What is the best polycarbonate for a greenhouse?
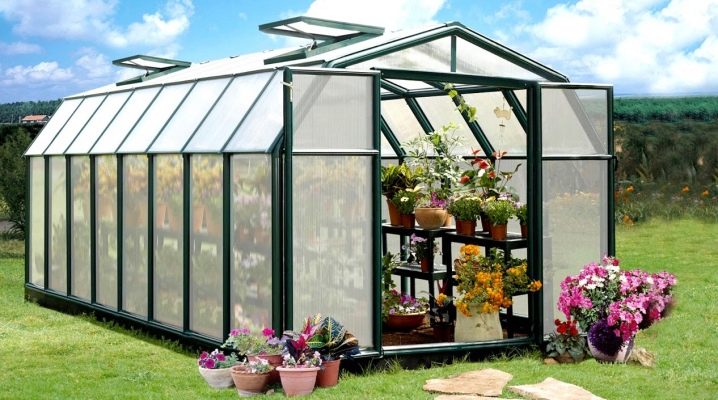
For the arrangement of greenhouses, manufacturers offer the consumer a variety of materials. Along with the traditional raw materials for the installation of the frame, such as glass or film, there are materials of the latest generation that have proven themselves perfectly in practice. This product is polycarbonate, which has been widely used in recent years.
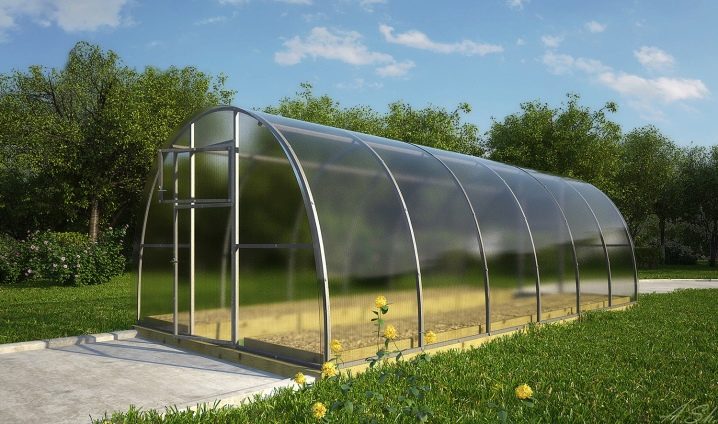
Features and types
Most gardeners and gardeners no longer wonder what material to purchase as a covering raw material for greenhouses and greenhouses, since polycarbonate is preferred. But sometimes the buyer is faced with a choice regarding the type of material, since these products are presented in a large variety on supermarket shelves. The task of the buyer is to purchase the best option based on the cost and quality of the product.
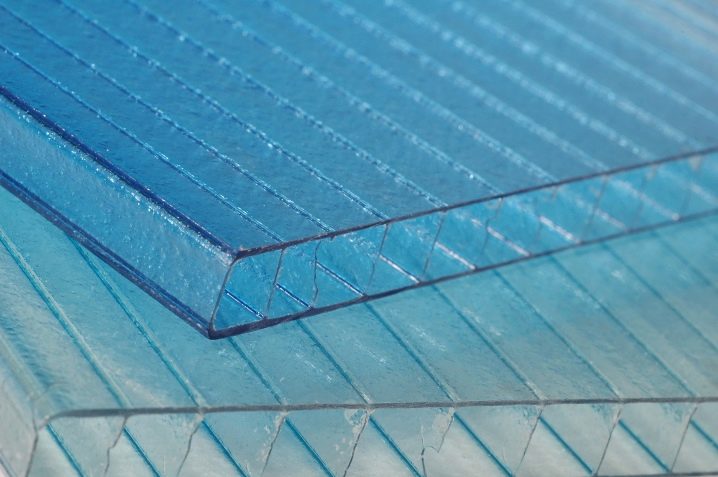
Polycarbonate is a plastic made from polymers.
As the positive features of raw materials, one can single out:
- minimum weight and ease of installation;
- flexibility and strength;
- environmental friendliness;
- resistance to temperature fluctuations and excellent thermal insulation properties.
The combination of the above qualities was the reason why the material has become very popular and in demand in many areas of activity, including the shelter of greenhouses.
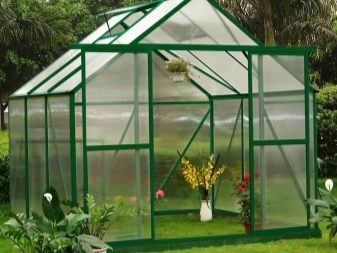
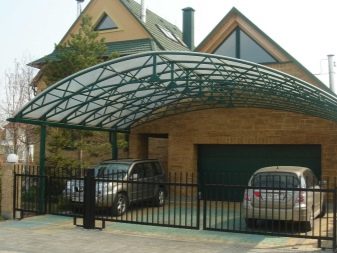
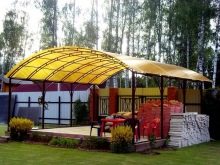
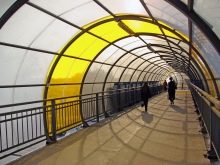

By their structure, raw materials are classified into two types:
- monolithic products;
- cellular polycarbonate.
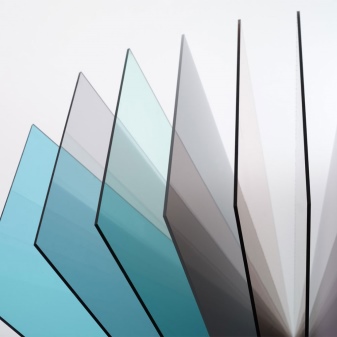
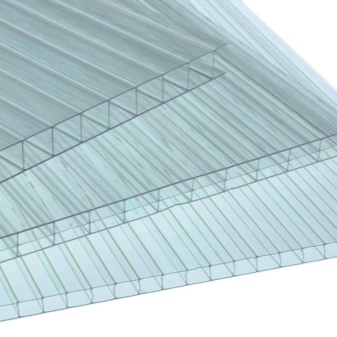
Based on the name of the first type of material, it can be noted that it only comes in the form of solid sheets, with different thicknesses and sizes of the product. And thanks to the heat treatment of raw materials, the required configuration can be set, which is very important for the construction of multi-level structures.
A distinctive advantage of a monolithic material is its strength, which is several times higher than that of cellular products. That allows it to be used for construction purposes without additional assembly of the frame. The color of monolithic polycarbonate varies from colorless sheets to materials of all kinds of shades. As a covering raw material for greenhouses, it is not used so often, since it has a rather high cost.
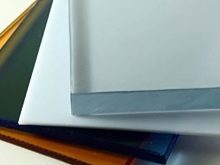
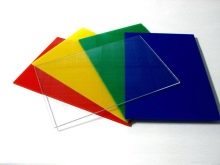
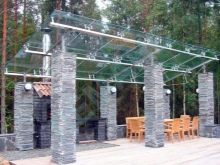
The correct solution for arranging polycarbonate greenhouses will be cellular material, which has a number of positive qualities. It is very important to carefully understand the presented assortment of these raw materials, since the functionality of the entire structure and its operational life will directly depend on the choice made in favor of one or another type of polycarbonate.
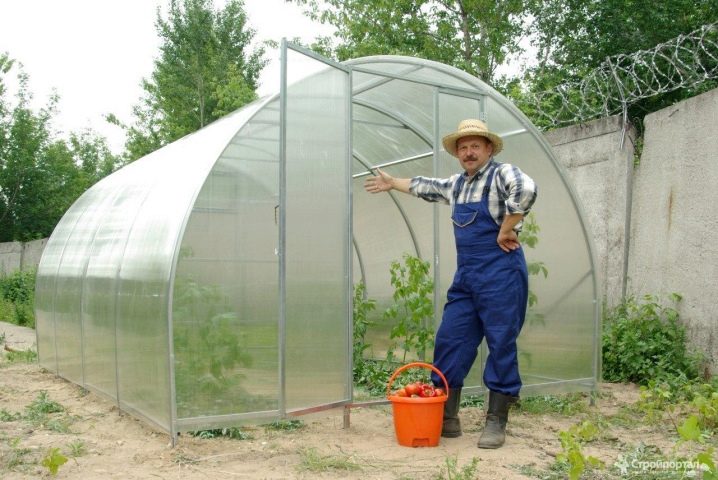
Benefits of the honeycomb structure
The material has many advantages over other greenhouse products:
- excellent light transmittance of raw materials;
- light weight;
- the presence of a coating that protects plants from ultraviolet radiation;
- an air layer in the cells favors heat protection;
- low cost in contrast to the monolithic type;
- long service life;
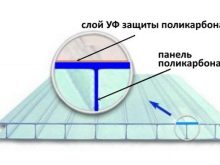
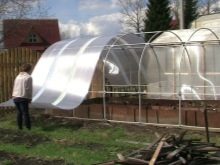
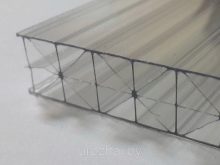
- resistance to various temperatures;
- does not conduct electricity;
- not subject to corrosion and decay;
- good plasticity and thermoplasticity of products;
- recyclable.
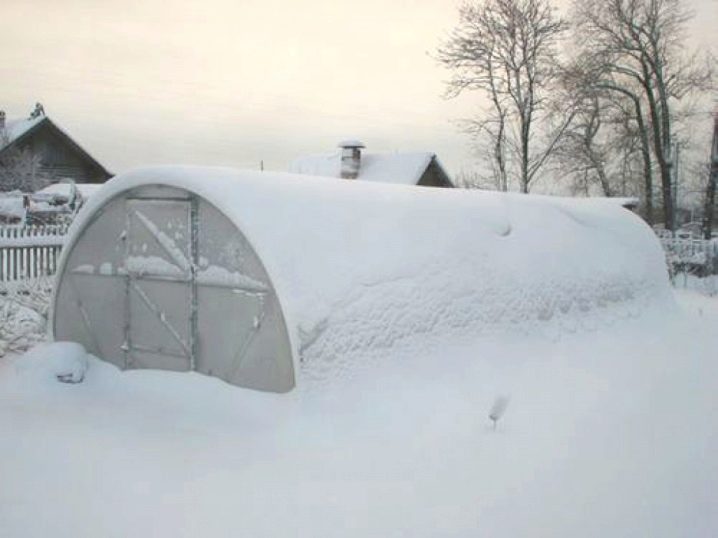
The disadvantages of products include low resistance to exposure to abrasive substances on the surface and cyclical expansion due to temperature changes.
There are lightweight types of cellular polycarbonate, which are distinguished by thinner partitions on the inside. The cost of such material makes it possible to save on the purchase of construction goods.
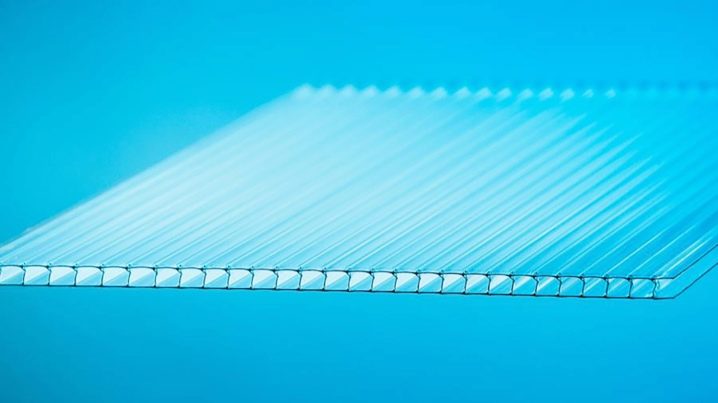
Characteristics and parameters
First of all, polycarbonate stands out for its strength when compared with other covering materials for greenhouses, for example, with glass or plastic wrap. The temperature range at which it does not lose its properties is: from + 120C to -40C. Cellular polycarbonate in its structure is of the following types: 2R, 3R, 3RX, 5RX, 6RS.
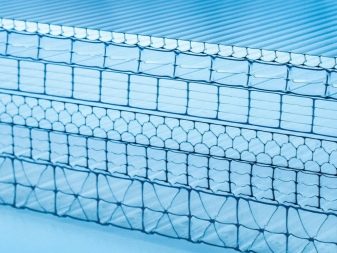
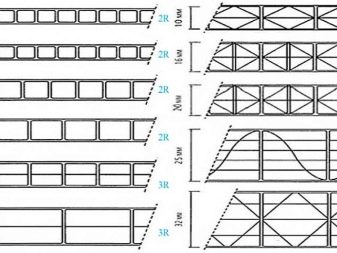
Honeycomb shape
An indicator such as density is a very significant parameter for a material. It depends on the shape of the voids in the cellular polycarbonate sheet. The highest rate is observed for material with triangular and hexagonal cells. This feature provides the product with good resistance to strong gusts of wind, but the flexibility of the product is reduced.
Rectangular honeycomb is present in a more budget type of polycarbonate, it is characterized by excellent flexibility.
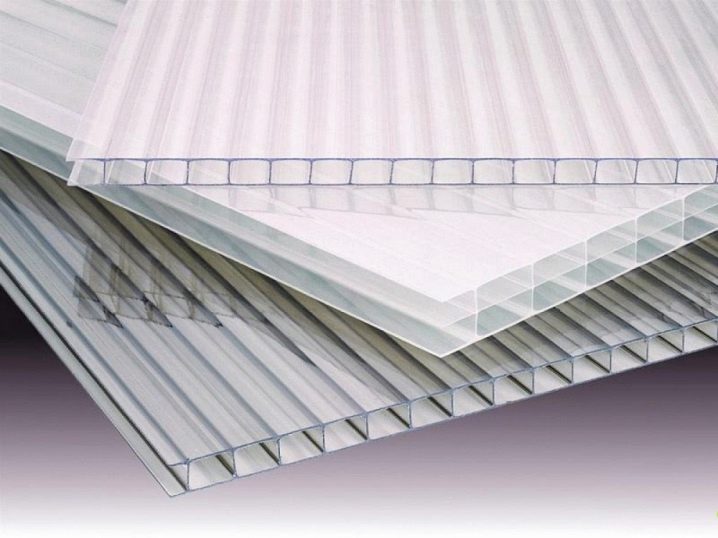
Thickness
Manufacturers offer products with the following thickness: 4, 6, 8, 10, 16 mm or lighter products, this parameter for which is 3-3.5 mm.
Sheets with a thickness of 20 to 32 mm are produced on an individual order, used for structures where a special level of coating strength is important.
To equip a private greenhouse, experts advise you to opt for the optimum material thickness for such buildings.of 4 mm. This indicator will allow the greenhouse to effectively cope with its functional tasks for about 3-4 years. Thick panels for greenhouses should not be used, since they will reduce the light transmittance and thermal conductivity of the product, at the same time, there will be a need to equip a reinforced frame.
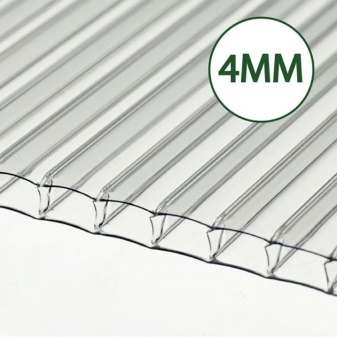
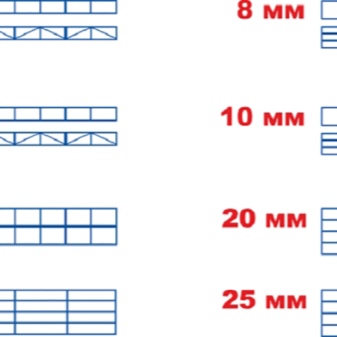
For climates with harsh weather conditions, 6 mm thick raw materials should be purchased. Such sheets will not deteriorate even from hail and strong winds.
Sheets with a thickness of 16 mm showed themselves better when performing vertical walls of swimming pools or other sports buildings.
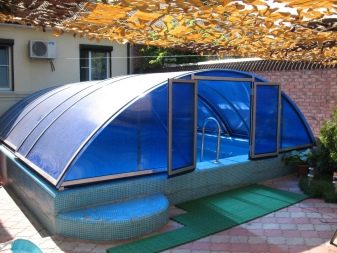
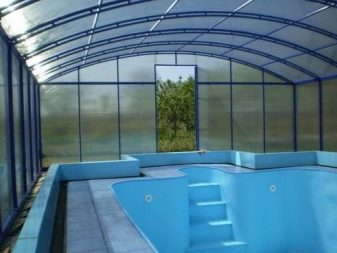
Sheet size
When building a greenhouse, it is necessary to take into account a number of mandatory factors, based on which a given amount of materials will be purchased. Purpose of the structure: the greenhouse will be used only in spring or in winter, too, its size, load on the walls, and so on. As for the dimensions of a sheet of cellular polycarbonate, there are uniform standards regarding these parameters, both from domestic and foreign manufacturers, regardless of the selected thickness.
The size of the sheet should be 2.1x6 m or 2.1x12 m.
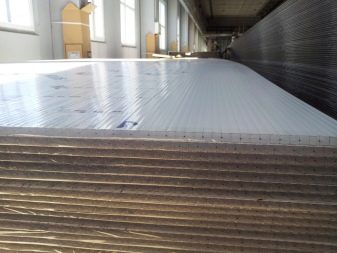
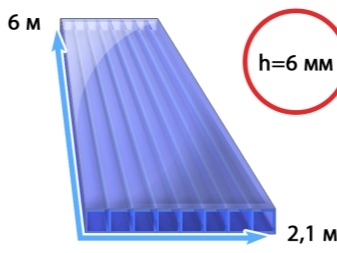
Monolithic polycarbonate is manufactured in dimensions: width 2.05 m, length 3.05 m.
Consumption is largely determined based on the rational cutting of the material.

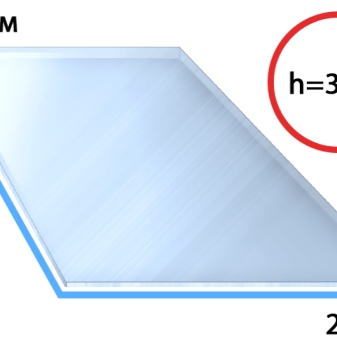
Colour
Foreign and domestic companies that specialize in the production of cellular polycarbonate offer the consumer completely transparent or colored products. In order to choose the right panel color for the greenhouse, a decision should be made based on certain criteria.
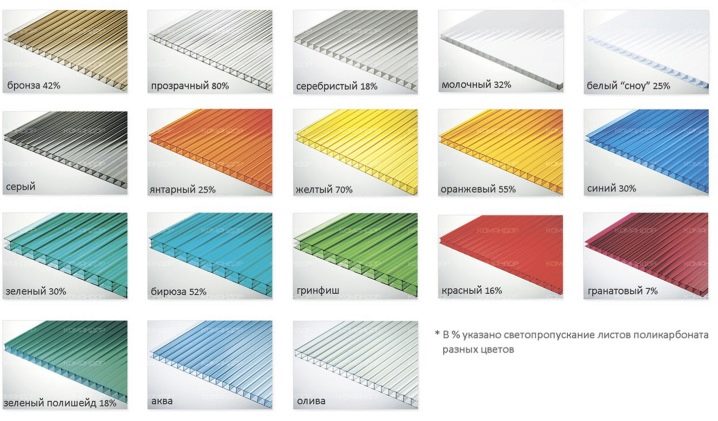
The surface of the building must provide high-quality light transmission for plants, so that the lighting is similar to natural sunlight. Colorless products fully cope with the task. Such products have a value of this parameter at the level of 80%. And, for example, a sheet of cellular polycarbonate of opal color scatters only 40% of the sunlight, a bronze tint - 60%. Such values will negatively affect the growth of plants, since a lack of light will lead to delayed development or death of seedlings.
Therefore, experts advise:
- purchase transparent materials for greenhouses that will provide good indicators of crop yields;
- the choice in favor of the blue or turquoise color of the panels should be abandoned altogether;
- yellow polycarbonate can be chosen for mild climates;
- if artificial lighting is planned for structures, then the covering material can be of any color;
- mushrooms and berries grow beautifully in green, red or brown coated rooms.
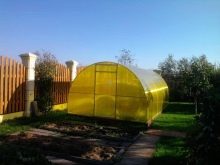
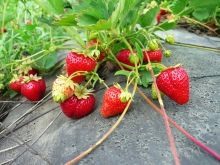
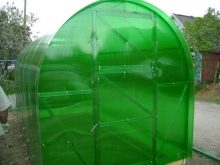
The need for UV protection
During the operation of transparent plastic, the material is exposed to intense ultraviolet radiation, which is fraught with the formation of microcracks on the surface due to the activation of photoelectric destruction processes. However, this is only the first alarm bell, in the future such seemingly imperceptible and frivolous defects increase and spread over the entire area, as a result of which the sheet becomes brittle, and it gradually collapses.
To protect the material from such destructive phenomena, a special protective coating is applied to the top layer of polycarbonate in the process of its manufacture. And the modern technology of coextrusion, which is used in the course of these works, makes it possible to eliminate the risk of gradual separation of the layer from the base.
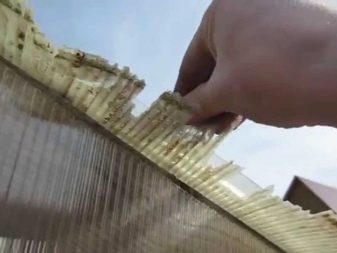
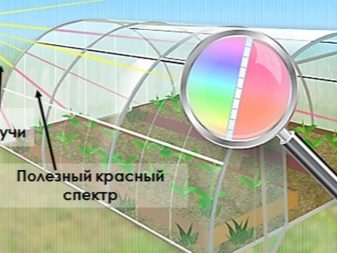
Almost the entire range of cellular polycarbonate has such a coating only on one side. To install the material in the greenhouse on the right side, the manufacturer makes a special mark on the film used for packaging, which will tell you how to lay the product.
There are some products where a stabilizing coating is applied on both sides. These products have a narrow scope: most of them are purchased for the installation of advertising structures or sound-absorbing boards, the installation of which is carried out everywhere along transport routes located near settlements. Such products are not needed for arranging greenhouses, since only one side is in contact with UV radiation during operation.
Today on the market there are panels made of cellular polycarbonate, which do not have a protective layer, and protection is provided due to a special composition that includes an additive that performs this function. On such products, its percentage is indicated, usually it is 30-46%.
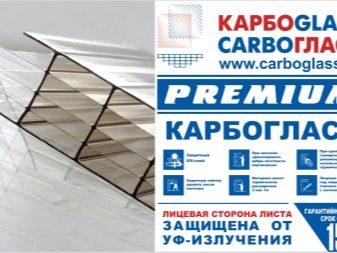
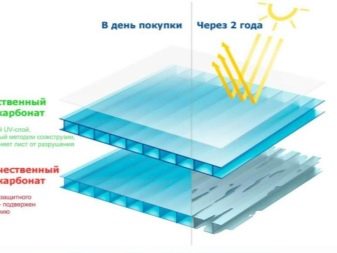
Some manufacturers sell polycarbonate without a protective coating. It can only be used for interior work, which exclude direct contact of the surface with the sun's rays, therefore, it is impossible to use such products for the installation of a greenhouse structure. Having bought such panels of cellular polycarbonate through carelessness, you can expect that the structure will last a maximum of one year. Destructive processes will not keep themselves waiting long, which is fraught with serious expenses related to the acquisition of new covering material.
Therefore, for the construction of greenhouses, polycarbonate will only be suitable with a protective film from ultraviolet radiation from trusted and popular trading companies or manufacturers. Buying items that don't have a manufacturer listed is likely to be a mistake that will hit your budget seriously.
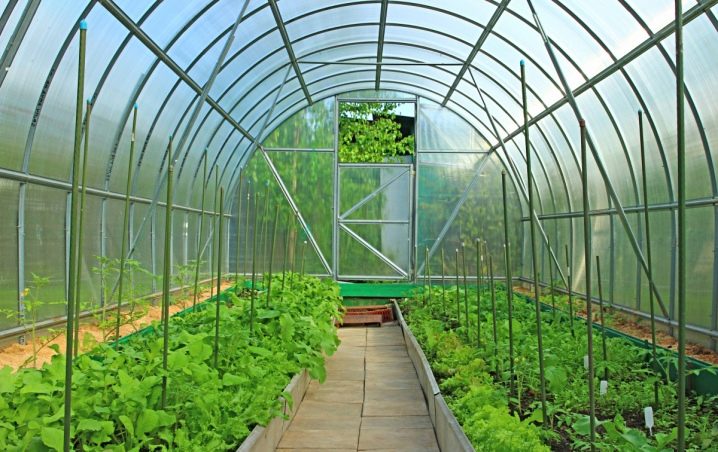
Selection guidelines and reviews
European manufacturers claim that premium polycarbonate material can be successfully used for about 20 years. Consumer reviews indicate that competent and correct operation makes it possible for the sheets to maintain their effectiveness over the specified period. As for domestic products, their average service life varies within 8-10 years. Chinese counterparts fall into disrepair two times faster, since the raw material for their production is recycled material.
Based on this, preference should be given to well-known firmswho monitor the quality of their products, as they value their name in the market. You can distinguish good products from low-quality ones by visual inspection of the packaging: as a rule, verified manufacturers make markings on the front side of the sheet, which contains information about the parameters of the product, including the date of production.
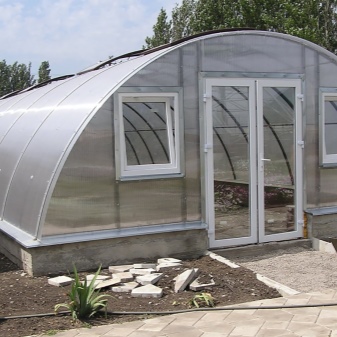
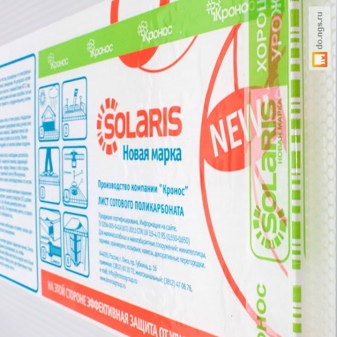
Products on both sides must be wrapped in plastic and free from visual defects and scratches. The surface of the product must be uniform in color, free from bends and free from bubbles. It will not be superfluous to ask for a quality certificate for the material for review, since many unscrupulous firms easily fake well-known logos and apply them to their low-quality products.
However, the service life of products is largely determined by the correct installation and selection of consumables., for example, for lathing. The diameter of the holes for the fasteners must be larger than the bolt itself in order to reduce the risk of cracking the material in these places due to thermal deformations of the surface. It will be useful to additionally use a rubber washer.
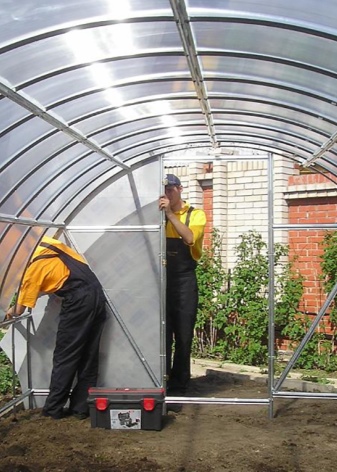
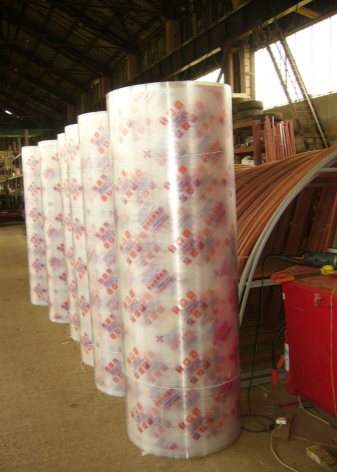
Polycarbonate panels are attached to a special profile. The open ends of the sheet must be closed with a vapor-tight profile, which will provide a moisture-proof function and eliminate the risk of clogging the inside of the sheet with various particles. The lower edge does not need to be equipped with a profile; as a rule, it is left uncovered so that condensation can drain off the surface without obstacles.
Competent installation of the covering material on the structure, in conjunction with the correctly selected material, including thickness, size, color and manufacturer, will serve as a guarantor of a long and productive functioning of the greenhouse. That will ensure a good level of yield and high quality of the product.
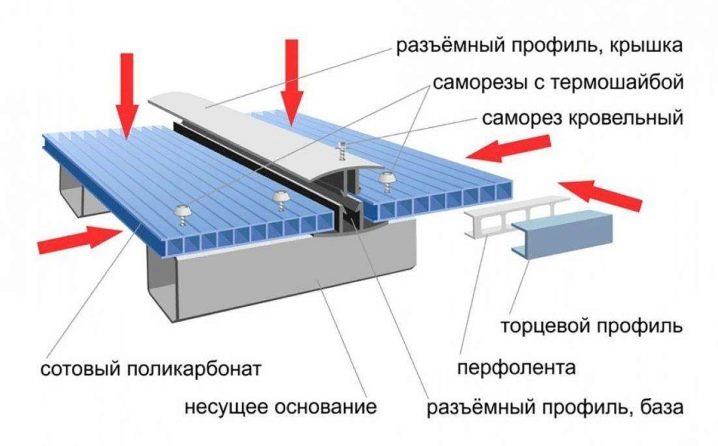
And also a stationary or prefabricated greenhouse structure can be ordered directly from the manufacturer, which will avoid mistakes associated with the installation and purchase of building materials.
For information on how to assemble a polycarbonate greenhouse, see the next video.
The comment was sent successfully.