What are glass drills and how to choose them?

Glass drills are a special type of drill designed for working with fragile and hard materials. The drills have a standard size range - 2-20 mm, there are other diameters, the design also has some differences. The choice of tools for drilling glass must be done, taking into account all the features of the material and the requirements for the parameters of the hole.


Peculiarities
Conventional drill bits are not suitable for working with brittle materials. Here it is recommended to use their specialized options, so as not to damage the surface, to avoid the appearance of cracks and chips. The glass drill must be harder than the material itself. This requirement is met by products with diamond or vicite plating. The material for the manufacture can be different. This is usually tool steel or brass. The type of tip is the most important, in addition to the hardness of the alloy. It can be in the form of a feather or a spear. Such options are relevant for drilling small holes - no more than 12 mm in diameter.
The cleanliness and quality of hole formation will greatly depend on the skill of the specialist, but small chips along the edges are not considered a serious marriage. Diamond spraying makes it easier to drill through glass surfaces. The drill's stroke turns out to be much softer. When forming large-diameter holes - for example, for assembling furniture, other drills are used, with a tubular tip or crown.
With a large volume of operations, it is most advisable to carry out the work using a special machine.


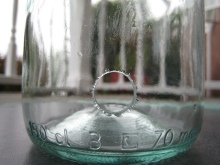
Species overview
All drills used when working with glass can be classified according to several criteria. Among the main parameters are the type of construction and the dimensional characteristics of the drill.... In addition, the type of tail is of great importance. It can be tapered for a drill chuck, hex for a screwdriver. For compatibility with machine tools, it is worth choosing shanks with the appropriate shape.

By design
Standard drills are not very suitable for working with glass. Here, special options are used that allow you to achieve the desired result with minimal effort. They have a shank - the part that goes into the chuck of the tool, it is the same as in other drills. The differences lie in the tip - the working element of the drill. Among the most popular types of construction are the following.
- The usual. Ideal for small holes. The diameter of these drills varies from 3 to 12 mm. Standard tip drills require a low speed drill or screwdriver with coolant supply to avoid overheating.

- Crown. Tubular drills of small and large diameters differ only in the way they work with them: ordinary ones are used in a set with hand tools, especially large ones - together with machines. The hole diameter can be varied from 12 to 80 mm.

- Diamond tubular. The product has an edge with a special coating of superhard stone chips. The diamond layer is electroplated.

- Feather. This tip is good for making large diameter holes. It has a central sharpened shaft and serrated elements around the circumference that cut into the material.
Depending on which type of drill design is chosen, the work will be carried out in a point or through way. Crowns allow for a neat creation of large holes, after which additional grinding of the edges is usually carried out.

To size
Each drill for working with glass has 2 main parameters - the diameter and length of the working part with a screw thread. The first characteristic affects exactly what size the hole will be. The standard versions are available in diameters from 2 to 20 mm, crowns and tubulars allow for a wider drilling range. The length is selected based on the thickness of the material: the thicker it is, the larger the size of the working tip should be.


How to choose?
When choosing drills for working with glass, you should pay attention to some of the subtleties of this process. The following guidelines will help you make the right decision.
- Victory drills the most versatile, they can be used to drill ordinary window glass, concrete, tiles. To prevent chipping, it is important to use a sharpened drill bit. This option is most often found in the arsenal of a home craftsman.
- To get a smooth hole without chips and defects in a conventional workshop, it is better to choose diamond drill with lance tip... It makes it possible to get a fairly large hole in diameter.
- Tubular drills optimal for furniture assembly. With their help, it is possible to make holes large enough in diameter in the glass without significant physical effort. It is recommended to work with crowns of large diameter using machine tools, especially if it is necessary to perform in-line work with repetitive operations.
- Appearance is also important. A high-quality drill will have all the necessary markings, including instructions on the alloy and diameter, the length of the working part. The lack of marking does not guarantee a good result.
- Steel is better than brass. Softer alloys of non-ferrous metals heat up more strongly and require more intensive cooling. In the case of glass work, their stainless structure does not offer any advantages.
- Color matters. Spraying is not the only thing that affects the quality of work. The black color of the drill indicates additional steam hardening. A bright yellow coating is obtained by processing with titanium nitride - these boraxes last longer than others, they are more durable.
Considering these recommendations, you can greatly facilitate your choice of a glass drill suitable for a home workshop or a small production workshop.
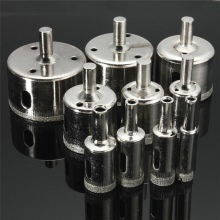


Terms of use
It is also necessary to drill the glass correctly. In most cases, work is carried out on the surface of display cases, window, furniture products. In some cases, a special machine is used, but usually a hand tool is sufficient. It is important to be careful when drilling, as the glass surface will crack and shatter easily if handled incorrectly. The process of forming holes in glass is divided into 2 main stages.

Surface preparation
Before starting drilling, you need to carry out certain preparatory work.
- Degrease the surface. You can take alcohol or turpentine, then thoroughly wipe the glass dry.
- Fix securely. It is important that the glass does not move. You can use special clamps with soft suction cups.
- Provide a secure footing. The surface area needs to be larger than the size of the glass sheet.
- Mark drilling point. To prevent the tool from slipping, it is worth sticking a small square of plaster or tape in this place. Then mark with a marker.


Carrying out works
After all the preparatory work is completed, you can start drilling. A suitable drill fits into the tool holder. It is installed strictly perpendicular to the glass surface. Drilling is not performed in one go.The depth is increased gradually, allowing the drill to cool down - it will heat up intensively during rotation. Having immersed the drill almost to the entire thickness of the glass, it is necessary to stop 1-2 mm from its surface. After that, the sheet is carefully turned over. Continue drilling from the reverse side. This minimizes the formation of cracks, significantly reduces the risk of chipping along the edges of the hole.
To obtain the most even edge, additional processing with fine-grain emery paper is used. When creating holes in glass, it is very important to correctly position the drill. Do not press hard, press on the tool. After every 5-10 seconds of operation, it is recommended to cool the heated drill in a specially prepared vessel with water.
To exclude a break in the material, from its edge to the center of the hole, they retreat 15 mm or more.


For information on how to drill a hole in glass without a special drill, see the next video.
The comment was sent successfully.