Features and types of drills for concrete

Strength and hardness are characteristic of concrete materials - this explains the high reliability properties during their operation. But if we want to fix any structure on such a surface, we inevitably come across the fact that, due to the hardness of concrete, it is very difficult to choose a tool for drilling it. A conventional drill is not suitable for these purposes, since it quickly dulls, but if you take a special one, you will be able to cope with this durable material quickly, and most importantly, efficiently.

Description
Concrete drill outwardly looks like usual: its design consists of a shank, cutting area and waste material removal. It is not difficult to distinguish a drill designed for concrete surfaces. It is made of high strength alloy steel. In addition, such a drill can also be identified by its tip, which has a "T" -shaped structure. It is the shape and material of the tip that allows you to drill into a concrete wall. The same drill is capable of handling marble, ceramics, porcelain stoneware and other similar materials.
The best drills designed for drilling hard concrete surfaces are considered to be victorious. The winner should be understood as the alloy of cobalt and tungsten from which the drill is made. This material is quite expensive, and today it is unlikely to buy such a drill, since cheaper products that are in no way inferior to him in quality and strength began to be produced to replace the winner.
In addition to being victorious, durable drills for concrete are also produced with diamond dusting. Such a tool has super strong performance. Externally, a diamond-coated drill looks like a crown located on a core in the form of a rod. The victorious drill is similar to its diamond-coated counterpart, but in shape it is a nozzle, and instead of a diamond coating, it has a hardfaced on the tip of the working part, which copes with hard concrete.



Species overview
All available drilling devices, which can be used to drill holes in reinforced concrete in a monolithic surface, are classified into 2 types.


For drill
This product differs from analogs in that has a cylindrical shank, sometimes this shank can be made with a hex shank... Such a carbide drill can be used not only for a drill, but also for a screwdriver.
These products are both thin and rather large in diameter.



For hammer drill
The shank structure of this type of tool looks like a cylinder. To distinguish them from analogs, these drills have a special marking in the form of the letters SDS Plus or SDS Max.
Concrete drills are divided into drums and unstressed. The difference between them is that the shockless version of the tool has a sharp cutting edge that cuts the material, and the hammer drill has a special carbide plate on 2 sides of the working part that breaks concrete. The impact option is also called a drill bit for concrete.
Impact drills are of 3 types.
- Auger drill - long professional drill for making deep holes. This device has special grooves, with the help of which the waste concrete material is removed.
- Gentle drill - it can be used to drill a hole with a small length and diameter. Working with such a device requires significant physical effort.
- Spiral drill - the drill has a large diameter and an elongated working part.


Some versions of the concrete drilling tool have special cutting crown. Such a device is used for drilling holes for sockets or socket outlets, a switch, as well as in all situations when it is necessary to make a round hole with a large diameter. Core drill is also divided into diamond and victorious. In the case of a victorious drill, instead of diamond spraying, small teeth with a victorious weld are located at the edges of the working bit.
There are also special drill shapes, designed for perforating aerated concrete. Outwardly, in terms of its structure, this product does not look like either a diamond or a victorious one. The device for aerated concrete has the form of a hexagon, and at the end it has a special design that allows you to carefully remove aerated concrete layer by layer, creating a hole of the required diameter in it.

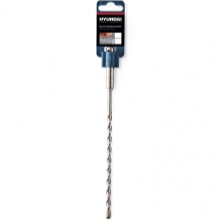

Dimensions (edit)
The quality of concrete drills and their sizes are regulated GOST standards - this tool has a marking, which indicates the length of the drill and its diameter. The diameter of this tool can be from 4 to 12 mm, and its length is from 50 to 540 mm, but there are drills, the length of which is 1000 mm.
Most often, for household purposes, products are used with dimensions of 6x110 and 8x600 mm. These drills are considered versatile and are used to drill deep holes. If it is required to drill not so deeply, then drills with dimensions of 12x200 mm or a 24x460 mm version used for installing a water supply or heating system are used.
When choosing the diameter and size of the drilling tool, it must be remembered that it will not work to make a deep and wide hole with a thin tool, since during operation, the drill will heat up and become dull due to excessive load on it.


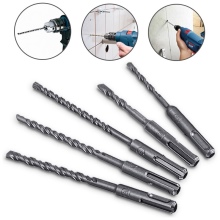
Popular manufacturers
The rating of the most famous manufacturers of drilling tools for concrete includes both domestic and European manufacturers. The best and most popular drills are produced under brands that are world famous.
- Bosch - high quality products, have the shape of a 4-sided spiral in the area of the working part of the rod. Such a tool does not require significant physical effort when drilling on a concrete surface. Due to its design, the drill does not overheat and does not undergo rapid blunting.
- Makita - manufactures especially durable products equipped with special soldering. The tools of this brand are mainly represented in the segment of equipment for shallow drilling of standard holes.
- Diager twister - produces percussive and non-percussive models of the instrument, distinguished by high quality and durability. Drills of this brand can be used for drilling not only concrete, but also natural stone and bricks.
The size range is supplied in a wide range.



Quite often, on the shelves of Russian construction outlets, you can see the products of companies Metabo as well as FIT or Stayer. These products have high quality and reliability indicators, but their cost is not cheap either.
Among the Russian manufacturers one can note high-quality products from the companies "Enkor", "Interskol" and "Zubr". The products of these famous brands are no less reliable than their European counterparts, but they are much cheaper. As for Chinese products, then their quality is also at a high level, although it is quite possible to run into a low-grade product.
When choosing a drilling tool, you always need to have a sensible approach to the question of its cost - a quality product cannot be too cheap.

How to use?
In order to prepare for installation work, experts recommend stocking up not only with a drill for concrete, but also with a tool for drilling metal. If, during the drilling process, it is found that the drill for concrete rests against the reinforcement of a reinforced concrete structure, you will have to change this tool by taking a drill for metal. After the reinforcement has been passed, the drill is changed again, continuing to work with a tool designed for concrete.
During the drilling process, you need to ensure that so that the drill does not overheat... Interruptions in work, which are done every 15 seconds of drilling, will help prevent this. The tool is removed from the wall for a short time and allowed to cool naturally, without using water or other cooling medium.
If, during drilling, the tool hits a stone, the drill is removed and the stone is crushed using a special bump stop, then drilling is continued again. When working with a supporting structure, experts recommend using a perforator, since even an impact drill cannot cope with the task and drill a hole of the required depth in such a wall.



Sharpening
After several cycles of work, even the strongest and most efficient drill gradually begins to dull. Sharpening the tool will help to correct this situation. It is performed on a special sharpening machine. Sharpening is subject to two sharp edges, which are located at the end of the drill and look like shelves. The process of sharpening the edges must be carried out so as not to violate their size, geometry and proportion. Sharpening work must be done carefully so that the drill does not break during processing on the machine's grinding wheel.
When sharpening, make sure that the drill does not heat up. To do this, the process is interrupted and the tool is given time to cool down - during the sharpening process, it is not recommended to cool the tool in water, as its tip may crack. It is best if the drilling tool cools naturally.
Sharpening a drilling tool requires experience and skill. At home, it is not always possible to do this correctly, since you can easily spoil the cutting part of the drill.
In this case, sharpening is carried out using sandpaper, but it is better to contact a professional workshop.

You can find out how to sharpen a betene drill with your own hands below.
The comment was sent successfully.