Varieties of bulk insulation for walls and ceilings
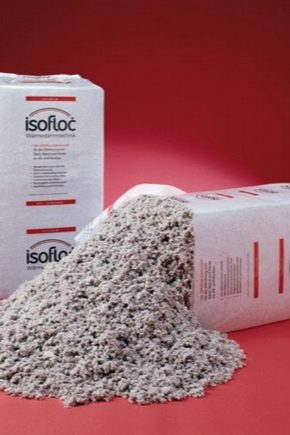
Nowadays, during the construction of buildings, internal and external energy-saving cladding is very often performed using bulk materials. A huge selection of such an option for insulation is offered on the world market. In this article, it will be sorted out what types of bulk insulation there are for walls and ceilings, which types of insulation fillings are best for walls, and which types for floors and ceilings.
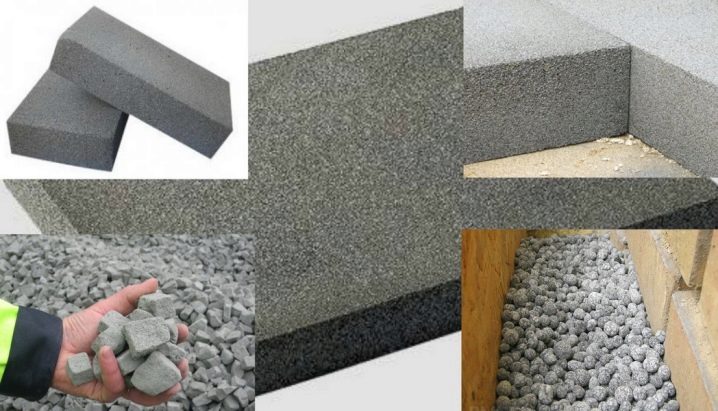
Types of loose insulation
Manufacturers of free-flowing granular heat insulators have a fairly large selection of materials. Bulk insulation is made of paper, stone, resin, polymers and even clay. Let's see what the advantages and disadvantages of certain types are, and also describe the main technical characteristics.
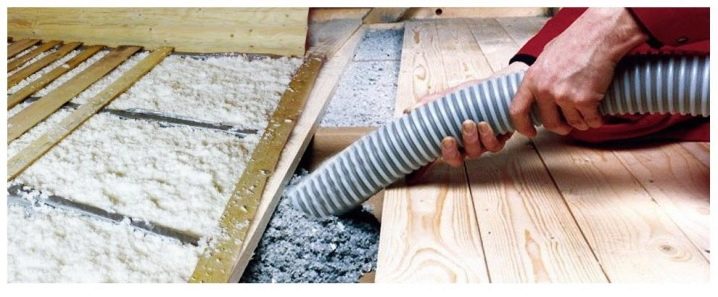
In order for the replacement of insulation in the house to be carried out correctly, you need to have some experience. The recommendations of specialists will also help in this. It is necessary to mix everything in the right proportions, choose a hygroscopic material, and foam powder can also be used.
Expanded clay
It is likely that this is the oldest and well-known type of raw material. In modern construction, expanded clay can be safely called the "classic" of bulk heat insulators. This species has a good advantage - light weight and porous structure. It is produced by firing light-alloy clay and is an environmentally friendly raw material. Expanded clay does not burn and practically does not absorb moisture, does not enter into any chemical reactions, mold does not start in it, mice do not live.
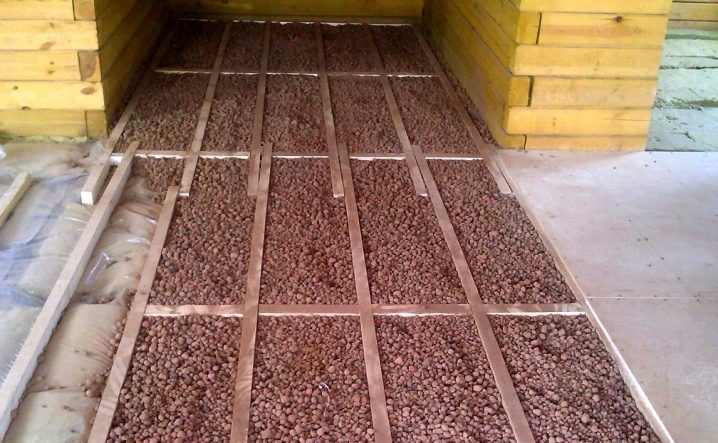
The main disadvantage is that, with possible absorption of moisture, expanded clay gives it back poorly - it is very difficult to dry a wet layer of insulation.
There are three types of these raw materials:
- expanded clay sand (screening);
- expanded expanded clay crushed stone;
- expanded clay gravel.
It should be noted that this bulk heat insulator is much cheaper than its competitors. It can be mixed with sawdust, while the insulation layer should be slightly larger, since wood has a slightly lower heat transfer resistance.
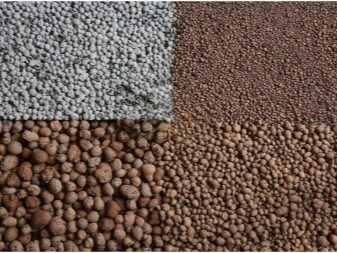
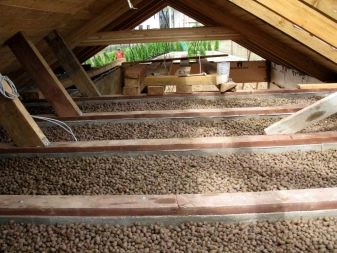
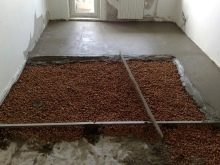
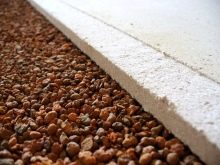
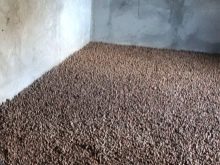
Granular polystyrene foam
We often hear this loose insulation under a different name - polystyrene. If you look closely at the expanded polystyrene sheet, you can see that it consists of many balls. If they are loosened well, then their density decreases, and their volume increases.
This type of heat insulator is mainly used when filling voids in ready-made structures. The crumb is simply blown out using a special device, while it is very important to bring the process to maximum compaction. The downside of this raw material is that it can shrink over time.
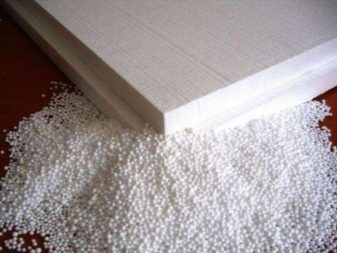
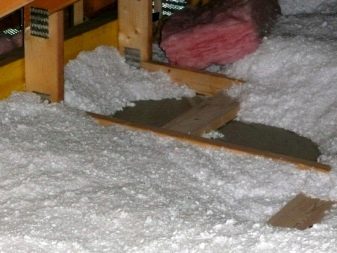
It can be used for floor, ceiling and sloping roof insulation. But there are still disputes about the use of expanded polystyrene in this area:
- on the one hand, it is a light material that is used to insulate walls and roofs, or is used as an additive in concrete (polystyrene concrete);
- on the other hand, they warn about its toxicity and flammability.
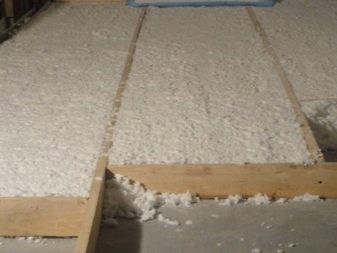
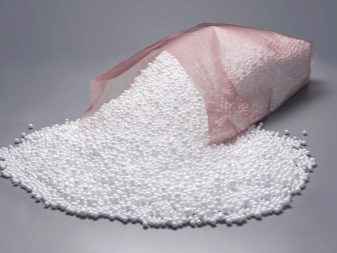
This material in the form of insulation began to be used relatively recently, and its properties have not yet been fully studied. Expanded polystyrene does not absorb moisture, but it is afraid of very high air temperatures.
Vermiculite
Many do not even know what vermiculite is, despite its natural origin. This insulating material is based on mica, which explains its layered structure. During the production of vermiculite, the addition of chemical additives and impurities is avoided, which allows its frequent use when insulating loggias, balconies, as well as living quarters.
When this heat insulator is covered with a layer of 5 cm, heat loss is reduced by 75%, and with a thickness of 10 cm, the heat loss is guaranteed to drop by 92%. The service life is unlimited because there are no perishable impurities in it. The insulation is non-flammable and non-toxic.
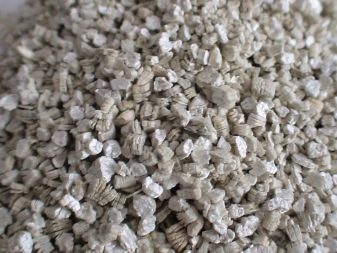
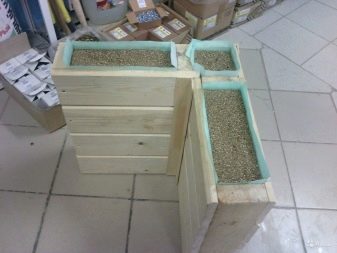
Even with a strong wetting of a separate area, this insulation will evenly distribute moisture over the entire area, and then completely bring it out. Thanks to this "smart" property, all the consequences of the heat insulator getting wet are minimized. Mold and pathogens will not develop in it, and the load on the foundation from structures with this type of insulation will be minimal.
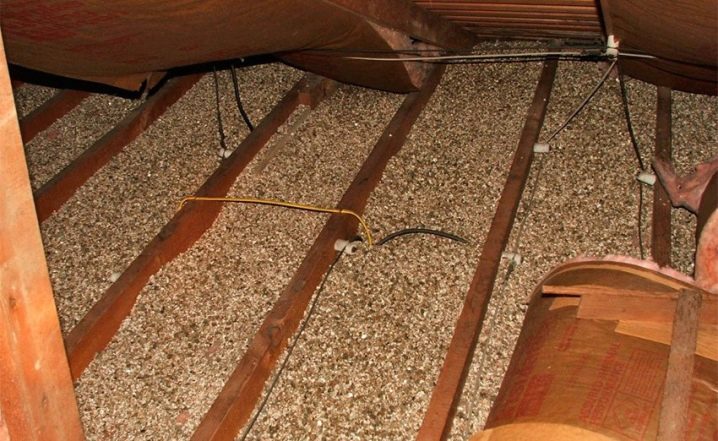
And it can also be mixed with sawdust in a 50/50 ratio.
Sawdust
Sawdust is the name given to particles of recycled wood obtained by sawing; outwardly, they look like fine dust. These loose insulation have traditionally been used for more than one century. And yet, due to their tendency to absorb moisture, sawdust rot over time. Many are mixed with other materials such as clay or vermiculite. It is important to know that only small sawdust can be used as a heater, which is obtained by processing wood on modern machines with high speeds.
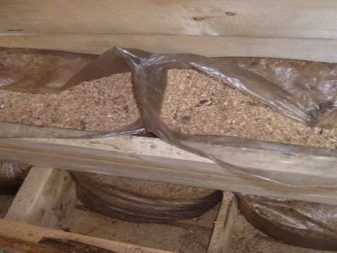
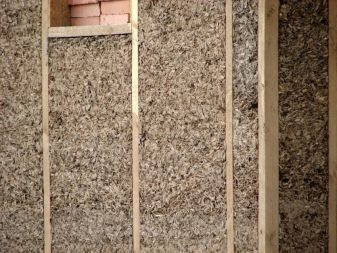
Cellulose insulation - ecowool
This loose insulation is a mixture of shredded newsprint (81%), antiseptics (12%) and fire retardants (7%). For the first time, this type of heat insulator began to be used on the world construction market about a hundred years ago, but in Russia it became known about ten years ago. The main antiseptic component is boric acid, and borax is used as a fire retardant (fire retardant element). Thanks to these substances, ecowool fully justifies its name. The material is non-toxic and environmentally friendly.
The minus of ecowool is the rapid absorption of moisture, which leads the insulation to shrinkage, therefore, it is not recommended to use it in regions with high humidity. Cellulose insulation is great for complex structures, as the fibers of the material fill all the voids in an energy-efficient finish.
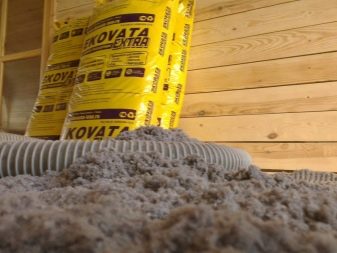
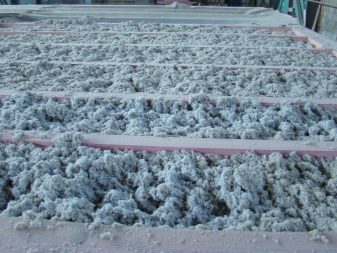
Foam glass in granules
Foam glass is produced from broken glass, which is crushed into tiny particles, remelted, and then mixed with coal. As a result, carbon dioxide escapes from this alloy, which forms air bubbles in the structure of the foam glass. The manufacture of this heat insulator is quite expensive, as a result of which it is very rarely used in private construction. But it is often used in industrial facilities or in the construction of high-rise buildings.
This material is found in two fractions - in the form of granules and crushed stone. Its advantages are that it does not absorb water, does not burn, does not pass steam, and has high compressive and bending strength.
Most often, this loose insulation is used for the ceiling due to its light weight. Foam glass can be used for the manufacture of cement mortars, for example, when pouring a screed or foundation, replacing ordinary crushed stone.
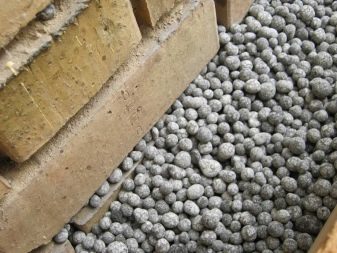
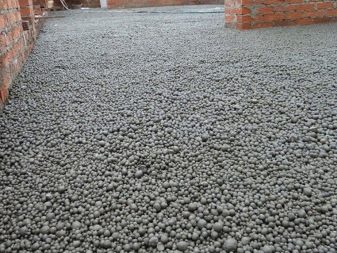
Aerated concrete crumb
It is a mixture of porous crushed stone and sand, made by crushing aerated concrete blocks and waste. Its fractions are always of different sizes (up to three centimeters) and variously often irregular shapes, but this does not affect the quality of insulation in any way - the shape of the filled layer does not change.
It is used not only as a bulk insulation, but also as an additional bedding for sound insulation in walls and ceilings. Perfectly maintains optimal humidity and air exchange. Often this material is used instead of expanded clay in lightweight concrete mixes, for example, when pouring a foundation. In this case, this component additionally insulates the foundation and protects it from swelling.
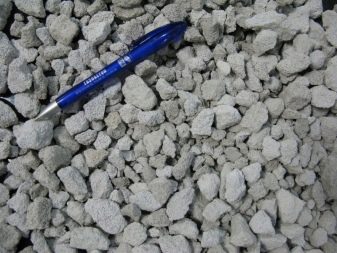
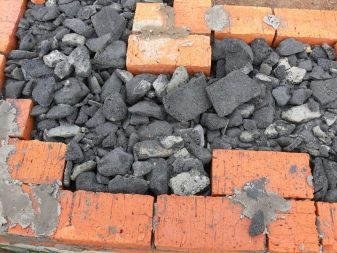
The cost of aerated concrete crumb is low, which does not prevent its use as an inexpensive drainage and insulation of road surfaces. The only drawback is the dusting of small pieces when backfilling.
Perlite
It is produced by melting volcanic ore (sour glass) at a temperature of 1000 degrees. When the ore is heated, the water in its structure evaporates and the material acquires a porous structure. The volume of raw materials sometimes increases up to 90%. The finished granules do not absorb moisture, but they do allow steam to pass through. For better insulation with this raw material, it is treated with bitumen, then the particles stick together and turn into a single insulating layer of any shape.
The main characteristics of this loose insulation are that it does not burn, does not absorb moisture, passes steam, and is chemically inert. During insulation, the disadvantage is the impossibility of using membranes, since they are clogged with perlite dust.
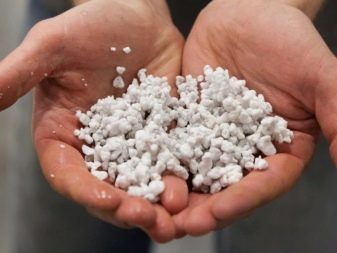
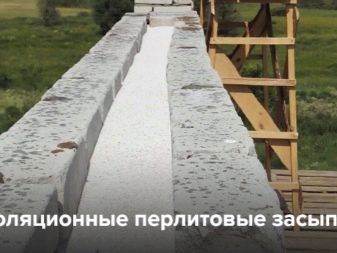
Granular penoizol
In everyday life, it is also called thermovat or foam-insulated crumbs. This heat insulator is based on a hardened urea resin. The manufacturing process consists in crushing the polymerized material into fractions of 10-15 mm in size. These granules retain their elasticity. The advantage of such a heater is that when it is crushed, the volume of the crumb increases several times.
By its appearance, penoizol is similar to snow flakes, at first glance it can be easily confused with expanded polystyrene, but it still differs from it. Its structure is smaller and rather soft, very light in weight - suitable for insulation of both walls and ceilings. It does not burn and does not absorb moisture.
In order to properly fill up this heat insulator, it is necessary to use the help of a special blowing machine, since it will take much longer manually.
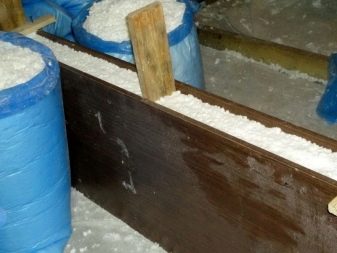
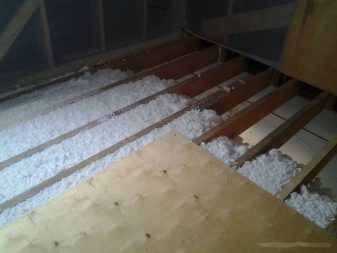
Features of raw materials
Having familiarized yourself with the main types of bulk insulation, we can summarize - that it is always a secondary raw material. It is produced by recycling various wastes ranging from cellulose to minerals. Loose heat insulators in most cases are clean ecological raw materials. Their common disadvantage is the need for a facing partition: insulation is poured between it and the main ceiling, for example, a wall.

Mounting
There are several basic rules for the installation of bulk materials. But each type has its own nuances, so experts recommend following the instructions with a full technological description for filling one or another insulation.
Let's get acquainted with the general recommendations for the correct work on energy-saving cladding with bulk materials.
- Pitched roofs are insulated from the outside after laying the vapor barrier. For a good and even distribution of thermal insulation along the slope, it is imperative to install transverse stops.
- When insulating the floor and basement, after filling the raw materials, it is important to tamp it well. This is done to avoid shrinkage of the insulation and subsequent deformation of the finish.
- When decorating rooms with high humidity, such as baths, saunas, a layer of backfill insulation will need additional, high-quality hydro and vapor barrier.
- Backfill heat insulators are laid in such a way as to avoid spilling them through cracks and cracks in the finish.
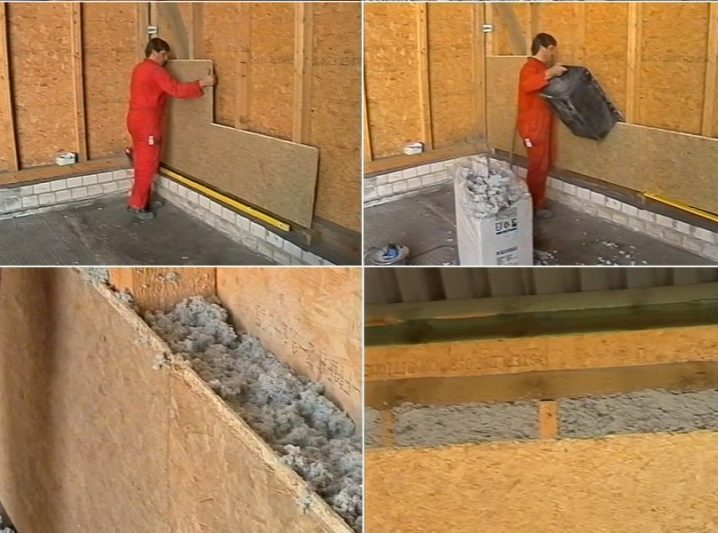
Loose insulation can be used to fill any space in building structures. This type of insulation does not lead to a violation of the main finish and its structure. Therefore, if it is impossible to insulate with traditional plates or rolls, bulk materials will come in handy.
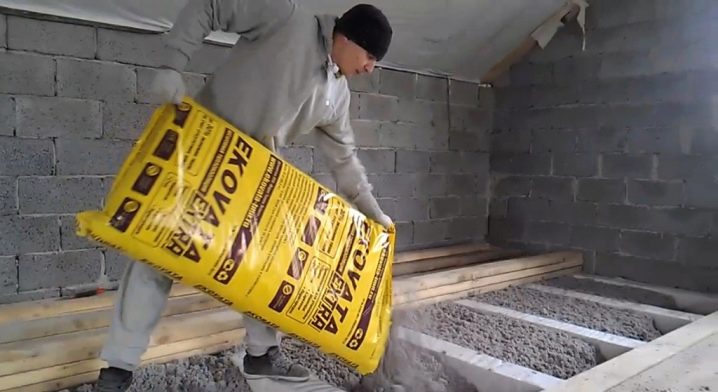
Thanks to the huge range of backfill thermal insulation materials, the consumer is given the opportunity to make an independent decision in favor of choosing one or another raw material.
For an overview of perlite bulk insulation, see the following video.
The comment was sent successfully.