How to choose drill bits for machine tools?

In certain industries (mechanical engineering, shipbuilding, metallurgy), special equipment is used, which is called machine tool.
An integral part of any machine is drill, with which you can make a hole of different diameters in absolutely any material, including concrete and metal. In this article we will talk about how to choose them, about the features, types and rules of operation.

Peculiarities
Drills for machine tools belong to cutting tools... They are used to drill new holes and increase the diameter of existing ones. Drills for machine tools are manufactured in accordance with regulations and documents for a specific technology.
This tool has a number of features, including:
- high coefficient of strength and reliability;
- high level of resistance;
- corrosion resistance;
- are made of quality materials, among which there are many different alloys and, of course, steel, which is called "high-speed", but not any steel is suitable, namely grades P18, P9, P9K15.
The constituent parts of the drill, whatever it may be, are the neck and the shank.
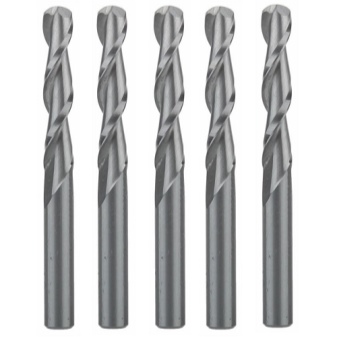

To increase the service life of the drill, during the manufacturing process it is coated with special compounds.
- Oxide film... This coating increases the coefficient of resistance of the product to heat during friction.
- Diamond coating. One of the most durable, it is used to process products intended for drilling in hard and very durable materials, such as stone or porcelain stoneware.
- Titanium coated.
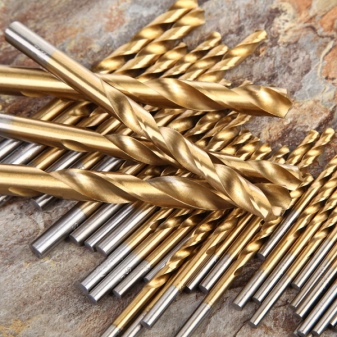
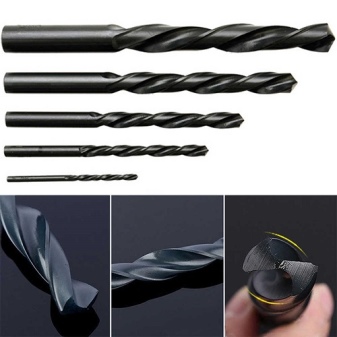
Drills for machine tools differ not only in technical parameters, but also in color, which indicates the way the product is processed.
- Gray... Indicates that the product has not been treated in any way. It does not have good technical parameters and a long service life.
- Black... At the final stage, the product was treated with superheated steam.
- Yellow... There was a special treatment, the main purpose of which is to relieve internal stress. Very strong, high quality and durable product.
- Golden... It says that the alloy from which the product was made contains titanium and nitride, several stages of processing have passed. These drills are the strongest and most stable.



Types
The assortment of drills currently on the consumer market is large and varied. There are the following types:
- spiral;
- crown;
- for drilling holes in pipes;
- screw;
- feather;
- centering;
- ring;
- conical;
- stepped.

Each of the above types intended for use in the operation of a specific machine... For example, core drills are the best option for a magnetic drilling machine; through, blind or twist drills are used for the filler device. Tapered samples are suitable for a lathe, and a special slotting machine is used for a slotting machine.
It is also worth noting one more classification separately - by appointment. Each product is designed to work with a specific material. So, drills are:
- universal;
- on wood;
- for metal;
- for concrete;
- on plastics and ceramics.
All drills for machine tools differ in size (they can be short, medium or long), weight and machining accuracy.



Criterias of choice
When choosing an attribute for a machine, it is imperative to take into account several basic criteria, guided by which the choice will be made correctly.
- Product technical parameters: size, weight, color, work accuracy, sharpening angle.
- Machine type. There is a special product for each machine.
- What material the work will be connected with.
- For what purposes do you need a product. Of course, if this is a large-scale industrial activity, you need to buy a professional attribute. But for household needs, household sharpening drills are perfect.
- Manufacturer and cost. Today the most popular and reliable manufacturers of drill bits for machine tools are Bosch, Ruko, Haisser and Zubr.
When buying carefully inspect the product... It should have marking - this is stipulated by legislation and regulatory documents according to which drills are manufactured. All requirements for its application are clearly spelled out in GOST 2034 - 80. Marking consists of a set of letters and numbers. This set of symbols indicates the diameter of the product, the presence of various impurities in the alloy for its manufacture, the hardness coefficient, the place of manufacture and the production technology.



Operating rules
The product itself cannot harm the employee. But if it is incorrectly established, then the consequences can be very serious. This should be done only according to the instructions, performing sequentially step by step. Every conscientious manufacturer must attach to the product instruction for operation and installation.
There are several basic storage rules:
- it is best to keep the product in a special metal cabinet;
- you need to sort the drills by diameter, purpose and place them at a short distance from each other;
- after use, it is imperative to clean the product from dust and dirt residues;
- store in a dry place, away from corrosive acidic liquids.
All these rules and recommendations have been developed and created by experienced professionals who have repeatedly encountered drills and machine tools in their work.
If you follow them, then you can extend the life of the product, and its work will be effective throughout the entire period of use.

See below for more details.
The comment was sent successfully.