Vibro-pressed paving slabs
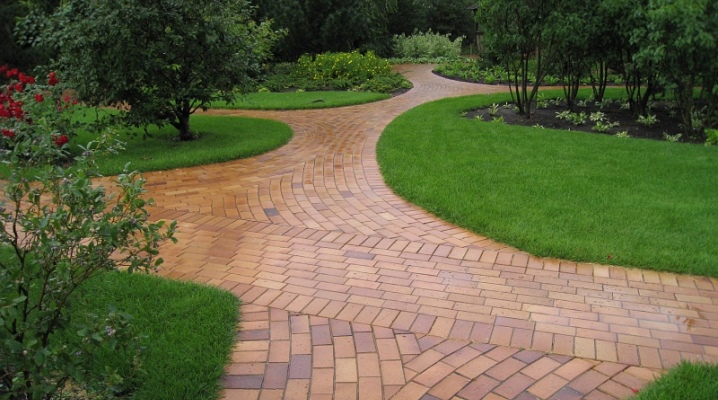
Manufacturing technologies for curly paving elements are different. At the same time, vibropressed paving slabs are considered to be a particularly popular product among builders. From the material in this article, you will learn what it is, what it is, from what and how it is made. In addition, we will consider the nuances of her choice and styling.
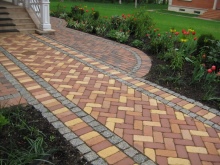
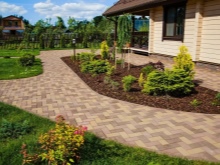
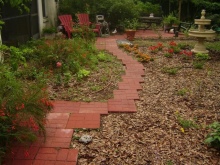
What it is?
Vibro-pressed paving slabs are a type of concrete coating used in the arrangement of sidewalks, squares and roads. It is a building material with excellent performance characteristics. It is maximally resistant to temperature fluctuations, high humidity.
Pressed tiles are designed to withstand impressive general and local loads. It is produced using a vibrating press, this process is fully automated. It is regulated by GOST 17608-2017 ("Concrete sidewalk slabs").
The vibrocompression technique involves the use of less water than in the production of conventional concrete.
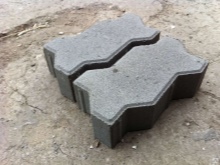
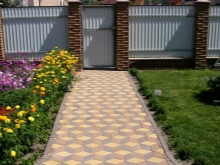
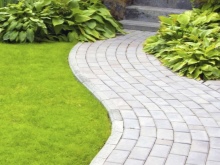
Such material is considered universal. It is heat-resistant, easily fits on a sand cushion, forms a dense and even coating. Tiles are used for track design. Outwardly, it resembles brickwork. Does not emit toxic substances, environmentally friendly.
Depending on the variety, it can withstand a load of up to 15 tons per 1 sq. m. It is not destroyed by the action of acids, it is distinguished by a strong compression of the rocks used. It is characterized by high aesthetic performance. It can have a different shape, which makes it possible to use different laying schemes when arranging the roadway.
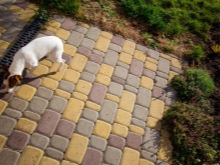
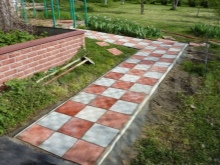
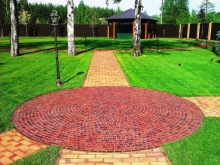
Suitable for paving any road sections. Does not crack in the cold, has a wide color palette. It can have different sizes, different textures, assumes a long service life. Perfectly decorates the landscape, suitable for the arrangement of territories near buildings of different architectural styles.
The technical characteristics of the material are as follows:
- abrasion - 0.21 g / sq. cm;
- strength - M-300 - M-500;
- frost resistance - F 300;
- water permeability - W6.
The water-cement ratio of the mixture is 0.55. Due to its dimensional stability, the material is easy to work with.
After laying it, it is possible to fill the joints with ordinary cheap sand (not quartz). It will not be washed out by rain and blown out by the wind.
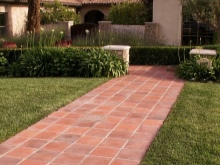
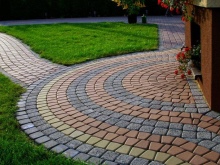
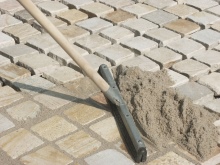
What is used for making?
In the production of vibropressed paving slabs, cement, aggregates, water, and modifying additives are used. The main ingredients of the mixture are sand, crushed stone, cement, water, pigments. Each component gives the solution certain properties.
- Cement is a binder. Its color can be traditional gray, white. White cement is used to produce tiles with a bright, clean color. Cement is needed for the strength and moisture resistance of the modules.
- The crushed stone used gives the tile compressive strength and increases its durability. In addition, it reduces creep, shrinkage, and cement consumption.
- Sand is responsible for the plasticity of the mixture. It prevents the concrete from cracking and is responsible for the smoothness of the surface.
- Pigments allow you to diversify the shades of the working solution. Thanks to them, you can lay out colored tracks of different shades, both monochromatic and patterned.
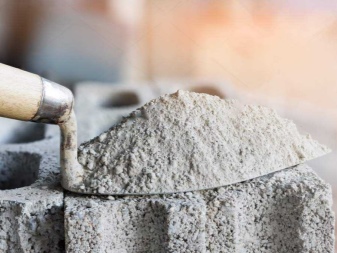
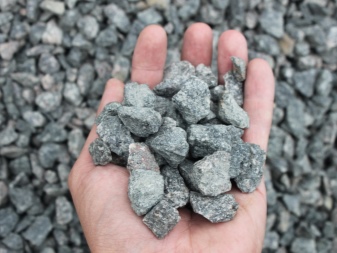
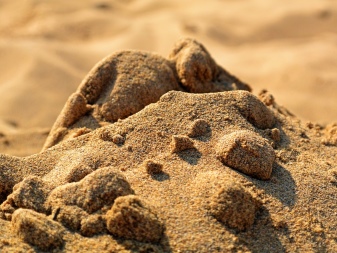
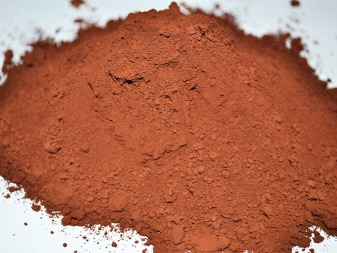
Production technology
Dosing, mixing, pressing the mixture is carried out in an automated way. Thanks to such a production system, the quality of the dyeing of the mixture is also higher. In production, molds and a semi-dry mixture of concrete are used.
Products are formed by means of a matrix and a punch, by the action of a vibrating press. This process is very complex and expensive, but it is considered the best way to produce paving stones. The production itself resembles vibratory casting, but with automation it becomes possible to supply the production of concrete to the flow.
The process looks like this:
- the equipment doses the composition of the concrete mixture in the specified proportions;
- stirring the mixture to a state of homogeneity;
- the equipment fills the curly forms with semi-dry material;
- after that, the modules are pressed with a machine under the influence of static and dynamic loads;
- perform demoulding of the compacted workpieces.
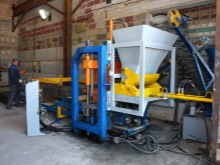
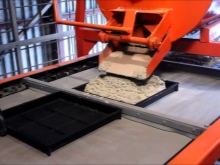
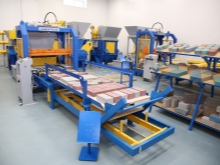
After removal, finished modules are stored on pallets in ordinary storage facilities. Sometimes building materials are stored outdoors. The use of vertical pressure automation ensures that the thickness of the modules is identical and the density is equal. Automation of the process simplifies demoulding, allows the production of not only typical single-layer, but also double-layer tiles. When using the machine, the strength characteristics of the modules and the finished finish are increased.
In-line production has clear advantages over other technologies for the manufacture of paving stones. This method of manufacturing with vibration and simultaneous pressing of the mixture allows to achieve a homogeneous product.
The tile can be hyper-pressed. In this case, a punch presses on the solution inside the matrix. As a result, slabs of special strength and minimal water permeability are obtained. Unfortunately, it is almost impossible to process them.
In view of this, when choosing a finishing scheme, one has to give preference to the simplest options.
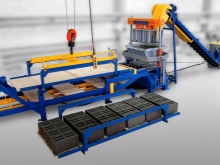
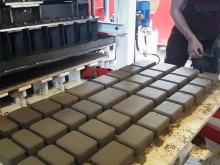
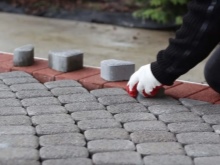
Comparison with vibrocast tiles
The main difference is the principle of forming modules. Cast bars are formed under their own weight. Vibropressed - by compression. Vibro-pressed paving slabs are ahead of cast ones in many respects, except for cost. Its frost resistance, strength, service life, abrasion resistance are 2 times higher.
It can be installed when constructing roads for light vehicles. It is more durable and practical than vibration casting. Its density is noticeably higher than casting and vibration casting. However, its production process is more complicated and time consuming. It is resistant to weathering and sunlight.
The difference between the materials lies in the type of surface. Vibro-pressed tiles have a rough structure. As a result, it provides increased safety for pedestrians in rain and icy conditions. However, vibrocasting tiles are cheaper. The surface of the vibrated variety is smooth and slippery, so manufacturers often make it textured.
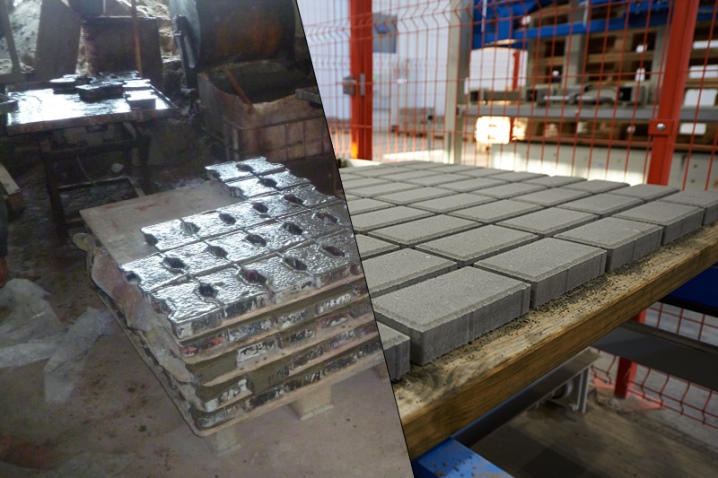
In addition, vibrocast tiles are easy to cut and fade quickly. It is produced using a liquid working solution. After evaporation of excess moisture, voids remain in the structure, which is not the case for a vibropressed analogue.
The structure of the tile, created using vibrocompression technology, is finely porous. Water cannot penetrate it. The cast material allows rainwater to pass through, and in case of severe frost, ice can break the module from the inside, reducing its strength characteristics.
As practice shows, the laid compressed roadbed requires repair in at least 25 years with the replacement of about 20-30% of the modules. Vibro-cast tiles will need to be repaired in 5-10 years. And about 70-80% of the flooring will have to be replaced.
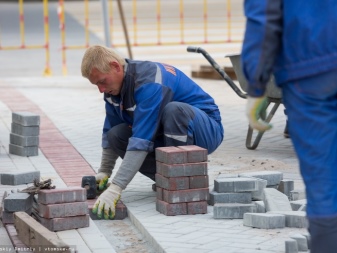
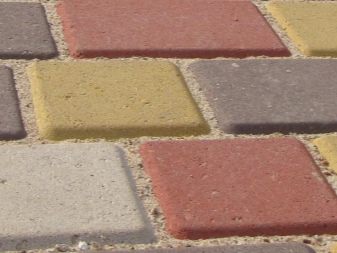
Casting tiles do not always have ideal geometry and identical thickness. The solidity of the coating suffers from this. With an automated production method, bars with precise shapes and sizes are obtained.However, in terms of the variability of forms, the vibrocasting variety is more diverse.
The difference between the materials is also visible in the structure. The vibrocast material has a noticeable heterogeneity of the layers. This can cause the surface web to peel off from the substrate. Vibro-pressed tiles are devoid of this drawback. She has a unique texture and noble appearance, but her tones are not so bright.
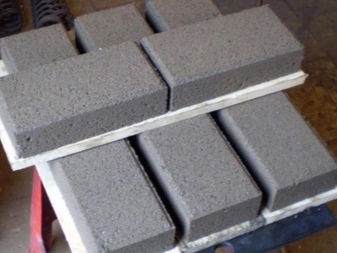
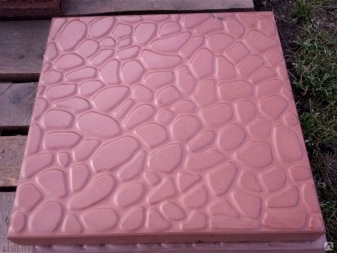
What happens?
Vibro-pressed paving slabs differ in color, size, shape, texture, number of layers. Its color solutions are varied: the buyer can purchase modules in gray, sand, red, black. Besides, on sale there is a material of brown, terracotta, green, white, marsh shades.
As for the texture, the material is conditionally smooth, rough and textured. Among other options, there are tactile-type modules on sale. The shapes of the pressed modules can be square, rectangular, diamond-shaped, hexagonal.
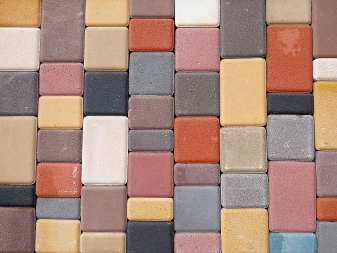
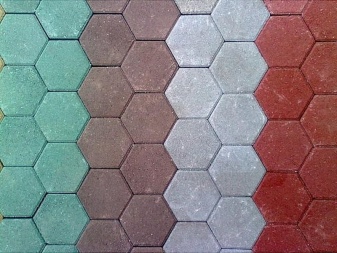
Paving sizes also vary. On sale there are products with parameters 300x300x60, 500x500x50, 100x200x60, 100x200x50 mm. Modules with a thickness of 20, 40, 60, 80 mm are a popular material.
The weight of the material also varies: a square module 40x40 cm weighs 21 kg. A 500x500 mm stone weighs 38 kg if the stone is 70 mm thick and 34 kg when the thickness is 60 mm. The weight of the paving stone 200x200x60 mm is 5.3 kg (1 piece). A brick with parameters 200x100x60 mm weighs 2.6 kg.
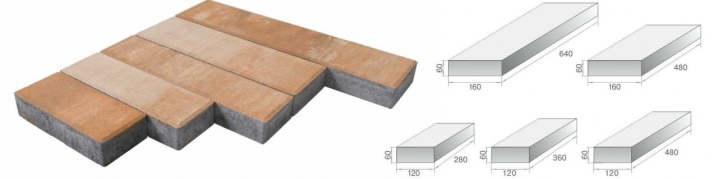
Nuances of choice
Vibro-pressed tiles are one of the best materials for the blind area of any territory. However, in order for it to serve for a long time, a number of nuances must be taken into account when purchasing raw materials.
The quality of the modules is indicated by their appearance. If, upon visual inspection, on the reverse side of the dice, rare pits of a round or oval shape (2-6 mm in diameter, 1-2 mm in depth) are noticeable, this indicates a violation of the construction material production technology. Or it is a tile made by the vibrocasting method.
The performance properties of this material are unknown. In order not to doubt the choice, you need to ask the seller for a certificate of conformity or a passport for the goods. The quality material has all the necessary documentation.
Therefore, its service life is calculated in decades. On average, such a coating lasts up to 30 years.
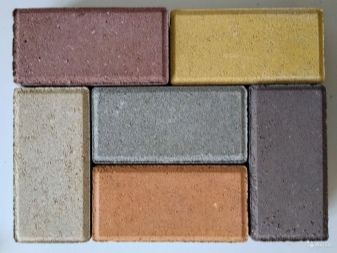
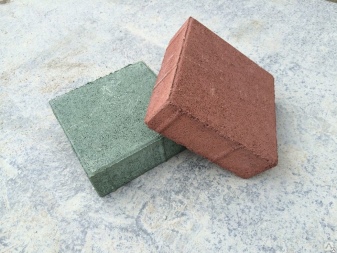
The certificate must contain the protocol number and the date of certification tests. If these data are not available, the quality of the material has not been confirmed, as is the technology of its manufacture and composition.
If the product is of high quality, the thickness is determined, taking into account the type of load. Modules 3-4 cm thick are used to equip garden and pedestrian paths, terraces, a blind area near the house. When building material is needed for laying areas with limited movement of light vehicles, plates with a thickness of 4.5-6.5 cm are chosen.
7 cm thick tiles are used for paving areas with heavy traffic. However, thickness is not the most important indicator. Frost resistance matters. If the frost resistance class of the components does not correspond to the winter temperature of a particular region, the purchase should be abandoned. With low frost resistance, the tile begins to crack and crumble after a few years from the moment of installation.
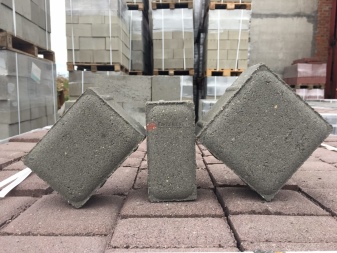
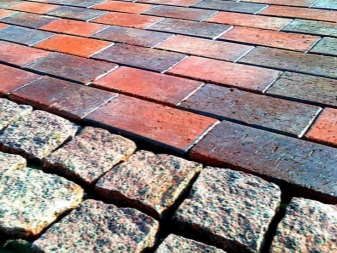
Experienced contractors prefer to purchase material from factories that strictly control product quality. At the same time, they note that good material is not too cheap: often cheap tiles are made using low-quality dyes and cement.
The criterion of pressing layers is important. A two-layer tile is a module with a rough base layer and a second decorative layer.
The base of the element is made of diabase or crushed granite. The top layer is shock and wear resistant.
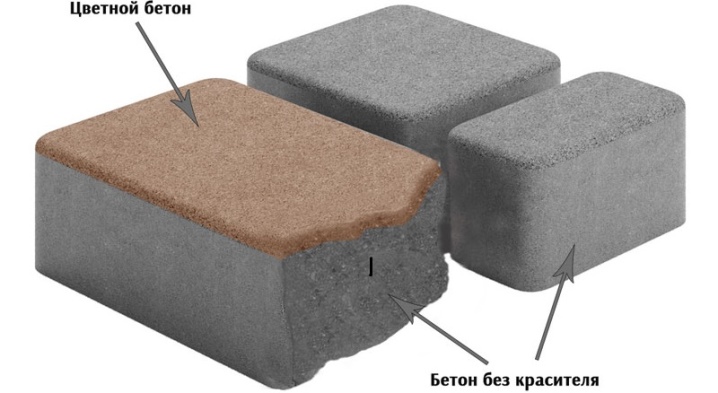
Single-layer tiles, although strong, are not so strong. In addition, it does not have such decorative properties as two-layer. To assess the quality of a two-layer module, you need to put its end in a pallet and pour water on the bottom (2-3 cm). If after 5 minutes the level of rise is more than half of the brick, this means poor quality.
It is impossible to choose a good tile in absentia: it is necessary to inspect the appearance of the building material. There should be no obvious defects on its surface (cracks, accumulations of graininess, imperfections). You can take 2 modules and lightly hit each other: a ringing sound indicates good quality of the product.
You need to take pigmented tiles from one batch. In order not to buy excess material, calculations are performed before laying. However, the material is not taken end-to-end either: a minimum stock is needed.
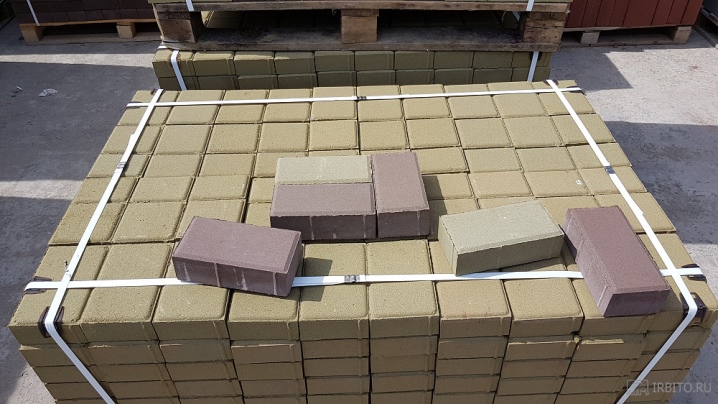
Styling options
Laying schemes for vibropressed paving slabs may be different. They depend on the shape of the material used; they can be a classic plain panel or a coating with an extraordinary pattern. In this case, the styling can be traditional or with a shift.
For example, tiles can be laid according to the principle of a diagonal herringbone: with a material of one color or two (three) contrasting ones. The same brick modules can be laid with teeth, forming wavy rows of them.
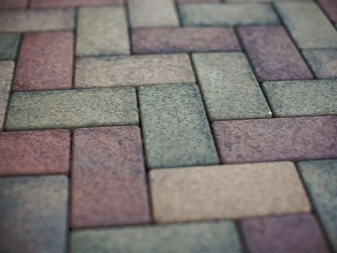
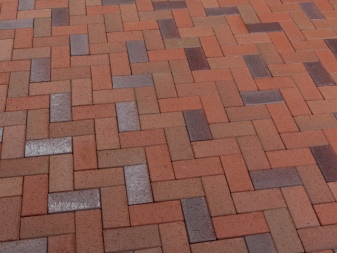
The surface, laid out by the method of conventional facing "brick with a shift", looks beautiful. If, during the installation of the finish, alternate material of identical shape, but in different tones, you get a coating with diagonal rows.
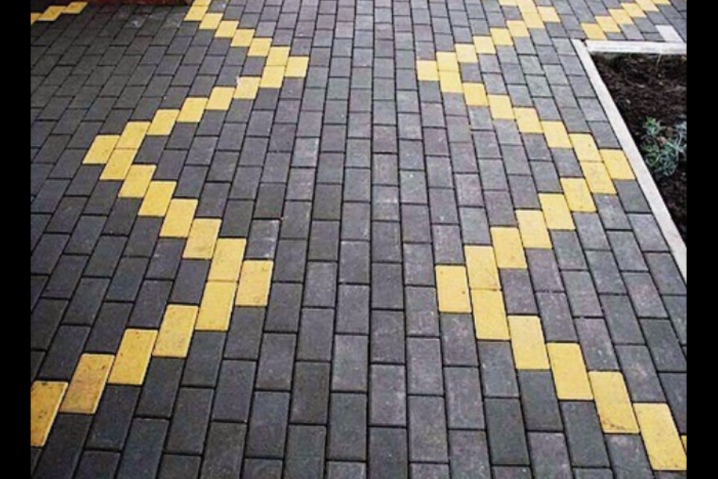
When choosing one or another installation option, you can use the same schemes as when laying floor (wall) tiles. This can be an alternation of perpendicularly located elements, a rotation of a tile according to the principle of a spiral. Some craftsmen can create canvases with a volume effect from ordinary geometric bars.
Due to the identical dimensions, the tile blocks can be rotated and shifted as desired.
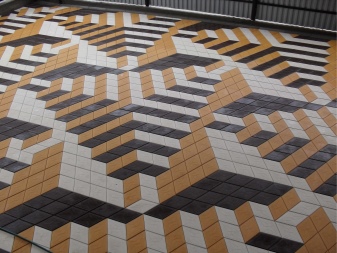
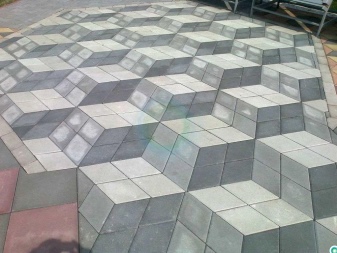
The comment was sent successfully.