How to make scaffolding with your own hands?

Scaffolding is a very useful structure that is rarely needed for walling or finishing work. It is quite possible to build such structures with your own hands. In this article, we will figure out how to do it correctly.


What are they?
Before proceeding to consider the step-by-step instructions for the manufacture of scaffolding, it is advisable to understand what such structures are.
In a general sense, scaffolding is a special frame structure that is assembled from several sections and component elements. The parameters of such components are standardized in accordance with international standards.
Scaffolding is essential to safeguard the work processes that builders face.


Varieties
Scaffolding comes in several different types. Each of them has its own design and features. Let's take a closer look at the most popular examples that are used for construction, finishing and restoration work.
- Wedge... In such structures, the constituent elements are connected to each other by means of a special wedge fixation. These are very reliable and high quality constructions. They are able to withstand impressive loads. In operation, wedge scaffolding turns out to be convenient and practical.


- Framed... The main part of such structures is a rigid frame. Most often, such a structure is used in conditions of painting and plastering works. The frame in the considered structures is connected with horizontal posts and diagonal connecting components.

- Pin... In such forests, the main connecting node is the pin. Pin structures are very popular among builders because they are extremely easy to assemble and can be disassembled right on the construction site. It often takes 1 or 2 days to build this.


- Clamp... If the building on which construction work is planned has a complicated structure, then clamp scaffolding will be an excellent solution. The fastening method in these models is professional.


Fundamental rules
Scaffolding is different. Their design features largely depend on the work for which they are applied.... For example, for the installation of materials that are lightweight, high bearing capacity is not so important, because there will not be heavy loads here. For such work, special attached scaffolds or structures in the form of a kind of envelopes are usually made. Finishing work in relation to gables or simple external finishing can be carried out using ordinary construction "goats" - flooring is laid out on their rungs.


Regardless of what kind of construction scaffolding means, and for what work they were prepared, they must necessarily be manufactured in accordance with a number of important rules. Only if this condition is met can one expect that the structure will turn out to be reliable and strong. Let's take a closer look at these rules.
- Scaffolding must be built in accordance with the loads that will be supplied to them.For example, if these are options made of wood, and the builder will install heavy materials, then it is advisable to use thick and maximally strong boards to create scaffolding.
- The materials from which the scaffolding will be built should in no case be of low quality, broken, rotten, with traces of mold and other defects. A sufficiently strong and safe structure will definitely not work out of such raw materials.
- A craftsman who builds scaffolding with his own hands may not pay attention to the attractiveness of the structure in question. You should focus on its reliability and safety, rather than appearance - in this case, it is not so important.
- Forests must be made resilient and strong. If the structure sways or collapses, to be unstable, then it will be simply dangerous to work on it. Such constructions cannot be called safe.
Even if the scaffolding is planned to be made from suitable materials at hand, the master still needs to remember about all the listed rules. The main thing to pay attention to is the level of stability and safety of the structure.


How to make wood scaffolding?
Very often scaffolding is made from wood components. This is a one-stop solution that many builders look to. Such structures have their own advantages and disadvantages. Let's look at the benefits first.
- Timber scaffolding is easy and fast to assemble. To dock all the prefabricated components of the construction, you do not need a welding machine or other similar equipment at all, for which you need the appropriate skills to work. Almost every craftsman who has worked with a hammer at least once can easily cope with the work.
- As blanks, it is allowed to use the most ordinary boards or bars. The tower can even be constructed from scrap materials. The materials are only subject to requirements regarding their reliability and condition. As mentioned above, rotten wood will not work for scaffolding.
- After the completion of all construction work, the frame of the wooden scaffolding is simply disassembled, and the remaining parts can be used for other purposes. The same steel pipes from which scaffolding is made are more difficult to adapt on the farm.

Wooden scaffolding has certain disadvantages. Let's get acquainted with them.
- Such structures are characterized by greater flexibility in comparison with metal ones. The flooring laid out on the frame base will bend under the feet of the builder.
- Metal is a more durable material, therefore, to add the missing stability to the wooden bars, the structure has to be made more massive.
- Wooden scaffolding always turns out to be fire hazardous. They are highly flammable and keep the flame alive. Even after processing wood with special fire retardants (protective compounds), the material can quickly catch fire.
- All components in wooden structures are fastened with nails and screws. These fasteners noticeably weaken the edges of the scaffolding, therefore it is strongly not recommended to exploit the array more than 2 times.
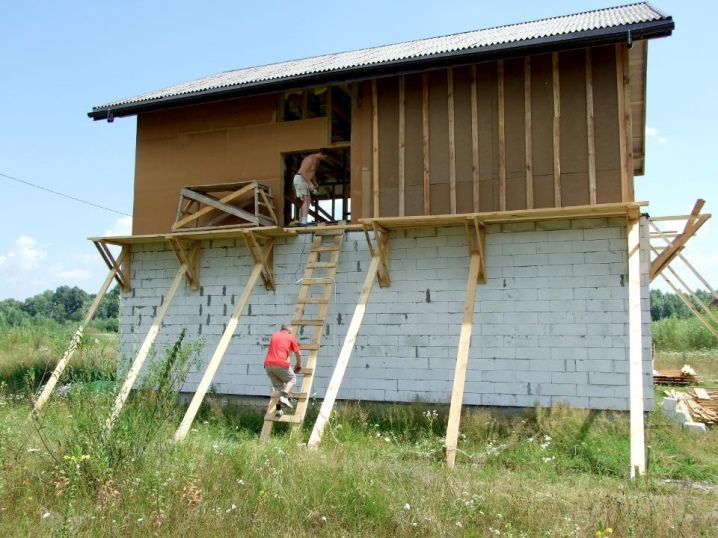
Wood scaffolding can be built with your own hands. Let us consider in detail what stages the construction of such a structure consists of.
Drawing and dimensions
The first thing that the master will need to do is to draw up detailed drawings of the future structure, indicating all the necessary dimensions on them. You can draw up a plan for a future design on your own, or you can use ready-made schemes, especially if the master has not previously encountered such matters. In this drawing, you can see the following marks with dimensions:
- maximum height - 6 m;
- the distance between the supporting parts is allowed in the range from 2.0 to 2.5 m;
- working platform width - 1 m.
Having at hand a detailed drawing of the future structure, it will be much easier to build high-quality and safe scaffolding without making serious mistakes.

Step by step diagram
When all the drawings and materials are ready, the master can proceed directly to the manufacture of wooden scaffolding. This process consists of several stages, none of which can be neglected. Let us consider in detail the step-by-step scheme for the manufacture of a structure.
- On the leveled surface of the ground, it is necessary to lay out a pair of supporting parts (best of all from a bar or board "fifty"). They must be laid parallel and with equal height.
- The supporting components should be fastened horizontally by means of crossbars, on which the platform will subsequently be laid for further work.
- The resulting 2 fastened structures must be installed in a vertical position against each other, and then connected diagonally and horizontally by means of transverse elements.
- Planks are laid and installed on horizontal transverse components. It is they who will perform the function of flooring in the future.
- To secure the scaffolding, you will need to install strong supports on the sides.
- A cranial bar is nailed onto the support bases, which will act as the railing of the structure.
- At the final stage of work, a ladder is installed and securely fixed, thanks to which workers will be able to climb the scaffolding made.




Manufacturing from shaped pipes
Excellent reliability and stability can be demonstrated by competently designed scaffolding, which is based on metal. Such self-made structures are more difficult to construct than wooden specimens, but they also turn out to be more practical in use.


Preparation of parts
Before proceeding with the construction of homemade products from shaped pipes, the master must take into account that their very design will be the same as in the situation with wooden options. To assemble a section of such scaffolding, you need to prepare the following materials:
- pipe for supporting bases - 4 pcs. 1.5 m each;
- profiled pipe for the manufacture of crossbars - 4 pcs. 1 m each;
- thin-walled pipe with a diameter of 20 mm - 4 pcs. 2 m each for a screed on a horizontal plane;
- profiled pipe with parameters 35x35 mm - 8 pcs. 10 cm each (will be used as adapters);
- steel plate, which will be needed for the manufacture of thrust bearings, with dimensions of 10x10 cm, 3 mm thick - 4 pcs.;
- to connect the cross members to the frame diagonally, you need to prepare 10 bolts with washers and nuts.
Having prepared all the listed details of the future installation, you can proceed to its direct assembly.


Assembly
Metal scaffolding, like wood, can be assembled on your own. Self-made structures from a professional pipe turn out to be strong and as reliable as possible, if you strictly follow the instructions for their assembly.
- You will need to prepare an OSB sheet shield. To it, using clamps, attach the supporting parts of the scaffolding.
- To the support bases, you need to weld the transverse components horizontally.
- On the top end of the racks, you will need to properly weld adapters, the size of which is 5 cm.
- Having lifted the struts together with the transverse components from the shield, they should be turned over 90 degrees. Then they are again laid out back on the shield and fastened to it with clamps.
- The edge sections and the middle of the profile pipe, which is prepared for stretching diagonally, are flattened, and then a slot is drilled in it to install the bolts.
- 2 diagonally directed crossbeams are correctly tightened in the central part with a bolt, then applied to the posts and find the appropriate area where drilling is required.
- The crossbeams of the structure are fixed on the racks by means of bolts, and then tightened with nuts.
- Holes are drilled on the handrails and support bases with a drill, and then bolted together.
- To the point of the base of the pipes, thrust bearings are welded.
- The constructed and assembled structure is exposed strictly vertically.
- Planks are laid out on the crossbars located on the sides. They will act as the basis of the working area of the forests.
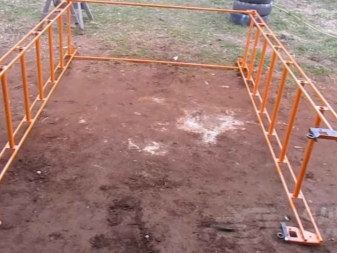

Scaffolding made of metal is as durable as possible and can be designed for heavy loads. From a metal profile it is possible to build a complicated homemade product with a variable flooring height or a collapsible model of scaffolding. It is easier to make such products on your own if the master has experience working with a welding machine.

Helpful hints and tips
Before starting work on the independent production of high-quality scaffolding, it is best for the master to arm himself with some useful tips and recommendations that will allow him not to face unnecessary problems and shortcomings.
- If a decision is made to make wood products, and the fasteners will be carried out by means of nails, then it is better to drill all the necessary holes in advance so that the boards do not prick during installation.

- Metal frame structures that remain after the completion of installation or finishing work can be simply disassembled, or can be rented out.

- If the scaffolding, constructed from a profile pipe, turned out to be not high enough, it will be possible to easily increase them in height by mounting additional tiers.
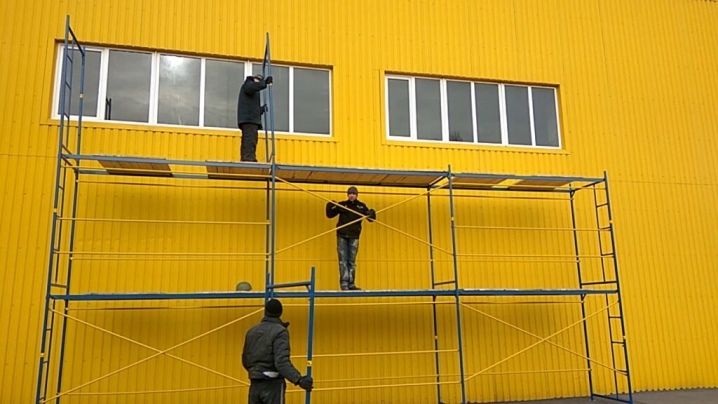
- If, during the assembly of scaffolding from wood, it is required to install 2 or more sections, then they can be connected to each other by means of a wide board. It just needs to be nailed onto the adjacent support bases.

- Wooden scaffolding can be built more rigid and strong. For such purposes, it is recommended to additionally strengthen them by installing stops and braces.

- So that the finished products do not fall from the support base on which repair, installation or finishing work is carried out, they should be propped up with boards or bars, 1 end of which is nailed to the racks, and 2 ends are buried directly into the ground.

- When assembling the scaffolding, it is recommended to install high-quality anodized self-tapping screws. If the structure turns out to be reliable and correct, it is recommended to play it safe a little and hammer a couple of nails into each of the available connections. If it is scary to damage the wood due to such manipulations, you should put trimmings of thin wooden boards under the nails, and on a long span, use solid boards, but with a smaller thickness.

- So that ready-made home-made scaffolding does not begin to fall on the base wall, it is recommended to construct cross-members in their device with an outlet that is about 25 cm. It is better to fix the racks at a distance of 150-250 mm in relation to each other.
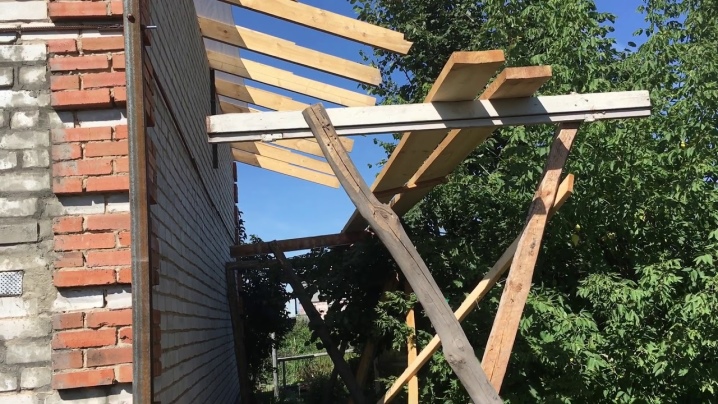
- All details in the construction of scaffolding must be secured with high quality, conscientiously. If some of the fasteners turn out to be too weak or of poor quality, then the structure itself will turn out to be not only inconvenient, but also dangerous.
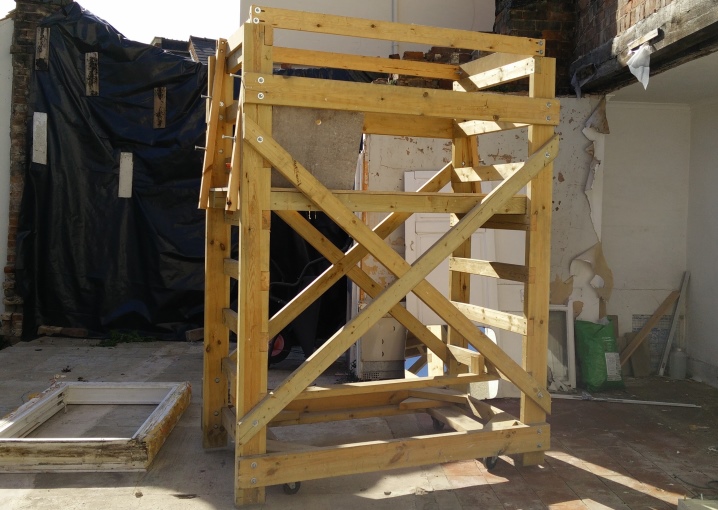
Homemade scaffolding is relatively easy to make. But if you have never encountered such work or are afraid to make serious mistakes, it is better not to take risks and purchase ready-made structures or use the service of professionals.
How to make wooden scaffolding with your own hands, see below.
The comment was sent successfully.