Features of Matrix drills

A drill is a tool for drilling and reaming holes in hard materials. Metal, wood, concrete, glass, stone, plastic are those substances in which it is impossible to make a hole in any other way. An elaborate tool, the result of an ingenious invention, it has many modifications. Our today's material is devoted to the Matrix drill review.


Description
Drills from the Matrix company are intended for:
- for drilling - obtaining friction holes;
- reaming - expansion of existing ones;
- drilling - obtaining blind recesses.
Drills differ in shank type.
Hexagonal and cylindrical are used in drills and screwdrivers of any kind. For jaw chucks, a triangular shank is used. SDS shanks are specially designed for rock drills.


The Matrix company has special requirements for the tool, both professional and manual, therefore the drills from this manufacturer are able to withstand a long load. In production, high quality carbide steels are used. Additional coating technology is applied.
Drills made of steels with added vanadium and cobalt received an excellent recommendation from consumers. Matrix drills are highly durable and wear-resistant; cobalt tools drill through even hardened metal. Drills for ceramic tiles, Forstner and others show excellent quality and accuracy results, give neat cuts with an even edge.

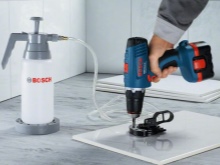
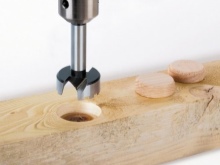
Assortment overview
All accessories are marked with the diameter of the hole to be drilled.
- Twist or twist drills - one of the most popular varieties in metal and woodwork, therefore they are used most often. They have a diameter from 0.1 to 80 mm and a length of the working part up to 275 mm.
- Flat or feather type drills are used to produce large diameter holes. The device has the form of a flat plate, is made with a shank or is fixed in a boring bar.
- Forstner drill similar to a nib drill, the modification has a cutter-milling cutter.
- Core drills are used in the case when it is necessary to cut only the annular part of the material.
- Single-sided drilling model used to obtain accurate diameters. Its sharpened edges are only on one side of the drill axis.
- Stepped model has the shape of a cone with steps on the surface. Each of these steps drills a certain diameter. With its help, drilling of different diameters is carried out without changing the equipment.
- To obtain tapered holes use a countersink drill.
- Diamond and Victory type used to work on ceramic tiles, glass, concrete, stone, brick, porcelain stoneware.



All types have different types of shanks:
- SDS, SDS +;
- conical;
- cylindrical;
- three-, four-, hex shank.
Twist drills have a diameter of 3 to 12 mm, feather drills - from 12 to 35 mm, a drill for wood has a size of 6 mm to 40 mm.

You can purchase both a single drill and a set. Manufacturers offer universal kits specialized for working on glass, tiles and ceramics. There are sets for metal, concrete, wood. A set of drills for metal has excellent performance. A set of 19 drills from 1 to 10 mm, with cylindrical shanks. The set is in a sturdy metal box.
The tool is made of high-speed steel, unique technologies have created a tooling that can withstand high shock and temperature loads. The spiral shape facilitates chip evacuation. It is used on machine tools, in working with drills, screwdrivers.

How to choose?
The choice of drill depends on what material it will work with. For wood, the choice of equipment depends on the diameter of the hole: for small diameters of 4-25 mm, spiral ones are chosen, for an increased diameter, feather models are taken, since they have a minimum size of 10 mm. An extendable centrobore pen is used when diameters are frequently changed.
Working with concrete requires a hard alloy tooling that is not inferior in strength to diamond. This is a winning tool that surpasses other options in terms of strength. For drilling metal, choose spiral, stepped or countersink drills made of steels with the addition of cobalt, molybdenum.
This tool has a three-layer coating of titanium nitride, aluminum and allows you to drill alloy and stainless steels.
For non-ferrous metals and carbon steel, steam oxidized tooling is required. A similar tool is black. For cast iron, ground drills are used.


How to choose a drill is described in the next video.
The comment was sent successfully.