Types and secrets of choosing carbide drills

A carbide drill can be used to process such high-strength materials as, for example, cast iron, stones - both natural and artificial, as well as work on concrete, on a printed circuit board, brick, non-ferrous metals, all types of plastics. They are called tungsten carbide for a reason, but because plates are soldered onto their cutting parts, for the production of which hard alloys are used. When high-strength materials are drilled with these hard bits, it makes the drilling process twice as efficient as using conventional steel tools.


Description and scope
The hardness of the cutting inserts, soldered to the bit, significantly prolongs its service life, however, this does not mean that such gimbals can be used to work on any surface. For example, When machining steel plates, carbide tips can wear out quickly, even break. To prevent this from happening, working tools must be very rigid.
Otherwise, due to vibration during operation, the carbide inserts will first lose color, and then simply break off the surface of the drill.

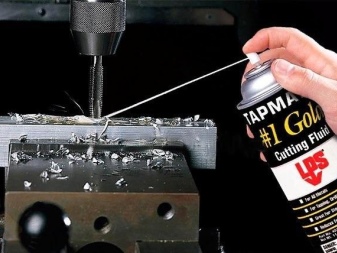
Species overview
To date, the attention of buyers is offered a wide range of gimbals with carbide plates, which can be used to process metal and other materials. These nozzles can be classified according to a number of parameters, for example:
- by the material from which the plates are made;
- by the method of attaching these plates to the working part of the nozzle;
- by the shape of the plates;
- in the shape that the grooves have between the cutting surfaces of the nozzle, these grooves are designed to efficiently evacuate chips and other waste arising from the drilling process.
The tips, equipped with carbide plates, have some design features that distinguish them from other "brethren".

This is, first of all, shorter working part - in comparison with other types of drills, it is less by 20-30%. This is due to the process of regrinding the drill - it can only be done on carbide inserts. If the drill and the jig make up a set, then the length of the drill is equal to the length of a conventional gimbal.
The diameter in the core of the nozzle in the direction of the shank increases every 10 cm from 1.4 to 1.8 mm. The angle at which you hold the bit is in direct proportion to the depth of the hole to be drilled. The shank in the form of a cone must be well adjusted to the spindle in the machine, because how rigid and strong the grip is, depends on how accurate and high-quality the drilling process will be.
In addition, the good clamping of the drill ensures trouble-free operation and no breakages in the process.
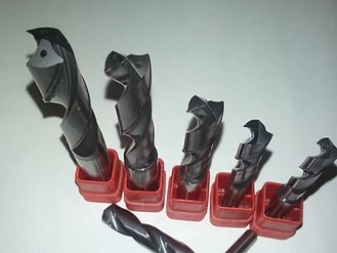

By material of manufacture
If we talk about the materials from which the cutting inserts are made, most often these are tungsten-carbide alloys. They are mainly obtained using powder metallurgy methods. The VK8 brand has long established itself as especially popular for stamping nozzles for working with durable materials. These gimbals are successfully used for drilling holes in alloyed steels, heat-resistant steels, cast iron, hardwoods. Moreover, it is precisely this composition that is most affordable.


By the method of fixing the plates
The fixation of carbide inserts takes place on the cutting parts either by soldering or by screw (mechanical) connection, then the inserts are replaceable. If soldering is used, re-sharpening is possible only a few times, after which the drill becomes unusable.
In the case of using the mechanical method of fastening the plates, replacing the non-resurfacing plates is quite easy.

By form
The carbide insert can have several different shapes - this is a parallelogram, and a rectangle, and a rhombus, and a triangle with six cutting edges. The type of groove shape between the cutting edges should not be ignored. Whatever shape they have, their inner surface must be thoroughly polished so that chips are effectively removed from the working area and do not clog the hole, interfering with the operation of the tool.


Marking
Carbide inserts, which are soldered to a solid drill, are manufactured in accordance with GOST 25393-90. Replaceable plates with a certain number of edges are made according to another GOST - 19086-80.

How to choose?
When choosing carbide tips, there are two main factors to consider: what surface you plan to work on, and what depth and diameter the hole should have. This will immediately narrow the selection down to a small group of drills. Next, you need to pay attention to what material the cutting edges are made of, how strong the carbide is.
The reputation of the manufacturer of the product and its quality are no less important, because, as a rule, the price for such gimbals is quite high. Therefore, you should carefully study the properties of the product before paying for it. Of course, the more famous the manufacturer of the drill is, the higher the price for it, but the quality of such products is also quite high.
Do I have to pay for tools whose manufacturer is unknown, and the quality raises a lot of doubts? Each buyer answers this question for himself.
If you want the product to serve you for a long time and work properly, it is better to choose those made by manufacturers with a good reputation and have been working on the construction tools market for a long time.


Cooling and lubrication
In order for the carbide gimlet to work more efficiently, it must be cooled from the inside. It is possible to do without the use of cutting fluid only when you drill a hole, the depth of which will be no more than 1 nozzle diameter (for example, with a diameter of 3 mm, the hole can also be 3 mm deep).
The quality of drilling depends not only on how much cutting fluid (coolant) will move through the inner cavity of the nozzle, but also on how much coolant will be supplied. The head must be at least 12 atmospheres. Then the tool will not only be intensively cooled, but also the removal of chips will be much more efficient.


Sharpening
To impart the required hardness to the drill in its working part (its measurement is carried out in accordance with the HRC scale), it is thermally treated, basically this process coincides with the soldering of the plates themselves. If the inserts are profiled, the drilling result will be much better. Removable plates on twist or monolithic drills are suitable not only for drilling holes, but also for boring ready-made grooves and holes.
If the drill is equipped with wave-shaped plates, it can work in a more subtle technique - step-by-step insertion. This technology stabilizes the position of the drill or hammer drill at the initial stage of tapping, and also minimizes the risk that the tool will "lead" in the process.
The incremental plunge cut also reduces the cutting force generated during drilling.

How to sharpen carbide drills is shown in the following video.
The comment was sent successfully.