considered safe from the point of view of environmental friendliness, is made from recycled rocks, expanded clay - from sintered clay.
- Soundproofing characteristics. Not all thermal insulation materials can be used for sound insulation. However, most of them have both of these properties, for example, mineral wool insulation, polyurethane foam. But the widely used polystyrene foam does not give a soundproofing effect.
- Biostability. Another criterion that is important for the buyer is biostability, that is, the resistance of the material to mold, fungus, the appearance of other microorganisms, rodents. The strength and integrity of the material, which means its durability, directly depends on biostability.
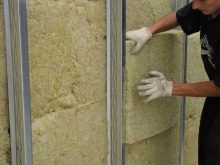
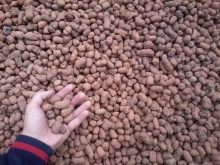
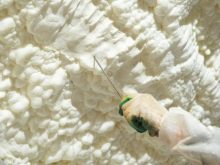
- Resistant to deformation. Insulation must withstand loads, since it can be located on the floor surface, loaded structural elements, between partitions. All this dictates the requirements for its resistance to loads and deformations. Durability depends largely on the density and thickness of the material.
- Durability. The duration of operation largely depends on the thermal efficiency, moisture resistance, vapor permeability and biostability of the material. For high-quality products (for example, polyurethane foam, basalt wool), a fairly long, up to 50 years, guarantee is given. Another factor in durability is compliance with installation technology and operating conditions.
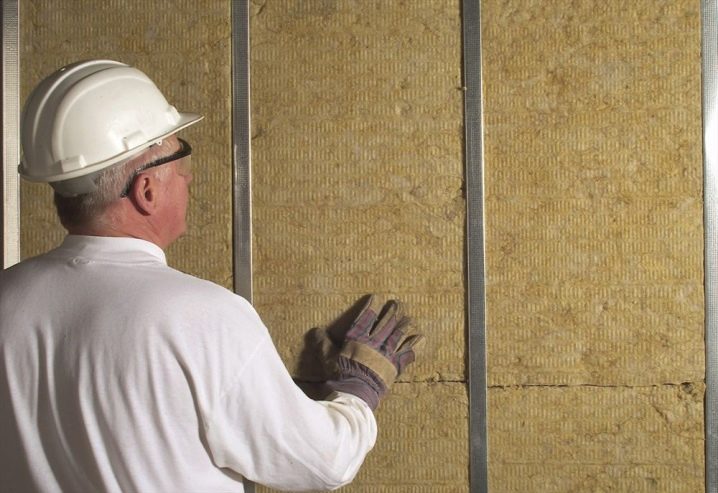
- Simplicity of installation and installation. Most of the heaters have a convenient form of release - in mats, rolls, sheets. Some of them are easily fixed on the insulated surface, without requiring special skills and equipment (foam sheets), while others require compliance with certain installation conditions (for example, when working with mineral wool insulation, it is necessary to protect the respiratory organs, hands).
There are also such types of insulation, the installation of which is possible only by specialists with special equipment (for example, polyurethane foam is sprayed with a special unit, the employee must use a protective suit, goggles and a respirator).
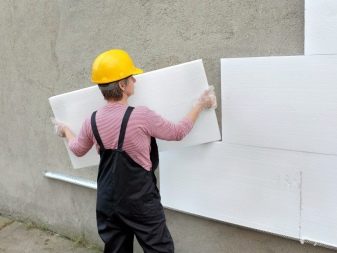
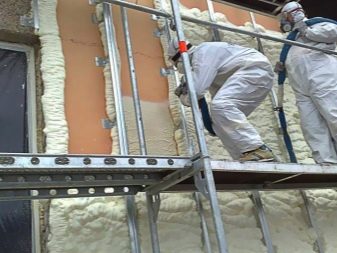
Types of jobs
Thermal insulation refers to the process of reducing heat loss to the calculated values (individual for each region and objects). This term is similar to the concept of "thermal insulation", which means the protection of an object from the negative exchange of thermal energy with the air. In other words, the task of thermal insulation work is to maintain the specified temperature indicators of the object.
The object can mean residential and office buildings, industrial and engineering structures, medical and refrigeration equipment.
If we talk about thermal insulation of residential and industrial premises, then it can be external (another name is facade insulation) and internal.
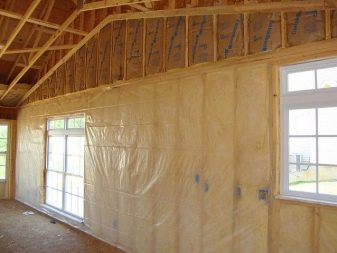
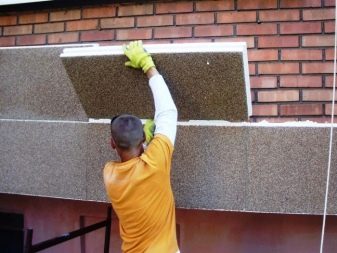
Thermal insulation of external walls of residential buildings is always preferable to thermal insulation of internal parts. This is due to the fact that external thermal insulation turns out to be more effective, with internal thermal insulation there is always 8-15% heat loss.
In addition, the "dew point" with internal insulation shifts inside the insulation, which is fraught with dampness, an increase in the level of humidity in the room, the appearance of mold on the walls, destruction of the wall surface, finishing. In other words, the room is still cold (since damp insulation cannot prevent heat loss), but damp.
Finally, the installation of insulation from the inside takes up space, reducing the usable area of the room.
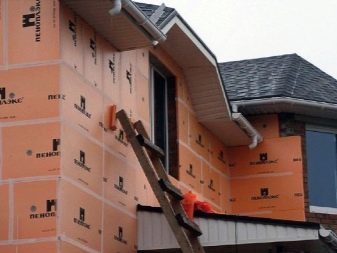
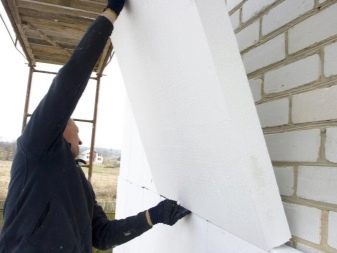
At the same time, there are situations when internal thermal insulation remains the only possible way to normalize the temperature. Strict adherence to installation technologies allows avoiding the unpleasant consequences of thermal insulation. Be sure to take care of the vapor and waterproofing of surfaces, as well as high-quality ventilation. A standard supply system is usually not enough, it is required to install a forced air circulation system or use windows with special valves that provide air exchange.
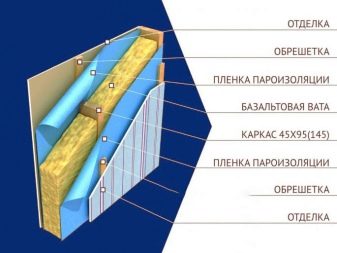
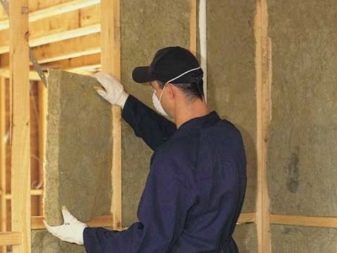
To increase the efficiency of external insulation, they resort to organizing a ventilated facade system or a three-layer system. In the first case, an air gap remains between the insulation and the facing material mounted on a special frame. The three-layer system is a wall covering erected by a well method, between which insulation is poured (expanded clay, perlite, ecowool).
As for the finishing, both "wet" (building mixtures are used) and "dry" facade (fasteners are used) facade can be insulated.
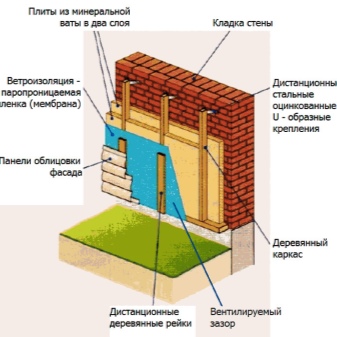
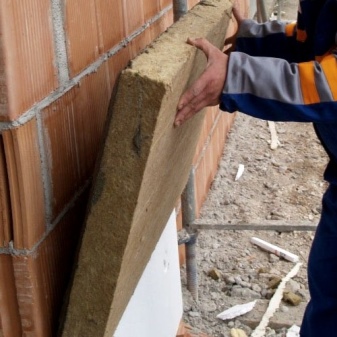
Often, a room requires not only insulation, but also sound insulation. In this case, it is more convenient to use materials that immediately have both heat and sound insulation properties.
When talking about insulating a house inside or outside, it is important to understand that walls are far from the only source of heat loss. In this regard, it is necessary to isolate unheated attics and basements. When using an attic, you should consider a multilayer insulated roof system.
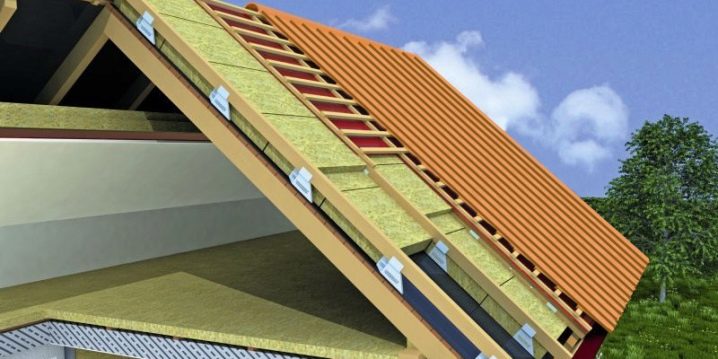
When carrying out internal thermal insulation work, great attention should be paid to the joints between the floor and the wall, the wall and the ceiling, the wall and partitions. It is in these places that "cold bridges" are most often formed.
In other words, regardless of the type of work performed, it is important to remember that thermal insulation requires an integrated approach.
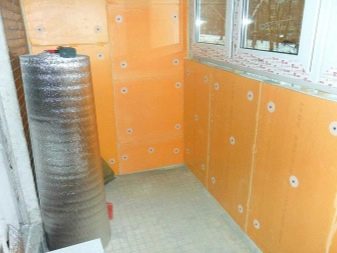
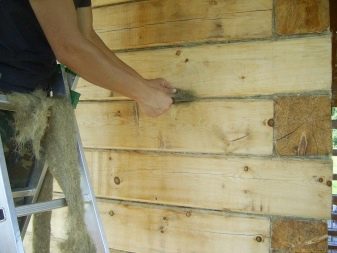
Variety of materials
All heaters, depending on the raw materials used, are divided into:
- organic (have an environmentally friendly composition - waste from agricultural, woodworking industries, the presence of cement and some types of polymers is permissible);
- inorganic.
There are also mixed products.
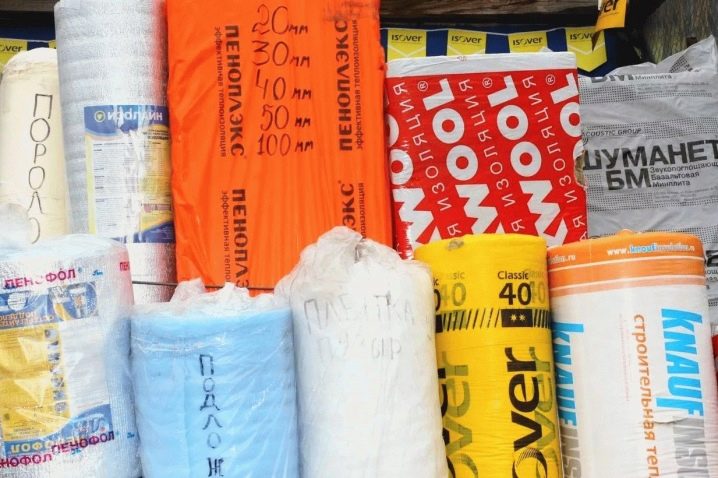
Depending on the principle of functioning, heaters are:
- reflective view - reduces heat consumption by directing heat energy back into the room (for this, the insulation is equipped with a metallized or foil-clad element);
- warning type - are characterized by low thermal conductivity, preventing the release of a large amount of thermal energy outside the insulated surface.
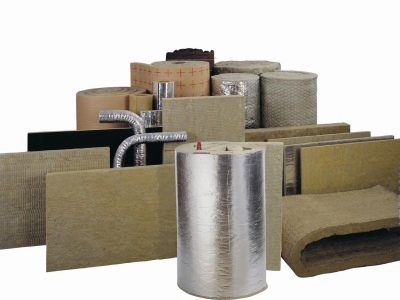
Let's take a closer look at the most popular types of organic insulation:
Ecowool
It is considered to be cellulose insulation, 80% consists of recycled cellulose. It is an environmentally friendly material with low thermal conductivity, good vapor permeability and sound insulation.
The addition of fire retardants and antiseptics to the raw material allows to reduce the combustibility of the material and increase its biostability.
The material is poured into inter-wall spaces; it is possible to spray onto flat surfaces by dry or wet method.
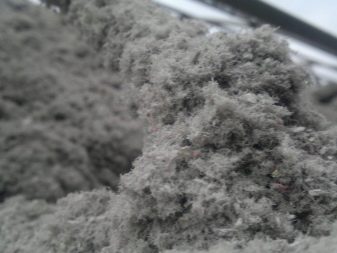
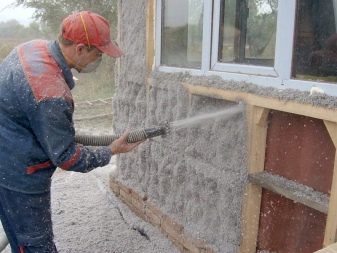
Jute
A modern substitute for tow, traditionally used to reduce heat loss in inter-crown gaps in timber buildings. Produced in the form of ribbons or ropes, in addition to high thermal efficiency, it does not require replacement even after the walls have shrunk.
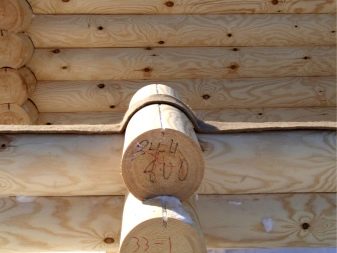
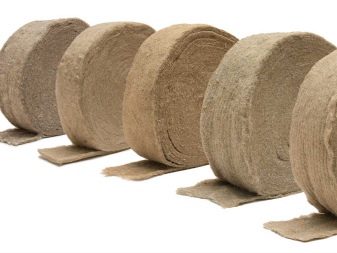
Chipboard
Insulation, 80-90% consisting of fine shavings. The rest of the components are resins, fire retardants, water repellents. It differs not only in good heat, but also in sound insulation properties, is environmentally friendly, durable.
Despite the treatment with water repellents, it still does not have high moisture resistance.
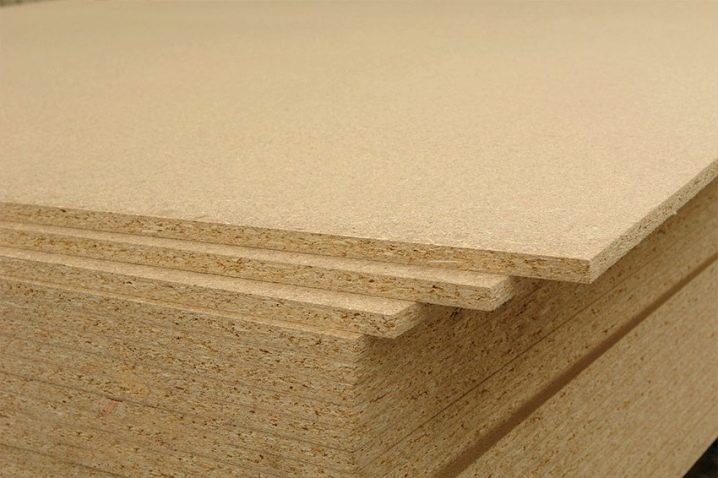
Cork
Heat insulator based on cork oak bark, available in roll or sheet form. It is used only as an internal insulation. Acts as a basis for wallpaper, laminate and other floor coverings. It can be used as an independent topcoat due to its unusual but noble appearance. Often they insulate panel houses from the inside.
In addition to thermal efficiency, it provides sound insulation and decorative effect. The material is hygroscopic, so it can only be mounted on dry surfaces.
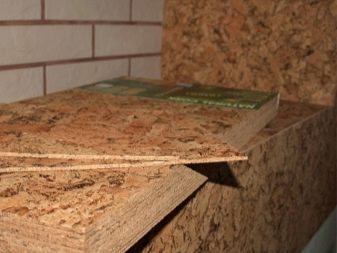
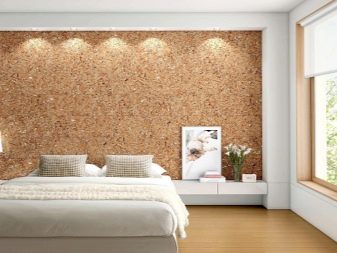
Arbolit
It is a block of chipboard concrete. Thanks to the wood in the composition, it has heat and sound insulating properties, while the presence of concrete provides moisture resistance, resistance to damage and the strength of the material. It is used both as insulation and as independent building blocks. It was widely used as a material for frame-panel buildings.
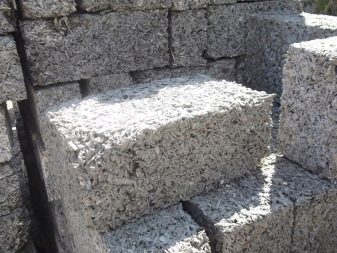
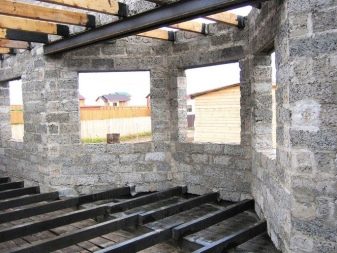
The modern market for inorganic thermal insulation materials is somewhat wider:
Expanded polystyrene
There are 2 known modifications of it - foamed (otherwise - foam) and extruded. It is a set of combined bubbles filled with air. The material being extruded differs in that each air cavity is isolated from the adjacent one.
Polyfoam is suitable for external and internal insulation, characterized by high thermal insulation performance. It is not vapor-permeable, therefore it requires a reliable vapor barrier. It is worth noting the low moisture resistance of the foam, which makes the installation of waterproofing mandatory.
In general, the material is affordable, lightweight, easy to cut and assembled (glued). For the needs of the buyer, material plates are produced in various sizes and thicknesses. The latter directly affects thermal conductivity.
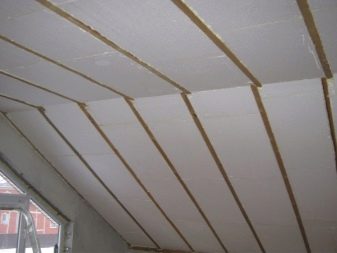
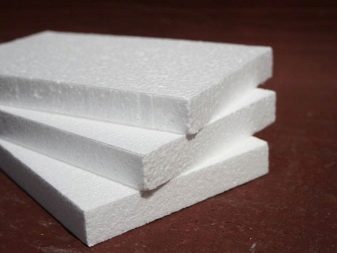
At first glance, foam is a worthy option for insulation. However, it should be remembered that during operation it emits toxic styrene. The most dangerous thing is that the material is subject to burning. Moreover, the fire rapidly engulfs the foam, in the process of increasing temperatures, compounds hazardous to human health are released.This was the reason for the ban on the use of foam for interior decoration in some European countries.
Polyfoam is not durable. Already 5-7 years after its use, destructive changes in the structure are found - cracks and cavities appear. Naturally, even minor damage causes significant heat loss.
Finally, this material is quite fond of mice - they gnaw it, which also does not contribute to long-term operation.
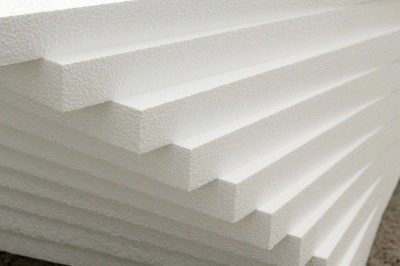
Extruded polystyrene foam is an improved version of polystyrene foam. And, although its thermal conductivity is slightly higher, the material demonstrates the best indicators of moisture resistance and fire resistance.
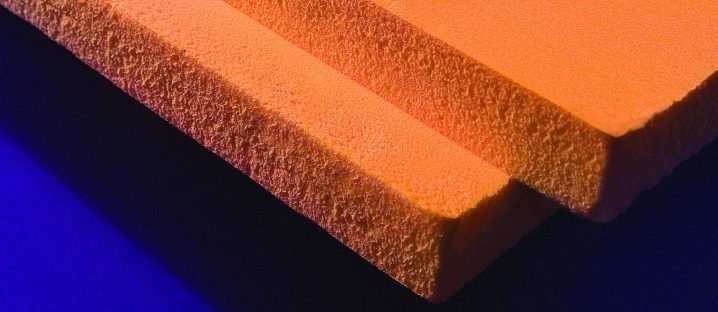
Polyurethane foam
Heat insulating material sprayed onto the surface. It has the best thermal efficiency, due to the installation method it forms a uniform hermetic layer on the surface, fills all cracks and seams. This becomes a guarantee of the absence of "cold bridges".
In the process of spraying, the material releases toxic components, therefore, it is applied only in a protective suit and a respirator. As the toxins harden, they evaporate, therefore, during operation, the material demonstrates complete environmental safety.
Another advantage is incombustibility, even under the influence of high temperatures, the material does not emit hazardous compounds.
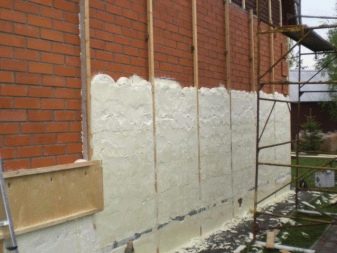
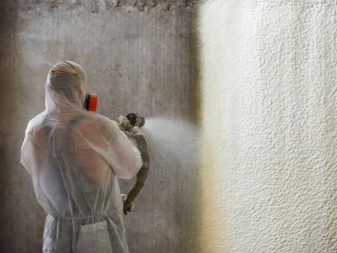
Among the shortcomings, one can single out low values of vapor permeability, which is why it is not even recommended to apply the material on wooden bases.
This method of application does not allow achieving a perfectly flat surface, therefore, the use of contact finishing (painting, plaster) is almost always excluded. Leveling (as well as removing the polyurethane foam layer) is a rather complicated and time-consuming process. The solution will be to use hinged structures.

Penofol
Universal insulation based on polyethylene foam. The air chambers from which the material is formed provide low thermal conductivity. The main difference between penofol is the presence of a foil layer on one side, which reflects up to 97% of thermal energy, while not heating up.
In addition to high values of thermal insulation, it demonstrates sound insulation properties. Finally, it does not require the use of vapor barrier and waterproof coatings, and is easy to install.
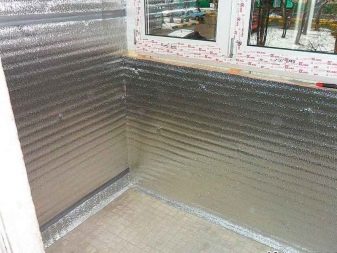
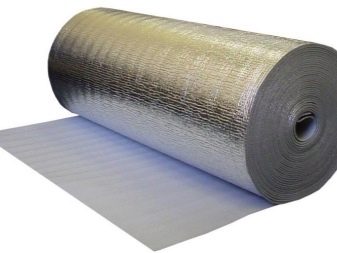
Among the disadvantages is the higher cost, however, it is leveled by the impressive indicators of the heat resistance of the product. Its use can reduce heating costs by a third.
Despite the strength of the material, it is not suitable for wallpapering or plastering. Penofol will not withstand the load and will collapse, therefore the walls treated with it are closed with plasterboard. Finishing is done already on it. It can act as a heater not only for walls, but also for the ceiling and floor.
Penofol is an excellent underlay for most floor coverings, as well as underfloor heating systems.
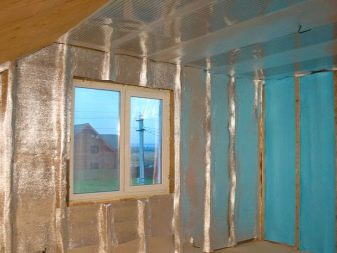
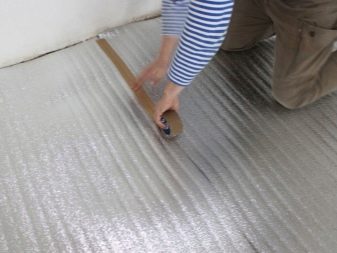
Fiberboard slabs
It is a wood-based board, bonded with a cement composition. Usually used for outdoor decoration, they can act as an independent building material.
They are characterized by heat and sound insulating properties, however, they have considerable weight (it is necessary to strengthen the foundation and supporting structures), as well as low moisture resistance.
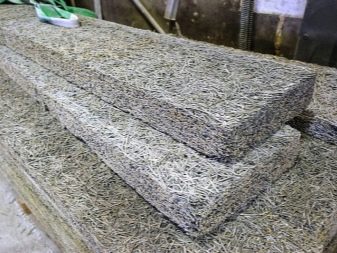
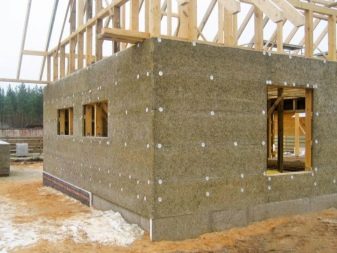
Liquid ceramic insulation
A relatively new insulating material. Outwardly, it resembles acrylic paint (applied, by the way, in the same way), which contains vacuumized bubbles. Thanks to them, a thermal insulation effect becomes possible (according to the manufacturers, a 1 mm layer replaces brickwork 1.5 bricks thick).
Ceramic insulation does not require a subsequent layer of finishing and does quite well with the function of a finishing material as well. It is used mainly indoors, since it does not take up useful space.
The moisture-resistant layer extends the service life of the coating and makes it possible to wet cleaning. The material is fire-resistant, non-combustible, moreover, it prevents the spread of flame.
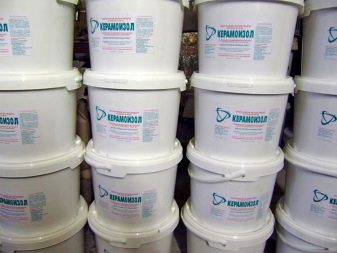
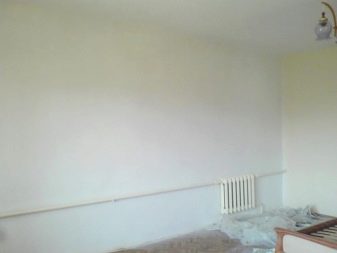
Mineral wool insulation
This type of insulation is distinguished by a fibrous structure - the material is a randomly arranged fiber. Air bubbles accumulate between the latter, the presence of which provides a heat-insulating effect.
Available in the form of mats, rolls, sheets. Due to its ability to easily recover and maintain its shape, the material is easy to transport and store - it is rolled up and packed in compact boxes, and then easily takes the given shape and dimensions. Sheet material is usually thinner than other options.
Tiles, wall panels, siding, corrugated board for external cladding and clapboard or drywall (as cladding) for internal cladding are usually used as a facade coating.
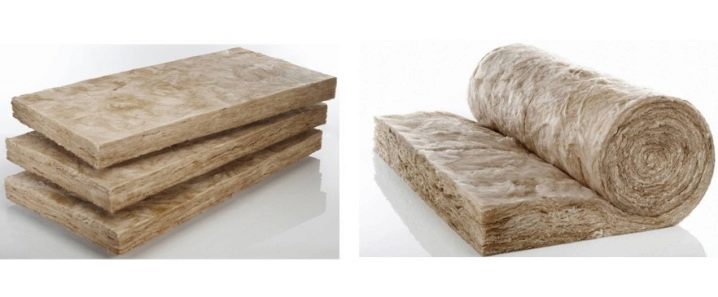
When working, you must take care of the presence of a respirator. During installation, material particles rise into the air. Once in the lungs, they irritate the mucous membranes of the upper respiratory tract.
Depending on the raw materials used, 3 types of mineral wool are distinguished - based on slags, glass and basalt fibers.
The first type of insulation has high thermal conductivity and the ability to absorb moisture, it is flammable and short-lived, and therefore is rarely used for insulation.
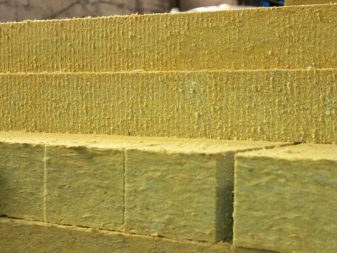
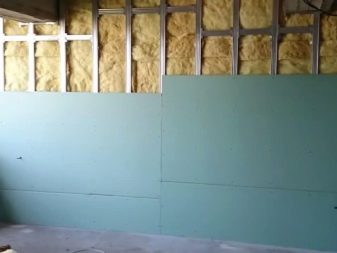
Fiberglass demonstrates the best thermal insulation characteristics, the combustion temperature is 500 degrees. The material does not burn, but decreases in volume under the influence of temperatures above the indicated ones.
According to the description of users, the material is biostable and has an affordable price. Due to its elasticity, it is suitable for finishing buildings and structures of complex shapes and configurations. Among the shortcomings, one can note the low indicators of water resistance (high-quality waterproofing is required), the ability to release toxic compounds (because of this, it is used mainly for external insulation or requires reliable protection).
Thin and long fibers of glass wool dig into the skin, causing irritation. Finally, having an amorphous component (glass) in its composition, glass wool shrinks, gradually becoming thinner during operation, which causes a decrease in thermal insulation properties.
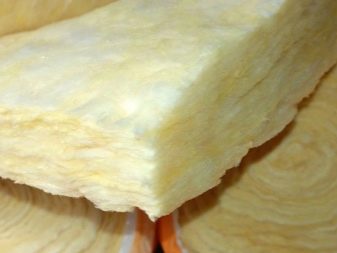
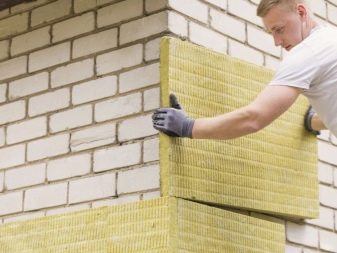
Basalt wool is obtained by melting rocks (basalt, dolomite). Fibers are drawn from semi-liquid raw materials, which are then subjected to pressing and short-term heating. The result is a durable, vapor-permeable insulation with low thermal conductivity.
Stone wool is treated with special impregnations, which makes it resistant to moisture. It is an environmentally friendly, non-combustible material for a wide range of applications.
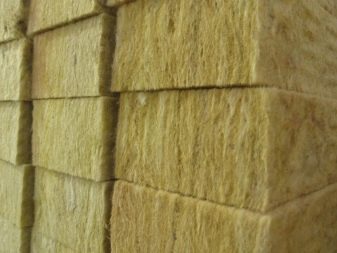
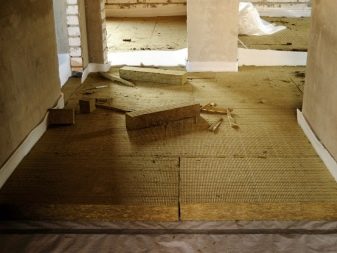
Warm plaster
Plastering and finishing mixture, which contains particles of such heat-insulating materials as perlite, vermiculite.
Possesses good adhesion, fills cracks and joints, takes the given shape. Performs 2 functions at once - heat-insulating and decorative. Depending on the place of use, it can be on cement (for outdoor decoration) or gypsum (for indoor decoration) bases.
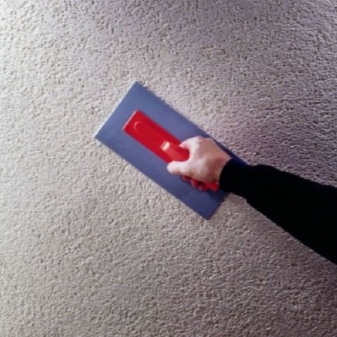
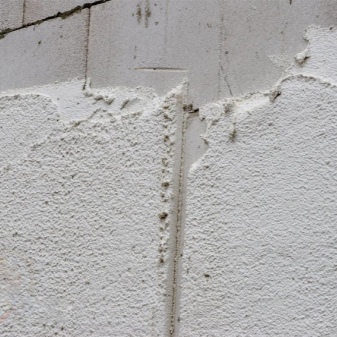
Foam glass
The basis of the material is glass recyclable materials, which are fired in high-temperature furnaces to the state of sintering. The result is an insulation material characterized by moisture resistance, high fire safety and biostability.
Possessing record strength indicators among other heaters, the material is easily cut, mounted, plastered. Release form - blocks.
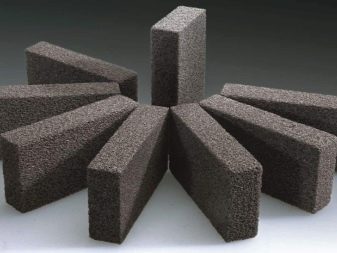
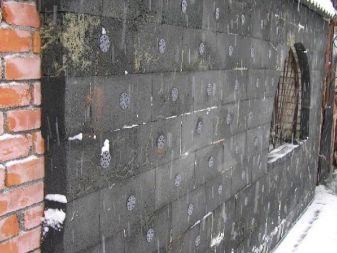
Vermiculite
It is a loose insulation on a natural basis (processed rocks - mica). They are distinguished by fire resistance (melting temperature - not less than 1000 degrees), vapor permeability and moisture resistance, do not deform and do not settle during operation. Even when wet, up to 15% is able to retain its thermal insulation properties.
It is poured into inter-wall spaces or on flat surfaces (for example, an attic) for thermal insulation. Given the high cost of vermiculite, such a method of insulation will not be cheap, so it can often be found in warm plasters. Thus, it is possible to reduce the cost of raw materials for thermal insulation, but not to lose the brilliant technical properties of the material.
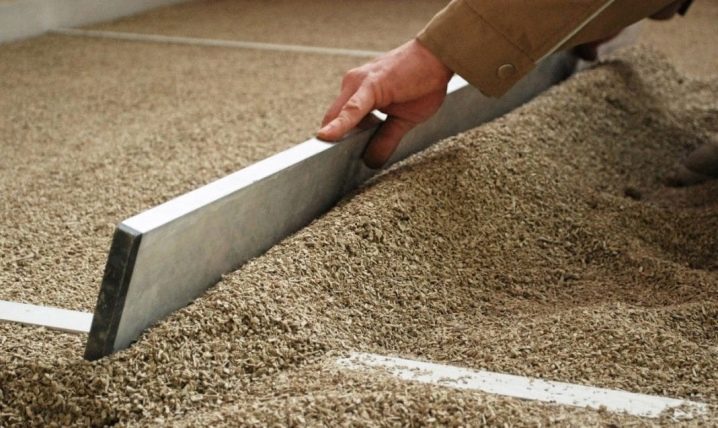
Expanded clay
Loose insulation known for a long time. It is based on a special clay that is sintered in the process of high-temperature firing. The result is extremely light "stones" (as well as crushed stone and sand) with high thermal insulation qualities. The material does not deform, is biostable, but extremely hygroscopic.
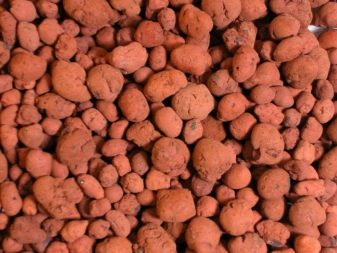
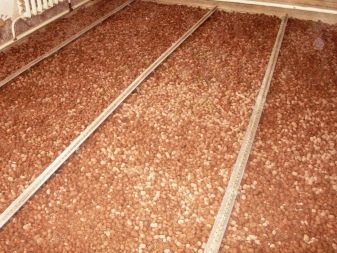
Expanded polystyrene granules
The same air capsules that form the basis of polystyrene foam boards. True, here they are not fastened together and are supplied in bags. They have the same characteristics as polystyrene foam boards - low thermal conductivity, light weight, high fire hazard, lack of vapor permeability.
For insulation, the material should not be poured into voids, but sprayed with a compressor. This is the only way to increase the density of the material, which means to increase its insulating capacity.
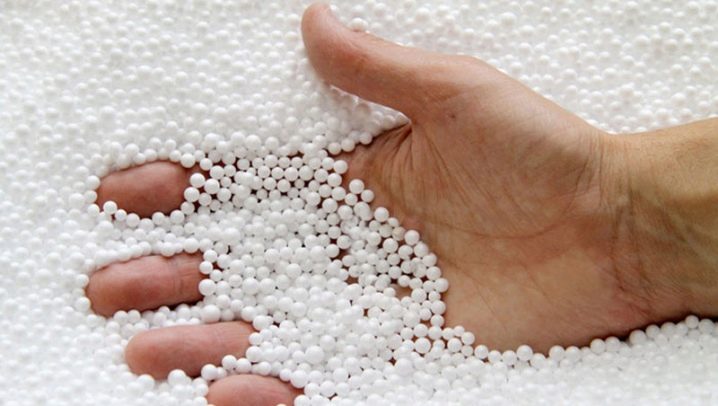
Penoizol
Outwardly it looks like small flakes (the material has a finer fraction in comparison with expanded polystyrene granules, softer). Natural resins are the basis. The main advantages are low thermal conductivity, moisture resistance and vapor permeability, fire resistance. Usually used for walls and ceilings, which are sprayed with special equipment.
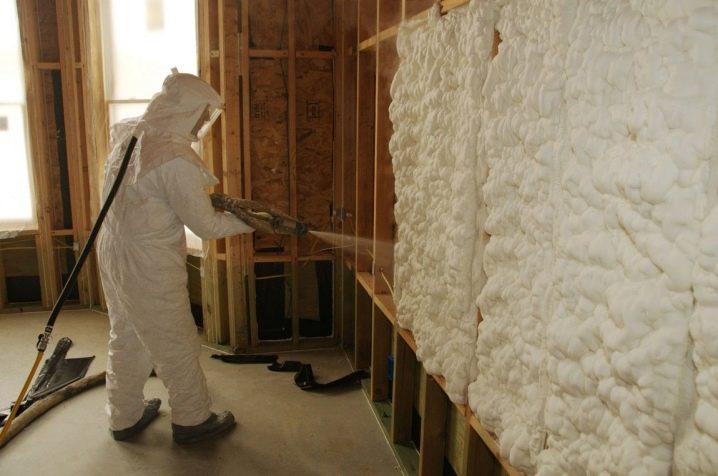
Manufacturers
There are a large number of thermal insulation materials on the market today. Choosing the best products is not easy, especially if you are completely unfamiliar with the brands offered.
However, there are manufacturers whose products are a priori of high quality. Among them is the Danish stone wool manufacturer Rockwool. The product line is wide enough - a variety of materials of different forms of release, dimensions and density. The most popular is 10 cm cotton wool for outdoor decoration.
Among the most famous lines:
- "Light Batts" - material for insulation of private houses made of wood;
- "Light Batts Scandik" - material for insulation of private houses made of stone, concrete, brick;
- "Acustik Batts" - material with improved soundproofing performance, used for the insulation of office buildings, shopping and entertainment facilities, industrial facilities.
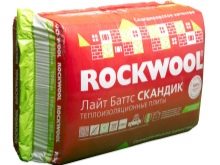
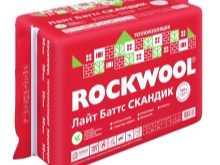
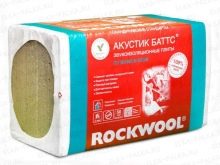
The rating of producers of mineral wool materials is also invariably headed by the French company Isover. In the product line, you can find a fairly rigid material that is laid on flat horizontal surfaces and does not require fasteners, as well as two-layer facade counterparts. Universal insulation, options for pitched roofs, as well as mats with improved sound insulation characteristics are in demand.
Most of the products are delivered in 7 and 14 meter rolls, the thickness of which is 5-10 cm.
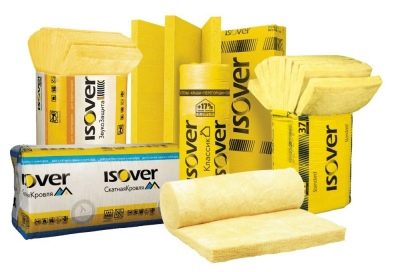
High-quality heat and sound insulation materials are produced under the trademark Ursa. The following types of insulation can be found on sale:
- "Ursa Geo" a series of mats and rolls of various hardness for thermal insulation of all areas of the house, including basements and attic spaces;
- "Ursa Tetra" - slabs characterized by high strength and the presence of additional hydrophobic impregnation;
- "Ursa PureOne" - soft fiberglass with acrylic as a binding component.Due to the environmental friendliness of the material, it is suitable for use in hospitals and child care facilities;
- "Ursa XPS" represents polystyrene foam plates of increased rigidity.
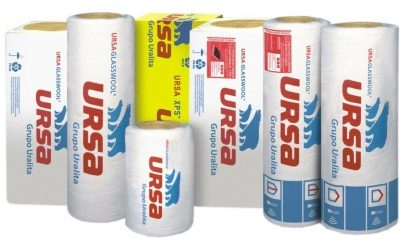
The German quality known to all is demonstrated by the products of German production Knauf. All the variety of manufactured products can be attributed to one of the series - "Knauf Insulation" (materials for professional insulation of multi-storey residential buildings, hospitals, administrative institutions) or "Knauf Heat" (materials for insulation of private houses).
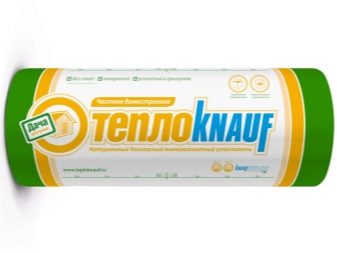
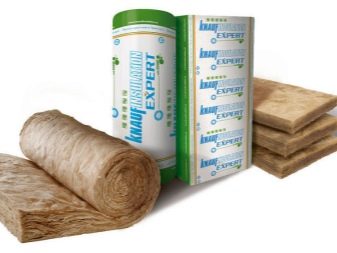
Brand insulation is considered an excellent solution for organizing a ventilated facade. Izovol... The slabs are rigid enough to withstand loads, have moisture-resistant impregnation, and are additionally reinforced with fiberglass. The most popular are the following product lines:
- general technical insulation (universal insulation for the attic and roof, walls, floor);
- technological cylinders and mats with a moisture-resistant foil layer to insulate pipelines;
- slab insulation for the manufacture of sandwich panels;
- thermal insulation mats with improved sound insulation performance.
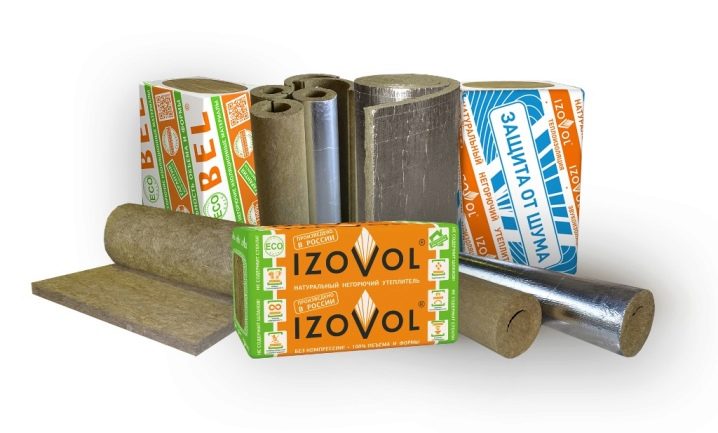
The leading domestic manufacturer of heaters is the TechnoNIKOL company. The main direction of production is the production of basalt wool and polystyrene foam insulation. The material does not deform, withstands heavy loads, and has increased sound insulation properties.
Depending on the type of product, the density and thermal conductivity of the material changes. There are the following types of TechnoNICOL products:
- "Rocklight" - slabs with increased strength characteristics and intended for insulation of a private house;
- "Technoblok" - a material suitable for the installation of facades, acts simultaneously as a structural element and insulation;
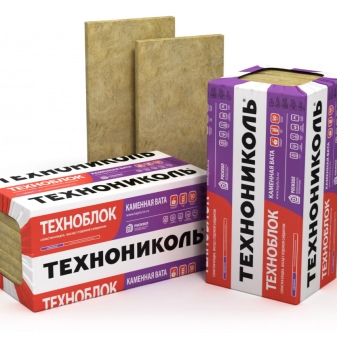
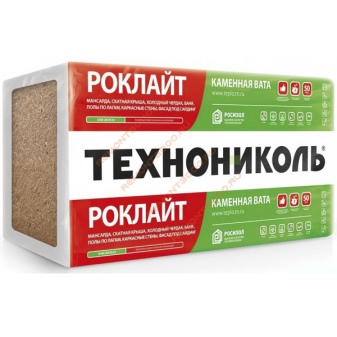
- "Teploroll" - elongated rectangular mats with reduced phenol content in the composition;
- "Technoacoustic" - heat insulator with improved performance of sound insulation (reduces noise up to 60 dB), used for sound insulation of offices, entertainment venues.
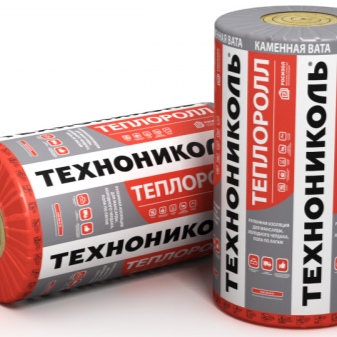
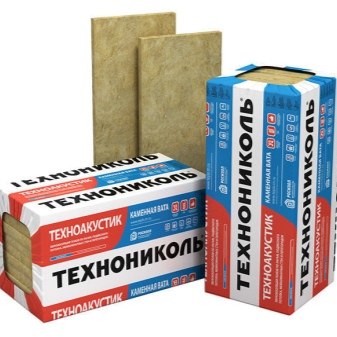
A worthy place in the rating of manufacturers of materials for insulation is occupied by the Belarusian company "Beltep". The products are only slightly inferior in quality to European counterparts, but they have a more affordable cost. Among the advantages - a special hydrophobic impregnation, increased sound insulation qualities.
If you are looking for high-quality and relatively safe from the point of view of environmental friendliness expanded polystyrene, then you should pay attention to brand products Europlex... The manufacturer's line includes both expanded and extruded polystyrene foam. The density of the material ranges from 30 to 45 kg / m³, depending on the type of product.
There are several size options for the buyer's choice. So, the length of products can be 240, 180 and 120 cm, width - 50 or 60 cm, thickness - 3-5 cm.
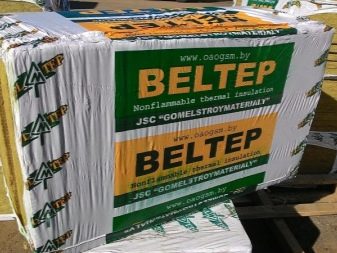
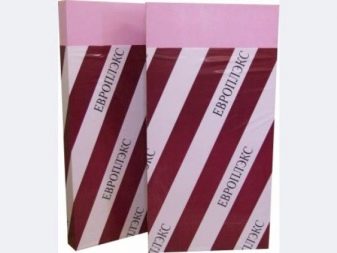
Extruded polystyrene foam is also distinguished by high strength and increased moisture resistance. "Penoplex"... The experiments carried out demonstrate the frost resistance of the material. Even after 1000 freeze / thaw cycles, the thermal efficiency of the material is reduced by no more than 5%.
As you know, styrene foam is the cheapest insulation, and since both companies are domestic, we can talk about significant savings.
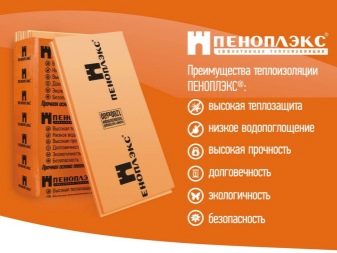
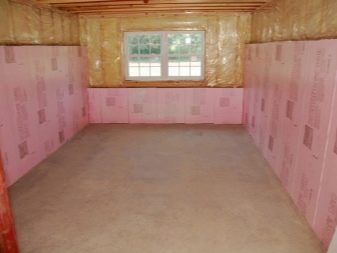
How to choose?
When choosing a thermal insulation material, it is important to focus on the material from which the walls or other surfaces to be insulated are made.
- For wooden walls, a related cellulose insulation, fiberglass or stone wool is suitable. True, it is necessary to carefully consider the waterproofing system. Jute will help to close the gaps. For frame-panel buildings, you can use fiber cement slabs or wood concrete blocks, which will act as wall structural elements.Between them, you can fill in bulk insulation (expanded clay, ecowool).
- For outdoor insulation, foam styrene insulation, mineral wool is well suited. When facing such structures with bricks, it is permissible to fill in expanded clay, perlite, ecowool formed between the facade and the main wall. Polyurethane foam has proven itself well.
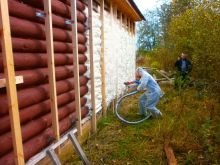
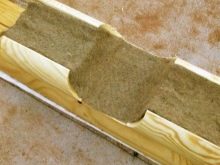
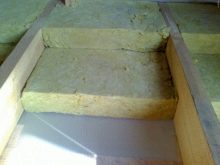
- For internal insulation of brick buildings, mineral wool heaters are traditionally used, which are sewn up with plasterboard sheets.
- Concrete surfaces with the worst thermal insulation performance are recommended to be insulated on both sides - external and internal. For outdoor insulation, it is better to choose a ventilated facade system. Warm plaster or hinged panels, siding are suitable as finishing materials. For interior decoration, you can use cork insulation, a thin layer of expanded polystyrene or mineral wool, decorated with drywall.
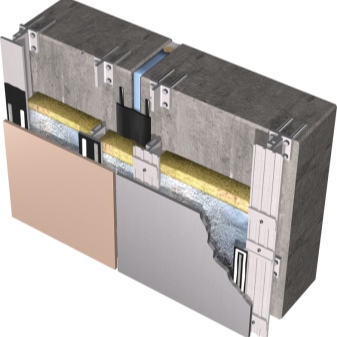
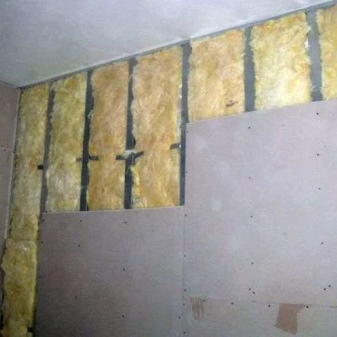
How to calculate?
Different heaters have different thicknesses, and it is very important to calculate the required parameters of the heater before making a purchase. Too thin a layer of insulation will not cope with heat loss, and will also cause the "dew point" to move inside the room.
An excess layer will not only lead to an unjustified load on the supporting structures and inappropriate financial costs, but will also cause a violation of the air humidity in the room, a temperature imbalance between different rooms.
To calculate the required thickness of the material, it is necessary to set the resistance coefficient of all materials used (insulation, waterproofing, facing layer, etc.).
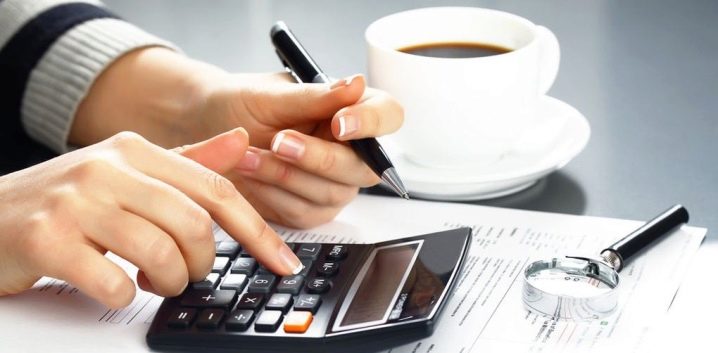
Another important point is the determination of the material from which the wall is made, since this also directly affects the thickness of the insulation.
Given the type of wall material, conclusions can be drawn about its thermal conductivity and thermal performance. These characteristics can be found in SNiP 2-3-79.
The density of the heat-insulating material can be different, but most often products with a density in the range of 0.6-1000 kg / m3 are used.
Most of the modern high-rise buildings are built of concrete blocks, which have the following (important for calculating the thickness of the insulation) indicators:
- GSPN (calculated in degrees-days during the heating season) - 6000.
- Heat transfer resistance - from 3.5 C / m kV. / W (walls), from 6 S / m kV. / W (ceiling).

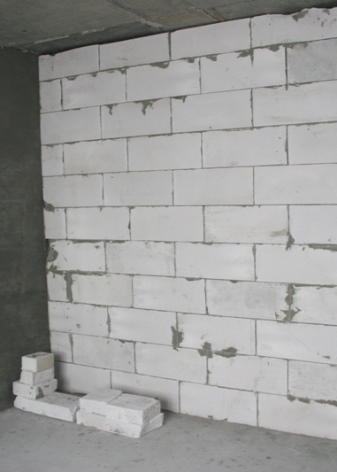
To bring the indicators of heat transfer resistance for walls and ceilings to the appropriate parameters (3.5 and 6 C / m kV / W), you need to use the formulas:
- walls: R = 3.5-R walls;
- ceiling: R = 6-R ceiling.
After finding the difference, you can calculate the required thickness of the insulation. The formula p = R * k will help in this, in which p will be the desired indicator of thickness, k is the thermal conductivity of the insulation used. If the result is not a round (whole) number, then it should be rounded up.
Experts recommend using a 10 cm layer of insulation when choosing expanded polystyrene or mineral wool.
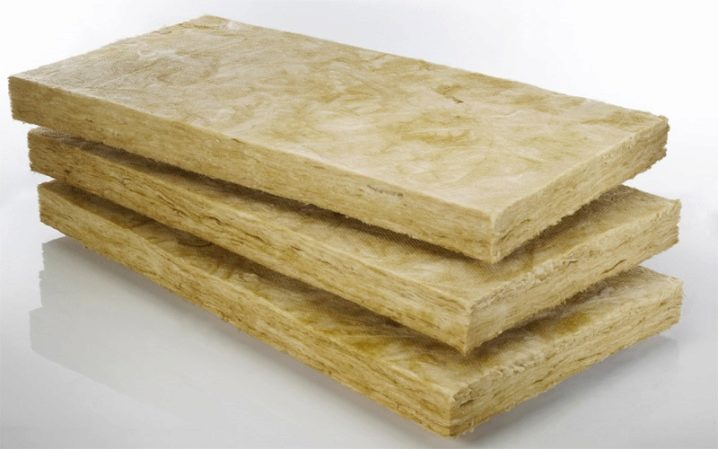
If independent calculations using the formulas seem quite complicated to you, you can use special calculators. They take into account all important scoring criteria. The user only needs to fill in the required fields.
It is best to use calculators made by reputable manufacturers of thermal insulation materials. So, one of the most accurate is a calculator developed by the Rockwool brand.
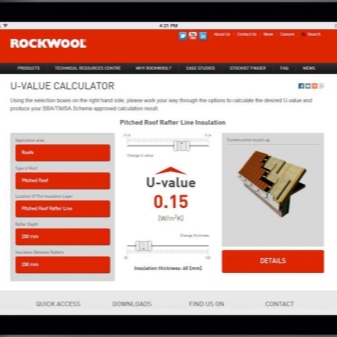
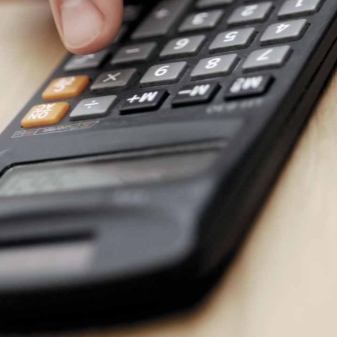
Application Tips
- Modern mineral wool insulation is supplied in rolls, mats and sheets. The last 2 delivery options are preferable, since they are easier to join without forming gaps and cracks.
- When installing plate heaters, make sure that their width is 1.5-2 cm greater than the distance between the subsystem profiles.Otherwise, a gap will remain between the heat insulator and the profile, which risks becoming a "cold bridge".
- Insulation, which will be preceded by diagnostics, will be much more effective and efficient. To do this, use a thermal imager to identify the main areas of "leakage" of heat. This recommendation becomes relevant especially when insulating the internal parts of a building.
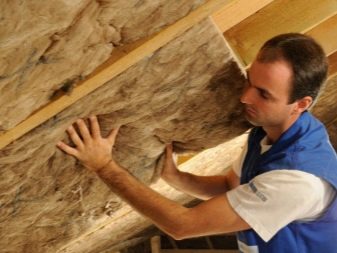
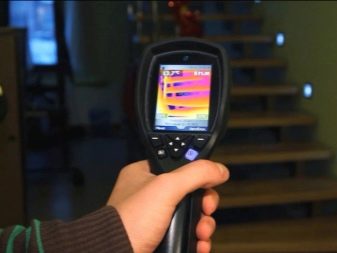
- Having identified the main points of heat loss (these are usually the corners of buildings, the floor or ceiling on the first and last floors, end walls), sometimes it is enough to insulate only them in order to achieve the optimal temperature in the room.
- Regardless of the method of insulation and the material used, the surface should be carefully prepared - it should be flat and clean. All existing joints and cracks should be repaired with cement mortar, unevenness should be repaired, and communication elements removed.
- The final stage of the preparatory work will be the application of a primer in 2-3 layers. It will provide an antiseptic effect and also improve the adhesion of surfaces.
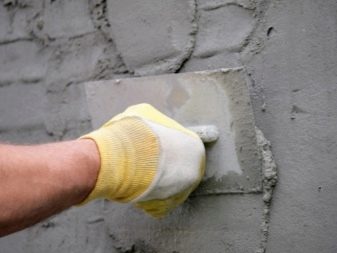
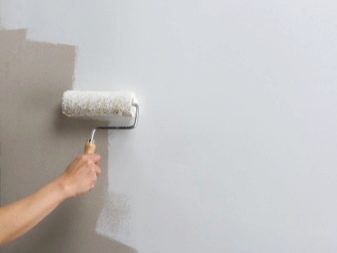
- When using battens made of metal profiles, make sure that they have an anti-corrosion coating. Wooden logs for the frame are also subject to treatment with fire retardants and water repellents.
- Mineral wool and felt heaters are stacked in several layers. The coincidence of joints between layers of different layers is inadmissible.
- Most of the glued heaters (expanded polystyrene, mineral wool) need additional fixing with dowels. The latter are fixed in the center of the insulating sheet, as well as at 2-3 points along the edges.

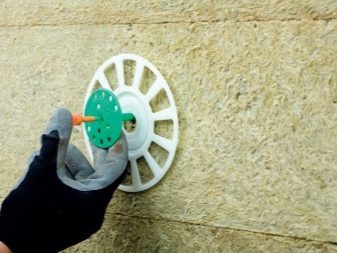
- Despite the similarity of liquid ceramics to paint, it should not be applied with a spray gun or similar devices. Thus, you can damage the ceramic shell, which means that the composition can be deprived of its heat-insulating properties. It is more correct to apply the mixture with a brush or roller.
- If it is necessary to give the treated surface a certain shade, the ceramic insulation can be diluted with acrylic paint. It is necessary to apply the composition in 4-5 layers, waiting for each of the coatings to dry.
- Fixation of the cork cover can be carried out only on perfectly flat surfaces, otherwise a "cold bridge" will form in the space between the cover and the wall, and condensation will begin to accumulate. If it is impossible to level the walls by plastering, a solid plasterboard frame is mounted on which the "cork" is glued. To fix it, you need special glue.
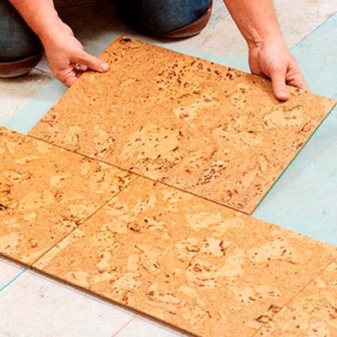
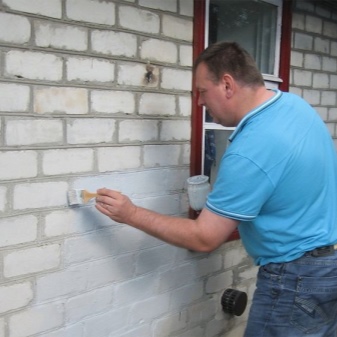
When using foam, it is important to thoroughly clean the wall surface from traces of old paint and solvents. It is important to exclude contact of the insulation with gasoline and acetone, since they dissolve polystyrene foam.
Each part of the building needs "its own" insulation.
- For sloped roofs high density basalt slabs are recommended. Polystyrene foam boards can also be used, but in this case it is important to provide high-quality ventilation. If installation speed is important, spray polyurethane foam, a cheaper option is ecowool. The layer thickness is usually 100 mm.
- For an unheated attic you can use expanded clay or other bulk materials. A more affordable option is dry sawdust mixed with slaked lime in a ratio of 8: 2. Perlite granules, ecowool or slab insulation are also suitable. When using bulk materials, the thickness of the layer should be at least 200 mm, for plate heaters, 100 mm is enough.
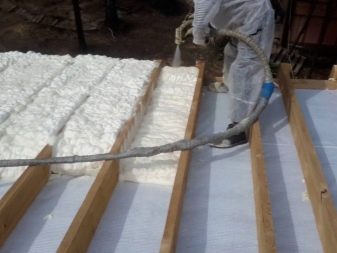
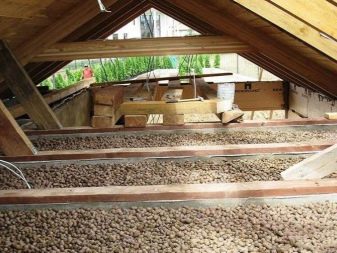
- Wall insulation more often it is made by means of foam, mineral wool, polyurethane foam spraying or ecowool. They should be chosen based on the characteristics of the structure and their own financial capabilities. The most affordable will be foam, more expensive options are mineral wool and polyurethane foam.
- Floor insulation - the question is ambiguous. In a house with a low subfloor, it is more logical to perform thermal insulation along the ground using bulk materials.For concrete screed, expanded polystyrene is suitable, if the height of the ceilings allows - you can fill in expanded clay (for insulation with expanded polystyrene, 50 mm of layer thickness is enough, while when using expanded clay - at least 200 mm). Any material is suitable as insulation between the lags. The technology is similar to the thermal insulation of the attic.
- For foundation and plinth polyurethane foam and polystyrene foam are applicable. An important nuance - both materials are destroyed by sunlight, which must be taken into account when insulating the basement.
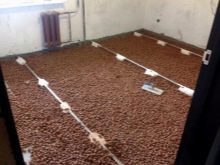
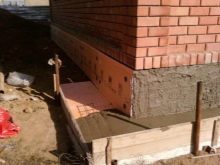
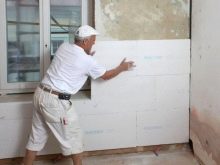
For even more about the most popular insulation materials for building a house, see the next video.
The comment was sent successfully.