Polyurethane foam: what is it and where is it used?
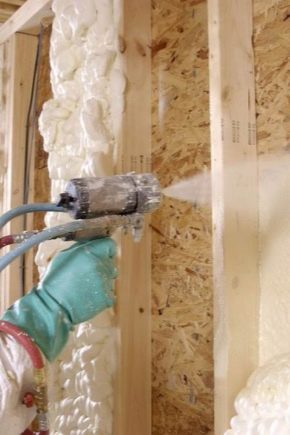
One of the most controversial building materials on the market today is polyurethane foam. In common people it is sometimes called "foam rubber". PU foam is widely used as a heater. However, polyurethane foam causes a lot of controversial reviews: some consider it universal, almost without flaws, others ruthlessly criticize it.
In order to form your opinion about this material, it is necessary to systematize and summarize all the information that is available about it.
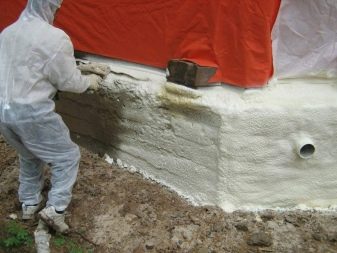
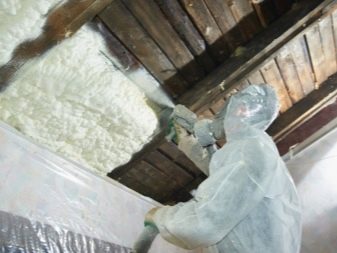
Material features
The material is a type of plastic, to be more precise, it is a porous gas-filled polymer. It is based on polyurethane components polyol and diisocyanate.
The polyol component gives the polymer base, which determines the density, hardness, flammability and other characteristics of the polyurethane foam. The isocyanate component is responsible for foaming.
Various additives are intended to correct different properties. For example, fire retardants accelerate polymerization, reduce the degree of flammability of the material.
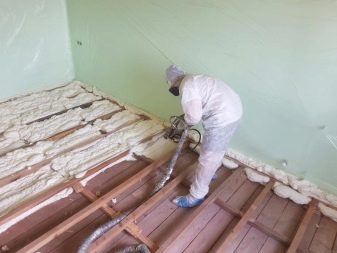
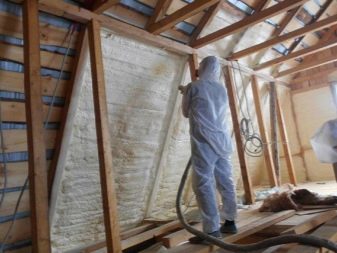
The constituents individually are toxic substances, therefore opponents of polyurethane foam first of all pay attention to this fact. However, when mixed, toxic ingredients form an absolutely harmless mixture that is neutral and does not enter into any chemical reactions with any elements.
The process of obtaining polyurethane foam is associated with the simultaneous formation of gases. Since carbon dioxide is predominantly emitted, which is characterized by low thermal conductivity, PU foam is endowed with excellent thermal insulation qualities. That is why the material is an excellent insulation.

The rate of the chemical reaction and the mixing ratio of the components determine the following characteristics of the obtained polyurethane foam:
- Flexible the springy material has elasticity, but is characterized by low tear resistance. Well-known foam rubber from this category.
- Dense and the durable version is hard but brittle when bent.
- Foamed PPU has a wide range of advantages.
As a rule, polyurethane foam is obtained from petroleum products, but there is a possibility of its production from components of plant origin. For these purposes, castor, soybean, rapeseed and sunflower oils are great. Since the production of polyols from plant raw materials is less profitable, this method of production is impractical and is rarely used.
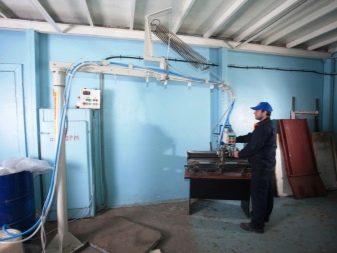
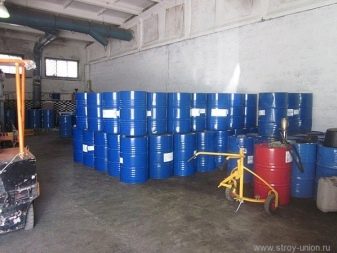
Description
Polyurethane foam is of two types: foamed and solid. This explains the various characteristics inherent in them. The first option is convenient for application and ergonomic, since it does not leave seams after application. The second one is designed to create shock-absorbing surfaces and serve as a heat insulator.
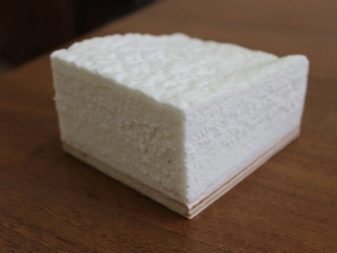
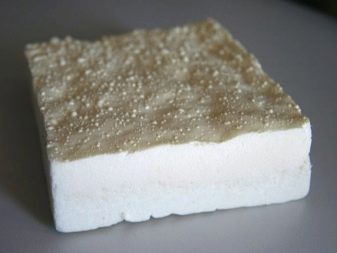
Thermal conductivity
The thermal conductivity properties of polyurethane foam directly depend on its cellular structure. For example, for rigid types of polyurethane foam, the thermal conductivity ranges between 0.019 and 0.035 W / (m · K).
For comparison, we can give an example of an indicator for gas glass 0.84 W / (m · K) or mineral wool 0.045-0.056 W / (m · K).
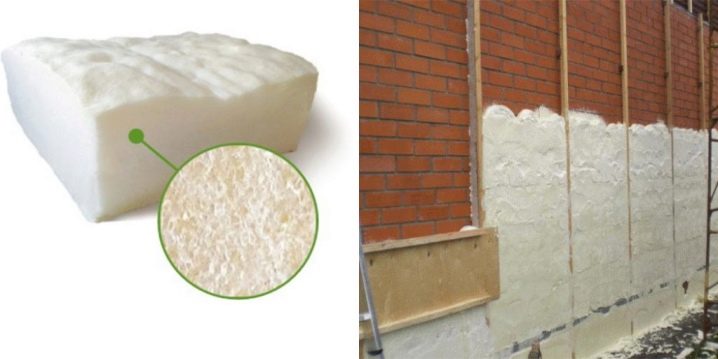
Noise absorption
The ability of materials to absorb noise of varying intensity depends on factors such as porosity, thickness and damping properties.
From the practice of using polyurethane foam, it was concluded that its ability to reduce the noise level depends on the rigidity of the frame and the frequency of sound vibrations. For noise absorption, it is best to use a semi-elastic type of polyurethane foam.
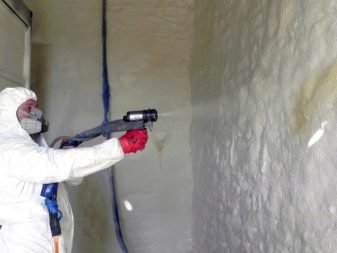
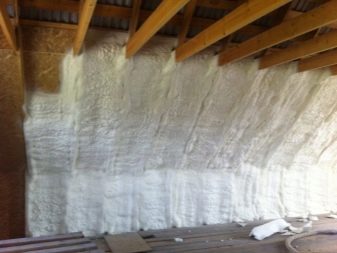
Chemical resistance
Polyurethane foam is considered to be a type of material that is relatively resistant to harsh chemicals. Its degree of resistance is greater than that of expanded polystyrene.
It has been experimentally confirmed that PU foam is not afraid of gasoline, alcohol, dilute acids and various types of plasticizers. It cannot be destroyed by the action of corrosive vapors, provided that their concentration is within acceptable limits. Concentrated acid can damage the surface of polyurethane foam, but, as practice shows, not always.
Due to this property, polyurethane foam is actively used to protect metal surfaces from rust. The effectiveness will depend on the grade of polyurethane foam.
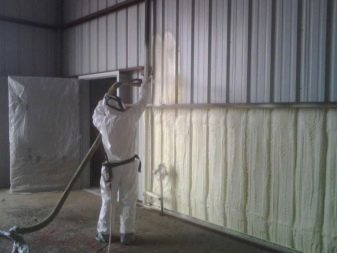
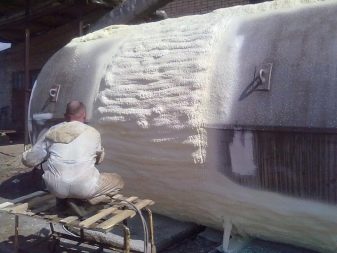
Moisture absorption
The moisture absorption indicator directly depends on the porosity of the material, therefore, it is determined by the density of the insulation. The denser it is, the less water it absorbs.
Polyurethane foam has a low absorbent effect - 1-3% per day of the original volume.
To increase water resistance, manufacturers introduce special substances into the PP composition - water repellents. For example, castor oil can lower this threshold by 4 times.
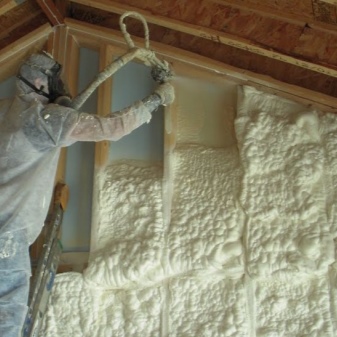
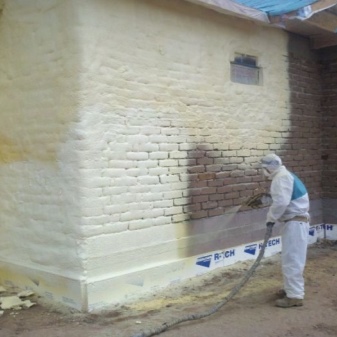
Fire resistance and flammability
One of the advantages of PPU is its fire resistance. The material belongs to the class of self-extinguishing, hardly combustible and hardly inflammable.
If it is necessary to increase the degree of resistance, manufacturers introduce special additives in the form of phosphorus or halogen compounds.
It is extremely convenient and economically justified to use a coating of two layers of polyurethane foam in industrial premises with a high level of fire safety. A fire-resistant layer is applied over the usual layer. It will be enough to keep the flame out.

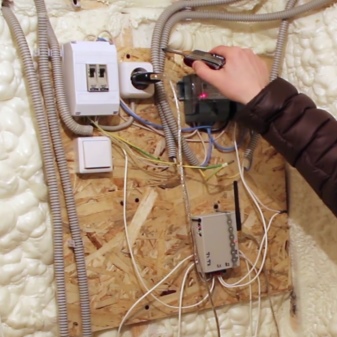
Density
A characteristic such as density is important for insulation, since many different factors and functional properties depend on it.
For polyurethane foam, the density is in the range of 30-80 kg / m³.
The indicator itself depends on several criteria, but two of the most important can be distinguished:
- polyurethane foam production technology;
- a specific functional task that the PPU will perform.
When insulating, different types of PU foam are used: hard, elastic, softer. Knowing the features of each type, you can save money during construction without losing functionality.
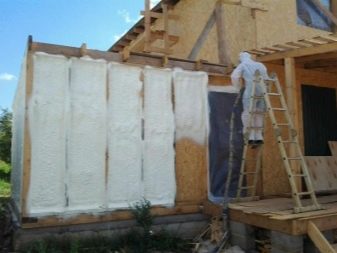
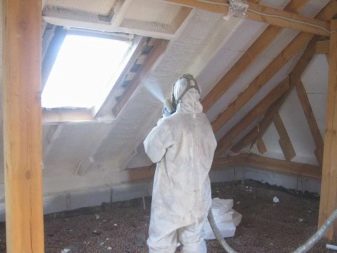
Rigidity
Hardness is not identical to density. For furniture foam rubber is characterized by division into several brands, depending on the rigidity.
- ST - the lowest degree of hardness. It is used for upholstery of furniture armrests or backrests.
- EL - modified material. Polyurethane foam of this brand is used for the production of hard mattresses, sofa seats and other products that imply dynamic loads.
- HR - the brand is characterized by a high degree of elasticity with initially low rigidity. The material is most suitable for the manufacture of orthopedic products and quality furniture.
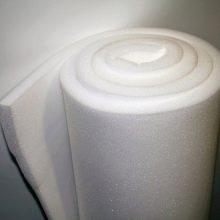
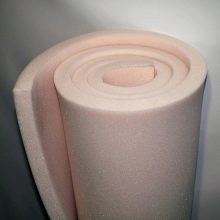
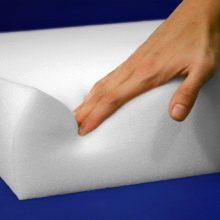
Durability
Laboratory and industrial tests have confirmed that the service life of polyurethane foam is at least 25 years. Moreover, after this time, the material slightly loses its performance, allowing it to be used further.
Eco safety
When applying liquid polyurethane foam, it must be remembered that vapors released during a chemical reaction are contraindicated for humans. Therefore, it is necessary to protect the respiratory system with a respirator. After hardening, polyurethane foam becomes safe.
During a fire, polyurethane foam does not burn, but at high temperatures it can emit carbon monoxide, which is hazardous to health.
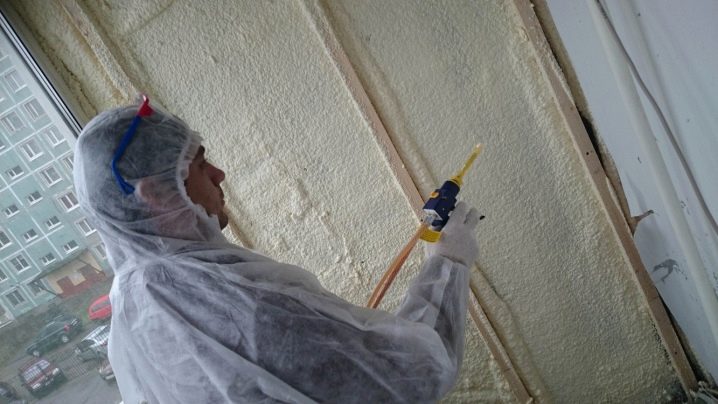
What is the difference from foam rubber?
Foam rubber is a type of flexible polyurethane foam.
The cellular porous structure provides good air, vapor and moisture permeability. The degree of elasticity is controlled by the addition of various types of polyols during production.
When choosing consumer goods, it must be remembered that "foam rubber" is the trade name of PPU, which was registered during the Soviet period by a Scandinavian company of the same name.
Foam rubber is mainly used in light and furniture industries. Furniture upholstery, mattress and pillow fillers, soft toys, mannequins - this is a list of the most common uses of this type of PU foam.
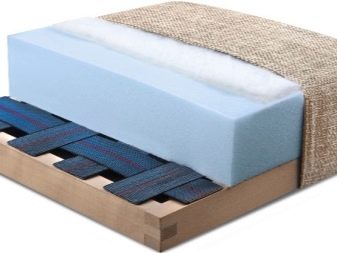
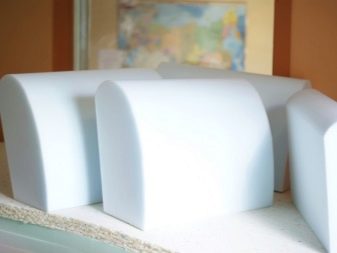
The material is characterized by different thicknesses and, accordingly, different rigidity. Basically, it is produced in the form of sheets or blocks.
Different types of foam rubber in the furniture industry are combined, which improves the quality of the products.
For example, a stiffer sheet is used for a sofa seat than for a backrest.
Orthopedic products, as a rule, should not be soft. They are provided so that the body is positioned correctly and comfortably. For this purpose, a new type of foam rubber with a "memory effect" has been developed. It is able to regain its original shape after deformation. During operation, such material repeats the contours of the body of a person lying on it, which allows you to relax as comfortably as possible.
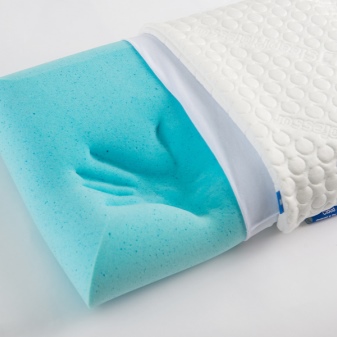
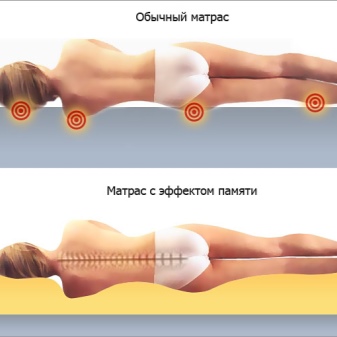
The main mechanical characteristics of foam rubber, on which the operating life of furniture products depends:
- rigidity;
- density;
- strength;
- elasticity;
- cell size;
- support coefficient.
For example, the support ratio and mesh size are decisive in highly resilient types of polyurethane foam.
Furniture foam rubber is exposed to significant loads, so conscientious manufacturers use the material with the highest density. It easily withstands long-term dynamic loads and static weights.
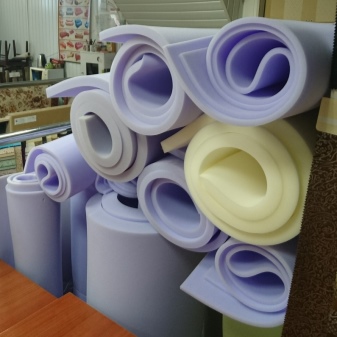
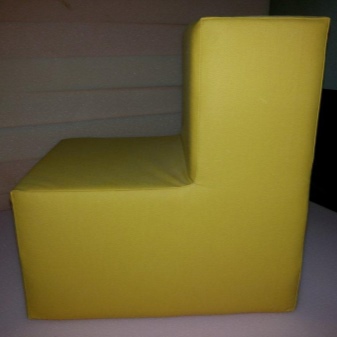
Views
Experts distinguish three types of polyurethane foam:
Hard
This type of material has high density, hardness and lightness. Due to these characteristics, it is used as acoustic or thermal insulation. Rigid PU foam looks like slabs. One of the applications is sandwich panels.
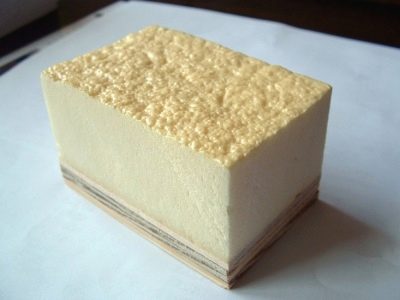
Reticulated
Polyurethane foam with an open-cell structure. It provides breathability and hygroscopicity. Therefore, panels made of reticulated polyurethane foam are most often used for thermal insulation of facades and roofs. The main advantage of the material is its low resistance index and high dust holding capacity. This gives it the ability to filter and regenerate. In this regard, the purification of various liquids and gases is very popular, since reticulated PU foam filters air with a high concentration of coarse dust. One area of application is the climate control system.
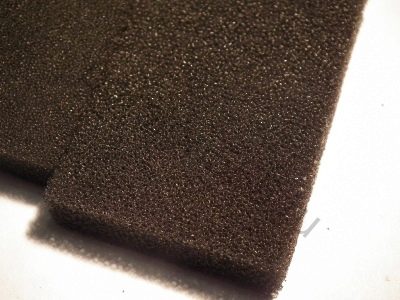
Elastic
The specified version of PU foam is similar to foam rubber. It is designed to create shock-absorbing surfaces, therefore it is used in the furniture industry. Due to its environmental and chemical safety, it is used in the field of medicine.
The latest developments have made it possible to obtain various subspecies of elastic polyurethane foam:
- Artificial latex in its properties it is close to a natural sponge. It is characterized by elasticity, the ability to regain its shape, increased wear resistance, and ventilation. Highly elastic characteristics have been highly appreciated by manufacturers of orthopedic products.
- PU foam with memory effect. The material has a high degree of elasticity, due to which, after deformation, it quickly restores its original shape.
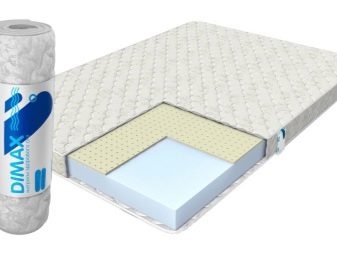
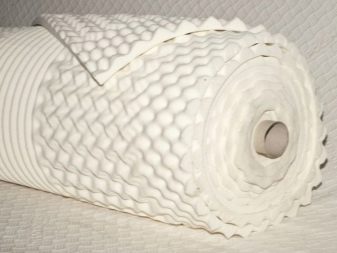
Integral
The species is characterized by solidity and dense consistency. Most often it is used in the manufacture of automobiles.
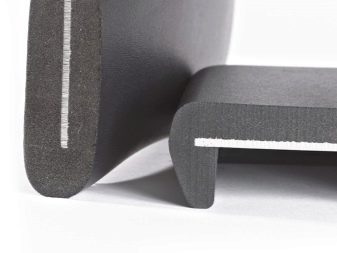
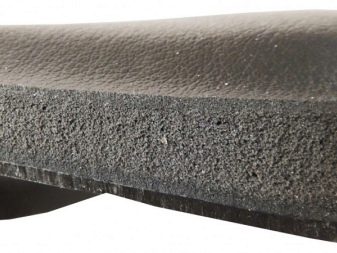
Foamed
PPU components are in a liquid state in cylinders. They mix during operation when applying foam to the surface.
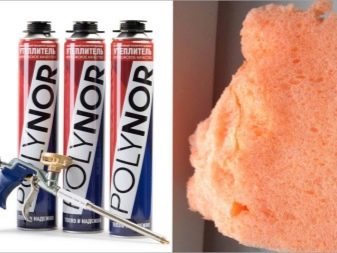
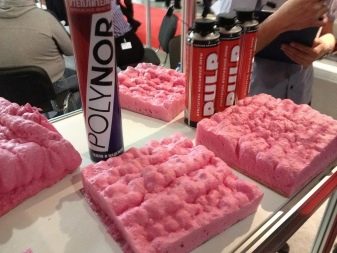
This type of polyurethane foam is divided into two subspecies:
- PPU with a closed cellular structure. When working on a large scale, professionals use two-component formulations. The parts mix during assembly, which causes a chemical reaction with the release of carbon dioxide. It gives the foam a rigid structure, the pores of which are air bubbles isolated from each other.
- PPU with open cells. For work in confined areas, as well as in everyday life, it is recommended to use one-component formulations. Most often they are called "polyurethane foam". In this case, all the components of the composition are already mixed and are under pressure inside the container. For the reaction to proceed, contact with oxygen and water is required, which is ensured when the valve is opened and the mixture exits. Air and water vapor, as well as a moistened surface, make it possible to obtain a porous structure of polyurethane foam, the cells of which will be open.
The second option cannot compete with the first, since it loses in strength. For foaming in polyurethane foams, freon is used, which eventually evaporates and is replaced by air, which reduces the thermal conductivity coefficient. Therefore, for insulation of buildings, PPU with an open cellular structure is not suitable, but it is quite suitable for sound insulation and noise absorption.
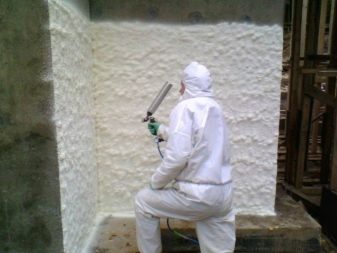
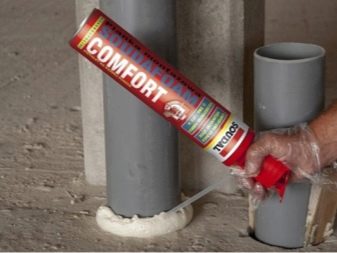
Applications
Polyurethane foam, due to the variety of shapes, types, characteristics, has a wide range of applications.
Construction
One of the most important areas of application is construction.
The low thermal conductivity of the material increases its competitiveness among other insulation materials.
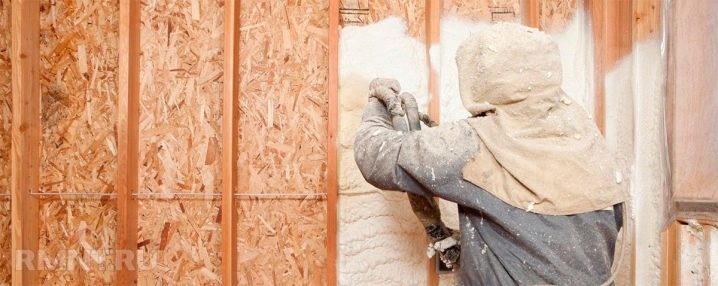
Low vapor permeability and waterproofing properties of rigid polyurethane foam blocks allow them to be used in almost any construction work:
- thermal insulation of the outer walls of the house, balcony, attic, roof;
- acoustic insulation inside and outside buildings and structures (hangars, workshops, warehouses);
- waterproofing and insulation of foundations.
Self-foaming polyurethane foam options, which have a high degree of adhesion to the surface, make it possible to use the material on any surfaces, in any conditions.
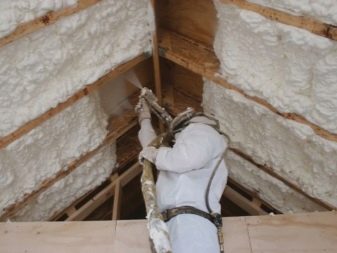
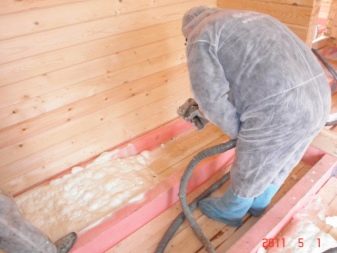
Construction and installation works are carried out faster and with better quality. Now it is possible to eliminate minor wall defects, gaps between frames when installing windows and doors.
Trunk pipelines are also insulated with polyurethane foam. For insulation, as a rule, three methods are used:
- Fill. A polyurethane foam mixture is poured between the main pipe and the polyethylene casing, which allows to optimize production, since the number of operations is reduced, the structural strength increases, and a high degree of temperature resistance is achieved. This insulation method significantly reduces heat loss. Trunk oil and gas pipelines are often insulated in this way.
- Spraying. The method is used for large diameter pipes. As in the first case, the method provides seamless application of insulation. It can be noted as an advantage that spraying can be done on site. The temperature range of the insulating layer is from minus 80 to plus 130 degrees.
- PPU shells. For insulation of outer pipes, polyurethane foam shells are created with a length of about a meter and a thickness of up to 10 cm.
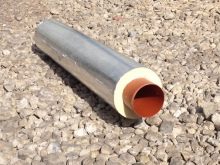
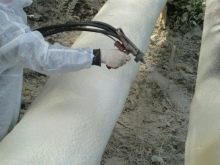
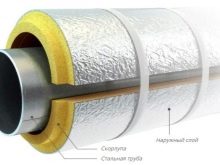
PPU is also present in the composition of modern sandwich panels used for industrial and civil construction. This building material is a multi-layer structure consisting of two cover layers and insulation.
When using polyurethane foam as a heat-insulating layer with a thickness of 3.5 cm, an effect is achieved similar to the use of a panel with mineral wool with a thickness of 12.5 cm.You can also compare such a panel with a brick wall 96 cm thick. The main advantages of sandwich panels are lightness, strength, durability, a high degree of thermal insulation, a low moisture absorption coefficient, a high construction speed, and no construction waste.
Recently, architectural decorative elements are also made from polyurethane foam. These include bas-reliefs and statues, moldings and baguettes, cornices, columns, balustrades, and more.
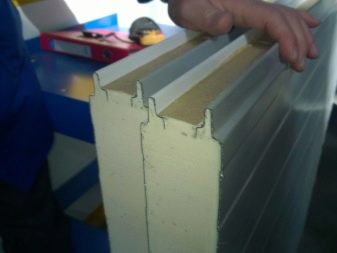
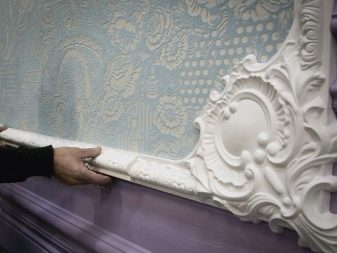
Automotive industry
Integral polyurethane foam is used in the manufacture of car seats as fillers, as well as sound insulation of the interior itself.
All soft panels inside the car are also made using polyurethane foam: armrests, handles, headrests, steering wheel and even bumpers.
The reticulated foam rubber is used to create the climate control system.
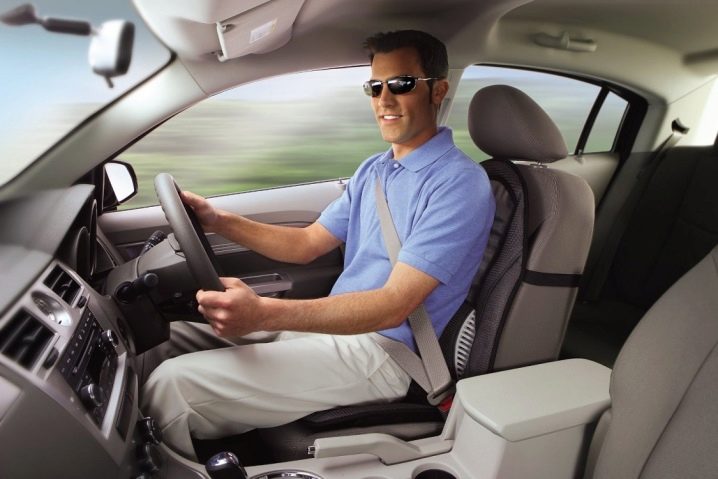
Furniture industry
Furniture manufacturers use polyurethane foam as a filler or cushioning material. Forming pillows, mattresses, various rollers cannot do without his participation. As the density varies, you can achieve different degrees of elasticity and provide any relief.
With the improvement of some properties, you can get a new type of PPU. Thus, for example, a viscoelastic material with a memory effect was obtained. It is used for orthopedic pillows and mattresses that adapt to the body structure of the person sleeping on them, which improves the quality of sleep and rest.
The elastic version of polyurethane foam holds its shape well and can withstand significant weight, so furniture based on it will last long enough. In addition, it does not accumulate dust and is breathable, which is especially important for allergy sufferers. Manufacturers warn that if you jump on furniture, as children often do, the elasticity will decrease much faster.
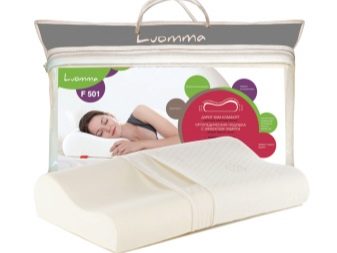
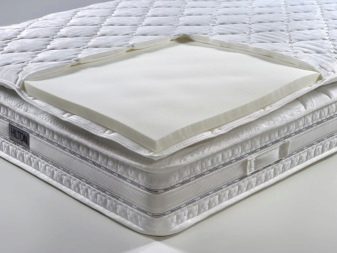
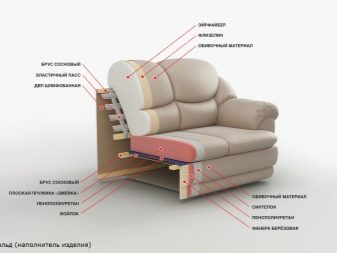
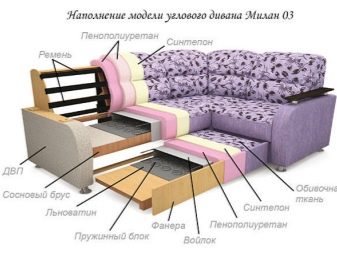
Light industry
The manufacture of footwear and various items of clothing often uses soft plastics in the form of polyurethane foam. For example, instep supports for heels, various reliefs. The polyurethane foam sole lasts a long time and has no complaints.
Foam rubber is the most common filler for soft toys and mannequins.
For everyday life, various sponges for washing dishes, rollers for painting, washcloths, "brushes" are produced from polyurethane foam. In this case, special purpose polyurethane foam is used, since it is necessary that it does not crumble during operation, withstand constant contact with water and household chemicals. Manufacturers for these purposes add special fillers that improve quality characteristics.
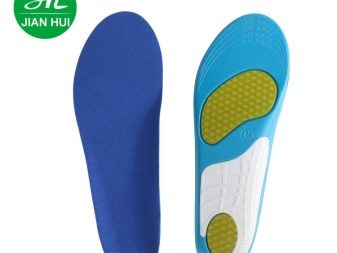
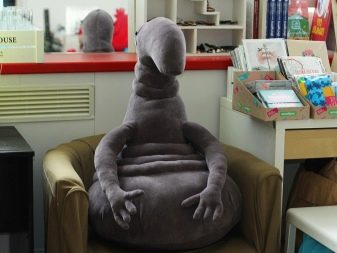

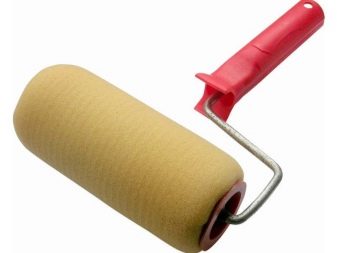
Reticulated polyurethane foam is a material for the production of air filters in any air purification systems: domestic and industrial air conditioners, vacuum cleaners. Filtration of water in an aquarium, petroleum products and various types of oils, fuels and lubricants during production and transportation - this is a considerable list of its applications.
Gentle transportation of fragile goods is not complete without polyurethane foam packaging.
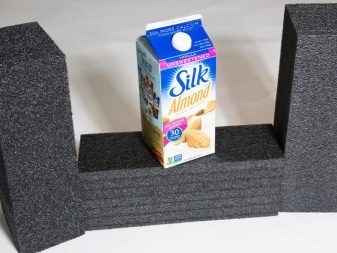
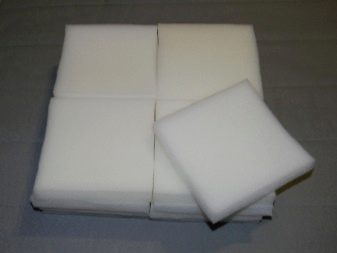
Chemical industry
Insulation of low-temperature pipelines cannot do without PPU.
Polyurethane foam is widely used as a cold insulator in any technique.
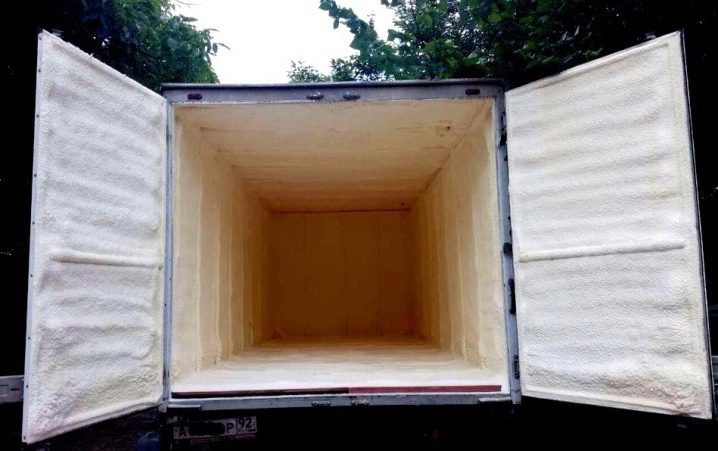
Medicine
Viscoelastic brands of foam rubber are used in the field of medicine for the manufacture of various linings for burns and other skin lesions, which makes it possible to less disturb the injured areas.
Also, the material is widely used for the manufacture of contoured orthopedic pads and holders: rollers, drawers or cylinders.
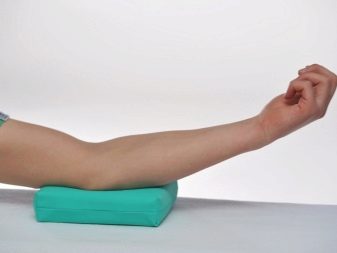
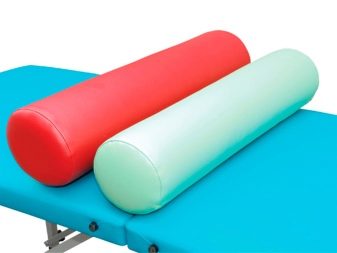
Manufacturers overview
Polyurethane foam insulation has become popular lately. Therefore, new manufacturers of these products appear on the market, as well as contractors providing services for its installation.
Respectable PU foam suppliers produce components under their own brands. The rest, as a rule, are resellers, purchasing components from well-known brands.Some firms use the services of local refineries.
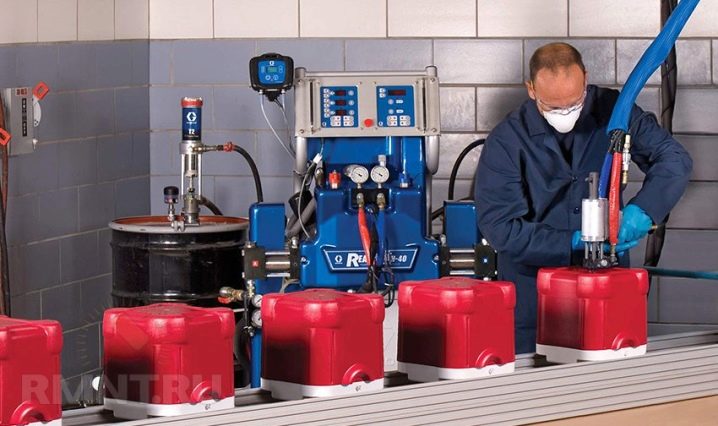
Using consumer reviews, there are several reliable manufacturers of polyurethane foam:
- Basf Is a German chemical concern with branches in 160 countries of the world. The brand produces a wide range of products. More than 7 thousand items, 60% of which are sold in the European market, about 22% of sales are in the United States of America, the rest is distributed between the markets of South America, Asia, Africa and the Pacific. In Russia, the company has several subsidiaries, including OOO Basf Stroitelnye Sistemy, OOO Basf Vostok, Wintershall Russland. One of the well-known joint ventures producing polyurethane foam products is Elastokam. The company manufactures polyurethane systems available to consumers of all levels, for a variety of applications.
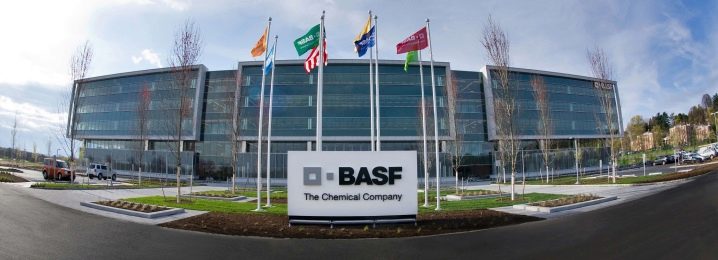
- Synthesia Internacional S. L. U. Is a Spanish chemical company founded in 1964. The main direction since 1966 is the production of polyesters, as well as polyurethane systems for various industrial sectors, for example, thermal and acoustic. Since 1970, polyurethane foam has appeared in the range for the first time for sandwich panels, construction and refrigeration systems. Today the company manufactures products for different market segments. The most famous distributor of products in Russia is Global Term LLC. The specified company provides direct deliveries, carries out a certain stock of products in a warehouse in Moscow, guarantees a flexible payment system and consultations of technical specialists.
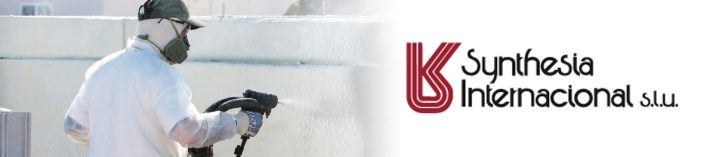
- Sipur (Poland) - one of the largest manufacturers of sprayed polyurethane foam insulation. Heat-insulating products are characterized by low thermal conductivity, which makes it possible to apply insulation in a thinner layer (spray thickness up to 6 cm). The company guarantees the service life of polyurethane foam for about 50 years. Thanks to the closed-cell structure, thermal insulation not only retains heat, but also allows structures to be strengthened and protected from moisture. The density of the insulation is 18-22 kg / m3, the degree of air permeability is about 0.0045 kg / (m2 * hour), the temperature range for operation is from -70 to +100 degrees. Modern innovative material is patented, developed specifically for the CIS market, therefore it has combined reasonable prices and high quality characteristics.
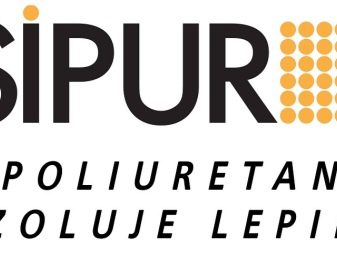
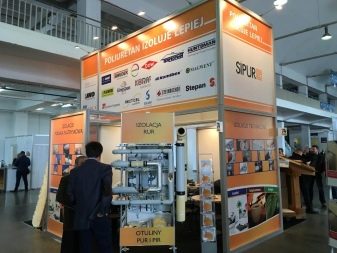
- Icynene (Canada). The brand produces energy-efficient polyurethane foam insulation for private and industrial construction. More than 300 countries have confirmed the quality of the produced material with certificates. The guaranteed period is 25 years. The company has appeared on the polymer insulation market since 1986.
- Wanhua (China). The company started production in 1998 and has achieved worldwide recognition today. The range of the company includes several high-quality types of polyurethane foam, aromatic polyamines, polyisocyanate (MDI). The latter is produced at two plants with a total capacity of up to 500 thousand tons per year.
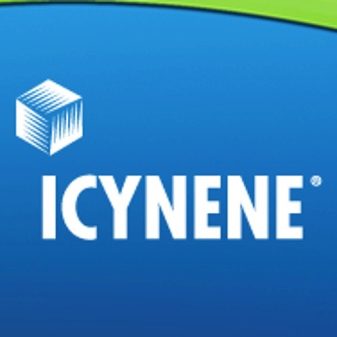
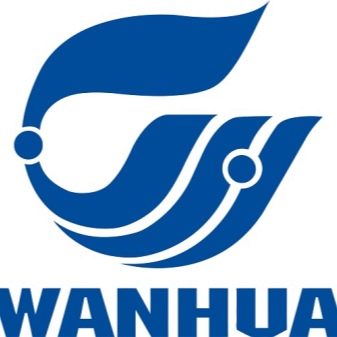
Advantages and disadvantages
The thermal insulation area of construction has been developing at a rapid pace lately. Innovative technologies and the latest equipment have made it possible to reach certain heights in the field of insulating finishing materials. Traditional insulation cannot provide such a long service life without losing its protective properties, while new heaters create comfort, make it possible to save on heating, eliminate drafts, and increase noise and moisture insulation. To use the material correctly, you need to know and take into account all its pros and cons.
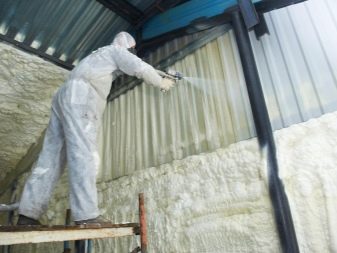
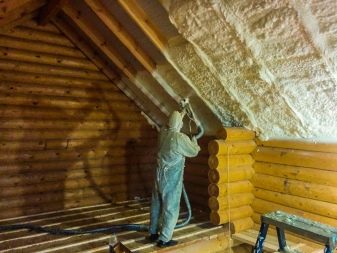
The advantages and disadvantages of different types of polyurethane foam differ significantly.
Foam rubber
The well-known foam rubber, which has been widely used since the sixties of the XX century, is valued for its softness, springiness, the ability to change shape, it can be cut, glued, sewn.The material was used in the furniture industry, in the production of children's toys, as packaging, in everyday life, and so on.
The most significant are the following advantages:
- High coefficient of wear resistance.
- Hypoallergenic. The material is safe for the production of goods for children.
- Not susceptible to the formation of harmful microorganisms.
- Elasticity.
- Variety of models. Depending on the hardness, color, thickness, polyurethane foam can be used in different areas.
- The service life is from 5 to 15 years, depending on the density and the functions performed.
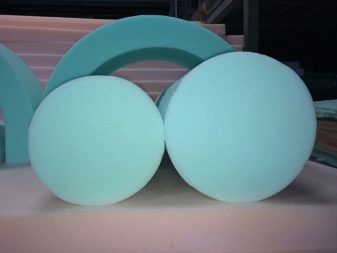
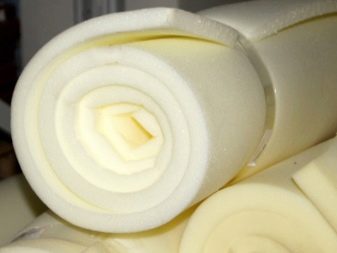
However, with all the advantages of foam rubber, significant disadvantages are also noted:
- It contains the toxic compound toluene diisocyanate.
- Foam rubber is hygroscopic. Absorbs odors and retains them for a long time.
- Has a limited temperature range.
- Low service life in comparison with rigid types of PU foam.
- Fire hazard. The material is highly flammable, therefore, according to GOST, it belongs to the group of flammable, highly flammable and toxic substances with a high degree of smoke generation.
Manufacturers tried to introduce fire retardants into the foam rubber, which would increase its fire resistance.
However, this led to a deterioration in the physical and mechanical properties, and also caused a significant increase in cost.

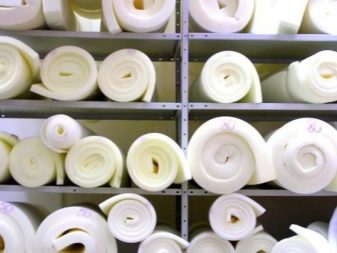
Self-foaming compositions
Let's list the most famous advantages of polyurethane foam that make it popular:
- The cellular structure of PU foam provides an effective degree of thermal conductivity.
- The possibility of spraying allows you to avoid seams and joints, increases the effectiveness of the insulation.
- The variety of polyurethane foam types makes it easy to work with surfaces of all shapes.
- The low degree of hygroscopicity makes it possible not only to provide thermal insulation, but also to waterproof structures.
- High vapor permeability.
- After spraying, polyurethane foam has a neutral odor.
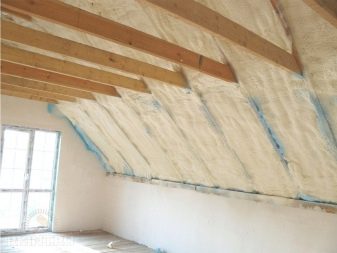
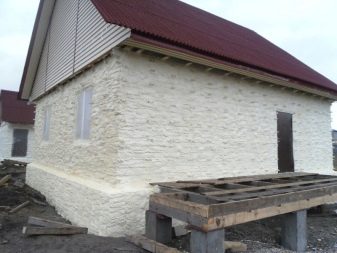
- High coefficient of adhesion. This property can sometimes be considered as a disadvantage, since the PPU sprayed onto the surface can only be removed mechanically. There are no special solvents for these purposes.
- Low weight. The material does not weigh down the surface.
- PPU allows you to strengthen the walls when applied.
- Large temperature range.
- Durability. The warranty period is usually around 20-25 years. However, manufacturers claim that even after twenty years, the quality characteristics deteriorate slightly.
- Low time interval for surface treatment with polyurethane foam.
- Fireproof. The material does not burn, it is self-extinguishing.
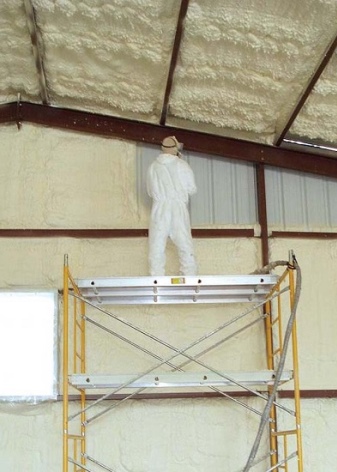
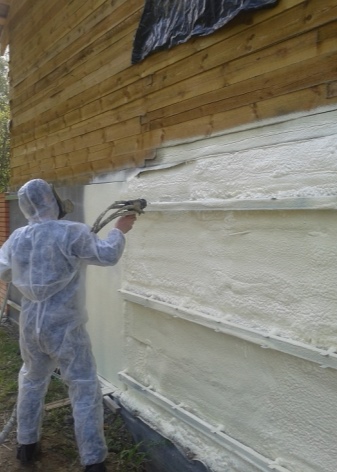
Among the disadvantages are the following factors:
- High price. The difference, for example, with mineral wool, is 2-3 times. However, it should be noted that the service life is significantly longer.
- If polyurethane foam is applied by spraying, then the quality depends on the skill of the specialist.
- High-tech equipment for spraying polyurethane foam is expensive, so not everyone can afford it, but only specialized firms.
- When ignited, PPU smolders and emits corrosive smoke. It is he who brings harm to health.
- The material is afraid of ultraviolet radiation, therefore, under the influence of sunlight, it darkens and takes on an unsightly appearance. To protect PPU, it is better to use a finishing finish. In addition, the sun causes fusion of the upper layer, but if there is sufficient thickness, it will protect the lower ones from destruction.
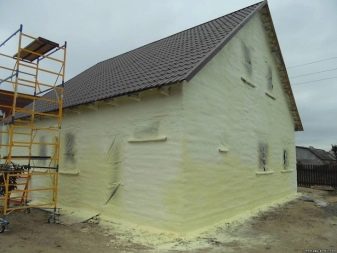
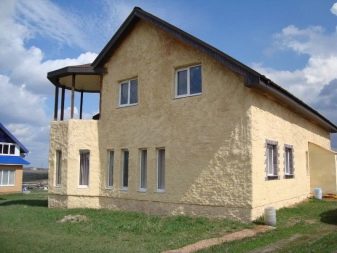
How to insulate yourself?
The process of wall insulation can be divided into two types: internal and external.
Internal
From the name it follows that the work is carried out indoors. Most often, corners, loggias or balconies are insulated.
Polyurethane foam allows you to handle even problem areas such as the bathroom and kitchen.
The material has good moisture resistant properties.To exclude hygroscopicity, a vapor barrier with a foil layer must be laid on top of the PUF, which must be located inside the room.
When insulating loggias or attics, polyurethane foam will help to avoid heat losses and save heating costs.
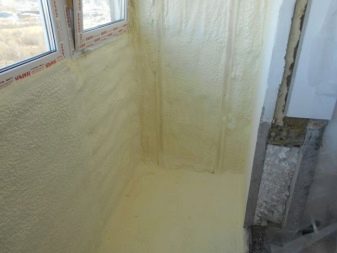
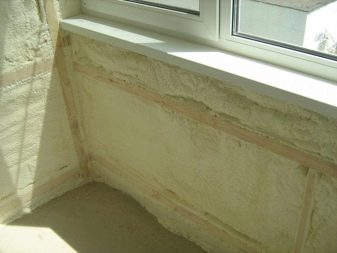
Thermal insulation technology for balconies and loggias
In order to insulate a small balcony or loggia, it does not take much time to spend. Usually for these purposes a standard set of tools and materials is required:
- aluminum profile for the lathing (from any construction supermarket);
- self-tapping screws with dowels;
- drill;
- PPU components (it is better to purchase a ready-made set);
- distributor pistol - if you buy a ready-made set, then the equipment is already in it;
- personal protective equipment - gloves, glasses, respirator;
- building level.
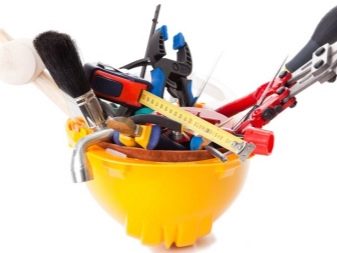
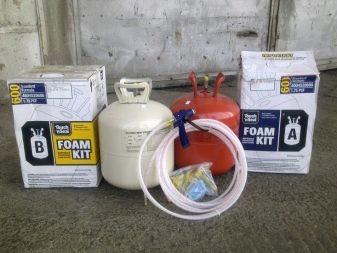
At the preparatory stage, the walls and ceiling are cleaned from the old coating, peeling plaster and other debris. If there are deep gaps in the joints between the walls or in the corners, it is better to fill them with pieces of styrofoam and putty. Minor defects do not need to be eliminated, since the foam will cope with this task.
The second stage is to install the battens. To do this, the profiles are fixed along the walls at regular intervals, fastening them with perpendicular bridges. Experts advise to crate all openings, window and door, along the entire perimeter. Next, you should cover all double-glazed windows, door leaves and communications with polyethylene, so as not to spoil during the application of insulation.
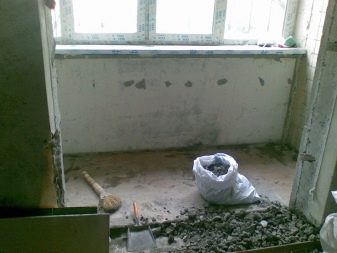
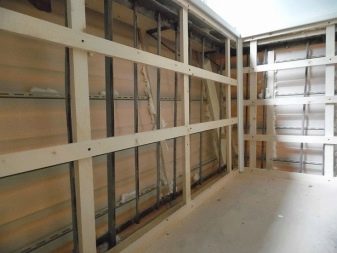
The third stage is spraying. According to the instructions for the insulation components, the pistol, supply hoses, and nozzles are collected. The cans are shaken well before use. First of all, it is necessary to foam the cracks in the joints between the ceiling and walls, corners and process openings. For these purposes, a narrower nozzle serves. Further, it is better to use a wider sprayer to evenly apply the polyurethane foam to the ceiling and wall surfaces. In places with minor defects or irregularities, the insulation is applied in a thicker layer in order to level it. After finishing the work, the excess polyurethane foam must be removed from the crate.
The final stage is finishing. Drywall is attached to the crate, if in the future it is planned to paint the walls, cover them with plaster or stick wallpaper. Finishing using plastic or wood panels is often practiced.
It must be remembered that in case of plastering, the reinforcing fiberglass mesh must be reinforced before applying the finishing coat.
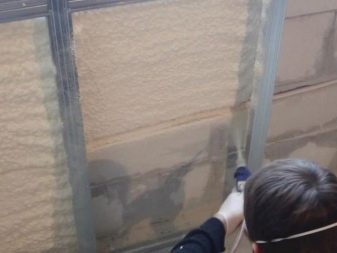
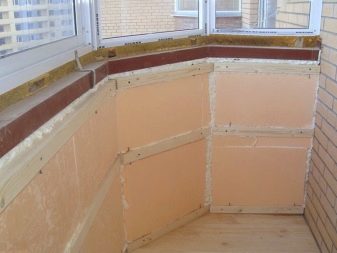
Basement
Damp basements are especially in need of insulation and waterproofing. Stages of work:
- The procedure for isolating the surface from excess moisture. To begin with, the floor is covered with roofing material. It should be remembered that the sheets are overlapped, 20 centimeters each is placed on the walls. To ensure high-quality tightness, roofing material is coated with mastic around the perimeter, it is also better to do with the joints. In the case of low humidity in the basement, the walls are also treated with mastic to a height of 10-15 cm from the floor. Deformation of the protective coating will help to avoid the screed.
- The application of polyurethane foam insulation begins from the corner to the exit. Better to make 3-4 layers, clearly tracking the level over the entire floor area.
- A concrete screed is evenly applied over the polyurethane foam. The rule is to level out the thickness. The minimum permissible thickness is 5 cm.
- Finishing finish. After the screed has dried, for at least two to three days, the floor is covered with tiles, panels, linoleum or any other material.
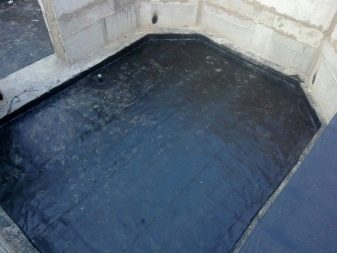
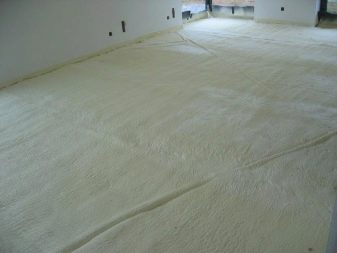
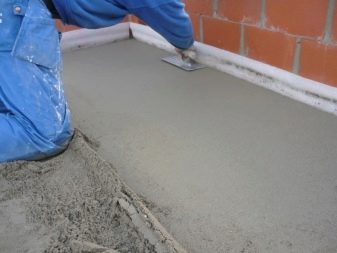
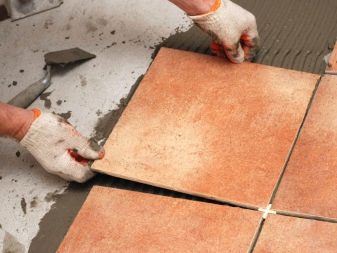
Attics and mansard rooms
Working with polyurethane foam insulation in the attic depends on the method of subsequent finishing.
- If the attic space after insulation is planned to be sheathed with eurolining or drywall, then the foam should be applied between the rafters. In this case, it is not necessary to cover the floor beams with waterproofing, antiseptic or primer.
- If the finishing involves decorative plaster, then PPU should be applied to all surfaces, including beams.
You need to start work with the joints and seams between the walls and the roof. It is important to monitor the uniformity of the insulation layer. It is convenient that you can start finishing in a short amount of time, since the insulation hardens almost instantly.
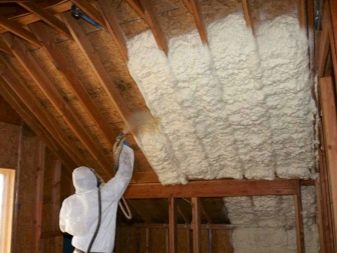
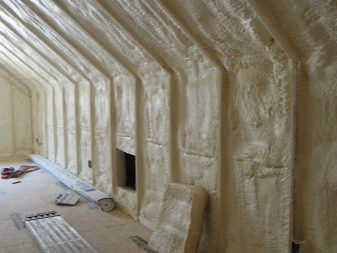
Outdoor
External insulation of the facade of the building allows not only to retain heat, but also to avoid dampness, the appearance of mold, and other harmful microorganisms.
For outdoor use, self-foaming polyurethane foam modifications are most often used. They are applied evenly, without seams, filling all defects and irregularities in the walls. In addition, the material has excellent adhesion and is suitable for insulating both a wooden house and concrete and brick structures. PPU hardens quickly.
Due to the fear of sunlight, it must be covered with a finishing decorative and protective layer.
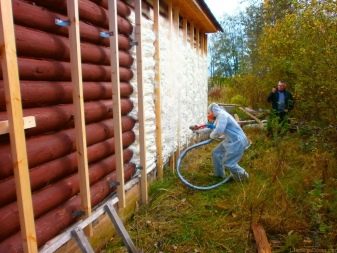
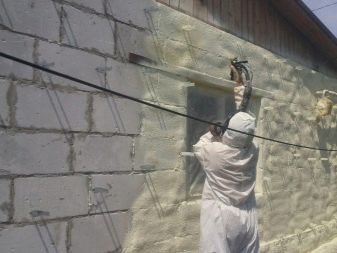
There are two ways to insulate the roof or walls with polyurethane foam, depending on the type of insulation used:
- With the use of polyurethane foam elastic structure. The plastic material has a porous structure and low density. In this regard, such insulation makes it possible to insulate the roof with simultaneous sound insulation.
- Using rigid PU foam. The material is most common in construction, because it has a high density.
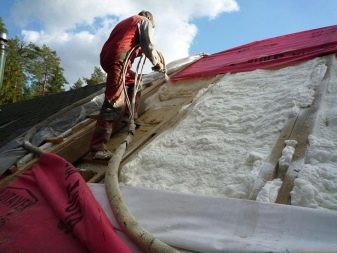
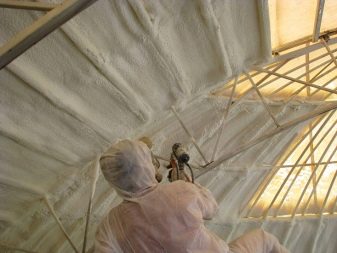
This leads to the following performance characteristics:
- moisture resistance - protection of the roof from water;
- resistance to deformation, due to which the insulation can withstand significant loads;
- the low weight of the PU foam reduces the overall load on the foundation;
- ease of installation - thermal insulation does not require analysis of structures, additional preparation.
When building private houses, the first method is more often used, when insulating large structures - the second.
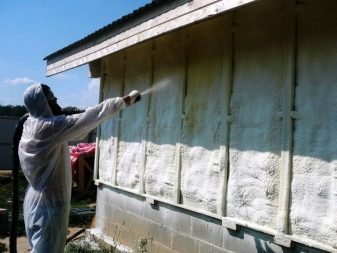
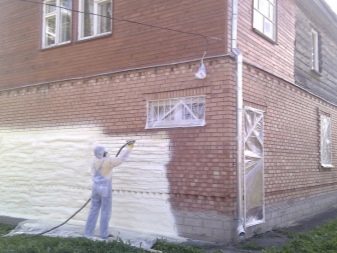
The main stages of applying polyurethane when insulating a low-rise building with your own hands:
- Cleaning the base and elimination of major defects on it. At this stage, it is necessary to clean the walls, necessary sections of the floor or ceiling from dust, old coating and various dirt. The procedure will improve the adhesion of PU foam to the surface. At the same time, experts pay attention that it is not necessary to level the bases.
- Application of polyurethane foam layer using special equipment. Spraying is carried out on cleaned surfaces. The thickness of the polyurethane foam layer will depend on several factors. Less material will be spent on leveled surfaces. The type of insulated floors themselves will also affect. A preliminary calculation for heat loss will help to avoid unnecessary costs by providing the necessary protection.
- Reinforcement with a special tie. As a rule, a fiberglass mesh with small holes is used as reinforcement. Professionals advise not to lay the reinforcement layer less than 6 cm.
- Finishing. To work on the protection of polyurethane foam insulation, you can use any materials: brick, plaster, artificial or natural stone, paint for facades, siding and others.
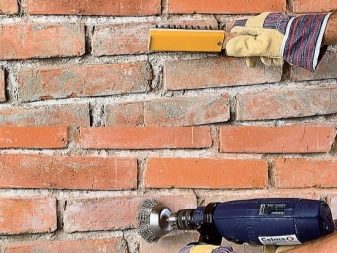
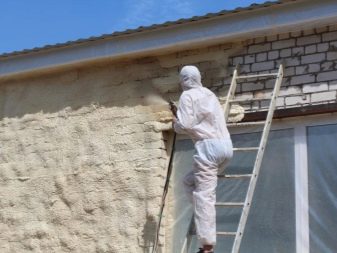
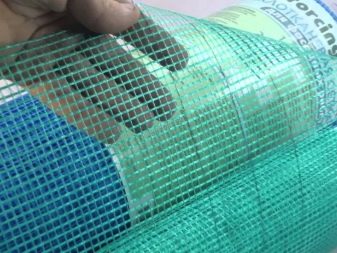
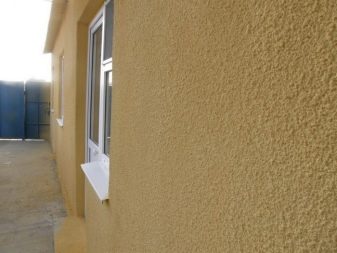
Large firms working on the construction of large buildings and structures often use a rigid type of polyurethane foam. This saves time and money.
In addition, it is economically profitable to cover the insulation of a hangar, warehouse or high-rise building with just such polyurethane foam, since it is more durable, faster to apply, and does not require additional costs for leveling the walls.
Polyurethane foam can be applied in two ways:
- Spraying. The process takes place with the help of special equipment in the form of a pistol, into which two components and water are supplied. A chemical reaction takes place, as a result of which polyurethane foam is obtained, evenly laying down on an open surface.
- Fill. In this case, the components are mixed in advance and the resulting mixture is poured into the hole.The method is suitable for closed and hard-to-reach places, complex architectural forms (niches, arches, various ledges, corners, columns), old buildings.
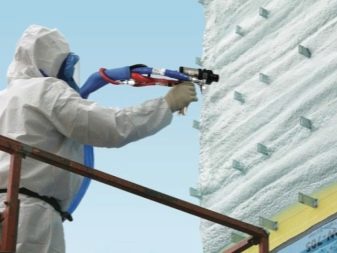
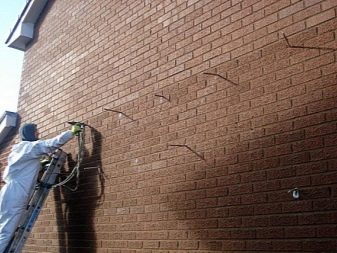
Helpful tips from the pros
- When self-warming the facades of buildings, it must be borne in mind that after applying polyurethane foam to the surface, it increases in volume within a short period of time. Therefore, it is better to foresee the amount of material to be applied in advance, so as not to break the cracks filled with it even more when expanding.
- PU foam hardens very quickly and has super adhesion to all types of surfaces. There are no products to wash it off. In this regard, it should be borne in mind that the time for doing the work itself and eliminating inaccuracies is extremely small.
- To fill cavities, for example, between a facing brick wall and a foam block, it is better to use special filling mixtures. They do not expand as quickly as foam, so the structure will not expand. However, it should be borne in mind that the cost of such a system is much higher.
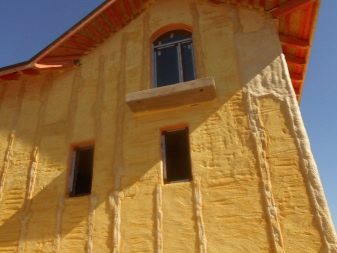
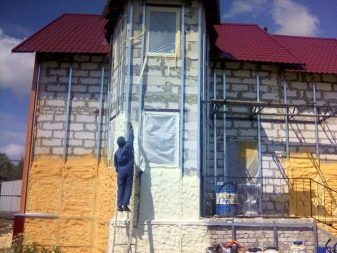
- Water is often used for foaming polyurethane foam, so experts do not advise applying such insulation to galvanized surfaces. This will degrade the properties of the metal. Also, closed-cell modifications of PPU are not suitable for galvanizing. Since the metal has sufficient strength, it does not need additional reinforcement.
- It is imperative to cover the polyurethane foam on top with some kind of finishing material during external processing, since polyurethane foam is afraid of ultraviolet radiation.
- Before starting the insulation, it is better to preliminarily make a calculation to determine the amount of polyurethane foam. First of all, the thickness of the applied layer is calculated. For example, for a roof with an area of 45 sq. m the best option would be a size from 6 to 10 cm. When increasing the area to 50 sq. m and more, the range will decrease to a level of 3-7 cm. When calculating the heat-saving effect, the number of window and door openings, wall material, the presence of energy-saving materials, and the climate of the region are also taken into account.
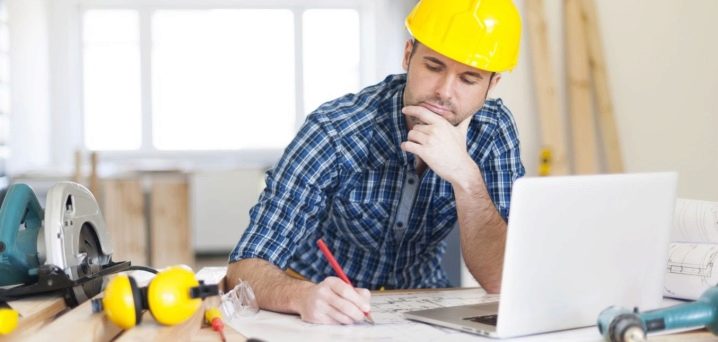
- Before insulating the wall from the inside, it is necessary to evaluate its thermal resistance coefficient. If the surface is warm, then the polyurethane foam insulation is best applied outside. In this case, the thermal resistance of the wall and the polyurethane foam add up, which means that the desired effect is achieved. If you do the opposite, the outer surface will freeze through, which will negatively affect the overall thermal resistance.
- For independent use, it is better to purchase disposable polyurethane foam application kits. Everything is provided in them: a spray bottle, hoses, fasteners, tools, spare parts, even personal protective equipment (glasses, gloves and a respirator).
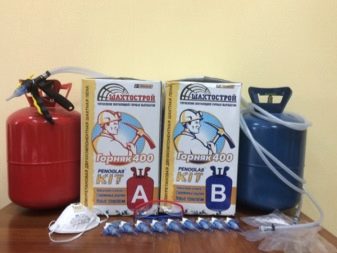
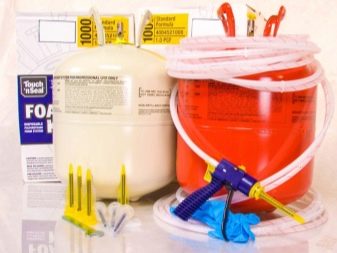
- Do not worry that wooden uprights, such as roof beams, will deteriorate under the vapor barrier made of polyurethane foam. The vapor permeability coefficients for wood and polyurethane foam are approximately the same, which excludes the occurrence of such problems.
- It is not recommended to process the roof from the inside with open-cell polyurethane foam. Of course, as a thermal insulation, it is better than other mineral heaters, but since its vapor barrier is worse, additional costs for ventilation and an insulating layer will be required. Therefore, this option is considered economically unfeasible.
- Polyurethane foam is not able to cope with fire, although it is fireproof. Therefore, if there is a constant effect of high temperatures on the surfaces to be insulated, then it is better to refuse from PPU. When burned, it smolders and emits acrid smoke that is harmful to health.
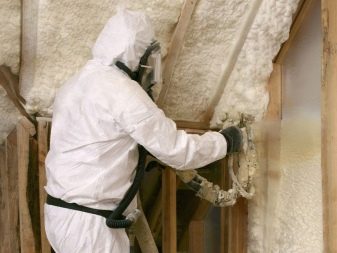
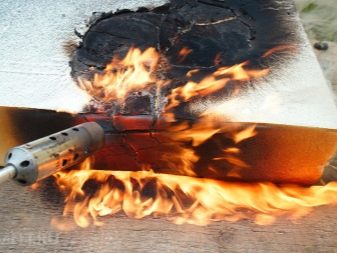
Contractor selection
Insulation of buildings and structures requires special practice, sophisticated equipment and high-quality components of the mixture. Therefore, if you have financial opportunities, it is better to use the services of specialized firms. In order not to get into a mess, professionals advise to adhere to the following rules when choosing them:
- Hire the best proven companies with recommendations.
- The components of polyurethane foam insulation must have quality certificates.
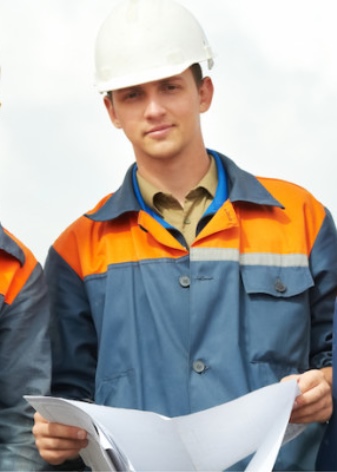
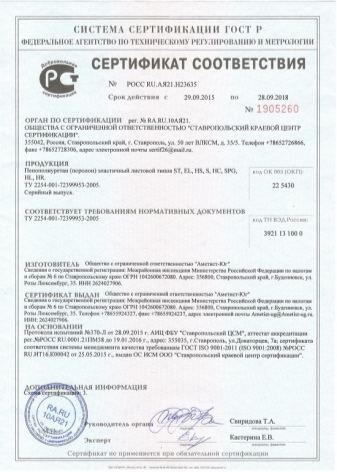
- Before starting work, it is better to make sure yourself that the storage period of the components has not expired.
- Equipment for spraying and feeding PUF must also have documents. As a rule, contractors who have been working in the field of construction with large objects for a long time use high-pressure washers of famous world brands that have proven themselves in this area. For example, Graco or Gama.
Plunger pumps ensure uniform application of PU foam.
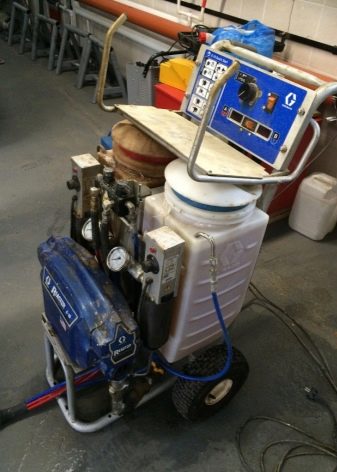

Before signing the contract, you need to carefully read all its terms and conditions and clarify all the incomprehensible places associated with the timing of completion of work, payment, prepayment, etc.
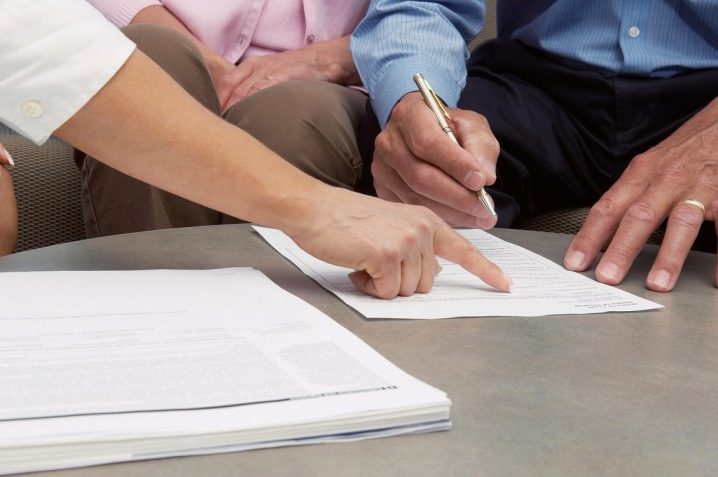
For the features of sprayed polyurethane foam and how to apply it, see the next video.
The comment was sent successfully.