Description and selection of conical drills for metal
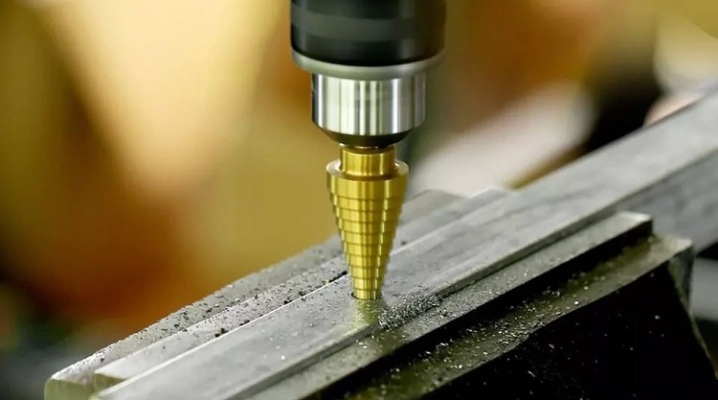
Taper drills are considered a professional tool with a long service life, versatility and simplicity in design. Externally, the drill looks like a cone, hence its name - cone. This type of structure makes it possible to make round holes, on which there are no burrs or roughness.
An absolutely smooth hole can be used for construction and installation work, when processing metal surfaces. To choose the right working drill, you need to carefully study its properties and characteristics.


Features and scope
A tapered drill looks like stepped series of transitions of annular spirals... The spirals are sharpened and located longitudinally, from the wider part they taper to the narrower one under the cone. In some embodiments, there is a groove that is located longitudinally - it is this groove that forms the cutting surface of the tool. Conical drill for metal is manufactured according to GOST standards. By purchasing one cone-shaped product, you can use it to make holes of various diameters. This versatility contributes to savings and ease of installation.

This drilling tool is well proven in application at high speeds of rotation of an electric drill - as a result of the work performed, smooth holes with a high quality of the edge part are obtained. The drill can be used for different sheet metal thicknesses and works great even on the thinnest pieces.
The design of the cutting surfaces characteristic of this tool makes it possible to work with steel blanks, non-ferrous metal alloys, plastic and plastic products, with wooden and plaster surfaces.


The working part of the drill is equipped with a sharpened tip, which guarantees the exact location of the tool at the point of work. Tapered drills can be used not only in electric drills or screwdrivers, but also be installed on stationary type processing machines. If you use a special adapter, then the drill can be fixed on a grinder or in a hammer drill chuck.
In addition to making holes, a tapered tool is also used to correct defects that are formed after drilling with a drill. The tapered drill assists in finishing operations by removing burrs and correcting the effects of misalignment during drilling. This tool is often used in the process of repairing vehicles, for performing plumbing works, in the decoration and construction of buildings and structures.


What are they?
The universal conical drill is a special attachment for rotating type electric tools. The drill has a cone-shaped working tip and a shank body, the end of which is machined in the form of a hexagon or a cylinder.
Conical drills are divided into 2 types.
- Smooth - have a smooth surface of the working part, with which you can drill even strong steel, increasing the hole diameter depending on the degree of deepening of the drill. To get an accurate hole diameter, the drilling process needs to be paused periodically to take measurements.For ease of measurement, many manufacturers put special marks on their products indicating the size of the hole diameter.
- Stepped - this design, thanks to its steps, helps to more accurately and simply track the passage of the drill, which forms the desired hole diameter. The process of drilling with a step drill itself is performed more smoothly and accurately.
Experienced experts believe that when performing large volumes of work related to drilling holes, it is more convenient to use cone drills, especially if work is required to be performed on thin sheets of workpieces.

Popular manufacturers
The cost of a tapered tool depends on the quality of the material from which it is made, as well as on the manufacturer's brand. If we talk about Russian drills, they are much cheaper than their European counterparts, although both products can be absolutely the same in quality. The most popular cone drills are tools from several well-known manufacturers, such as:
- Russian brands Zubr and Attack;
- Ukrainian brand "Globus";
- Japanese brand Makita;
- German brands RUKO, Bosch (professional segment) and Geko (household segment).
The cost of tools from these manufacturers is high, but it is justified by the impeccable quality of the products and their long service life.



How to choose?
To choose a quality drill, experts recommend paying attention to several nuances.
- The speed of drilling, as well as the quality of the result, depends on the number of steps, located on a cone-shaped working part. In addition, the diameter, height and pitch of these steps are important. Some professional models have up to 12 steps.
- Cone diameter depends on the size of the hole to be made.
- Duration of use of the drill and its cost depends on what material it is made of, as well as on the processing of its surface.
- In Russia, it is more convenient to use drills that have dimensions in millimeters in accordance with GOST. Models of American manufacturers are marked in inches, which takes too much time to convert their values into millimeters.
- A high-quality drill does not need sharpening for a long time, but he must be provided with such an opportunity.



Often one of the selection criteria for a tool is its cost. For example, products from a Russian or Ukrainian manufacturer will cost about 500-600 rubles. for a product with a maximum diameter of 20 mm, and if you take an option with a maximum diameter of at least 30 mm, its price will be already 1000-1200 rubles. The same samples of the European brand will cost 3000-7000 rubles. Based on the cost, some craftsmen consider it more expedient to buy several products of a domestic manufacturer than to pay for 1 drill of a European brand.
When deciding whether you need a set of tools, or just buy 1 drill, should be decided on the basis of the amount of work performed. If you frequently perform large volumes of work, it is advisable to buy drills of good quality and those diameters that you need. To perform one-time tasks, it is enough to buy a model of the required diameter from an inexpensive price segment.

Marking
The taper tool is marked with letters and numbers. The digital marking indicates the diameter of the cone from the minimum to the maximum, as well as the step of its steps. Letters indicate the grade of the steel alloy from which the nozzle is made. The most recent numbers in the marking indicate the instrument according to the Rockwell system.
Alphanumeric markings are made on the outside of the drill by the factory method using engraving. The order of letters and numbers begins with the letter designation of steel.Most models are made of cutting steel, so the first letter is "P", if the alloy contains molybdenum, the letter designation will be "MZ". Next comes the numerical designation of diameters and pitch.
It is noteworthy that drills made in Russia with a diameter of no more than 2 mm are not subject to marking.


The size
The cone diameter is available in 2 sizes. The first indicator gives information on the minimum diameter of the drill, and the second on the maximum. The step with which the diameters change is also indicated in the marking. For example, marking 4-10 / 2 would mean that the minimum size that can be made with this drill is 4 mm, the maximum hole can be made 10 mm, and the pitch of the varying diameters is 2 mm, that is, the drill will have diameters of 4, 6, 8 and 10 mm.


Coating
The color of the metal from which the drill is made is an indicator of the quality of the tool. If the drill has a gray steel shade, it means that the alloy from which it is made has not been subjected to high-temperature processing, so such a product will not be strong and durable... The drills, which are black, have been treated with hot steam, and their strength is higher than that of their silver counterparts. If the instrument has a golden sheen, it means that its surface is covered with a layer of titanium - such a product is the most durable and durable.


Sharpening capability
The drill, when used, loses its sharpness over time, its edges become dull, and in order to increase the efficiency of the work, the tool must be sharpened. You can perform this procedure in a workshop specializing in sharpening tools, or you can sharpen the drill with your own hands. Tool sharpening performed on professional equipment is more preferable than manual version of this procedure. The choice in favor of professional processing is based on the following reasons:
- the diameter and geometric shape of each taper step will be saved;
- the correct angle of the edge at the cutting surface is maintained;
- the correct technological process of sharpening is observed, which protects the tool from overheating.

If it is not possible to sharpen the tool in the workshop, you will have to perform this task yourself. In the process of work, you must adhere to the following rules:
- the cutting parts of the drill edges must be kept the same size, grinding off only a minimal part of the metal;
- cutting edge angle cannot be changed;
- the step between the degrees of the cone must be the same and uniform on all turns of the drill;
- from the cutting edge to the side surface of the upper or lower turn must be the same distancestored on each diameter of the taper steps;
- tool sharpening is performed subject to its rigid fixation;
- process is running devices with fine abrasive;
- tool sharpening should preserve all its geometric proportions and cutting edges as much as possible.
The easiest way to sharpen the drill is to use a special machine that is glued around with fine-grained sandpaper. How well and qualitatively the drill is sharpened can be determined by the nature of the chips that are obtained if you use them in your work.
If the sharpening is done correctly, the chips will be the same not only in shape, but also in size.


How to use?
To use a tapered tool, you need an electric drill or screwdriver, into the chuck of which the drill is fixed. The choice of drill depends on the desired diameter to be drilled into the work piece. It is best to choose an electric drill with the ability to regulate speeds; for work, a speed of 3000-5000 rpm is used.
Hole drilling is done in 3 steps.
- The drill is securely fixed in the chuck of the electric drill... Then a place for drilling a hole is marked on the workpiece.
- Having placed the drill at an angle of 90 degrees to the workpiece, they begin to drill the hole. In this case, the position of the drill should not change until the end of the work.
- Drilling starts at low speed, gradually increasing their speed.... When the hole reaches the required diameter, the drilling process is stopped.
The result of the work will be a hole of the desired size with neat edges, without roughness or burrs.
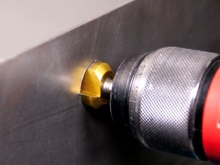


Care Tips
Modern taper stepped drills can be used to drill holes in wood, metal, plastic and other materials. After use, the tool must be treated with a special protective compound intended for the care of the cutting tool. If such a composition is not at hand, you can make it yourself by taking machine oil or thick liquid soap for lubrication.
If you regularly process a tapered working part with this composition, you can extend the life of the cutting surfaces, since the above components will be able to protect them from dullness in case of mechanical damage arising during storage.

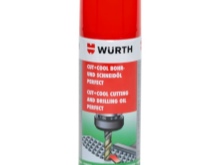

In the next video, you will find an overview and test of the GRAFF step drill for metal.
The comment was sent successfully.