Features and varieties of sandwich panel grippers

Recently, the popularity of advanced technologies for the installation of wall and roof panels has been growing at a record pace. Such building materials are distinguished by ease of use, manufacturability and high heat capacity. And one of the important points is the varieties and design features of various grippers for sandwich panels, which are widely used in modern construction.

What it is?
Initially, it is worth clarifying that the considered segments of wall and roof structures do not have their own fasteners that could be used during their transfer and installation. Taking into account all the features of the material and the nuances of the construction technology itself, it can be concluded that one cannot do without specialized mechanisms. And we mean reliable grippers for sandwich panels.

Strong ropes and slings, as well as special mechanisms, are designed to comfortably and quickly deliver the panels to the required height in the appropriate position. It is important to take into account that all such devices must ensure the safety of the material. In addition, the labor intensity of the panel slinging itself is significantly reduced.

At its core, any grippers are a specially designed holding device based on elements made of high quality and most durable materials. All mechanical devices have a rubber base. This ensures a reliable fixation of the movable and installed plate. In parallel, the risk of damage to the panel is minimized. In other words, using the described equipment, you can quickly and as safely as possible perform all the necessary work.

Features of the device and basic principles of operation
Taking into account the nuances of installation and the requirements imposed on it, the equipment used must comply with certain standards.

In the situation with mechanical devices, we are talking about structures, the basis of which is a metal frame with an eyelet for fastening rings. The outer wall of the device has holes in which threaded bushings are located. On the opposite side there is a pad made of thick, corrugated rubber.

With the help of a threaded connection, a handle is fixed, which also has a rubber pad. Due to its rotation, the sandwich panel is fixed. A similar device is located on the other side of the structure to be installed.
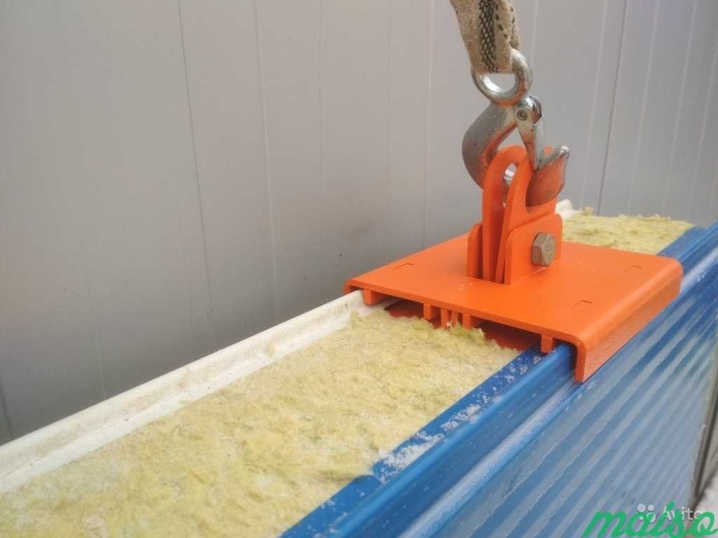
In mechanisms equipped with levers, the fixing unit is located on a lowering part called a rocker arm. In such situations, a counterweight (thrust) is mandatory on the opposite side. Fixation and retention of the movable plate occurs due to the tension of the lever.

Vacuum grippers are equipped with an additional unit - a drive, and are installed on a crane hook. It is important to remember that devices belonging to this category should be located exclusively in the center of the panel. When the suction cups come into contact with the profile sheet of the plate, the piston of the device moves downward, thereby activating the removal of air from the cylinder through the control valve.As soon as all the air has been expelled and the suction cup is fully connected to the surface of the panel, the chain link will immediately begin to descend until the switch is pressed.
As a result of all the described manipulations, the air outlet is blocked, and therefore, the pressure in the cylinder increases to the maximum. It must be remembered that the clamping force of the suction cups is determined by the weight of the mounted elements of the wall and roof structures. Stable retention of the gripper suction cups is ensured by an equilibrium vacuum installed in the cylinder of the device. And they are peeled off from the surface of the plate when all the above operations are performed in the reverse order.

Varieties
All work related to the transfer and subsequent installation of multi-layer plates using lifting and transport equipment must be carried out in strict accordance with the current regulations. In particular, the lifting of slabs (according to GOST, length - 12 m, thickness - 0.250 m) is carried out only in the longitudinal position when gripping by the sidewalls. It is worth noting that the latter are not stiff. Taking into account such nuances, the grips should:
- completely eliminate material deformation;
- ensure the reliability of fixation;
- provide for the minimum indicators of labor intensity when performing work.
Taking into account the current standards and regulations, several types of devices have been developed. Today, panels are transported and installed using textile and synthetic slings (ropes), mechanical devices, and vacuum suction cups. Taking into account all the nuances, the last two options are optimal. It is important that from a financial point of view, mechanical models will be much more profitable. At the same time, vacuum grippers provide a uniform clamping, and, consequently, a more reliable and safe fixation for the surface of the plates.

Textile slings
The so-called cable slinging of panels today is the most affordable, but at the same time the least practical option. One of the most important points is that in factories producing multi-layer panels, they are packed flat, that is, horizontally, several panels in a package. In such a situation, the separation of the slabs for subsequent slinging will be quite laborious. It should also be borne in mind that due to insufficient rigidity, bending of the panel is possible, which, as a rule, cannot be leveled.

Slinging when using ropes of the 2SK series is possible only in the following situations:
- if there are at least two pairs of slings;
- the angle of the guy is no more than 60 degrees;
- the fasteners are located on the linear traverse of the lifting mechanism;
- rubber gaskets must be placed under the slings;
- slings are installed in increments of no more than 1.5 meters.

With such restrictions, it will be almost impossible to lift a panel longer than 4 meters. This requires a crane with special equipment.
Taking into account all the nuances, a number of advantages of slinging can still be distinguished, namely:
- minimum weight;
- maximum flexibility;
- no danger of damage to the coating of the panels;
- affordable cost;
- the ability to use at almost any temperature.
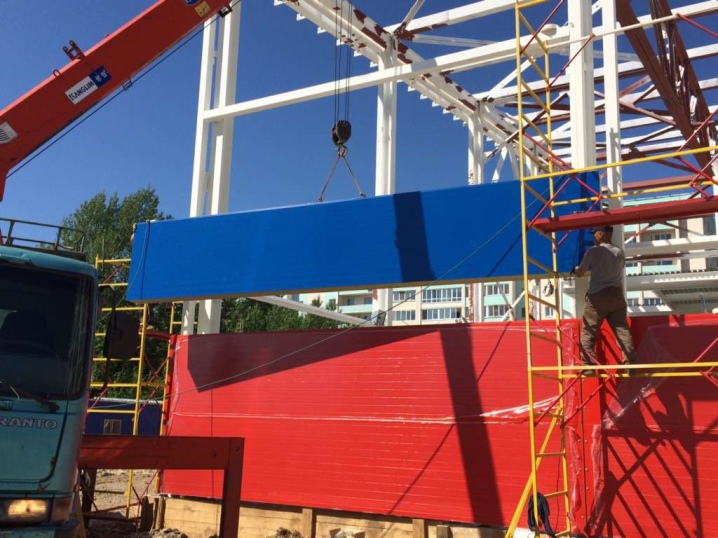
One of the main disadvantages of textile and synthetic products is the high probability of damage to the threads on the sharp edges of the boards. In addition, it should be borne in mind that most often the panels are located flat on the objects. This leads to problems during slinging and un-slinging.

Mechanical
At the moment, when working with the described panel elements, several types of mechanical equipment are widely used. Initially, it is worth considering designs such as clamps. These devices provide not only a secure fit, but also the ability to adjust the compression, which minimizes the risk of damage to surfaces.It is worth noting that with a relatively low weight, such clamps allow you to work with slabs, the thickness of which varies within 5-20 cm, and the weight reaches 200 kg.

The next type is structural and clamping models, consisting of a rigid main frame, which is fixed, and a screw assembly. As a result of the rotation of the movable part, the distance between the pressing jaws changes. In the desired position in relation to each other, they are fixed with a screw or a lever.
Devices, which provide for fixing panels "in a lock", are successfully used when transferring them. It is important to take into account that one of the fastening elements in such situations are the locks of the plates themselves, that is, a "thorn in a groove" connection occurs. At the preparatory stage, the plates are placed vertically on special spacers. This type of holding device is used both for transportation and for fixing in a horizontal position.


Another type is mechanical structures, the use of which provides for through drilling of plates. It is important to take into account that drilling accuracy will be the determining factor. In this case, the fixing pin must be perpendicular to the surface. This type of equipment is most often used in situations where vertical mounting is performed. The holes made for the pins after the completion of the work are closed with shaped or fasteners.
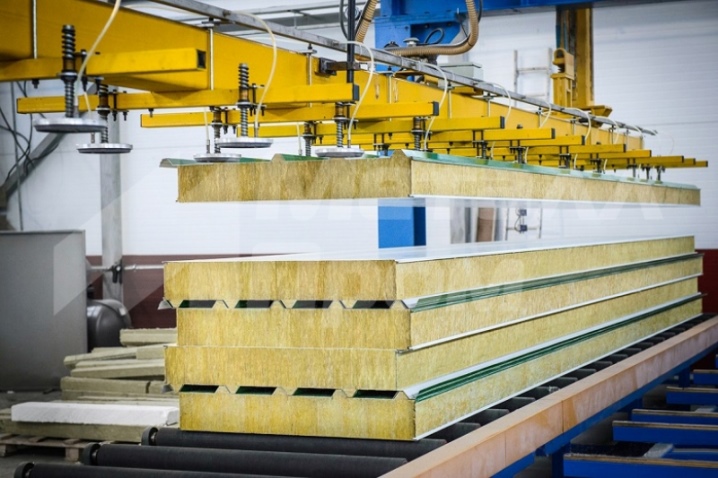
Vacuum
This category of fixing devices is the most technologically advanced, since it is equipped with a special drive system. At the same time, only these devices provide the most reliable fixation of panels with minimal risk of damage. The uniformity of the clamp greatly facilitates the lifting, tilting and installation of the plates itself. For operations with mounted segments of the future design, one device located strictly in the center is enough.
All holding devices of this type have the following structural elements:
- piston and cylinder;
- suction cups;
- chain-type traction;
- vacuum chambers;
- device responsible for regulating pressure (valve).

The mechanisms of this category are characterized by a whole list of undeniable competitive advantages. So, during installation, the following points will be the most important.
- The suction cups guarantee maximum safety for the surfaces of the profiled sheets. They do not even leave traces at the points of contact.
- When carrying and holding the slabs during installation, the possibility of displacement is completely eliminated.
- Maximum reliability of fixation is ensured.
- Due to the operational properties of the grippers, the speed of work is significantly increased (on average, panels are installed per day, the total area of which is 50-800 "squares"). The panels are taken out of the stack and immediately assembled without any preparation, which significantly saves time.
- 2-3 people are enough to carry out the work.
- The devices are distinguished by their versatility.
- The suspended slab can be rotated as desired during installation.
- It is possible to work with slabs up to 26 meters long.
- Vacuum grippers differ from other models in maximum ease of use.
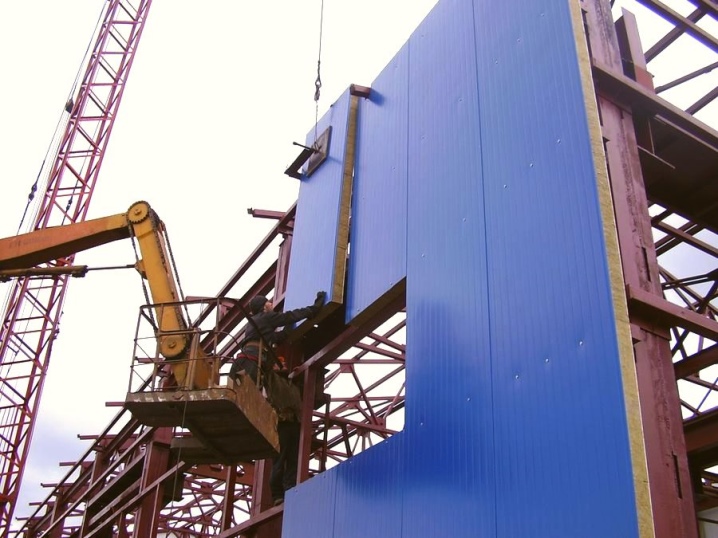
The only significant drawback of such structures is the high cost. If mechanical structures will cost 4-8.5 thousand rubles, then you will have to pay up to 280 thousand for a vacuum gripper.

Safety rules for operation
As already noted, the fixing devices for the considered wall panels are devices that significantly simplify and speed up installation work. In principle, you can do without such structures, but in this case, the risk of damage to the building material increases many times over. But regardless of the type of devices used, certain rules must be observed when moving and installing plates.

In particular, before starting work it is required:
- identify the most dangerous areas;
- put up fences at all openings;
- install warning labels;
- if necessary, ensure the availability of reliable forests;
- provide sufficient illumination of the site;
- check the stability of the lifting mechanisms;
- check all rigging devices under double load.
Among other things, it should be remembered that from a safety point of view, one of the determining factors is the correct selection of personnel. Fitters must have knowledge, practical experience and adequate physical fitness.

The video shows one of the most effective gripping methods for installing sandwich panels.
The comment was sent successfully.