Features of metal scaffolding
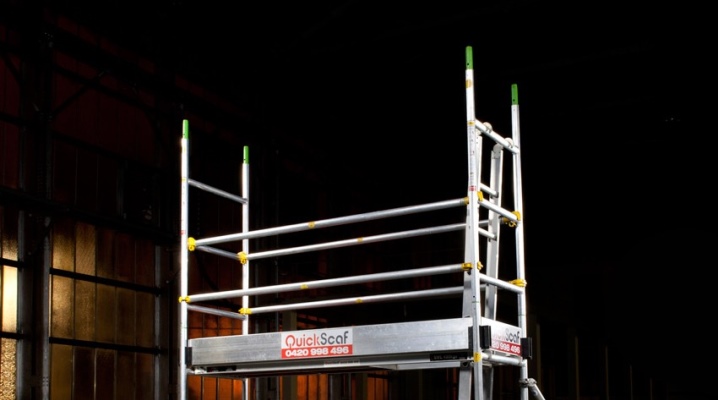
The peculiarities of metal scaffolding must always be taken into account during construction and repair work. There is a difference between collapsible aluminum and stainless steel structures. You should definitely know how much they weigh, how they are installed, how the scaffold flooring is mounted.
Advantages and disadvantages
Traditionally, scaffolding for construction is made of wood. Such a solution is well worked out and seems to be time-tested. However, metal scaffolding is gradually entering the market. It is necessary to figure out what they are good or bad, and whether, in general, it is worth buying such a product. Wood is cheap, and by and large they use waste recycled material.
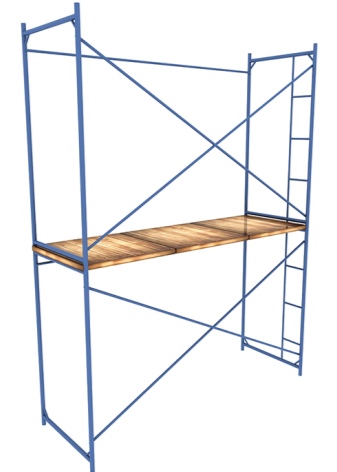
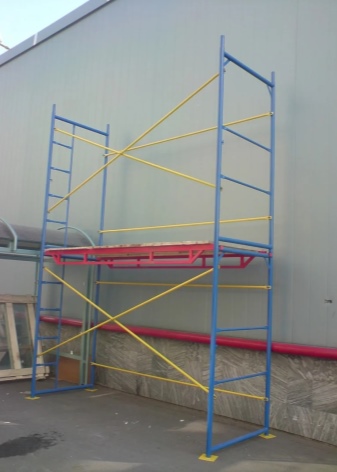
But this is where the advantages of wood over metal end. Steel structures, of course, weigh more. But they:
-
can be used repeatedly;
-
resistant to moisture ingress;
-
do not dry out even in the most intense heat;
-
are distinguished by increased bearing capacity;
-
are equally applicable in large and private construction;
-
ease of installation and disassembly;
-
suitability for work on buildings of any geometric shape, even very intricate ones;
-
ease of storage;
-
ease of transportation (we can confidently say that such models are very convenient and fully justify all investments).
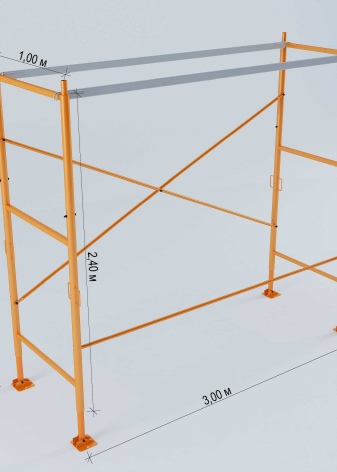
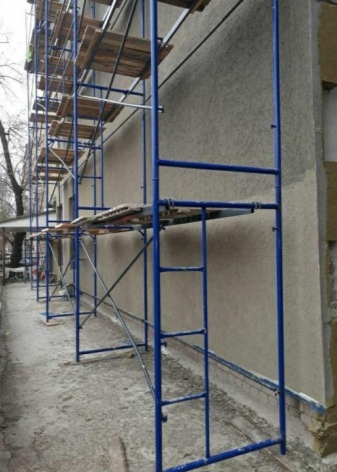
Description of species
Many consumers choose metal scaffolding on wheels. Their other name is a tower-tour. Similar designs can be used both inside buildings and outside. The wheelbase allows you to conveniently move the support structure to the places where you need it first. In addition, the absence of the need for installation work on the building itself and, in general, a minimum of preparatory procedures are pleasant.
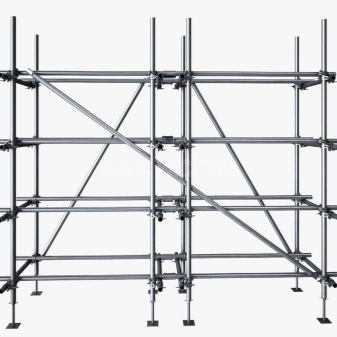
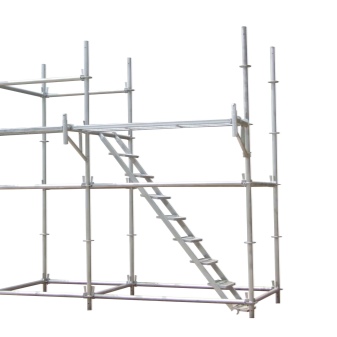
But other types of metal scaffolding are still popular. So, collapsible frame products, as their name implies, are formed by frames, between which are located horizontally and diagonally connecting elements. In fact, the scheme is reproduced, typical for ordinary wooden scaffolding. It is possible to assemble the structure in a short time; no special devices are needed for this. The delivery set includes:
-
side frames with a ladder embedded in them;
-
persistent shoes;
-
connecting elements of horizontal and vertical types.
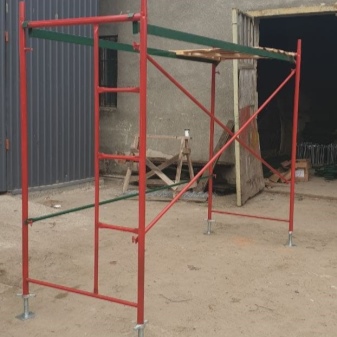
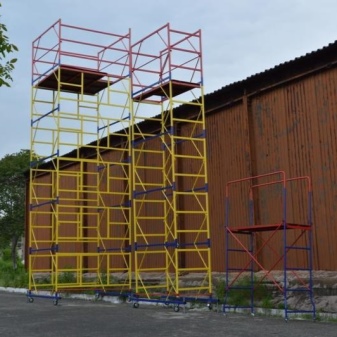
Frame design allows you to reduce the cost of assembly. The components themselves are also inexpensive. To join parts, flag locks are used. The load standard reaches 200 kg per 1 sq. m.Bricks can be laid at a height of 25 m, and facing up to a maximum of 40 m.
But before proceeding to the characteristics of other types of scaffolding, you need to thoroughly disassemble what metal they should be made of. Almost all builders in Russia prefer stainless steel structures. They:
-
durable (within the normal endurance of steel);
-
exploited very widely;
-
stable and can perform the assigned tasks even in difficult outdoor conditions;
-
look aesthetically pleasing;
-
safe;
-
reliable;
-
can be repaired.
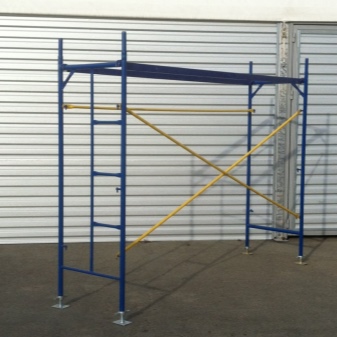
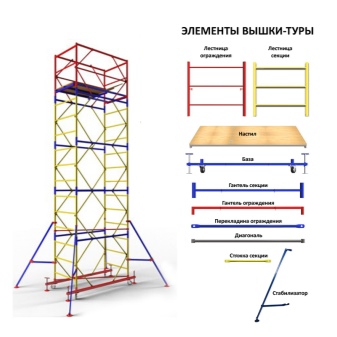
Aluminum models:
-
better corrosion resistance;
-
do not generate sparks (which is very important when storing carbide and other hazardous, easily flammable materials nearby);
-
serve for a long time;
-
weigh less than steel counterparts;
-
just like them, they can be repaired;
-
somewhat less durable;
-
are relatively expensive.
In the so-called Vishnev forests, the main frames are placed horizontally. They are responsible for tying the uprights and supporting the decking. There are no diagonal contact points. Can be used both inside and outside the building. The highest height of the Vishnev forests is 20 m, and the specific load is 250 kg per 1 sq. m.
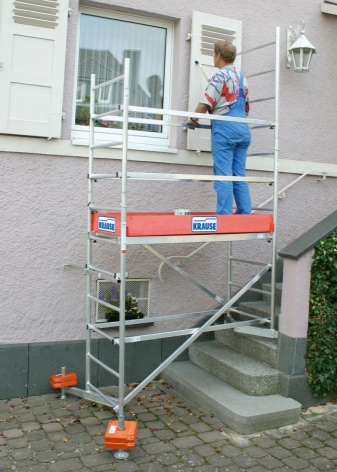
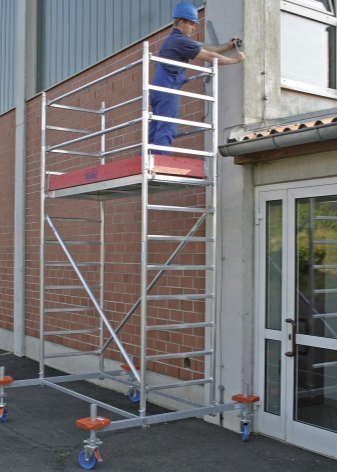
Wedge versions get their name from the way they are fastened. As you might guess, steel wedges are used for it, driven by an ordinary hammer. The permissible load of one "square" in such a scheme is twice as high as in Vishnev's design. This is very important if you plan to equip a large building and carry out large-scale works. The lifting height reaches 120 m, and the wedge-shaped scaffolding is also used by shipbuilders and building restorers.
When characterizing clamp assemblies, attention is drawn primarily to their increased complexity. The lifting height reaches 80 m. The load does not exceed 250 kg per 1 sq. M. m. Work on a complex facade is allowed.

You can also work on large areas. In the assembly process, along with deaf clamps, reversible clamps are used.
Last but not least, pin-type scaffolds deserve mention. Their horizontal blocks are equipped with welded pins. Such structures are inserted into tubes, which are attached with a welding machine to vertical posts. From the bottom, the racks are laid in the shoes. Bricks and blocks can be laid at a height of up to 50 m, and walls can be finished at a height of up to 100 m.
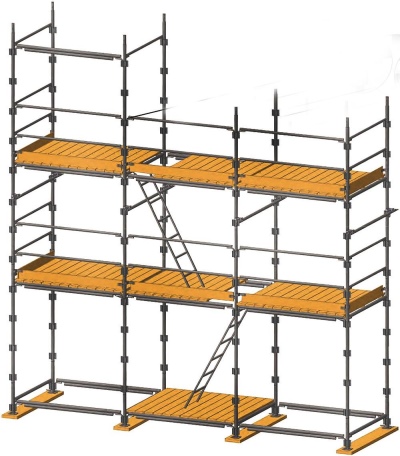
Installation
The scaffolding is installed without any problems. They start by checking the quality of all designs. Any cracks, kinks or curves in the part mean that parts need to be replaced. The assembly begins on a pre-rammed site, which is equipped with drainage communications. The shoes are installed on top of the lining board.
Farther:
-
supports are attached to the shoes;
-
are engaged in the first level racks;
-
connect them with diagonal and transom blocks;
-
control the accuracy using plumb lines or laser levels;
-
reinforced frames or steel beams are mounted on top of the racks;
-
use girders to fasten wooden scaffolds;
-
are engaged in second-level rack parts;
-
fix diagonal, barrier structures and screeds;
-
carry out the installation of additional trusses or girder beams;
-
they mount the floorings along the girders;
-
equip enclosing elements;
-
repeat this procedure on each tier (disassembly is no more difficult, and should be done just as carefully).
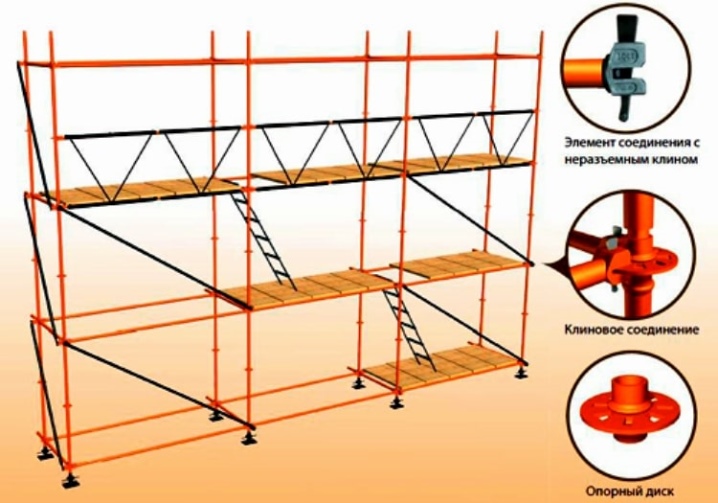
The comment was sent successfully.