Everything you need to know about core drills

To drill a certain hole in metal in the shortest possible time, you can use a new type of drill. This is a core drill that, due to its excellent characteristics, is gradually replacing the spiral types.
Device
A core drill is also called a hollow or ring drill, since it looks like a hollow cylinder. Used for drilling round recesses in metal and wood products. During operation, removes material around the circumference of the hole, leaving drilling residues in the center. These drills are an excellent alternative to expensive options with low efficiency.

The drills are characterized by high productivity, have a rather complex configuration, which consists of a shank, connecting screws, a pilot drill and the working crown itself. To assemble one structure from these elements, it is necessary to insert a pilot drill into a metal shank and connect with screws. Then the drill with the shank is installed in the crown, and the resulting structure is fixed.
The main and most important cutting element of such a drill is its teeth located on the working part of the tool. They differ in uneven pitch and are made of carbide.

Thanks to this, the tool has a long service life with high drilling accuracy. All quality standards and dimensions of core drills are indicated in the corresponding GOST. Failure to comply with these standards is punishable by law.
Where are they used?
Drills of this type can be used on equipment with low power. For example, the use of a magnetic machine, the power of which varies from 800 to 1000 kW. If you use a hole drill on it, you can get a hole with a diameter of 30 to 35 mm. If a twist drill is used under the same conditions, then at the same power the hole will be much smaller.
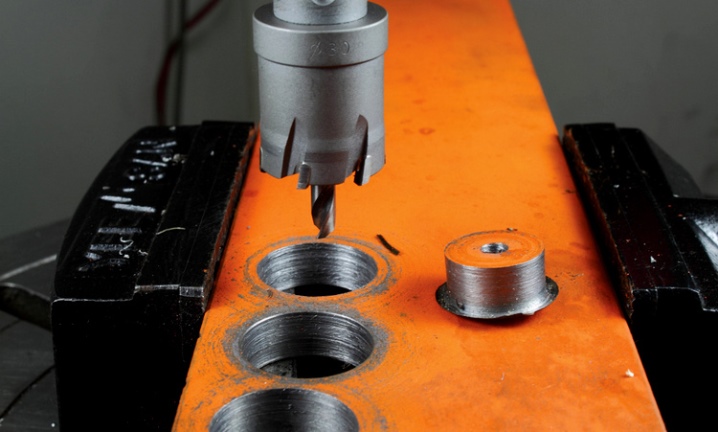
Working with such drills does not require much physical effort and special preparation, and the accuracy and quality of the machined surfaces will be much higher, since the roughness of the hole is reduced. It is possible to make overlapping holes. During operation, only through holes are obtained.


Core drills are indispensable when drilling pipes or curved surfaces, since conventional twist drills require special preparation and a lot of tweaks to work with.
During operation, the drills emit a minimum of noise. With their help, in combination with other tools, you can:
- perform multi-tool processing;
- get holes in concrete and stone structures, in ceramic tiles and natural stone;
- perform horizontal drilling for laying utility lines.

What are they?
Core drills are available in various types.
- Some are designed for magnetic drilling machines and have the highest strength.
- Others are made from high speed steel, which has no secondary coating on the cutting edge. This steel is of special grades with a small percentage of cobalt. The drills are used for drilling metal with low strength and a diameter of up to 35 mm.
- It can also be carbide bits, which have an unlimited number of cutting teeth made of carbide.Used for very strong materials, can produce holes larger than 35 mm.

Marking
All core drills are marked by means of which their main characteristics are determined. This is information about the manufacturer or trade mark, about the type of metal manufacturing, which is indicated by a letter. Thanks to the marking, you can understand what material the drill is intended for.
There are also geometrical parameters of the drill, based on which you can find out the size of the hole to be made. Each drill has a logo, its working length and diameter.

Popular brands
- One of the most famous manufacturers of various drills is Kornor company... All products are made of powder, high-speed steel, so they have a long service life in any conditions. The product range has a varied set of shanks that are suitable for all types of magnetic drills. The triple edge of the blade ensures high drilling speed with little vibration. The drills are reusable sharpening, which prolongs their service life. Ejector pins facilitate fast and accurate drilling. The company offers a wide range of adapters that allow the use of drills for various types of machines.



- Ruka brand started its activity back in 1974. Specializes in the production of metal cutting tools and accessories. All products are manufactured in our own factory located in Germany. The equipment has a high performance, only new production technologies are used. The products are of high quality, they are used on a professional level, in industry and trade. Finished products are tested and materials are tested during the production process. The manufacturer has received an international quality certificate. Affordable cost and reliability are the main features of the product.


- German brand Metabo manufactures electric and pneumatic tools, as well as various types of drills. The history of this company began in 1923 with the creation of the first hand drill. The company currently has 2,000 employees. There are 25 subsidiaries and 100 different representative offices located around the world. The company owns over 700 patents and rights. The assortment of core drills includes short and long, carbide and diamond, for concrete and metal. There are also sets that consist of different types of drills with different lengths. All products are of reliable quality and affordable cost.
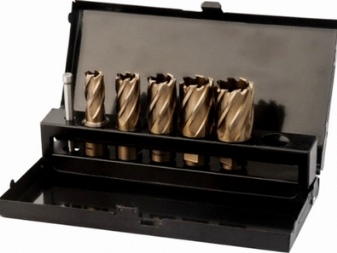

- The Chinese manufacturer of core drills is Bohre company... It entered the industrial equipment market in 2016. Its main direction is the production of consumables for rail drilling machines, as well as core drills. All products are highly durable and durable. In terms of quality, the products manufactured are analogous to many world brands. It is manufactured using identical technologies that are used by the most famous companies. To keep products at an affordable price, Bohre does not include a brand markup. The assortment of drills includes various types of carbide with brazed plates, products from high-speed steel with different diameters and lengths of the working part.


How to choose?
In order to choose a core drill, the following characteristics must be taken into account. At first, this is the working diameter and hardness of the working part, as well as what depth the drill can produce during operation... What series does the tool belong to, what is the size of the shank, with which it will be necessary to install the drill into the chuck of the equipment. What material is the drill intended for, what is its centering method and what level of roughness it gives out during drilling.

Of course, you need to take into account the design features of the drill. It can be made from high speed steel or have brazed carbide inserts, which means it can be used for hard and soft metals. If you need a tool for drilling recesses no more than 35 mm with low metal strength, then it is better not to overpay, but to purchase a HSS drill. It has a low cost, eliminates the risk of tooth breakage.
For working with hard metals in the production of large holes (over 35 mm), you need a HSS drill.

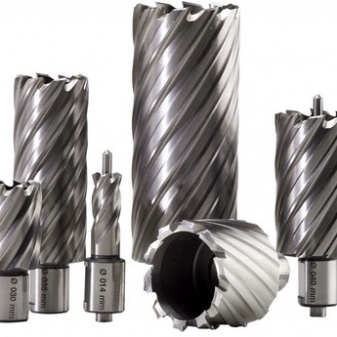
To choose a crown for wood, you should pay attention to the material of manufacture of the cutter, as well as the form of sharpening of the teeth and their number. Such crowns are easy to distinguish from the rest, as they are painted black and are produced from metal alloys.
When choosing a drill, it is very important to have a centering pilot in it. Usually it is already included with the crown. But if it is not included in the kit, you can purchase the pilot separately. Thanks to him, the drilling process is more accurate.
How to use?
In order to drill, you must first of all collect all the components. Clamp the center drill inside the shank, slide over the bit and secure. The shank is a replaceable part, therefore it is matched to the dimensions of the electric drill.

Next, you should carry out the marking on the metal or other surface where the center of the hole will be located. Place the center drill in the designated area and drill. With the help of a special spring, the center drill is retracted inside the shank, the surface is drilled with a crown. At the end of the work, the spiral pushes the emerging metal cylinder out of the crown. The resulting recess has an ideal shape, smooth edges that do not require grinding.
Drilling in metal can be done dry or wet. The first method is used in domestic conditions, when there is no technical possibility of supplying cutting fluid, it is used for drilling holes with a diameter of up to 20 mm.


Wet cutting is carried out using a liquid supply that effectively cools and flushes out the resulting waste. This method is used in large installations, in professional hand tools, and is intended for holes with large diameters.
For more information on core drills, see the video below.
The comment was sent successfully.