How to make a vise with your own hands?
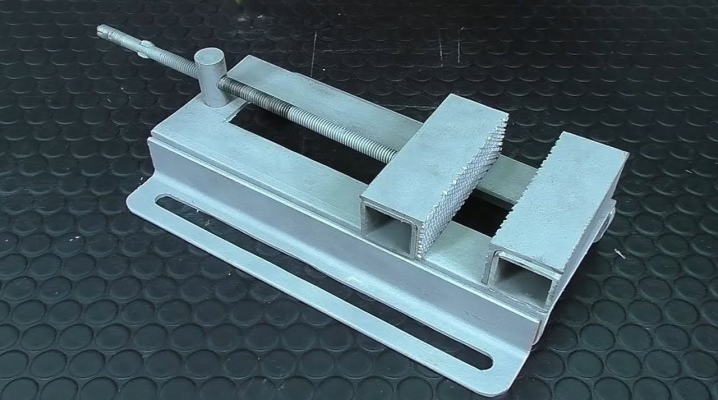
A standard vise may not be suitable for a craftsman for a variety of reasons. And buying a large number of tools is not only financially unprofitable - they will take up a lot of space in the workshop. Making a vice with your own hands is an ideal solution to this problem. All that is needed for implementation is a little patience and careful following the instructions. At home, you can make any type of vise with minimal investment in time and money, many parts can be removed from those models that are out of order.


Device and principle of operation
Large joinery vice have several advantages over other designs. They can be mounted either on a workbench or on any suitable support in the workshop. It is also easy to remove them from the surface at the end of the work. So, despite the size, the tool does not take up too much space, and you can work even with large parts.
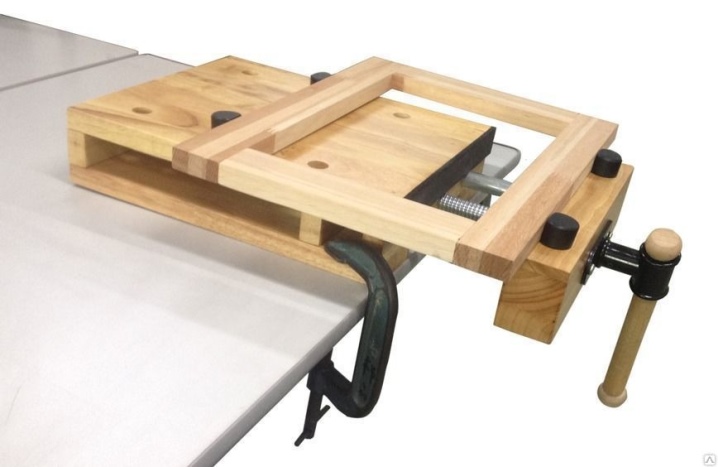
It includes more than just a handle, tripod and anchoring leg. The design of any vise includes:
- support with all stationary parts;
- a movable jaw designed to fix the material to be processed in one position;
- wings that move the part during processing;
- lead screw;
- gate that transmits torque to the screw.

Support fastened to a workbench or stand with screws or bolts. Planks on many factory models, the jaws can be changed depending on the level of wear, but this possibility increases the price of the vice several times.
For home-made such strips, it is recommended to use cast iron or polymer steel. In addition to the versatility of the strap, it is possible to keep other parts of the vice from deformation during their active operation.


Also bench vise includes a spring, with which you can work with truly dimensional parts. Lead screw holds it in place with ease. If it is not in the design, then the master will have to bend over to hold the spring with his own weight, which greatly complicates the work. It is best to navigate the manufacturing process on the drawing of the selected model in order to avoid mistakes.

What can be made of?
The number of materials from which you can make a homemade vise for work is practically limited only by the user's imagination. It is customary to make the main parts for a vice made of metal, it is much more reliable than all other materials. Best suited for this purpose steel and cast iron... They do not rust longer and are much more resistant to negative environmental influences. Cast iron from those types of metals that can serve the owner for several decades.
If we talk not only about the material, but also about the base for the vice, then they are usually made from a number of household items:
- from car blocks;
- from round pipes;
- from the corner;
- from the rails;
- from a profile pipe.
On average, the service life of a factory vice with active operation is a little more than a year. The cause of failure is often the breakage of the paw of the sponges, sometimes the wear increases due to the poor quality of the material itself.


A vise is necessary for working with workpieces, when they need to be fixed in one place. If they are urgently needed, they can be quickly made even from wood. For crafting, you need nails, wood and an ax.If the design is planned to be complex, it will not be superfluous and ripsaw in the general list of instruments.
The tree is sawn almost at right angles, the stationary part, called in different ways a sponge or heel, is attached to the structure with nails driven obliquely. The angle is important so that the nails do not bend when working with the vice.

The movable jaw should slide freely on the bed. A clamp is also needed, usually a hewn sharp branch. But the sharpness must be controlled, otherwise the vice will not hold the part and the entire structure as a whole, if, on the contrary, the sharpness is not enough. This design is reliable during operation and is relatively simple: to remove the workpiece from the vice, it is enough to knock out the wedge.
In technology and in everyday life, clamps are used for a number of different purposes, so before you say anything about the characteristics and differences with factory models, it is worth determining what type of vise you need to make.
Not every design can be reproduced at home, for some things professional equipment is required and certain skills.

Therefore, the next question worth paying attention to is: what do you need to make a vise with your own hands?
What do you need?
The secret of making any budget tool at home is quality training.
Materials required include:
- corner 50 by 50 mm;
- channel up to 0.5 m, steel;
- M6 bolts, nuts, washers, engraver on average up to 18 pieces;
- threaded screw (sometimes screws from old vices are used);
- metal sheet up to 5 mm;
- thick metal up to 10 mm and more;
- 1-2 cans of paint;
- a nut suitable for the thread of the selected screw;
- steel bar under the handle.

Next, you should collect all the necessary instruments for work. These include:
- welding machine;
- drill;
- Bulgarian;
- brush;
- sandpaper;
- wrench;
- construction compasses;
- metal ruler;
- steel file;
- the marker of the most vivid color.


Manufacturing steps
In the manufacturing process, you need to take into account many different little things. Different models will require their own algorithm of actions. For example, in order to make a hydraulic vise with your own hands, among other tools, you will need to use a plasma machine. In addition, in this case, the main thing in the design is the hydraulic steam from the pump and cylinder. Sheet steel with a thickness of 10 mm or more is used as the main material. Before starting work, the wizard will need:
- sheet steel from 10 mm;
- hydraulic cylinder;
- pump;
- hose;
- springs;
- bolts;
- overlays;
- channel.

If we talk about tools, then you will need:
- drill;
- welding machine;
- Bulgarian;
- clamps;
- belt sander;
- thread marks;
- pendulum machine.


The home making process can be divided into several stages. One of the main ones will be creating a base plate, in other sources the craftsmen also call it the basis for the vice. A piece of a certain size is cut from a sheet of steel using a plasma cutter or similar tool. Further several holes are created to secure the plate in one position. Drill marks can be set independently using a marker. The parts are fastened together by welding.

Then you can equip the inside of the vice, where the movable jaw is attached in the future. Here you will need a channel prepared earlier. To him plates and all other parts are attached by welding.
In order not to be mistaken with the size, you can use a drawing or sketch, where all the main parameters are indicated. It is in the inner part that the hydraulic cylinder is subsequently installed. All seams must be reliably ground so that the vice does not jam during operation.

After arranging the interior, you can proceed to outwardwhere is installed fixed lip. Several pieces of sheet steel should be cut off and welded to all other parts. To avoid mistakes, it is recommended to do this directly above the moving part.
As a stop for the hydraulic pump behind the structure, the back is welded. The use of steel in this case is quite justified, since it must be strong enough to withstand pressure. At the final stage the inner movable part must be sanded using a grinder and sandpaper. The final surface should be perfectly smooth, after which all parts can be welded together.

Next comes installation stage of the hydraulic cylinder. On the one hand, it is supported by the edge of the stationary part of the vice, on the other, it actively works with the movable one. As soon as the cylinder is extended, the vice is closed. A spring must be provided in the structure to return the vise to the open position. The pressure is then dropped to zero.
The lips of the vise are made of the most durable material, since they are the ones who experience the bulk of the load. Sheet steel and welding must be of good quality, seams smooth and polished. Holes for the installation of the lips are usually drilled in advance. They are fastened with screws or self-tapping screws.

Details are additionally coated with paint not only for aesthetic reasons, but also so that the metal is not exposed to rust for a longer time. The weight of the final work will be about 30 kilograms, usually they are desktop and take up a minimum of space in the garage or workshop.

Another tool option is quick-clamping vice with eccentric clamping. It is much easier to work with them due to the fact that you do not need to constantly adjust to the size of the part, you just need to fix it in the center. Many steel parts are used as material, such as pre-sized corners, nut, washer and bed. Also in this kit you will need a shock-absorbing drain, a channel, a rubber bushing and an eccentric itself.

The channel is cut, and the workpiece is marked for future vice. After the centers are marked and the workpiece is oiled, several entry holes are drilled for the stem. The stem is inserted there, one of the corners, the length of which should be at least 230 mm, is cut in half.

After that, the workpieces are cooked together in the shape of the channel and cleaned with a disk. Further, the workpieces are welded together, fastened with a vice and a bed. Movable and fixed jaws are installed at the final stage and fastened with nuts. Eccentric installed in the middle on the workpiece, after that you need to check the quality of the grip and finally weld all the seams.
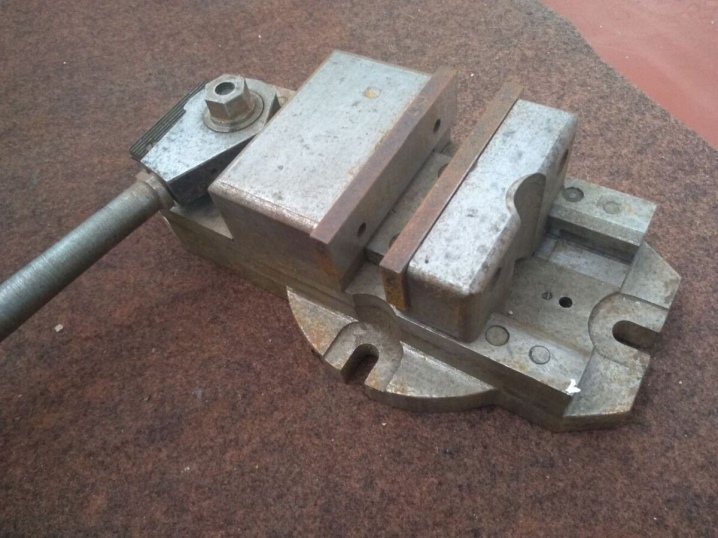
Locksmiths
Ball vise without screw clamp - usually a locksmith's tool, which is made from a channel and steel. An important part in the design is also the lead screw, one of the steel plates stands strictly in the middle, splitting the structure into two parts. The steel base and corners are welded to each other, the seams must be cleaned. Sometimes bolts and nuts are used for the connection. Holes can be marked with a marker. Jaws and a rod are placed at the very end, a lever is attached to control the vice. Such a vice can be used for leather or wood, they will withstand the required level of stress.

Machine tools
The swivel vise will require lengthy metal work. Best suited for these purposes stainless steel... The vice is held on the structure with a clamp, they are attached directly to the workbench. The guide pieces are mounted on several steel plates, holes in which are drilled in advance. Along the edges of the plates, smooth pins should be provided for the smooth installation of the guides, on which the clamping jaws will be. A control lever is installed on one side of the screw pin.

The sponge is screwed onto the bolts, the nuts are always located on the outside, so that, if necessary, it is possible to disassemble the structure. The jaw holder is welded and bolted at one end, just like the jaw itself. This will enable the master to change them when the need arises. The workpiece hinge is also secured by welding, pin and nuts.

Carpentry
Make a simple carpentry vice from become or cast iron for the house you can do it yourself, just pick up a drawing and all the necessary components. For the sake of simplicity, the clamping jaws can be made of wood, and the metal is fixed in place of the workbench, which will serve as a support for the tool.
Important! The key in this design will be a clamping screw with a diameter of up to 20 mm, depending on this parameter, the purpose of the vise also changes. The larger the diameter, the larger the details the master will be able to work with using a home vise.

The wings will be made of steel or cast iron with a thickness of 10 mm or more. Another important detail is crank, with which you can control the vice. Any steel strip is suitable for this. The dimensions must be perfectly matched to each other for the most snug fit of the parts. The longer the crank, the more force is applied when working with the workpiece.

If nothing suitable was found at hand, it may come up and wrench, a threaded screw is pressed into its connector. And in this case, there is no risk of making a mistake with the size, you can choose the right one quickly, focusing only on visual coincidence. A classic option is a rod wrench, with the help of a special hole, free sliding in the screw thread is ensured. This makes it much easier for a beginner to work with a vice.
You can make a device for a workbench - a movable and fixed jaw - from wooden blocks. Pine is best suited because of its strength and softness in processing. Next, three holes are drilled for the remaining parts, the markings can be made with nails, they can be easily removed at the end of this stage.

After that, the installation of the vice begins directly. This can be done without welding using nuts and other fasteners, the thread is always pre-planned in order not to make a mistake with the size. First, a fixed jaw, wings and a screw are installed. A movable jaw is installed on the edge of the front surface and secured with several nuts for structural reliability. The collar is installed last after fixing all other elements. The principle of operation of such a vice is simple: as soon as the knob turns, the screw enters the nut and attracts the movable jaw, changing position. They can be made without a lathe and other complex equipment.

Pipe
Disassembled pipe vices are quite simple, they can be made from almost any available materials. They can easily grip metal and cylindrical parts. For manufacturing, you will need several parts of the profile, pipe sections and a sheet of metal with a minimum thickness of 10 mm. The design will definitely need to provide a screw.
The first stage is considered to be the manufacture of the body, for this a number of parts of equal parameters are cut off from the pipes and profile. After that, all the parts are connected together using through holes and fasteners. The frame with the base is welded, the seams are cleaned as carefully as possible. After that, you can safely use a homemade pipe vise!

Recommendations
The first thing to consider: dimensions of the future instrument. They can be divided into several main categories.
- Small size - length is from 290 mm, height - from 140 mm. Jaws up to 50 mm high. The total weight is 8 kg.
- The average size - length up to 372, height - up to 180 mm, jaws - up to 70 mm inclusive. The total weight is up to 14 kg.
- Big size - length is 458 mm, height up to - 220 mm, jaws - up to 90 mm.The total weight, depending on the complexity of the design, is up to 30 kg inclusive.
These are only average parameters in size, which can be guided by when making your own.
Some models on the market can significantly exceed the weight of 30 kg, a lot will also depend on the material chosen. Cast iron, for example, is much heavier than certain types of steel or wood. Each master will have to choose the material and calculate the dimensions for future grips individually.


Another important parameter to pay attention to is clamping force... The higher this parameter, the more forces will be required to process the workpiece. If the clamping force is insufficient, this can lead to tool breakage during operation, not to mention the fact that the workpiece itself will be damaged.

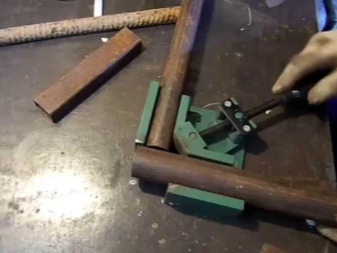
If the master plans to make a rotary vise, then very it is important to understand the key design features of the mechanism itself. In addition to the movable and fixed jaw, this includes the shank. In this case, it is recommended to select the standard width of the jaws: 80 and 140 millimeters. Depending on the design of the clamping mechanism, the vice can be different. For self-production, models with a mechanical clamp are especially popular. They can be divided into specific types.
- Screw where the lead screw - the main part of the structure, controlled by a handle or a lever from the outside.


- Keyless - there is also a lead screw, but it passes through the part and during operation can move freely without unnecessary friction and rotation.


- Quick release - here the screw is not provided in the design, it is replaced by a mechanism with a small lever to change the position of the jaws.

- Eccentric - the main thing is an eccentric mechanism with a control handle. If it is not there, then you will need to clamp the eccentric.

Knowing these features, it will be much easier to choose a suitable design and assemble a vice with your own hands. It is worth focusing not only on the weight or complexity of the structure, but also on the practical purpose of the tool... Most often, it is the locksmith's vice that is used for the home workshop because of their versatility.
Next, watch a video on how to make a vice from an old jack with your own hands.
The comment was sent successfully.