Choosing milling drills for metal
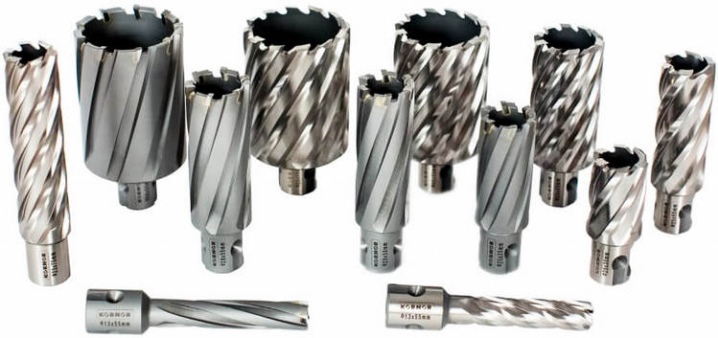
Craftsmen know that metal products can be processed mainly with the help of special equipment and tools. However, all this is not suitable for use at home or in a small workshop. The solution was the use of a cutter for metal, which is inexpensive and can work together with a conventional drill.
Peculiarities
A drill-milling cutter is, in fact, one of the types of cutting tools that combines the functions of both a drill and a milling cutter. It is used to make various holes in all kinds of materials.
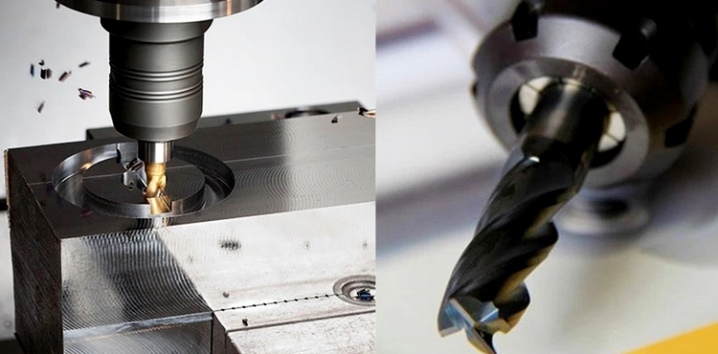
The hole itself is made using a drilling element. But to expand it, while giving the desired shape, as well as size, is obtained with the help of a cutter, which is a side face. Since there are only two working surfaces, the tool is called a milling drill.
The tool with which you can perform work with metal can be considered universal. It can be applied to almost any material. Such a drill-cutter has its advantages and disadvantages.

First of all, it should be noted the advantages. This tool is capable of performing two operations at the same time, since it not only makes a hole, but also immediately gives it the required shape. This is especially true for production conditions when labor productivity plays an important role.
The second advantage is ease of use, because you can use not only special equipment, but also any tool with a clamping device. For example, a bench-top machine, conventional drill, or hammer drill will do. Also, the drill bit can be re-sharpened. This means that when the sharpening angle is blunt, it is restored without problems.


Users name only one factor as a disadvantage - the lack of the required degree of roughness can play an important role in certain cases. In such a situation, other ways of reworking the hole may be required.
What are they?
The milling drill for metal has a fairly large number of varieties. Specialists distinguish end, cylindrical, disc, shaped, angle and end tools. Let's talk about each of them in more detail.
When working with metal, when it is supposed to use a drill, the most in demand is an end-type drill with a vertical axis of rotation. It is excellent for use on flat surfaces, as it can be used to remove a layer of material of the required size.

With the help of a rotary cutter, you can form all kinds of grooves and grooves on the metal surface. This becomes possible due to the fact that the teeth are located not only on the side, but also on the end part of the product.


The cylindrical drill is used to work with flat areas of metal elements... The teeth are located on the sides and can be either straight or helical. They have a horizontal axis of rotation.
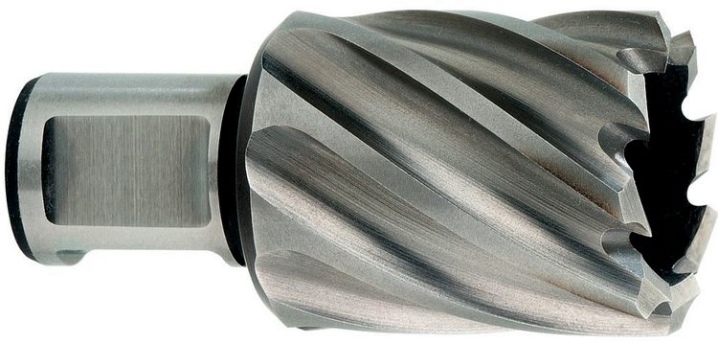
An end mill is most often used when working with a drill. With its help, you can make fairly deep grooves or contour grooves. Processing of mutually perpendicular planes is also permissible. There are main teeth in the side of the tool, while other cutting elements are located at the end.


When working with shaped surfaces, you should opt for a similar drill. They are produced by pulling and are not very long.The main difference is the fact that such a cutter is used for structures with a significant length-to-width ratio.
As for corner cutters, their design can be called the most complex. They are used most often when working with angular grooves, as well as inclined planes.


As for the design, one-corner and two-corner products can be noted. In the first case, the teeth are located not only on the side of the cone, but also on the end. With a double-corner cutter, the cutting elements are located on both conical surfaces that are adjacent.
If the end mill is the most popular, it should be noted that corner and shaped tools are the least in demand.
How to choose?
Choosing a cutter for metal can be difficult for an inexperienced user. Therefore, professionals advise focusing on the diameter of the product, its cutting teeth and their location, the shank, which helps to place the drill in the drill chuck and fix it securely.

The material of manufacture and the quality of sharpening also play an important role. If you intend to use an electric drill, we must not forget that it is intended for manual use, so the drills used in special machines will not work here.
If a tool of an assembly type is required, it is necessary to check how well the cutting element is fixed. Most often, the soldering of the product is used, in this case the plates adhere reliably to the surface, otherwise they will simply fly out during the work process.
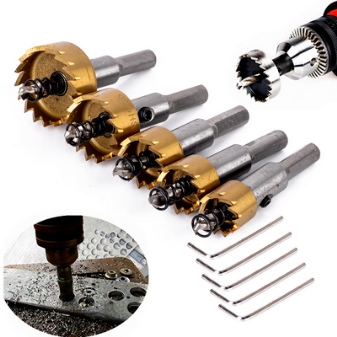
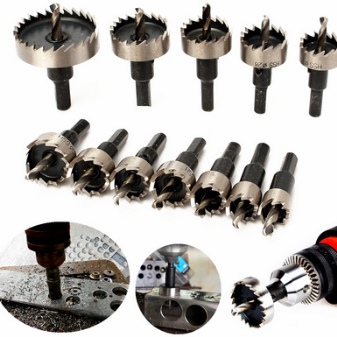
Sharpening quality is also fundamental. It's not just productivity that is directly related to it, but also how well the job gets done. Manufacturers often try to develop a unique sharpening technology, but experts say that standard schemes are the most preferable.
The material of manufacture also affects various indicators. This is the service life of the tool, and the quality of work, and their productivity. When it comes to one-time jobs, the requirements are not so high. In this case, it would be optimal to use a solid element, for the manufacture of which steel of the same grade was used.

In a situation where the tool is planned to be used quite often, it is better to opt for a more expensive one, which has teeth made of carbide inserts.
Some users are trying to save money. To do this, they make a drill-cutter on their own using available tools. However, it should be borne in mind that such a tool is suitable exclusively for elementary tasks. It is not necessary to count on a particularly high-quality result in this case.
For more information about milling drills for metal, see the video below.
The comment was sent successfully.