Technology of laying paving slabs for screening
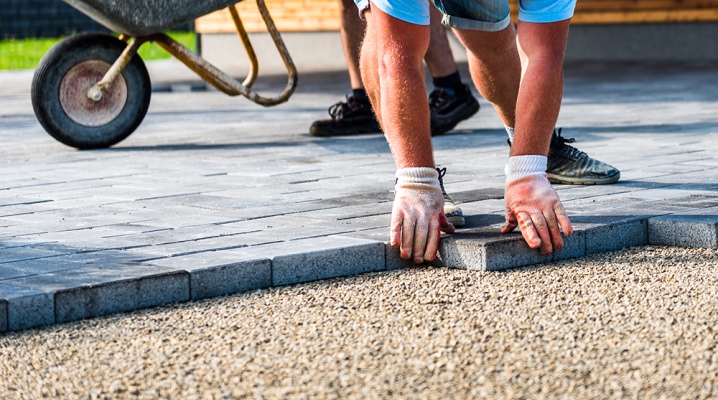
The technology of laying paving slabs for screening is very important when decorating any yard or other site. It is necessary to carefully study the step-by-step instructions for laying paving stones with your own hands in order to avoid mistakes. At the same time, the technology of work and the choice of the best dropout rate are equally important.
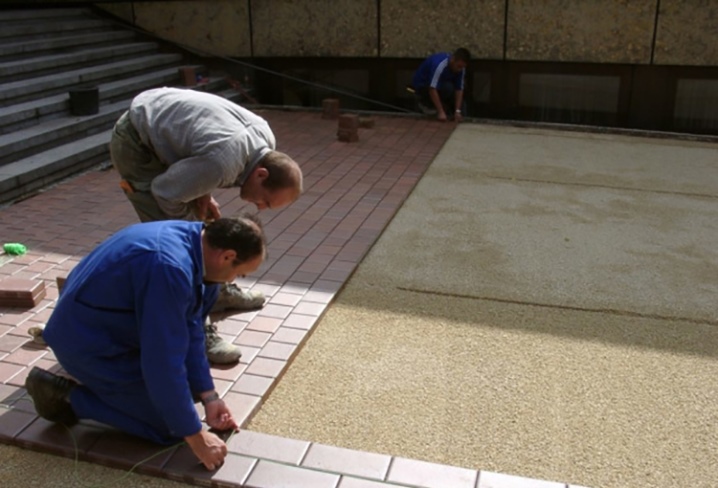
Advantages and disadvantages
Laying paving slabs for screening is not such a new technology as it might seem. This procedure is used in very many cases. Lay out the layer perfectly evenly, and it is also not difficult to tamp it. Moreover, sifting perfectly fills the gaps that form between individual tiles. Additionally note:
-
excellent moisture permeability;
-
inability to retain water;
-
almost zero risk of being washed out by rain - in this regard, screening out the comparison with sand wins absolutely;
-
almost complete absence of subsidence even under heavy load.
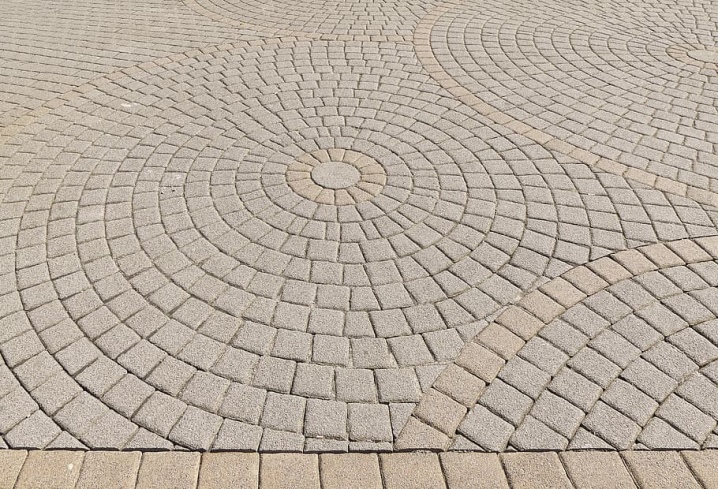
Screening of fines is supplied in containers of 25-50 kg. And also it can be shipped in bulk in almost unlimited volume. Of course, this allows such a material to be used in the most flexible way for laying paving stones and other types of tiles.
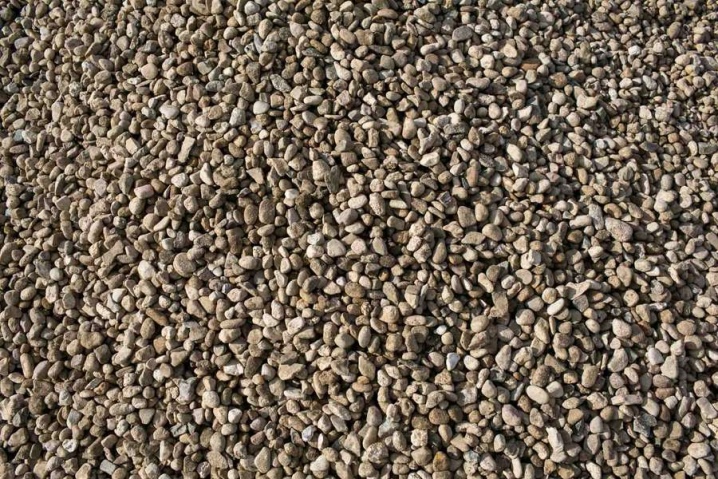
The cost of the screening mass is quite sparing, and you can afford it even with a limited budget. But it should be borne in mind that sifting when moistened can turn into porridge, and this can only be avoided by careful preparation and solid tamping.
Dropout selection
On the market, the screening mass is presented in a large number of varieties. And the widespread opinion that you can safely choose any option is not entirely true. Of course, the externally filled layer will look about the same in any case, when the technology is followed.
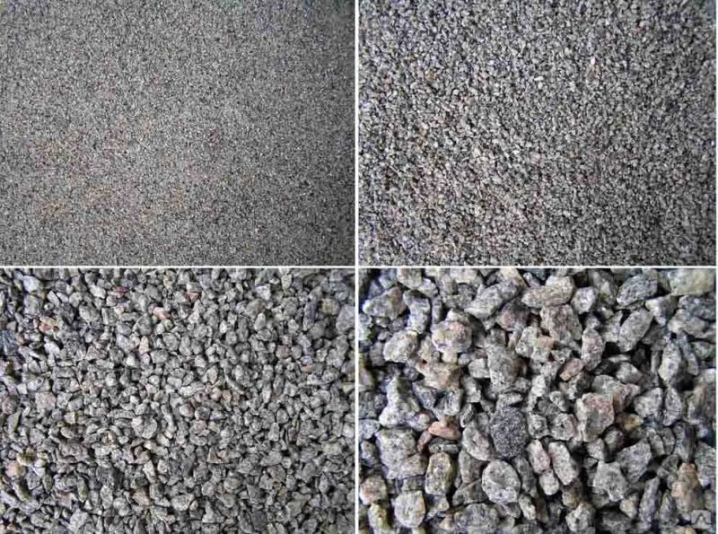
However, practical properties can vary greatly. As a pillow, according to experts, it is better to choose a fine fraction.
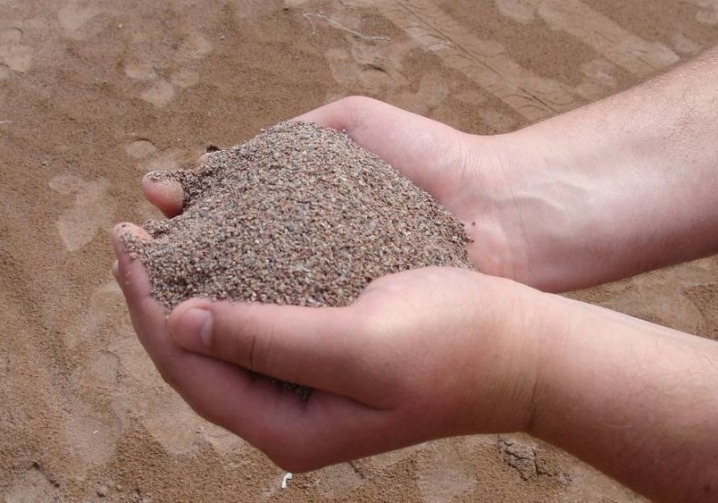
It is closest to the sand and therefore lends itself well to tamping and subsequent leveling. It is convenient to lay plates on top of the shallow dropout. Their bias is almost completely excluded. The cover and pad will not be separated by a void where water can collect.
Important: almost always, the screenings have to be mixed with cement, which will have to be taken into account when determining its volume.
Also critically important:
-
concentration of clay and dust particles;
-
mechanical fortress;
-
resistance to cold;
-
filtration intensity;
-
the degree of radioactivity.
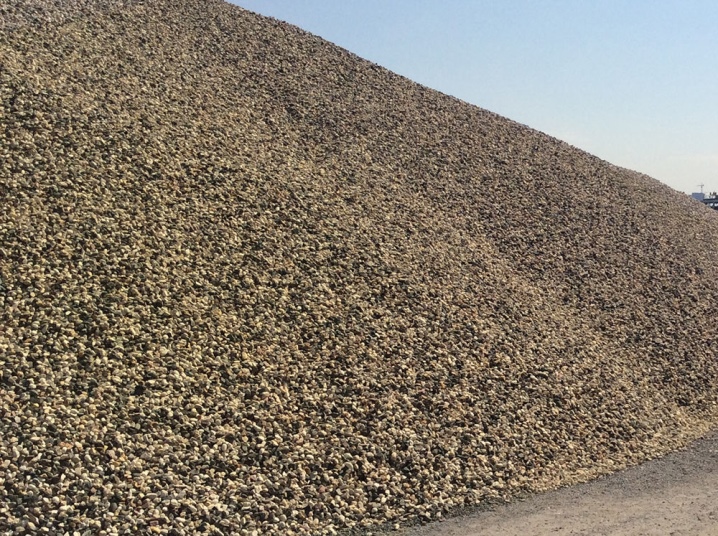
Dust particles - anything smaller than 0.063 mm. The share of such inclusions should account for a maximum of 1/10 of the total product. If there are more dusty masses, the screenings will gradually turn into porridge even with slight dampness. The presence of clay is not much better - it provokes swelling. Following the substrate, the laid tile will also deform.
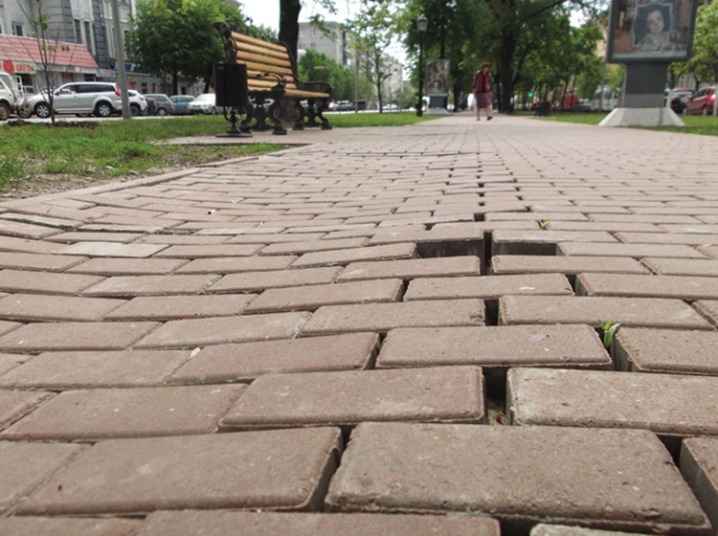
Strength is most important when planning to design an area for the entrance of cars or for parking. An insufficiently strong pillow tends to sag in such places. In Russian conditions, the importance of frost-resistant qualities is also obvious. If they are weak, the pillow will easily break with ice. As for the filtration parameters, they determine the ability of the future pillow to drain water; violation of this ability threatens with alternating swelling and subsidence, they can even be at the same time in different places.
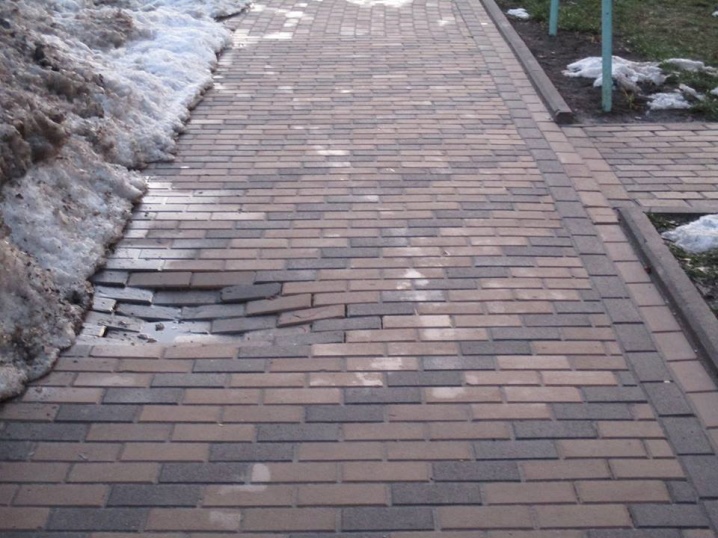
The norm is a filtration activity of at least 0.2 m in 24 hours. But paving slabs are always considered an attribute of a residential area.Therefore, an increased level of requirements is imposed on it. An important safety criterion is minimal radioactivity. Its intensity cannot exceed 370 Bq per 1 kg of mass (this is the natural, permissible radioactive background).
You can lay paving slabs:
-
for granite screening;
-
on gabbro;
-
on diorite or serpentinite.
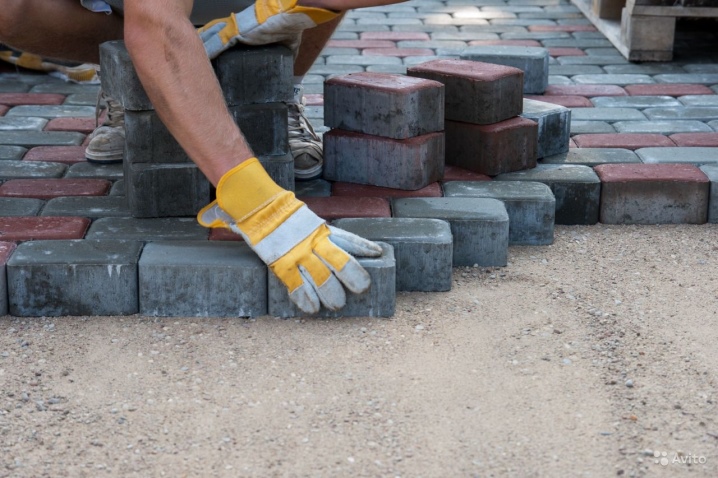
Important: in each region, a particular breed has certain qualities. For example, in a number of regions, gabbro contains a lot of dust and therefore has a poor filtration rate. More precisely, it can correspond to the norm, but there are much better materials. And even in this case, gabbro can be used if the site is dry and the soil water is deep.
Screening of granite fraction 0-5 has a very good reputation. It is a sturdy material with decent performance. There is almost no clay there. Depending on the proportion of dust particles, the water filtration rate varies from 20 cm to 8 m in 24 hours. An important role is played by a specific quarry and the conditions for the formation of the breed in it; a well-suited filter material with a limited proportion of small grains is better suited for the tiles.
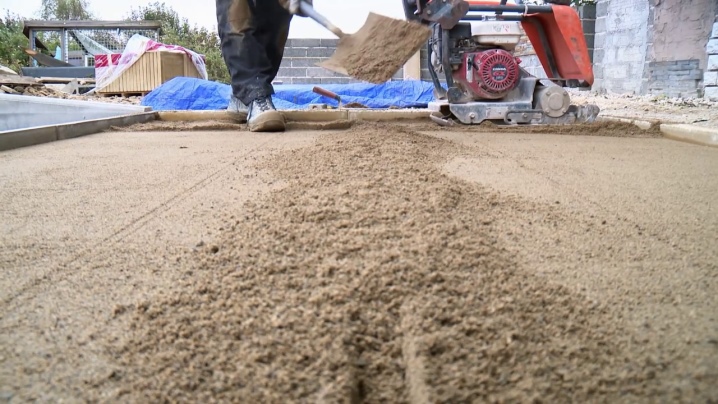
Diorite is also usually taken in fractions 0-5. The composition of such a product will contain no less than 0.81% and no more than 8% of dust particles. Therefore, the filtration coefficient is quite high. This material can be rammed without problems and, in addition, is inferior to granite in terms of radioactivity. On the other hand, there is almost no difference in strength.
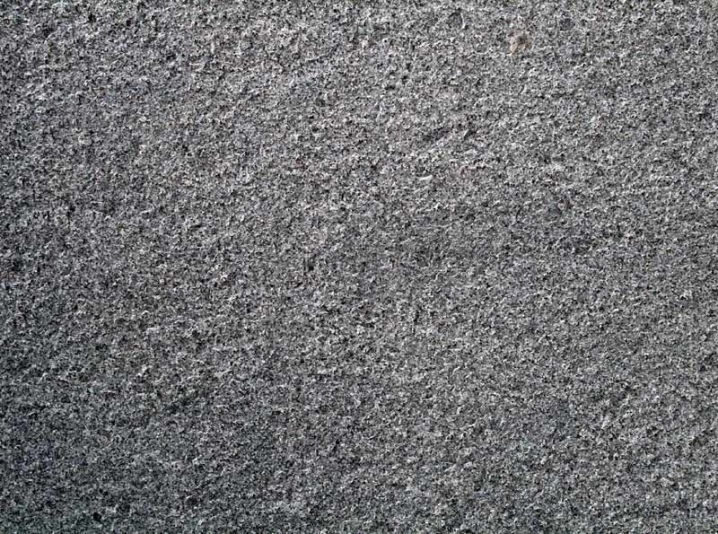
Screening of serpentinite is rarely used in the substrate of paving slabs. It is quite expensive. In addition, there is a lot of dust in this material, and the filtration level is rather weak. Lime screening is appropriate only on garden paths - in all other cases it is advised to replace it with more solid counterparts, primarily granite.
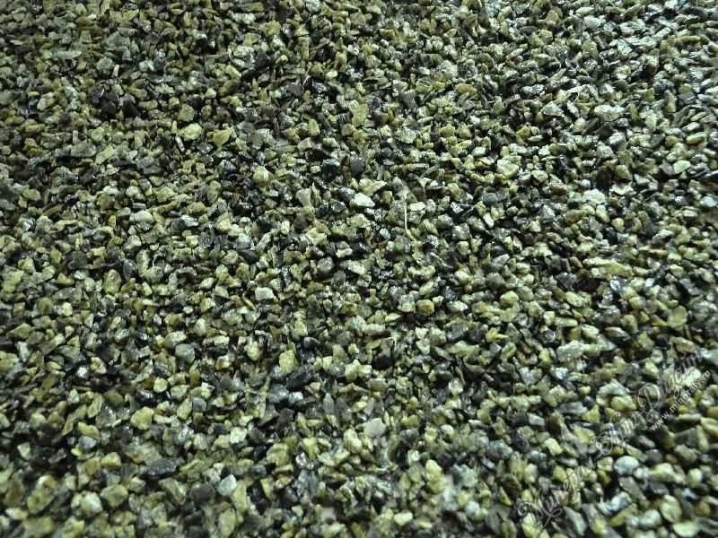
Step-by-step instruction
Screening technology involves the formation of a rigid box. Otherwise, individual blocks will slide. When breaking down, first of all, with their own hands, they put the so-called cast-offs, carried out 1 m from each corner. Curved segments are marked with lime mortar or special paint on the ground. Sifting can be placed only after the design of slopes under the stormwater trays (from 2 to 4 degrees).
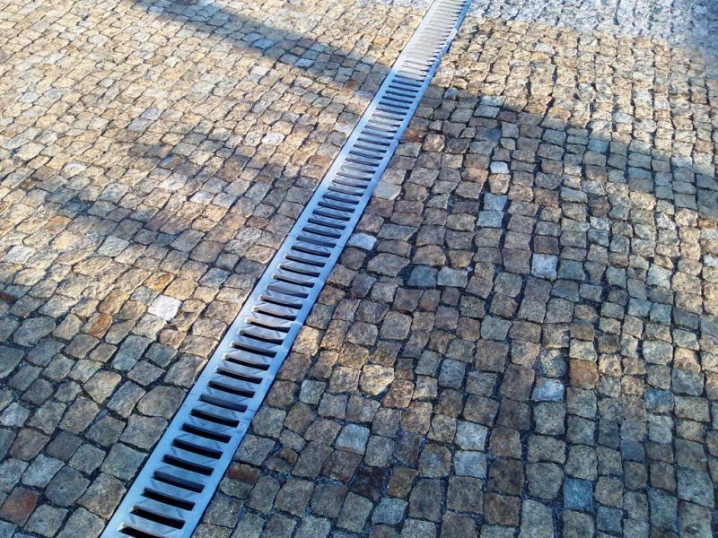
Other subtleties:
-
you cannot work on top of the fertile layer;
-
screenings should be laid in layers of 10-15 cm with sequential compaction;
-
putting mortar blotches on the sides for fixing is very useful;
-
the tiles are knocked out with a mallet.
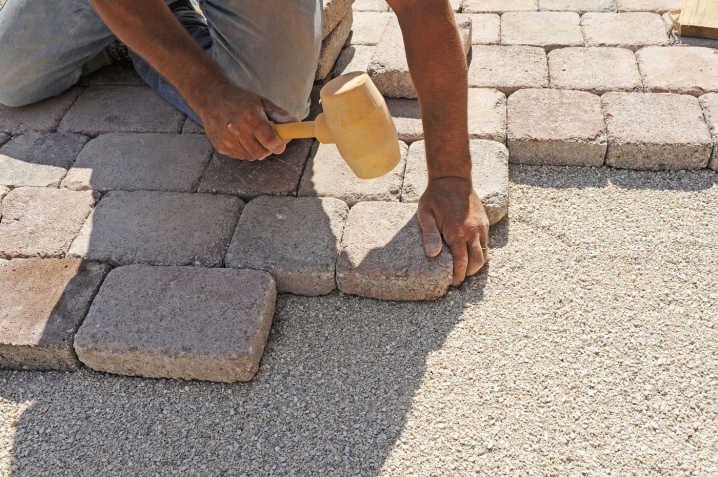
Making seams
Grout is prepared from:
-
cement M-400, M-500;
-
river washed sand;
-
clean water.
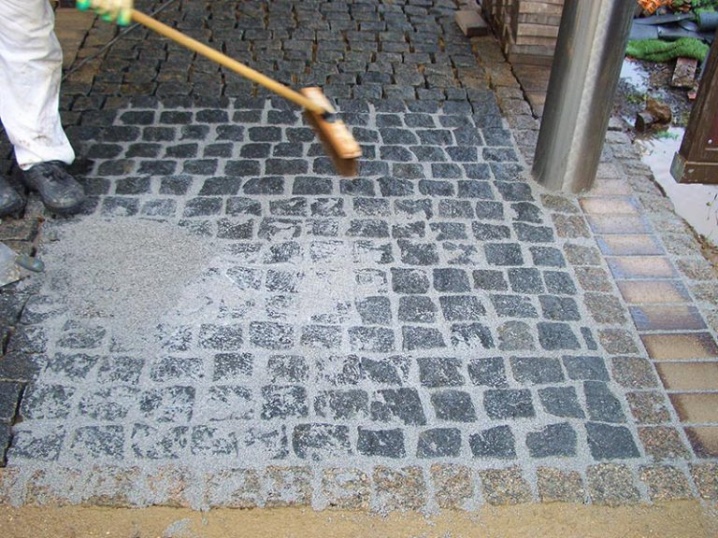
Operating procedure:
-
grouting on a concrete base is done only after 72 hours;
-
ensure cleanliness;
-
fraction up to 0.3 mm;
-
sand needs to be sieved;
-
the excess is removed after 2-3 hours.
You can see the process of work with your own eyes in the next video.
The comment was sent successfully.