Mixes for laying paving slabs

The mixture is the main component when laying paving slabs, because the quality of the future road surface depends on it. Various materials and technologies are used in its manufacture. To choose the right option, you should consider the methods most often used when laying paving slabs.
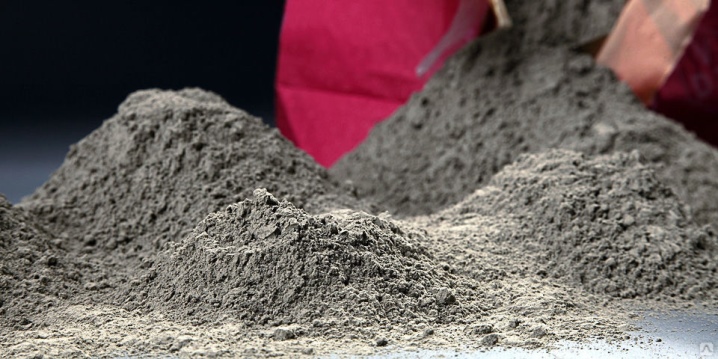
Properties
A ready-made mixture for laying paving slabs can be purchased at a specialized store or you can prepare it yourself.
The packaging of the mixes from the store contains all the information you need to know about the product. This allows you to choose a suitable option, as well as calculate the flow rate of the solution for the work.
However, a home-made mixture is just as good as a store-bought mixture if prepared correctly.
The main properties of a mixture of paving slabs depend on its type. So, a sandy solution is an excellent drainage, and there is practically no need to care for the tiles installed on such a base.
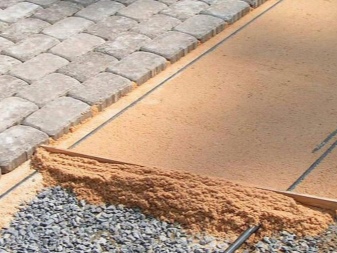
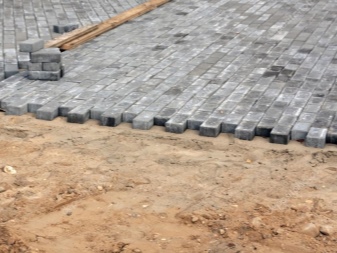
If one of the structural elements is damaged, you can easily replace it with a new one. An obvious disadvantage of the sand mixture is the lack of resistance to loads. Cement-sand mortar has high strength and resistance to stress, but it has a high cost compared to a sand mixture. The concrete mix is the most durable of all of the above, it is perfect for those areas on which people will constantly walk or transport vehicles. However, the complexity of the installation of tiles when using this method is significantly increased.
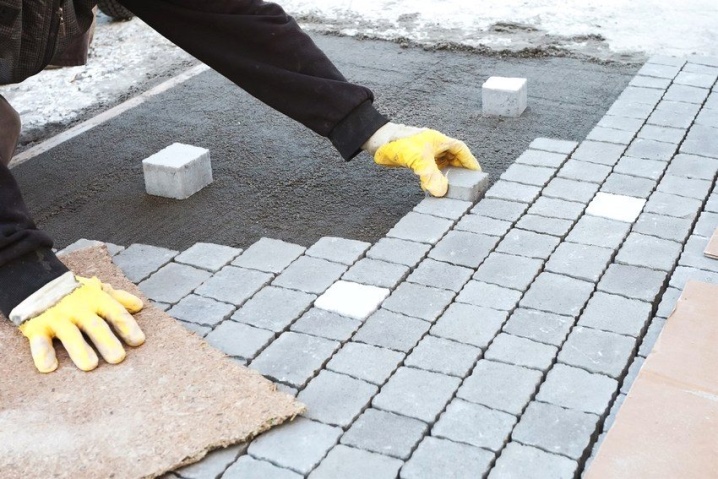
Types of compositions
Today the market offers a wide range of mixes that are intended for masonry or renovation work.
This includes track, assembly, plaster, glue and other types of mixtures used by modern specialists.
The types of mortars for installing paving slabs can be different.
- Cement mix, to which sand, sealant and water are added. The most popular mortar for paving slabs.
- Sand mixture. A simple composition based only on sand with the addition of water. Suitable for areas where a heavy load is not expected.
- Concrete mix with the addition of sand and gravel. Highest quality and most durable option.
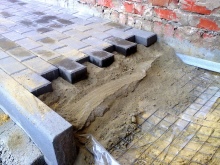
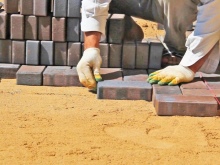
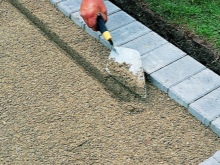
There are also different styling methods.
- Wet way, in which water is added to the mixture. Provides a stronger fixation of paving slabs.
- Dry methodthat does not involve the addition of liquid. A dry mixture takes much longer than a wet one, and perfectly eliminates gaps, if any, between tiles.
It is worth noting that most often the choice is given in favor of a cement mixture, which is distinguished not only by its ease of preparation and use, but also by excellent strength.
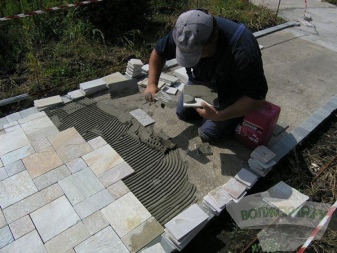
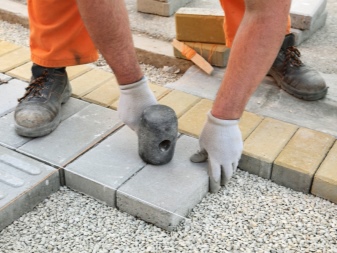
Preparation
For convenience, it is worth considering the technology for preparing the most common mixture - cement.
To make the material for laying paving slabs, follow the step-by-step instructions that will help you prepare the mixture at home with your own hands.
First of all, you need to prepare the components for manufacturing. The main materials are cement, water and sand. You will also need large containers and a tool with a nozzle to bring the mixture to a suitable consistency. It's great if you can use a concrete mixer. Sometimes a special glue is added to the solution for installing tile tiles.
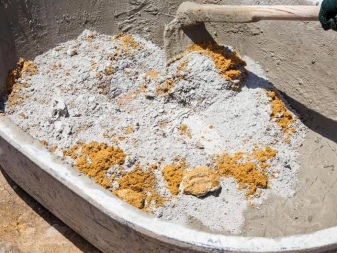
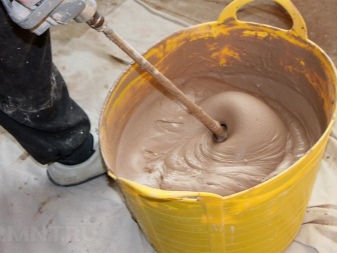
It is important to determine the exact amount of materials that will be needed to make the mortar. This will help keep costs to a minimum. The amount of materials required directly depends on the density of the solution. A mixture with a dense consistency requires more consumption. It is also not worth making the solution liquid: this can negatively affect its quality. The main component of the solution is the binder that provides fixation of the paving slabs - cement. If you follow GOST, the masonry mix should consist of Portland cement, which does not contain mineral impurities.
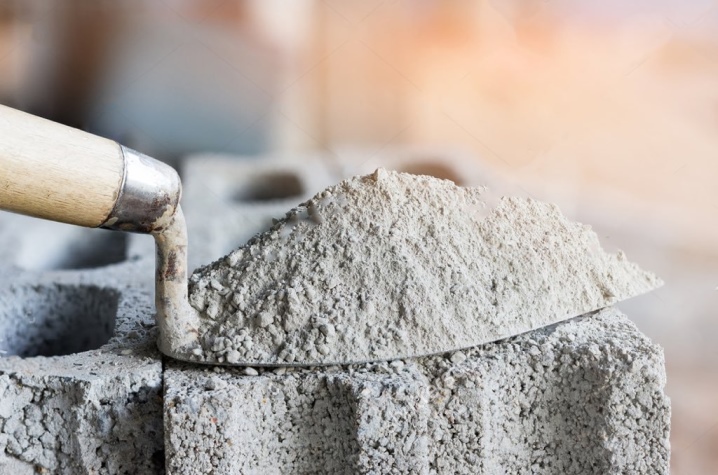
To prepare a high-quality mixture, it is necessary to observe the proportions of the ratio of sand and cement - 3: 1. In this case, it is worth considering the type of cement: the higher the number of its brand, the more sand will be needed to prepare the solution. After mixing the materials, the solution is poured onto a sand cushion, which can be pre-moistened with water. Its thickness should be no more than 5 cm. But to prepare a concrete mixture, it is necessary to use not only sand and cement, but also crushed stone. The proportions of the solution preparation are 1: 3: 2.
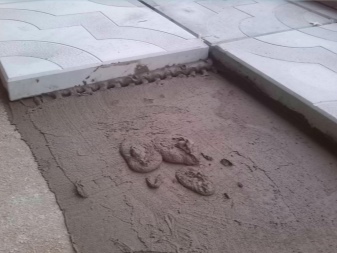
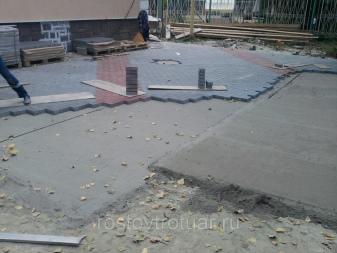
Application rules
The correct application depends on which method you choose to lay the paving slabs. If the tiles are laid on a sand base, the thickness of the installation layer should be about 60 millimeters. This method is appropriate for the improvement of pedestrian paths: a sandy base will perfectly cope with the drainage function, but will not withstand heavy loads. To evenly distribute the solution, use galvanized profile beacons, which are used when installing drywall.
Beacons must be installed over the surface area, the distance between them should be no more than one meter.
To compact the surface, the material should be tamped by hand or with a vibrating plate. Lighthouses are removed, and the space is covered with sand. The solution must also be tamped. To compact the layer, the surface must be poured abundantly with water. It is easier to work with a mixture saturated with moisture, so it will be much easier to lay paving slabs.
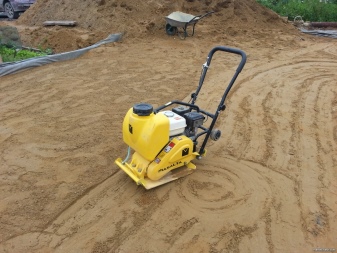
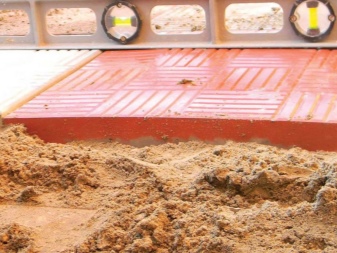
The method of laying paving slabs on cement mortar is the most common. Mortar installation has more advantages than dry mix installation. The material adheres more closely to the surface, which increases the quality of the masonry. Before laying the tiles on a mortar of cement and sand, it is worthwhile to prepare the surface in advance and carefully tamp it. Its layer should be at least 30 cm. To strengthen the coating, it is recommended to install a network of reinforcement. The cement-sand mortar can be prepared independently, but when buying a ready-made mixture, it is easier to calculate the material consumption.
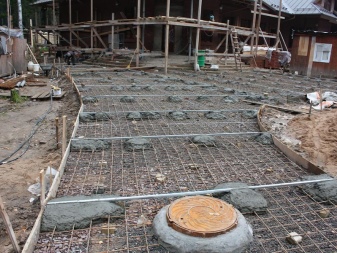
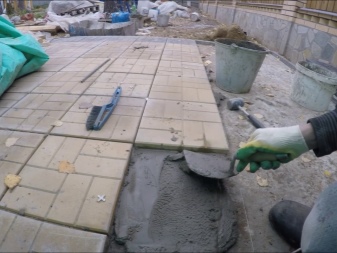
The highest quality of installation is achieved by placing the tiles on a concrete mortar. Such a coating is capable of withstanding heavy loads. You can lay tiles and not worry that the quality of the coating will suffer after the passage of heavy vehicles. To strengthen the base, the reinforcement mesh is installed without fail: its rods should be about 10 mm in thickness. The concrete mixture is poured in a layer up to 5 cm, and after installing the mesh - up to 10 cm.
The resulting base must be compacted with a vibrating plate in order to remove the remaining air. It will be possible to start the installation of paving slabs only after 3 days, so that the concrete will properly set.
The joints that appear after the installation of the tiles must be filled: otherwise, the integrity of the material may be compromised in the future. A budget but short-lived option is to cover them with sand. Another way is to use a cement-sand mortar, which will ensure the strength of the joint. After grouting, the joints should be watered with water to increase the strength of the fixation.
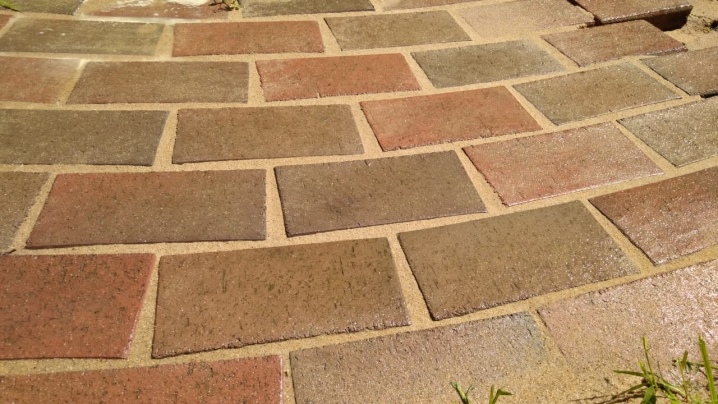
The comment was sent successfully.