Proportions and composition of mortar for paving slabs
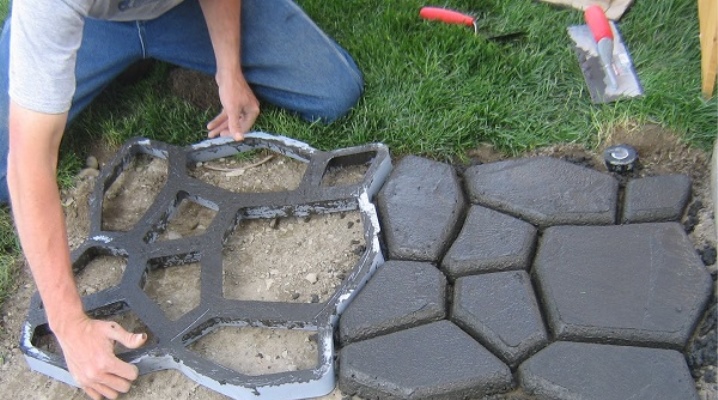
Paving slabs are a building material that is very often used for the arrangement of private plots and public areas. You can purchase it from specialized stores or make your own. You should learn about the features, proportions and composition of the mortar for paving slabs.
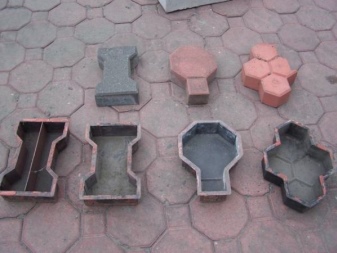
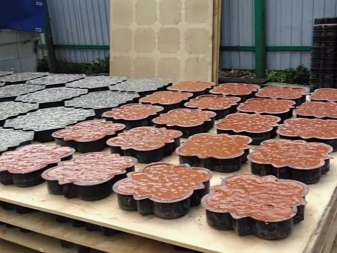
The composition of the mixture
A mortar for paving slabs, for example, for concrete paths in the country, can be composed of a variety of components: it can be cement-sand, consist exclusively of cement, do not contain crushed stone, be colored (containing dye). In this case, the solution, in any case, must meet several key requirements, among them:
- resistance to negative environmental influences (for example, to low air temperatures);
- strength and reliability;
- low level of porosity;
- low moisture absorption coefficient;
- aesthetically pleasing appearance.
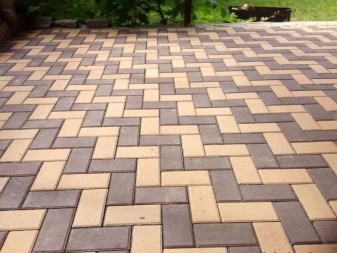
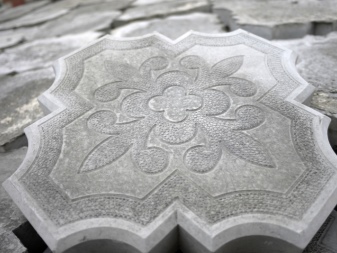
Let's take a closer look at the main elements that are part of the mortar for paving slabs.
- Cement. The basis of any mortar for paving slabs should be cement. Traditionally, experts choose Portland cement M500. In addition, it should be remembered that the composition of the cement should include tricalcium aluminate, but its volume should not exceed 8%. Due to these characteristics, the final solution will be distinguished by high strength indicators.
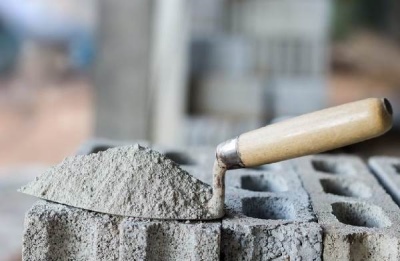
- Sand. It is one of the main components of any paving slab mortar. In fact, this substance is a fine aggregate, therefore, increased quality requirements are imposed on it. Experts recommend giving preference to river sand without debris and impurities. The presence of sand in the solution provides friability.
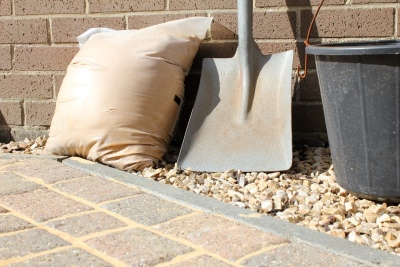
- Seals. They serve as a reinforcing component. Thanks to their use, the level of strength and stability of the finished paving slabs increases. Materials such as gravel, crushed stone or expanded clay are usually used as compactors.
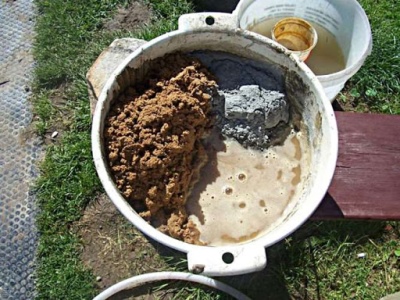
- Hardeners. Thanks to the use of hardeners, the speed of concrete hardening significantly increases (while the products do not crack during drying). In this regard, solutions with hardeners can be used at any time of the year (both summer and winter). It should also be noted that the use of hardeners increases the speed of work. This is especially true if you are making a large number of paving slabs.
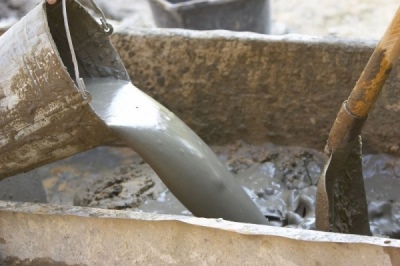
- Dyes. Depending on your wishes and needs in the production of paving slabs, dyes can be added to the solution (or you can do without them). With regard to the choice of color, it is recommended to focus on personal taste preferences, as well as on the general color scheme of the landscape. In this case, the coloring matter must be classified as inorganic oxides. Most often, these dyes are produced and sold as dry powders. When using the dye, it is very important to distribute it evenly throughout the mixture - this is usually done with a concrete mixer. The ratio of the dye to the total mass of the solution depends on the required color intensity; on average, up to 8% of the dye powder is used.
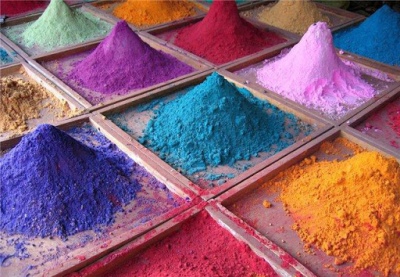
Helpful advice. The final color of the solution is influenced not only by the dye used, but also by the brand of cement.Accordingly, in the process of producing paving slabs of the same batch, it is important to take care of using the same brand of cement.
- Crushed stone. When making mortar for paving slabs, crushed stone and sand must be used in the same ratio. Thanks to this, the tile will not collapse during freezing and thawing (which is especially important for regions where temperatures change frequently). As for the distinctive characteristics of the crushed stone used, they must correspond to the following indicators: size - from 5 to 10 mm, frost resistance - from 1,000, no impurities.
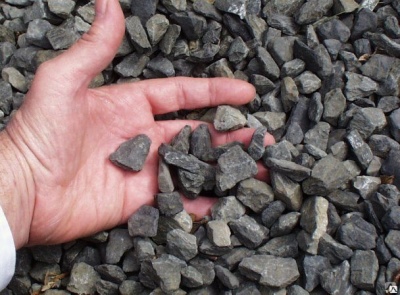
- Plasticizers. These components have a positive effect on the plasticity of the finished composition (hence the name of the elements). Plasticizers provide a high level and reliability of adhesion of particles to each other. As plasticizers, you can use polyvinyl chloride glue, hydrated lime, detergents. Among other things, these components increase the water repellency of the products.
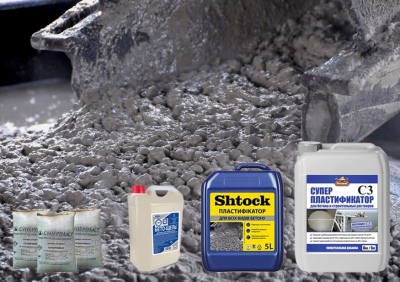
- Water. When adding water to it, it is very important to observe the optimal proportions. This is due to the fact that an excessive amount of moisture will make the solution liquid, and accordingly, will reduce the quality of the finished tile.
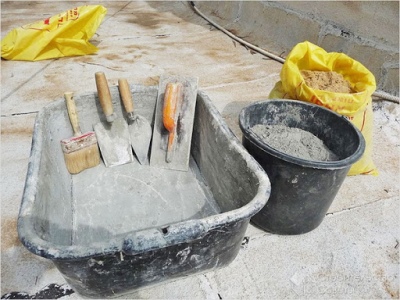
Proportions
In addition to the need to use a certain set of components when preparing a mortar for paving slabs, you must also observe the necessary proportions and ratios of sand, cement and all other elements.
Helpful advice: Despite the fact that there are universal rules regarding the proportions of the components of the composition for paving slabs, individual nuances must also be taken into account. For example, paving and grouting compounds can differ significantly from each other.
It should be noted that the independent calculation of the required ratio of components is a rather complicated and complex task. At the same time, ideal proportions can be achieved only by experience and taking into account all the mistakes made earlier. Therefore, if you are not a competent builder and do not have a sufficient amount of knowledge, skills and abilities, then you should clearly follow the advice and recommendations of specialists.
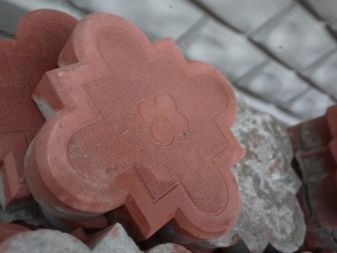
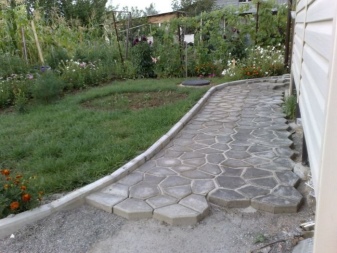
Remember that even small inaccuracies can result in a mixture that will eventually be unusable. In addition, it should be borne in mind that the number of components also depends on their quality. If we talk about traditional proportions, then they look like this:
- 23 parts of cement in buckets;
- 20 parts of sand from the sifting;
- 57 pieces of crushed stone;
- plasticizer, which should be 0.5 parts of the cement used;
- 40 parts of warm water (the calculation is based on the amount of dry components);
- strengthening mixture additives in the amount of 90 g per 1 m 2
- pigment in the amount of 700 ml per 1 m 2.
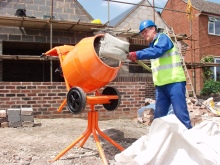
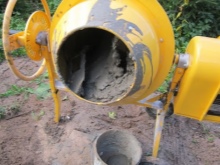
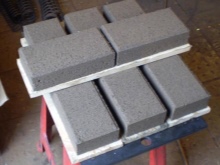
In addition, there are several universal rules:
- sand and cement in the solution should be present in a ratio of 3 to 1;
- add water until a stretchy and viscous consistency is formed;
- if you want to make a two-layer type tile, all components should be used in a 1 to 1 ratio.
It should be remembered that the observance of proportions is as important as the observance of the composition. Only if all technological standards are met, you will receive the desired material, which will be of high quality and long service life.
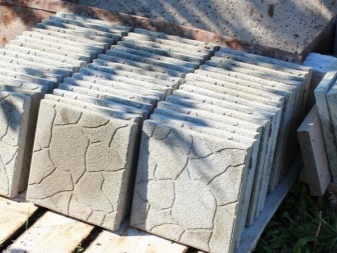

How to cook with your own hands?
Preparation of mortar for paving slabs can be done independently at home. In this case, it is very important to follow the recipe and mix the pouring solution correctly. You will receive solid paving slabs, which in their qualities, properties and characteristics will not be inferior to factory products. Consider a detailed instruction on how to prepare a solution for paving slabs with your own hands:
- first you need to mix 2 main components of the solution: sand and cement;
- further, to create a homemade solution, you need to add a plasticizer;
- the next step is to add crushed stone;
- now you can add liquid (while it is worth remembering that in the end the solution should be of an ideal thick consistency).
After the completion of the mixing process of the components, you can start pouring the solution into pre-prepared molds for paving slabs. The molds must be placed on a special vibrating table (and they must also be greased with oil with a brush). The vibrating table is intended for compacting the mixture in the form. The next step is the drying procedure, which can take up to 48 hours at temperatures ranging from 15 to 25 ° C.
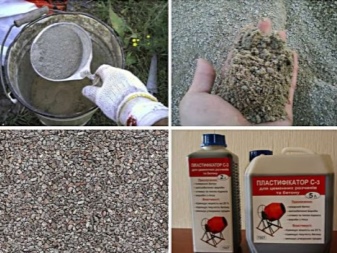
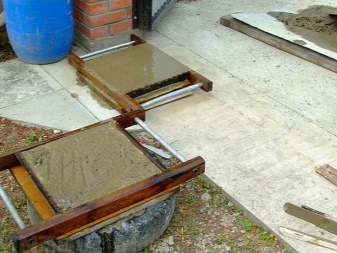
Possible problems
If you knead the composition properly, you will get the desired result in the form of a building material that will fulfill its functional purpose 100% and will last a long time. It is always worth remembering that the process of preparing a solution for paving slabs can be accompanied by various difficulties. Most often, problems arise due to the fact that you did not follow the algorithm of actions, did not use all the necessary components, or took them in inappropriate proportions. Let's consider the most common problems that a user may encounter while preparing a solution.
- Chipping off paint. It is very important to stir the paint evenly. If this rule is not followed, then the dye can be distributed in layers, respectively, the necessary marble effect will disappear. This problem very often arises if the exposure of the molds with the solution on the vibrating table was longer than necessary.
- Difficulties in the process of separating the finished tile from the mold. This is due to the fact that in the manufacture of building material, you used an insufficient amount (or did not use at all) the lubricant.
- The presence of bubbles and voids in the finished tile. Such defects in the finished material are usually associated with insufficient exposure of the composition to the vibrating table. In addition, excessive lubrication can result in bubbles and voids.
- Crumbling tiles. If the tile is crumbling, then there is a high probability that you did not observe all the necessary proportions when preparing the solution.
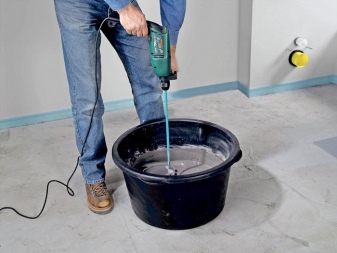
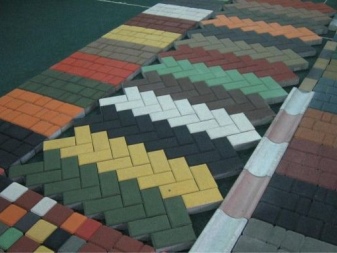
The proportions and composition of the mortar for paving slabs, see the video below.
The comment was sent successfully.