Sand-gravel mixture: features and scope
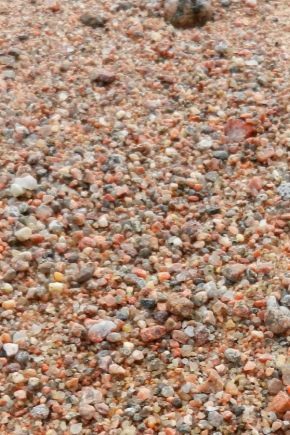
Sand and gravel mixture is one of the most common inorganic materials used in the construction industry. The composition of the material and the size of the fractions of its elements determine which variety the extracted mixture belongs to, what are its main functions, where it is more suitable for use.
Sand-gravel mixture is used in construction for filling in the lower layers of various substrates, for example, asphalt or other road surface, and for the manufacture of various mortars, for example, concrete with the addition of water.
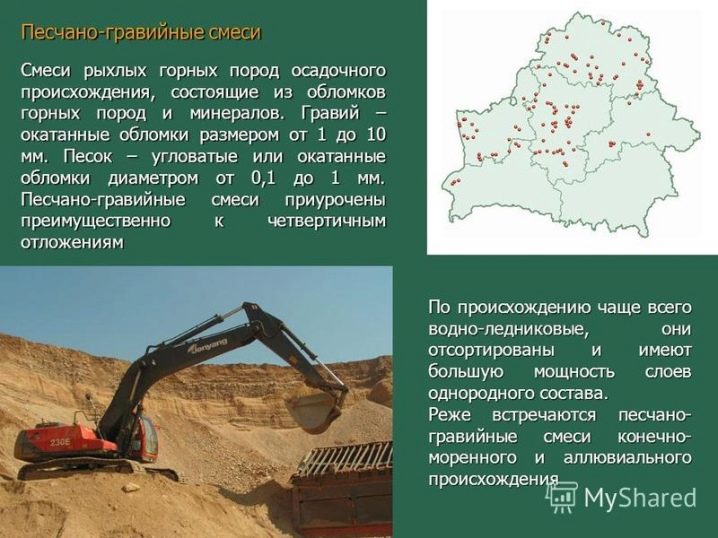
Peculiarities
This material is a versatile ingredient, that is, it can be used in different types of activities. Since its main components are natural materials (sand and gravel), this indicates that the sand and gravel mixture is an environmentally friendly product. Also, ASG can be stored for a long time - the shelf life of the material is absent.
The main storage condition is to keep the mixture in a dry place.
If moisture does get into the ASG, then when using it, a smaller amount of water is added (for example, when making concrete or cement), and when the sand-gravel mixture is needed only in dry form, then you will first have to dry it thoroughly.
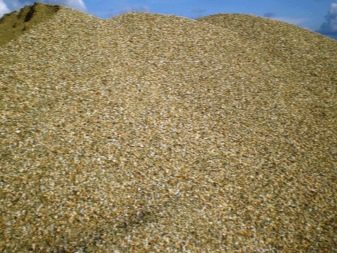
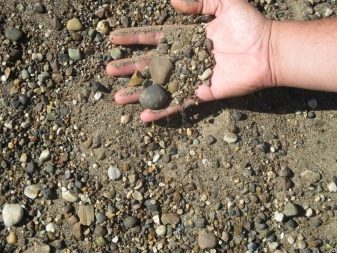
A high-quality sand and gravel mixture, due to the presence of gravel in the composition, should have good resistance to temperature extremes and not lose its strength. Another interesting feature of this material is that the remnants of the used mixture cannot be disposed of, but can later be used for its intended purpose (for example, when laying a path to the house or in the manufacture of concrete).
Natural sand and gravel mix is notable for its low cost, while the enriched ASG has a high price, but this is compensated by the durability and quality of buildings made of such an environmentally friendly material.
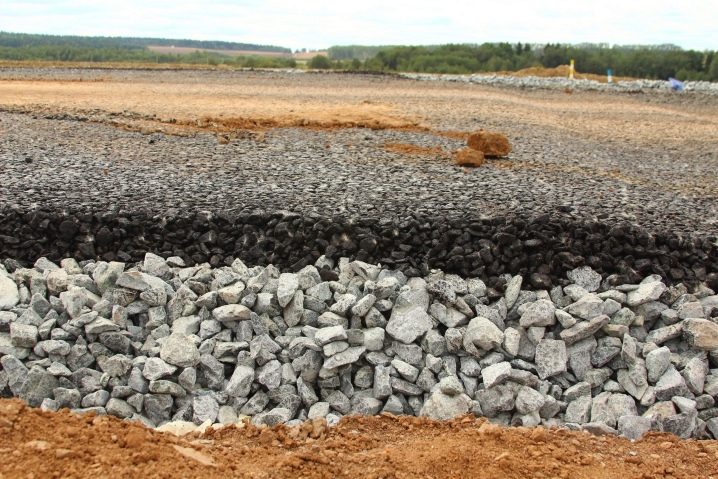
Specifications
When purchasing a sand and gravel mixture, you must pay attention to the following technical indicators:
- grain composition;
- the volume of content in the mixture of sand and gravel;
- grain size;
- impurity content;
- density;
- characteristics of sand and gravel.
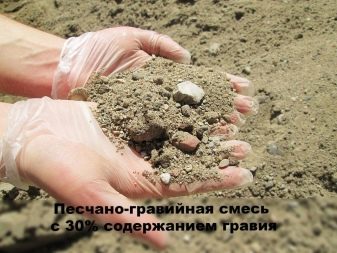
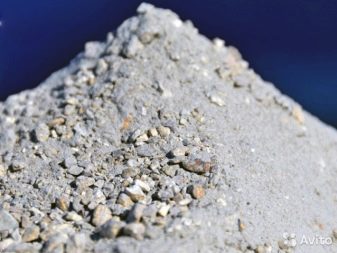
The technical characteristics of sand and gravel mixtures must comply with the accepted state standards. General information about sand and gravel mixtures can be found in GOST 23735-79, but there are also other regulatory documents regulating the technical characteristics of sand and gravel, for example, GOST 8736-93 and GOST 8267-93.
The minimum size of sand fractions in ASG is 0.16 mm, and gravel - 5 mm. The maximum value for sand according to the standards is 5 mm, and for gravel this value is 70 mm. It is also possible to order a mixture with a gravel size of 150 mm, but not more than this value.
The content of gravel grains in natural sand and gravel mixture is approximately 10-20% - this is an average value. The maximum amount reaches 90%, and the minimum is 10%. The content of various impurities (particles of silt, algae and other elements) in a natural ASG should be no more than 5%, and in an enriched one - no more than 3%.
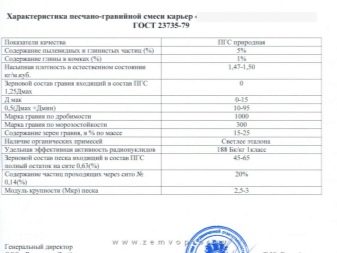
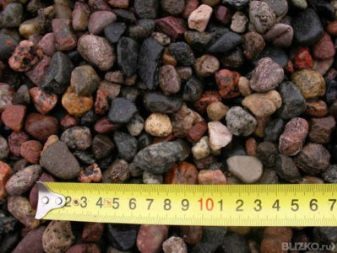
In the enriched ASG, the amount of gravel content is on average 65%, the clay content is minimal - 0.5%.
According to the percentage of gravel content in the enriched ASG, materials are classified into the following types:
- 15-25%;
- 35-50%;
- 50-65%;
- 65-75%.
Important characteristics of the material are also indicators of strength and frost resistance.On average, ASG should withstand 300-400 freeze-thaw cycles. Also, the sand and gravel composition cannot lose more than 10% of its mass. The strength of the material is influenced by the number of weak elements in the composition.
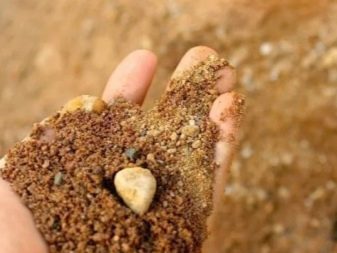
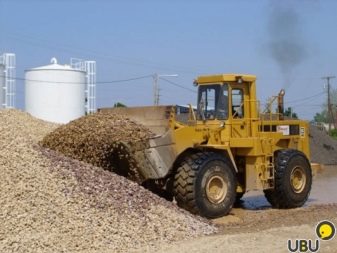
Gravel is classified into strength categories:
- M400;
- M600;
- M800;
- M1000.
Gravel of the M400 category is characterized by low strength, and M1000 - high strength. The average level of strength is present in gravel of categories M600 and M800. Also, the amount of weak elements in gravel of category M1000 should contain no more than 5%, and in all others - no more than 10%.
The density of the CGM is determined in order to find out which component is contained in the composition in greater quantities, and to determine the scope of the material. On average, the specific gravity of 1 m3 should be approximately 1.65 tons.
The higher the gravel content in the sand and gravel composition, the higher the level of material strength.
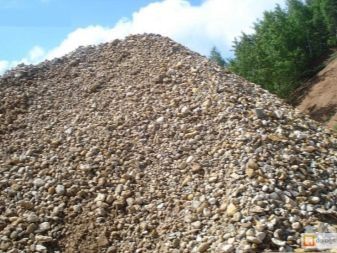
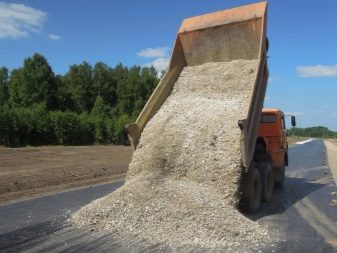
Not only the size of the sand is of great importance, but also its mineralogical composition, as well as the modulus of coarseness.
The average compaction coefficient of ASG is 1.2. This parameter may vary depending on the amount of gravel content and the method of compaction of the material.
The Aeff coefficient plays an important role. It stands for the coefficient of the total specific activity efficiency of natural radionuclides and is available for the enriched ASG. This coefficient means the rate of radioactivity.
Sand and gravel mixtures are divided into three safety classes:
- less than 370 Bq / kg;
- from 371 Bq / kg to 740 Bq / kg;
- from 741 Bq / kg to 1500 Bq / kg.
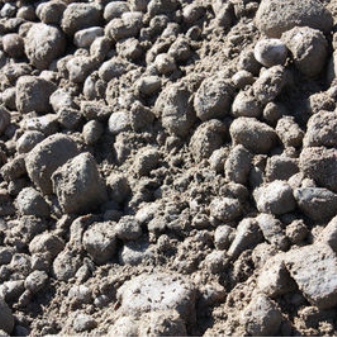
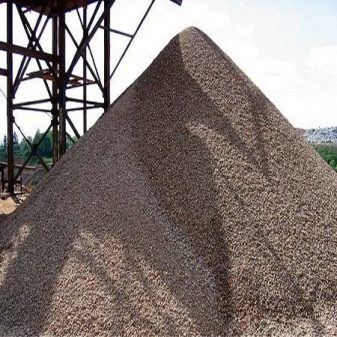
The safety class also depends on which field of application this or that ASG is suitable for. The first class is used for small construction activities, such as manufacturing products or renovating a building. The second class is used in the construction of automobile coatings in cities and villages, as well as for the construction of houses. The third safety class is involved in the construction of various high-traffic areas (these include sports and playgrounds) and large highways.
The enriched sand and gravel mixture is practically not subject to deformation.
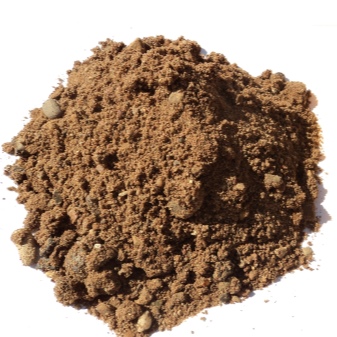
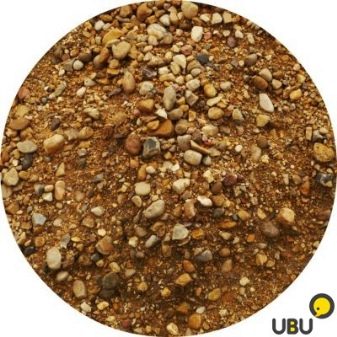
Views
There are two main types of sand and gravel mixtures:
- natural (PGS);
- enriched (OPGS).
Their main difference is that the enriched sand and gravel mixture cannot be found in nature - it is obtained after artificial processing and the addition of a large amount of gravel.
Natural sand and gravel mixture is mined in quarries or from the bottom of rivers and seas. According to the place of origin, it is divided into three types:
- mountain ravine;
- lake-river;
- sea.
The difference between these types of mixture lies not only in the place of its extraction, but also in the field of further application, the amount of the volumetric content of the main elements, their size and even shape.
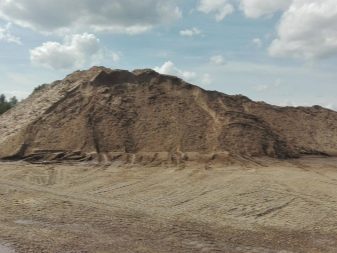
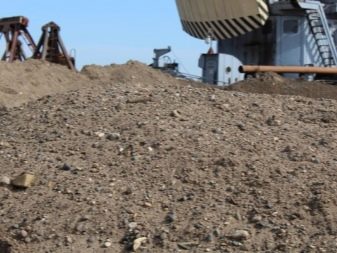
The main features of natural sand and gravel mixtures:
- the shape of gravel particles - the mountain-ravine mixture has the most pointed corners, and they are absent in the marine ASG (smooth rounded surface);
- composition - the minimum amount of clay, dust and other polluting elements is contained in the sea mixture, and in the mountain-ravine they prevail in large quantities.
The lake-river sand-gravel mixture is distinguished by intermediate characteristics between the sea and mountain-ravine ASG. It also contains silt or dust, but in small quantities, and its corners have a slightly rounded shape.
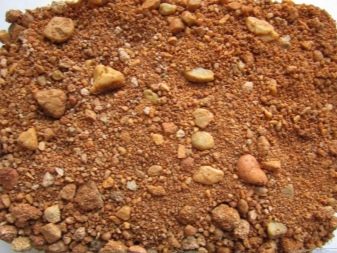
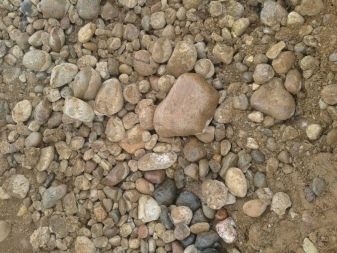
In OPGS, gravel or sand can be excluded from the composition, and gravel crushed stone can be added instead. Crushed gravel is the same gravel, but in a processed form. This material is obtained by crushing more than half of the original component and has sharp corners and roughness.
Crushed gravel increases the adhesion of building compounds and is perfect for the construction of asphalt concrete.
Crushed stone compositions (sand-crushed stone mixtures - PShchS) are divided according to the fraction of particles into the following varieties:
- C12 - up to 10 mm;
- C2 - up to 20 mm;
- C4 and C5 - up to 80 mm;
- C6 - up to 40 mm.
Crushed rock formulations have the same characteristics and features as gravel formulations. Most often, a sand-crushed stone mixture with a fraction of 80 mm (C4 and C5) is used in construction, since this type provides good strength and stability.
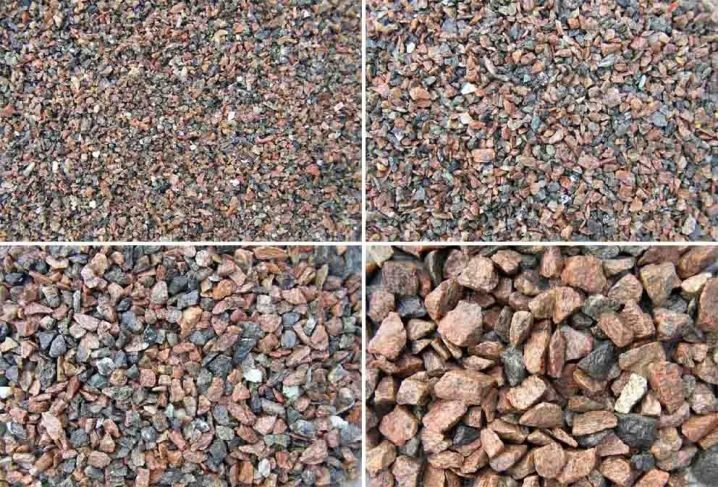
Scope of application
The most common types of construction in which sand and gravel mixtures are used are:
- road;
- housing;
- industrial.
Sand and gravel mixtures are widely used in construction for backfilling pits and trenches, leveling the surface, building roads and laying a drainage layer, producing concrete or cement, when laying communications, dumping foundations for various sites. Also used in the construction of the base of the railway bed and landscaping. This affordable natural material is also involved in the construction of one-story and multi-storey buildings (up to five floors), laying the foundation.
The sand and gravel mixture as the main element of the road surface ensures the resistance of the road to mechanical stress and performs water-repellent functions.
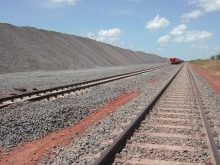
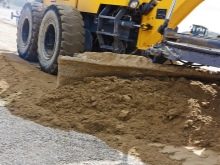
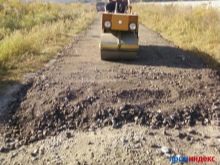
In the manufacture of concrete (or reinforced concrete), in order to exclude the possibility of the formation of empty spaces in the structure, it is the enriched ASG that is used. Its fractions of various sizes perfectly fill the voids and thus determine the reliability and stability of structures. The enriched sand and gravel mixture allows the production of concrete of several grades.
The most common type of sand and gravel mixture is ASG with a gravel content of 70%. This mixture is highly durable and reliable; it is used in all types of construction. Natural ASG is used much less often, since, due to the content of clay and impurities, its strength properties are underestimated, but it is ideal for backfilling trenches or pits due to its ability to absorb moisture.
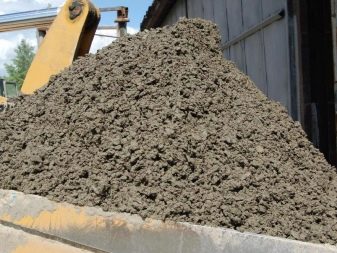
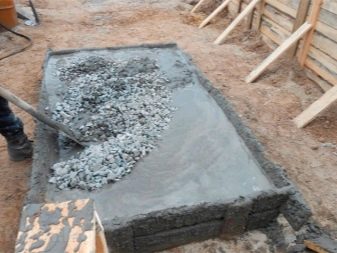
Most often, natural ASG is used for arranging the entrance to the garage, pipelines and other communications, building a drainage layer, garden paths and arranging home gardens. The enriched train is involved in the construction of high-traffic highways and houses.
How to make a foundation cushion from a sand and gravel mixture, see below.
The comment was sent successfully.