Drill sizes
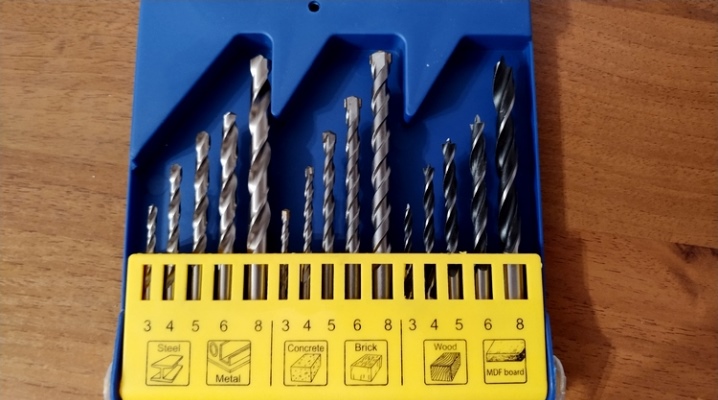
Drill sizes are information that even novice home craftsmen cannot do without. It is necessary to study the table of diameters of drills for metric threads and other types of holes. In addition to the standard sizes according to GOST, there is one more subtlety - how to determine the size of the structure.
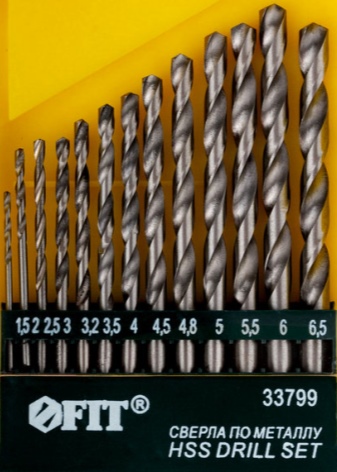
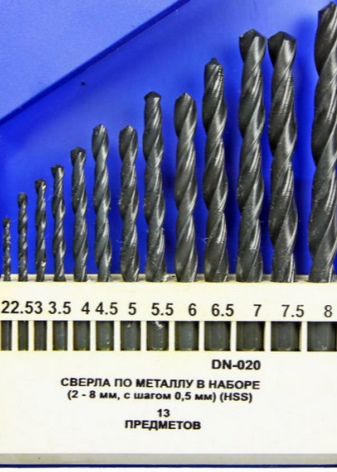
Overview of standard sizes
Processing metal, wood, plastic and some other materials without holes is sometimes impossible. This means that you will have to deal with the diameters of the drills. Typical provisions regarding them are given in GOST 885, approved in 1977. The standard only regulates the dimensions of the spiral products.
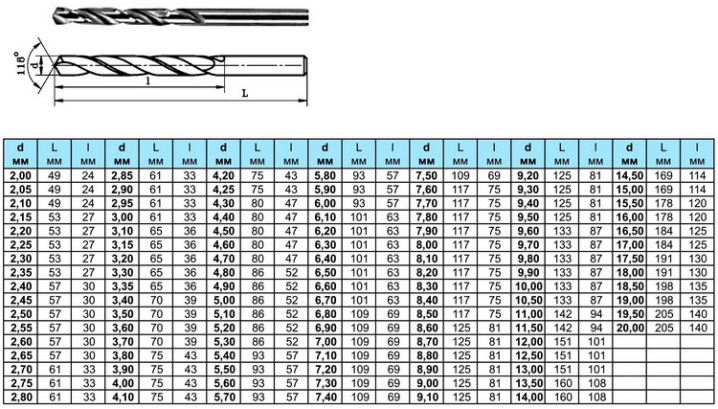
Some options are shown in the table below (dimensions are in mm).
Range series |
Occurring values (in brackets - variants of significant digits after the decimal point) |
Up to 0.3 |
0,25 (28; 3) |
Not less than 0.3 and not more than 0.38 |
0,32 (35; 38) |
0,38 — 0,48 |
0,4 (42, 45, 48) |
0,67 — 0,75 |
0,68 (70; 72; 75) |
1,06 — 1,18 |
1,1; (15) |
1,50 — 1,70 |
1,5 (60; 65; 70) |
1,90 — 2,12 |
1,95; 2,00; 2,05; 2,10 |
3 — 3,35 |
3.1; 315 (by special order); 3.32; 3.33; 335 (by special order) |
9,50 — 10,60 |
9,6 (7; 8; 9); 10,0 (1,2,3,4,5,6) |
23,02 — 23,6 |
23,25; 23,50 |
53,00 — 56, 00 |
54; 55; 56 |
It is worth considering that tools for metric threads can be regulated by various other standards. However, the overall gradation is universal. Allocate:
-
short (length from 2 to 13.1 cm, section from 3 mm to 2 cm);
-
elongated (with sections similar to the previous category, but with a length of 13.1-20.5 cm);
-
a full-fledged long (section from 1 mm to 2 cm, length from 20.5 to 25.4 cm) group.
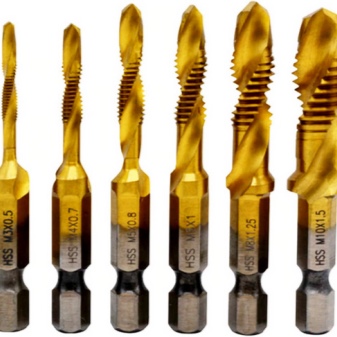
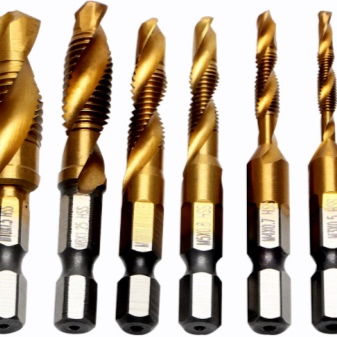
How to determine?
The easiest way to find out the size of the drill is by looking at the factory markings and the accompanying packaging - it is always supplied with the necessary inscriptions. But sometimes it doesn't work that easy. Experienced craftsmen can quite accurately determine the dimensions of a drilling tool by comparing it with samples of a previously known type.
The highest quality measurement is done using a caliper or micrometer.
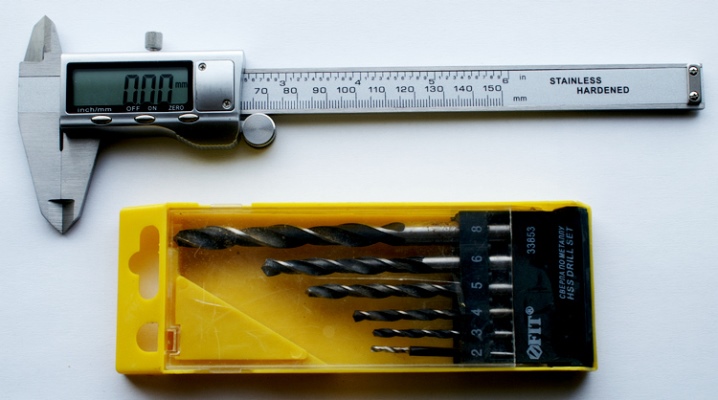
They also do this:
-
leave a mark on the end of the shank;
-
lay out the hardware on paper (necessarily - on a flat, smooth support);
-
turn the mark down;
-
a dot is put in the place where the mark touches the paper;
-
by carefully rolling the drill, turn it one turn;
-
put the second point;
-
measure the distance between them;
-
substitute this distance L into a formula of the form R = L / 2x3.14, where R is the desired section.
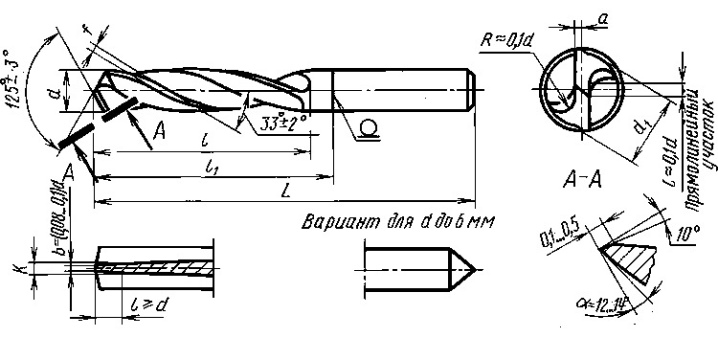
How to choose the size?
The so-called SDS shanks are widely used. The situation with them is as follows:
-
Simple SDS is used in 40mm rounds;
-
SDS + 10mm is also used in such chucks on light type hammer drills;
-
SDS top is a rare 14mm format used in 70mm cartridges;
-
SDS maximum - with the expectation of drills larger than 2 cm and cartridges of 90 mm.
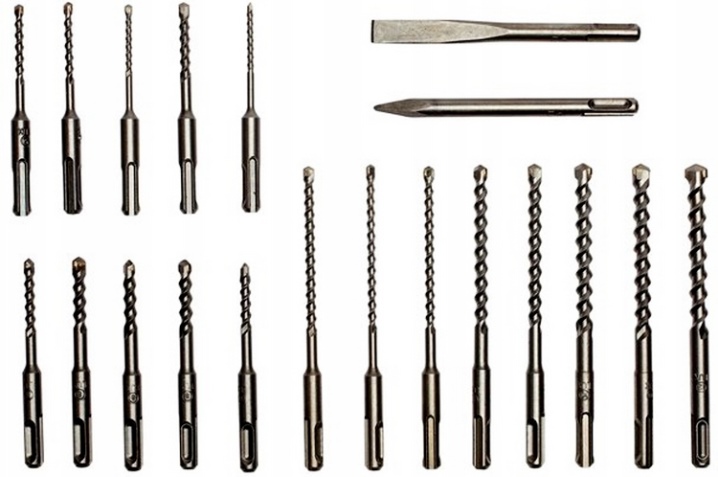
In addition to the shanks, the correspondence between the size of the drill and the size of the hole to be made should be taken into account. So, a tool of category "1.6" can punch channels with a size of 1.75 mm.
Other main options are:
-
with an M5 thread and an own section of 4.2 mm, it will turn out to make a channel up to 4.5 mm;
-
an M10 drill with a width of 8.5 mm will pierce a passage from 8.7 to 9 mm;
-
taking M16 (by 14 mm), you can count on a hole of 14.5 mm in the first and 15 mm in the second row.
For more information on drill sizes, see the video below.
The comment was sent successfully.