Features and secrets of choosing Forstner drills
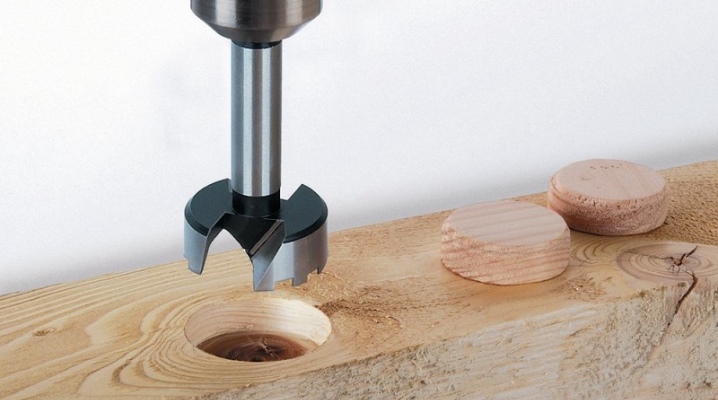
The Forstner drill appeared in 1874, when engineer Benjamin Forstner patented his invention for drilling wood. Since the inception of the drill, many modifications have been made to this tool. New samples of Forstner's drill have a different structure, but retained its principle of operation. This tool is used in those areas where it is required to make an even and neat hole, while the workpieces can be not only made of wood - it can be drywall, furniture board, polymer materials.
Drill modification depends on the raw material to be worked with and the task to be performed. The drills are of different quality, which directly affects their cost.


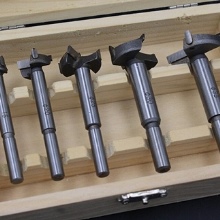
What is it and what is it used for?
The Forstner drill is a kind of milling cutter that most often works on wood. In the process of work, the tool uses 3 cutting edges - a circular rim cuts the edge at the hole strictly according to the specified diameter, a central pointed projection helps guide the cutting process in the desired direction, and two paired cutting surfaces, like small carpentry planers, cut the plane of the material layer by layer. The result is a flat hole with a flat bottom or a through hole.
The tool is widely used in woodworking of soft and hard wood species. Its purpose is to make through or blind holes, which are needed for installing locks, for hinges, for threaded or eccentric type ties, for holes needed when installing fittings. In the processing of modern types of materials, the Forstner drill has proven itself well when working with MDF, chipboard, DPV and their various options.
As a result of machining, the edges of the holes are clean, without chipping and rough roughness.



In addition to woodworking, Forstner's cutter can be used for installation work on the installation of window frames, when conducting channels for electrical wires, when installing plumbing equipment, water supply and sewerage systems. Forstner drills are installed in the chuck of an electric drill or screwdriver and operate at 500-1400 rpm. The rotation speed of the drill depends on the diameter - the thicker the drill, the lower its rotation speed should be.
For the manufacture of drills, high-strength steel is used, which has high-speed properties. In the process of work, thermal energy is generated, and such steel withstands it well, retaining its properties. To make an even more durable tool, manufacturers coat their products with a thin layer of titanium or apply hard-alloy brazing to the working area of the drill. To increase efficiency, the cutting edges of the drill can be serrated, which better grip the material, but this loses the cleanliness of the cut. Based on the quality of the alloy that was used in the manufacture of the drill, its cost also depends.

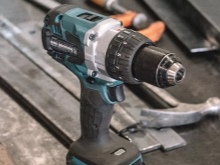
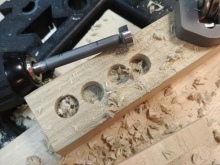
Advantages and disadvantages
The hole drilling tool has a lot of positive properties, but, like everything else, it is not devoid of some negative characteristics.
Advantages of the Forstner drill:
- well-sharpened sharp edges of the drill are the indisputable guarantor of high-quality and smooth processing of the workpiece material;
- the tool can be used with a handheld electrical device or installed on an industrial-type stationary machine;
- the direction of the cutting elements in the hole of the material occurs not only due to the sharp centered protrusion, but also with the help of the edge in the form of a closed ring, as well as the entire cylindrical working part of the drill;
- even if the hole diameter in the process of work goes beyond the workpiece, the specified direction of the drill does not change, making high-quality and smooth cuts without chipping and burrs on the part of the product where possible.


The smoothness of the cut when processing the workpiece with a milling cutter occurs by cutting the wood fibers around the circumference. Moreover, this process takes place even before the moment when the main working edge of the drill begins to touch these fibers.
This drill also has disadvantages:
- the cutting parts of the cutter are at some distance from each other, which does not give them full contact with the working surface as it happens with the edge of the annular rim, as a result of which the drilling process is accompanied by vibration of the tool, and there is a risk that the cutter may simply jump off the intended holes;
- if the cutting blades are equipped with teeth, then the vibration during operation increases, and the risk of the drill coming off the intended stencil increases;
- Forstner's drill is more expensive than other similar tools designed for drilling holes.
Despite some drawbacks, the drill has a high level of performance and a long service life, provided that the rules of use are followed.


Species overview
Various versions of Forstner's drill are produced today by both domestic and European manufacturers - a wide range of their products is presented on the Russian market. Many companies are trying to improve the design of the drill for ease of use, so on sale you can find models with a drill depth stop, which can be either fixed or adjustable. In addition, models that can be sharpened by machine are very popular. In such a drill, the cutting edge of the rim on the back of the cutters has a special cut.
Forstner's drill bits are also subject to modifications, depending on their type of model, they are divided into two main groups.
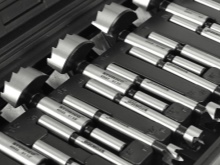


With carbide cutters
The design feature of such a tool is that some modifications have cutters to which sharpened elements made of high hardness carbon steel alloys are soldered. Such cutting edges significantly increase the cost of the tool, but these costs are justified by the efficiency of the work and the long service life of the drill.


With toothed rims
The design of the drill on the cutters has a serration located along the entire annular cutting rim. The advantage of such a tool is that during operation, the drill itself and the surface of the workpiece to be processed are less exposed to overheating. In addition, all modern Forstner drills with a diameter of more than 25 mm are available with teeth.
In addition to the listed modifications, there are Forstner drills with a removable tip. Such a tool reduces the risk of perforating through when drilling a blind hole in workpieces.
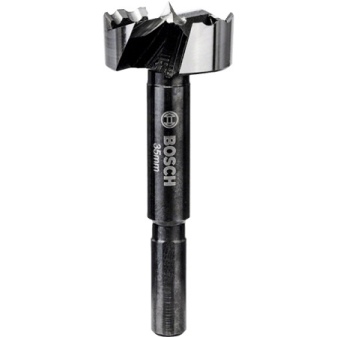

Dimensions (edit)
As a rule, the size range of a Forstner drill starts from a minimum diameter of 10 mm. Such sizes are not in great demand among craftsmen because of their specificity of application, when compared, for example, with the most common diameter of 35 mm, which is used when performing work on the installation of door hardware and locks. In hardware stores, you can easily find drills with a diameter of 50 and 55 mm, as well as 60 mm. It is noteworthy that diameters ranging from 15 to 26 mm have an 8 mm shank, while larger models of cutters with a working part diameter from 28 to 60 mm have a shank slightly larger and already 10 mm.


How to choose?
The choice of a Forstner cutter depends on the tasks to be performed with its help. In carpentry or in manufacturing, this is a frequently used tool, where different drill diameters are used, so for such intensive use it is advisable to have a complete set of the required dimensions in stock. As for domestic use, the drill is purchased for a specific task, then it is rarely used. In this case, there is no need to buy a set of expensive tools, since the costs may not be recouped.
To purchase a quality Forstner drill, you need to pay attention to several main features:
- the original model of the drill has small round holes in the center of the working part;
- the cutting blades of the cutter interrupt the annular rim only at two points opposite to each other;
- the blades of the original drill can only be sharpened by hand.


The original models of Forstner's drill are made only by the only American company in the world, Connecticut Valley Manufacturing. Here, each part of the tool structure is milled separately from a steel billet, and the alloy contains an admixture of carbon, while other manufacturers make each part of the drill by casting with the subsequent assembly of finished parts. A real Forstner cutter has a thicker cutting part than its counterparts, so such a tool is less susceptible to overheating and rotates faster, making it possible to work at high speeds of the power tool, while maintaining the quality of hole processing at the highest level.
In the process of choosing a Forstner cutter, it is necessary to pay attention to the appearance of the condition of the cutting edges. It often happens that manufacturers pack their products in opaque packaging. In such cases, it is impossible to consider and evaluate the details of the tool, so you run the risk of purchasing a low-quality product, which, when opening the package, may be with burrs, chips or deformation.
It is unrealistic to correct such significant shortcomings with the manual sharpening method, since the geometry of the drill structure will be violated, therefore, it is better to refuse to buy a product in an opaque package.


Terms of use
The use of a Forstner drill is straightforward. Taking the tool in hand, the centering protrusion is brought to the intended center of the future hole and the tip is slightly pressed into the thickness of the material. It is necessary to press in so that the annular cutting part of the drill lies flat on the working surface. Then you can start the work process, but start drilling at first at low drill speeds, gradually increasing the speed. The drills are designed to operate at a maximum of 1800 rpm. The basic rule of work during drilling is as follows: the larger the cutter size, the slower it should rotate. This low speed mode is necessary in order to keep the cutting edges of the tool from melting and blunting when it overheats.
Besides, at too high speeds, the probability of the drill breaking off the intended working area of drilling becomes more frequent. If you need to protect yourself in order to make a hole very accurately, at a given depth, it is best to use a cutter with a stop for this purpose. This device will stop the drill in time and protect the material from perforation, but you will have to work at low speeds. When drilling a blind hole in a thin-walled workpiece, experienced craftsmen recommend using 2 Forstner drills at once.They begin work first, having outlined the area of the working hole, and finish with another one, which has a sharp protrusion previously grinded. Thus, the cutters will not be able to cut the material as deep as a conventional drill.


How to sharpen?
In the process of work, any, even the highest quality, drill becomes dull. Original products can be sharpened by hand, and non-original counterparts can be sharpened on a grinder. When sharpening a Forstner cutter, specialists are guided by certain rules:
- the cutting part of the annular rim is not manually sharpened - this is done only on sharpening equipment;
- it is necessary to grind the cutters minimally so as not to change the geometry and proportions of their working surfaces;
- internal incisors are sharpened with a file or a grindstone.
High-quality but expensive products with a thin titanium coating do not require frequent dressing or sharpening and effectively last longer than their inexpensive counterparts made of conventional steel.
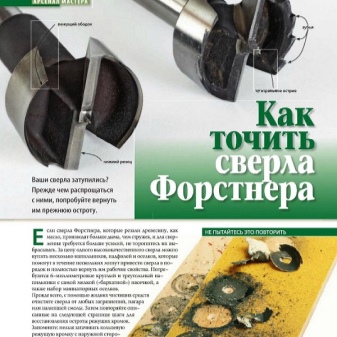

In the next video, you will find a review and testing of Forstner's Protool ZOBO drills.
The comment was sent successfully.