All about drill bits
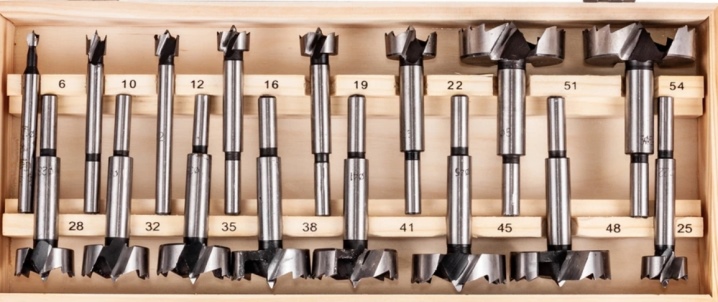
Drill-milling cutter is a universal solution for simultaneous drilling and processing of metal, wood, and other materials with low hardness values. With the help of such a tool, you can not only make holes, but also expand them using the side face. To learn more about it, advice on choosing a milling drill for metal, wood, and other options for materials and products for various purposes will help.

Peculiarities
Combined cutting tools are gaining in popularity. The drill-milling cutter belongs to this group of products, provides simplification, reduction in the number of operations when processing materials. Each of them has 2 elements: drilling and milling. The first part is needed to create the hole with the desired depth and diameter. The cutter is on the side edge, if necessary, it is activated without changing the tool - by changing the pitch of the spiral along the length, it is possible to obtain the desired result in 1 pass.
The distinctive characteristics of such a tool include high wear resistance and long service life. They are made from hard steel grades that are not subject to intense wear. In addition, such a tool lends itself to regrinding. If the angled part of the drill becomes blunt, its sharpness can always be restored.
Among the technological capabilities of such products, one can single out the performance of a whole range of operations. In addition to conventional drilling, this can be V-grooving, chamfering and milling.




These drills are versatile. They are suitable for use with a wide range of materials:
- plastic;
- MDF;
- Chipboard;
- plywood;
- drywall;
- solid natural wood;
- metal.
It is important to consider that the successful operation of a combination tool is determined by its correct use. It works best when working with heat-treated metal and soft woods.


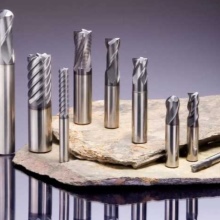
In the design of the milling drill, there is a shank for fixing an electric or hand tool in the chuck. And also there are 2 working surfaces at once, with which you can work sequentially or individually. Such combined models are most in demand in the field of woodworking. Depending on the type and diameter of the seating part, drill-cutters can be universal, for machine tools and hand tools, as well as specialized.
To increase the strength of steel tools, increase their service life, and reduce friction during work, their surface is often coated with special compounds. Most often, there are products of golden color. They are coated with titanium nitride. Drills-milling cutters are sold not only individually, but also in sets - it is advisable to purchase such a set if drilling is performed often or put on stream.

Species overview
The classification of drills-milling cutters in wood is largely determined by their shape and method of attachment in the tool. Let's consider the main varieties found on the market.
- Flat milling. The product with a wide flattened cutting element allows working with large diameter holes.
- Cylindrical. Externally resembles classic drills, the milling part has the same diameter as the tip.
- Nasadnoe. This version of the drill-cutter is used as a tool for a milling machine. Its tip is oriented for installation in the spindle and has a standard bore diameter of 32 mm.
- Terminal. This option is also called finger. Its landing part is rather thin, simple, has a diameter of 8-12 mm. End milling drills are also called universal end drills, as they can be mounted in special machines and in ordinary hand tools.
- With a two-tipped blade. This tool can be used for chamfering, milling and drilling soft non-ferrous metals. The optimum tilt angle for it is 60 to 120 degrees. To improve the performance characteristics, titanium-boride spraying is applied to the product.
- With a four-blade type blade. Drilling and milling tools of this type increase the diameter of the holes to be made and help to increase the number of grooves to be formed. This option is used for the processing of hard metals.

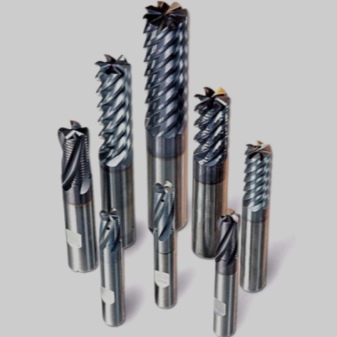
This is the main classification. Besides, drills-milling cutters are carbide - they are most often used for metal work, as well as made of high-speed tool steel. The shank of the end products is cylindrical and hexagonal. It can be of different lengths.
The classification also includes the type of surface to be treated. Versatile varieties are suitable for working with different surfaces.
And there are also specialized options for metal and wood. According to the manufacturing method, compound and solid serla cutters can be distinguished.

Selection rules
You can choose the right drill-cutter for use, if you take into account all the significant points.
- Country of origin and brand. Inexpensive products from China do not always justify the hopes placed on them - they quickly become dull, break, and bend. More reliable options are produced by companies from the USA, Germany, and Russia. Market leaders include Metabo, Hawera, Ruko.
- Material of manufacture, availability of coating. For metal work, carbide steel options are used, the most durable and productive, with or without coating. Other drills are more suitable for processing wood and composite materials, chipboard and fiberboard. They are made from high speed tool steel.
- Tail type. It directly determines the compatibility of the instrument. For a drill, hammer drill, options with a hexagonal or cylindrical tip are best suited. In addition, the length of this part is important. It must correspond to the parameters of the hand and power tool on which the accessory will be installed.
- Dimensions. The diameter of the drill-cutter is indicated by the manufacturer in millimeters. This parameter is always determined by the dimensions of the working part.
- Milling element type. It determines which holes can be obtained after processing. And the angle of its sharpening is also important.
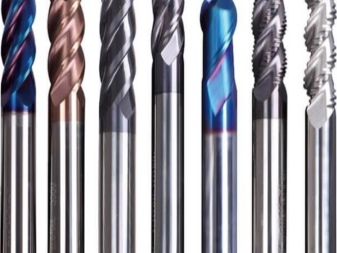

All these factors help to select high-quality and reliable drills-milling cutters for performing work on metal or wood. Combined instruments help to simplify and reduce the number of operations, eliminating the need to change the tip. Refusing to change bits, choosing the right combination product, you can get the result no worse than when performing work using special milling equipment.


The following video talks about drill bits.
The comment was sent successfully.