What is an F-shaped profile and what is it for?
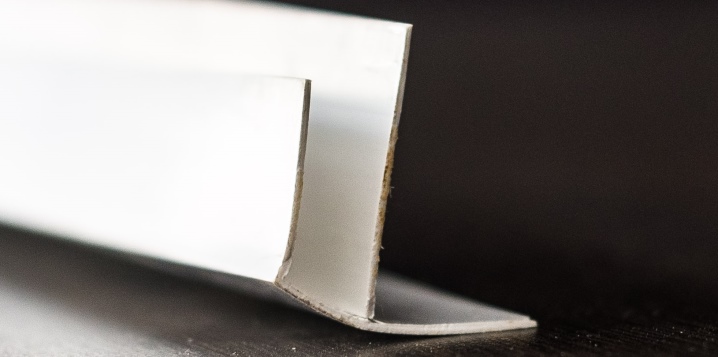
When erecting various building structures, all kinds of profile models are used. These devices allow high-quality processing of structures in such a way that unnecessary sloppy parts are hidden. Today we will talk about the features of F-shaped profiles, as well as where they found their application.
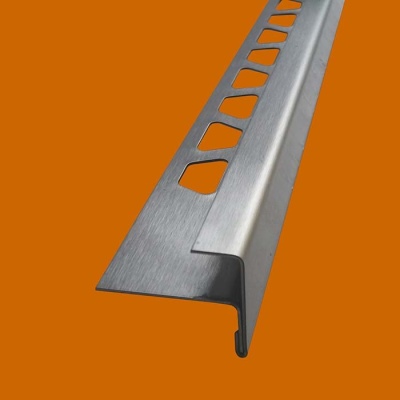
What it is?
F-shaped profiles are special metal platbands, equipped with a groove for the panel, they are designed to decorate slopes. Some models are made from different types of plastics.
These structures have excellent UV resistance and can be installed by yourself without the help of specialists. Such profiles are quite elastic, the material can be easily bent if necessary, and at the same time it will not break or crumble.
F-shaped profiles are reusable. They can be quickly removed and reinstalled. In addition, such products have an aesthetic appearance. They allow you to give the structures a complete look, secure them securely and tightly.
Such decorative elements will not turn yellow and lose their original appearance for a long time. In addition, they are equipped with a special semicircular shank, which makes it possible to fix the element even on curved surfaces.
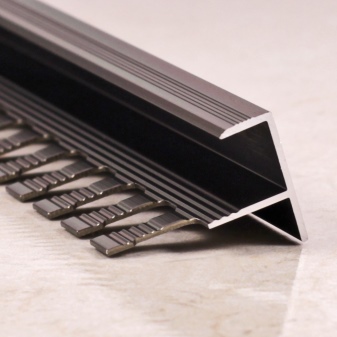
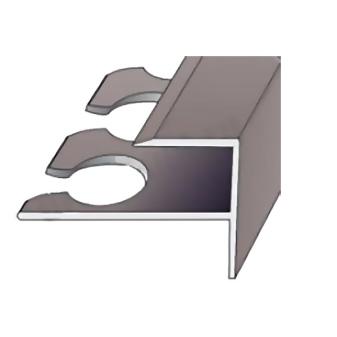
After cutting such strips, chips and cracks will not form on their surface. These parts will be able to serve as long as possible; if necessary, they can be easily changed to new ones on their own.
Types and sizes
These types of building profiles can be classified into separate groups depending on what material they are made of. Most often there are several types of models.
-
Aluminum. Such metal products are particularly durable. They will be able to serve for a long time without breakage and deformation. In addition, the profiles made of aluminum are lightweight, which makes installation as easy as possible. They are resistant to fire, the aluminum structure is almost impossible to set on fire. It should be noted that the material is absolutely safe for humans. A special anodized coating is most often applied to the surface of aluminum parts, which also significantly extends their service life.
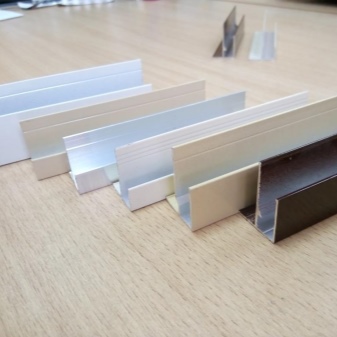
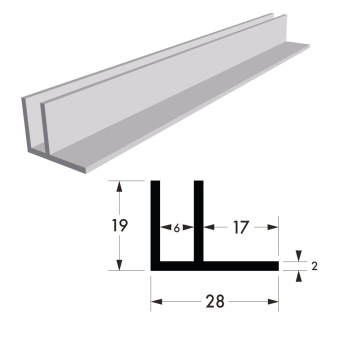
- Brass. These varieties have a fairly high strength, corrosion resistance, flexibility. They are easy to install, they are often fixed with silicone sealant. Brass products allow you to create the most accurate fit.
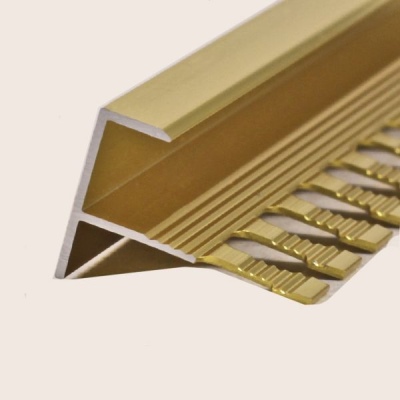
- Steel. As a rule, stainless steel is used in the manufacture of such parts. It boasts a high level of quality, durability and increased wear resistance. Products made of this metal have a relatively low weight; over time, a layer of corrosion will not form on their surface.
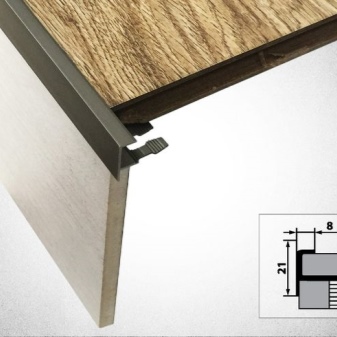
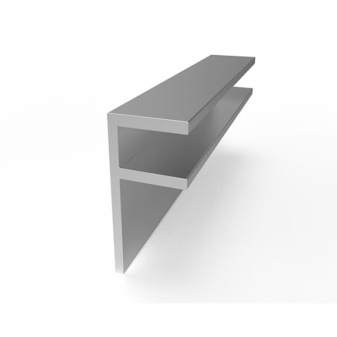
- Plastic. It is plastic profiles that are most often used in the design of window openings. They, as a rule, have a low thermal conductivity, good sound insulation, resistance to various atmospheric influences. In addition, plastic models also boast durability and relatively low cost.
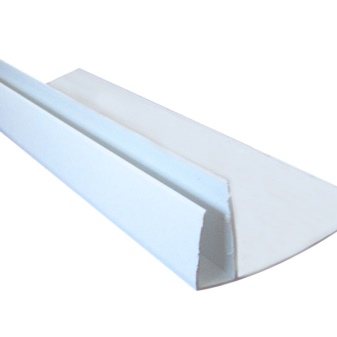
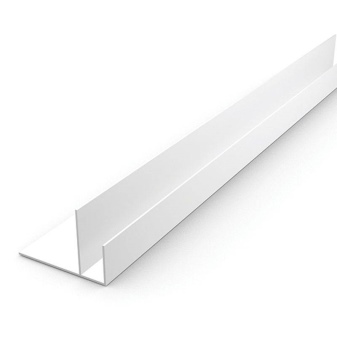
Such profiles can be divided into separate groups depending on what design features they have.
-
Finite. This type of profile is used for reliable and durable fixing of the slope to the wall, as well as simply for finishing window openings. Products can be painted in a variety of colors, but more often there are models of white, brown colors, there are also black samples. Most often they are made from high quality plastic. These structures can easily withstand exposure to ultraviolet radiation, sudden temperature changes. As a rule, they are attached with special screws.
-
Laminated. This type is a standard F-shaped building profile, while its surface is covered with a special decorative application. The outer film of such structures is characterized by high strength and wear resistance. It can be applied to the surface of products with powder dyes.
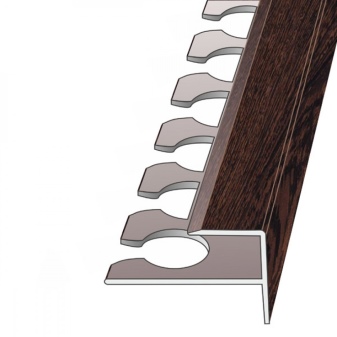
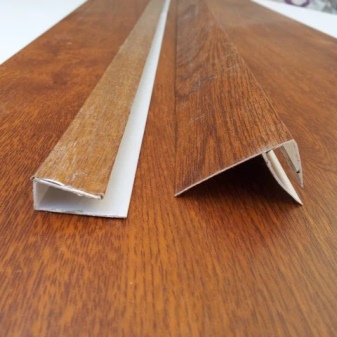
In hardware stores, buyers can see a wide variety of these profiles. They all come in different sizes. Mostly there are samples with the following values: 3000x10 mm, 2700x12 mm, 4000x30 mm.
The width of these decorative designs can vary considerably. You can often see such products with a value of 8 mm, 10 mm, 45 mm. Wider versions are also available: 60 mm, 65 mm, 70 mm.
Application area
F-shaped profiles can be used in many areas of construction. But most often they are used for finishing window structures. At the same time, the products will make it possible to ensure the most tight adhesion of panels to wall coverings.
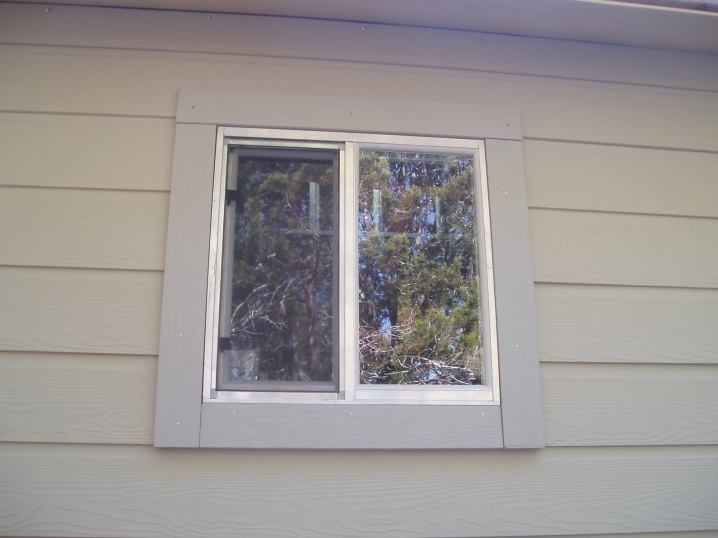
These profiles are often used in the design of door structures. Moreover, their installation does not require the use of a special adhesive. With the help of such products, it is easy to make an even and neat joining of even different materials.
Sometimes these elements are taken as a starting profile. In this case, one of the sides will be tightly pressed against the wall, and the other - against the slope.
F-shaped models can be used when installing siding. In this case, they will close the end, if the surface on it is not finished with material. Thus, it turns out to make a much more beautiful and neat design.
Details of this type may well be suitable for decking. This material is used in the construction of verandas and terraces in suburban areas. The profile will allow you to neatly hide all the flaws, make the finished structure more beautiful.
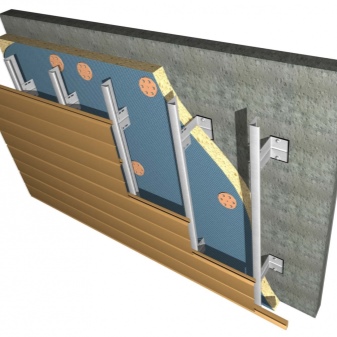
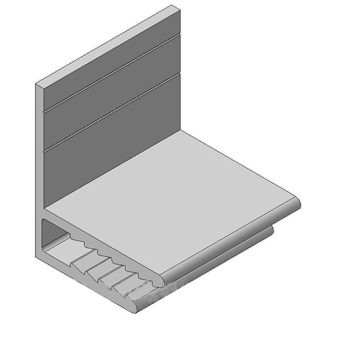
Sometimes parts are used for sandwich panels, which are a durable three-layer building material with an insulating layer, for the construction of structures made of plasterboard or gypsum vinyl, polycarbonate.
F-shaped metal models can be purchased for the most winding staircases. After all, they are easy to bend, giving the necessary smooth shape, while they will not break. To give a wavy shape, a special metal bending machine is often used, it allows you to process the structure right at the installation site.
Installation methods
Let's consider the simplest method of fixing F-shaped profiles when finishing slopes. First you need to fix the starting part. Installation is carried out with the back side using special self-tapping screws. The element is fastened along the edges of the frame.
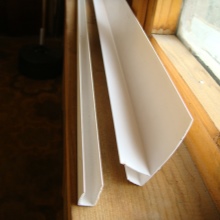
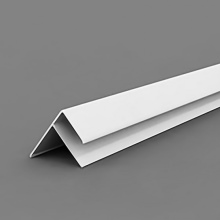
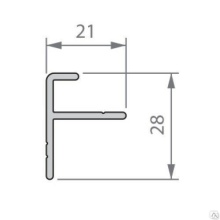
The main thing is to properly cut the structure. This should be done in such a way that there are no significant defects in the corners at the joints. After that, you can start installing PVC panels. First, overlap the side slopes, while inserting an eraser into the bar. At this stage, we must not forget about laying an additional insulation layer.
At the final stage, another profile is taken. It is trimmed a little, adjusting to the desired length. After that, the part is attached to the plastic part with grooves.
The installation method is often used, in which a special liquid glue is used. If, as a result, after installation, cracks formed in the structure, they can be removed with the help of silicone sealant.
After installation, the part will appear as a small and neat corner that hides the joints while ensuring a secure connection of different or identical building materials.
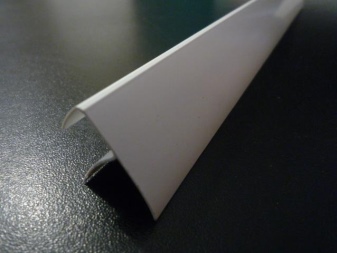
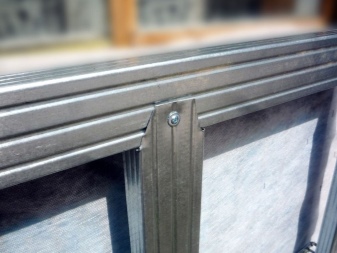
The comment was sent successfully.