All about large paving slabs
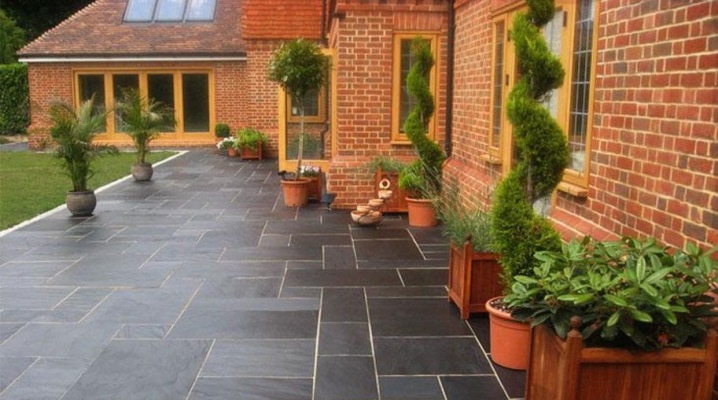
One of the most popular and frequently used materials for the improvement of the local area, park paths, alleys and even sections of highways is currently large paving slabs. You shouldn't be surprised at this - our ancestors began to manufacture and use its similarity 6000 years ago for the same purposes. Of course, those tiles could hardly compete with modern specimens in terms of a variety of shapes and colors, but as far as durability and strength are concerned, ancient tiles were unmatched.
Many good words can be said about modern large-format paving slabs. It is made from quality raw materials using innovative technologies and new equipment.



Peculiarities
The wide scope of application of large paving slabs is due to a number of features and advantages. It has the following positive characteristics:
- high strength;
- durability;
- made from quality raw materials;
- economical in consumption;
- when laying in accordance with all the rules and regulations, the number of seams is insignificant, and those that exist are hardly noticeable;
- a wide range of sizes and colors;
- styling does not take much time.
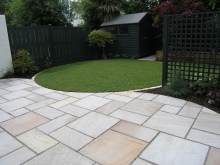


The material also has one drawback - it is difficult to lay out a patterned pattern from large-sized products.
As for the size of such paving slabs, it is precisely because of their variety that it can be used for the improvement of both large and small areas. Today, the most "popular" in the construction process are the following dimensions of these products: 500x500, 600x300 and 1000x1000 mm.
The largest tiles are also called road slabs, as they are used for paving roads. Products 60x60 or 60x80 cm are most often used for laying in the local area or in the country.



Species overview
The modern construction market offers a varied assortment of large-sized tiles, which are classified by material of manufacture and shape.
Large slabs are:
- concrete;
- clinker;
- plastic;
- stone;
- rubber.
Below is a brief description of each variety.

Concrete
These tiles are considered to be the most used. They are characterized by high durability and reliability. Most often they are gray, but if you make an individual order, the manufacturer can add a coloring pigment to the material of manufacture. Concrete paving slabs are vibrocast and vibropressed.
The first is used for paving, for example, garden paths, while the second, which is highly resistant to mechanical stress, is used for highways and parking lots.

Clinker
Clinker is clay that is fired at a very high temperature. Such a tile is durable, frost-resistant, repels moisture, does not fade and does not slip. Comes in different sizes and colors.


Plastic (polymer sand)
The components of such a product are sand, polymer chips and coloring pigment. Since the design of the product is very diverse, it is often used for paving adjacent areas. This type of large-sized paving slabs is one of the cheapest.
However, the longevity and breadth of territorial distribution is very limited - it does not withstand severe frosts or heat.

Stone
Natural stone is a very expensive material, so tiles made from such raw materials will have a high cost.It is because of the high price that these products are not used for paving large areas. Most often, they are laid out sidewalks, paths. They have excellent physical and technical parameters and are made of granite, basalt, marble and labradorite.


Rubber
Such tiles are made from recycled rubber, they are completely safe, so they are mainly installed in playgrounds. In the process of manufacturing products, all kinds of dyes are added to the raw materials, so that the color of the finished tile can be whatever you want.

As for the shape, the products in question can be either square or rectangular.
Styling tips
The wear resistance and durability of large-sized paving slabs depend in most cases on adherence to the laying technology. Observing the rules and following the instructions, you can make a device with your own hands, for example, paths or an adjoining area from a large tile, no worse than professionals. Only time from habit it will take, of course, more.
The installation process is divided into several stages.
- Preparing the styling area. The site is completely cleared of weeds, debris and leveled.
- Marking the territory taking into account the slope.
- Material preparation. In addition to tiles, you will need the following materials and tools: sand, cement, level, lace, trowel, mallet, rammer. And it is also desirable to have a grinder on the construction site, with the help of which it will be possible to cut the product, if necessary.
- Installation of curbs, if such work is planned.
- Preparation of the base - a cement-sand cushion is poured.
- Laying tiles.
- Grouting.


After completing the installation work, it is advisable to fill the area with water. So the products will stick well in place, and all the excess grout will go into the cracks.
Before proceeding with the installation, you need to draw up a work plan, organize a place, and, if necessary, purchase missing material and tools. Besides, it is important to correctly calculate the required number of paving slabs. To do this, you need to calculate the working area and select the material, knowing exactly its dimensions. Next, using a simple arithmetic formula, count the number of tiles.


The comment was sent successfully.