How to make a do-it-yourself epoxy table?
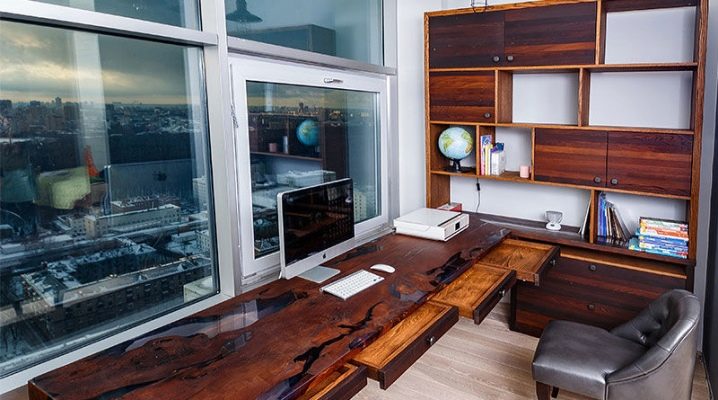
In the modern design of rooms, extraordinary and exclusive interior items are increasingly used, capable of focusing on themselves all the attention of the people present in the room. This original interior solution includes tables decorated with epoxy resin.
You can do this interesting thing with your own hands, turning an ordinary piece of furniture into a genuine work of art.
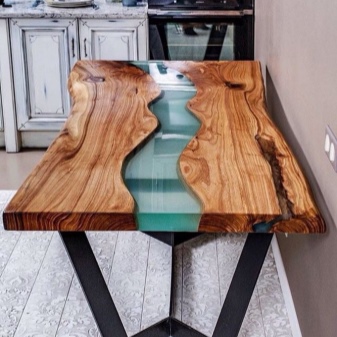
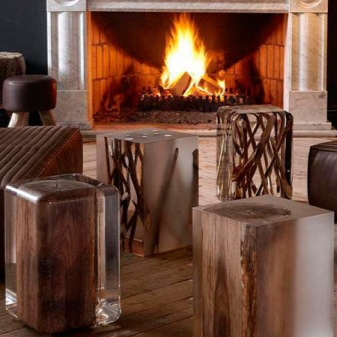
Properties
In the production of furniture, epoxy resins are not used in their pure form, since the magical qualities of epoxy are manifested as a result of its contact with a special hardener. By changing the ratio of these two parts to be joined, you can get a composition of different consistency. Depending on the purpose for which it will be used, it can be:
- liquid essence,
- stringy or rubbery substance;
- solid;
- high-strength base.
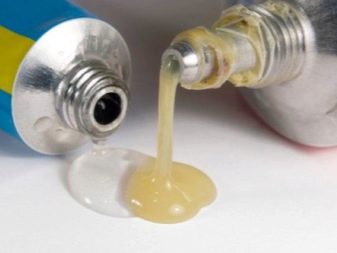
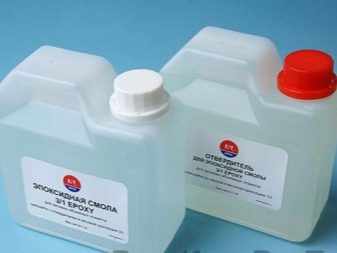
The process of making any furniture with decor using epoxy resin involves coating the wooden base with this polymer and thoroughly polishing the product after the resin has hardened, as a result, you will get a product with high wear resistance. The general properties of the entire composition will depend on the correct ratio of ingredients. The wrong amount of hardener can significantly reduce the strength of the finished product, as well as its resistance to the environment and household products. Therefore, it is so important when preparing a mixture for work to comply with the ratios recommended by the polymer manufacturer, most often these indicators are 1: 1.
According to the method of use, epoxy can be hot cured or cold cured. When creating pieces of furniture at home, the second type is most often used.
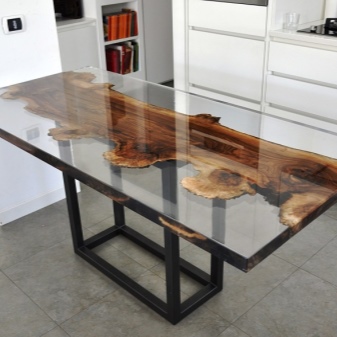
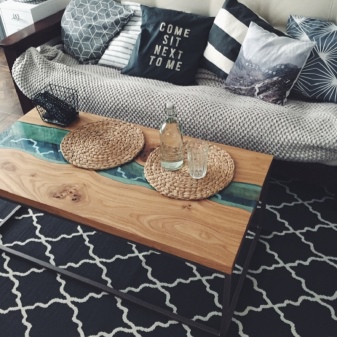
Advantages and disadvantages
Compared to conventional natural wood tables, epoxy treated tables have a number of advantages:
- the resin composition, when dried, practically does not shrink, holds its shape well, retains its original color, does not deform and is not subject to mechanical damage;
- the exclusivity of each product and limitless design options;
- the ability to use various additional materials for decoration (coins, tree cuts, shells, stones, starfish, etc.);
- the ability to add multi-colored dyes to the mixture, including phosphorescent paints;

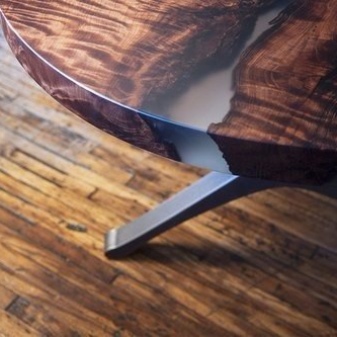
- impermeability to moisture and dampness;
- excellent tolerance to cleaning chemicals.
The main disadvantage of these tables is the very high cost of the product. To cover one copy, depending on the size and shape of the product, it can take up to several tens of liters of polymer substance. Another possible unpleasant drawback is the presence of air bubbles, which are formed in the epoxy mixture as a result of non-compliance with instructions and technologies during production.
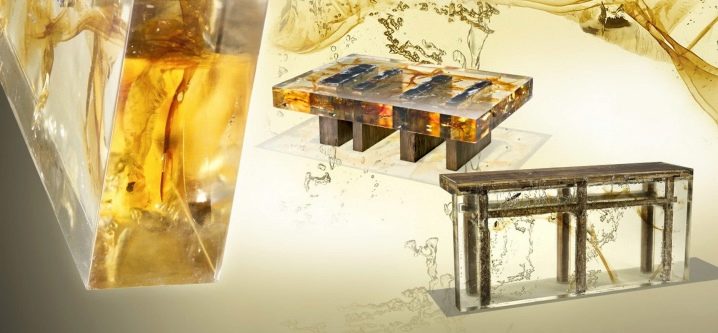
Manufacturing process
The very first and one of the most important steps in preparing a wooden structure for epoxy resin casting is the thorough removal of dust and all other contaminants from the wood surface. After that, the surface of the table, which will be poured, must be primed. If this is not done, then the resin, absorbed into the porous wood, forms air bubbles, which will ruin the appearance of the product.
Only after the preparation stage is completed, the required amount of a mixture of epoxy resin and hardener is prepared. At this stage, the most important thing is strict adherence to the proportions indicated in the instructions for use. Depending on the chosen design, dyes or additional decorative materials can be added to the finished mixture. Next, the resulting mixture is applied to the prepared wooden surface.
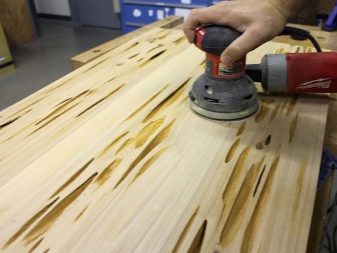
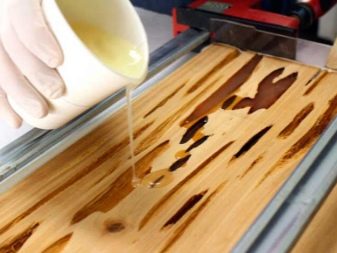
If a certain design from additional materials is conceived on the tabletop, then they must be placed on the table surface even before pouring. Moreover, light materials, such as wine corks or shells, must first be glued to the surface in accordance with the intended pattern. It is necessary, so that during pouring the mixture they do not float, thus turning a thoughtful composition into a messy and uninteresting structure. If unwanted air bubbles appear during the filling process, they can be removed with a construction hair dryer, directing a stream of hot air to the problem area.
The mixture will begin to set in fifteen minutes, but the final stage, namely, the grinding of the product, can be started only after the resin has completely hardened. It is advisable to keep the product for a week, since after this period it is already completely stable and will be ready for use.
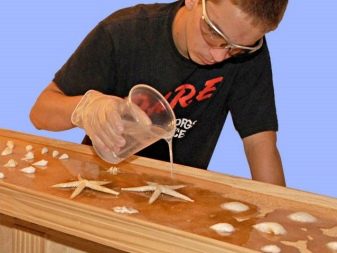
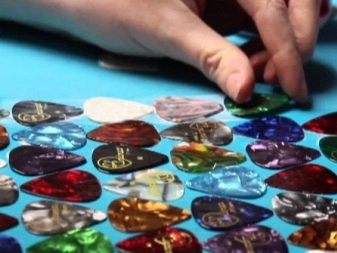
After sanding, it is advisable to cover the product in several layers with a protective varnish. This will prevent the release of toxic substances into the atmosphere, which in small quantities may be contained in resin compositions.
Variety of options
To create a table with an original tabletop decorated with epoxy resin, you can take absolutely any tree species, including a variety of debris, saw cuts, chips and even sawdust, as long as everything, even the smallest particles of the future tabletop, are thoroughly dried. Old and rough wood looks amazing in epoxy resin. For decoration, you can also successfully use sea and river shells, pebbles, dry herbs and flowers, coins, and other inclusions that can give the product a special originality or a certain theme. And by mixing luminescent dyes with epoxy resin, you will create a magical glow effect.
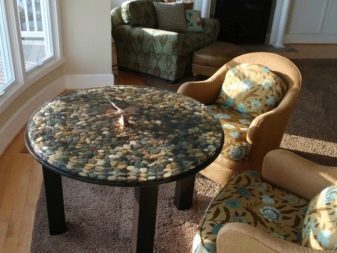
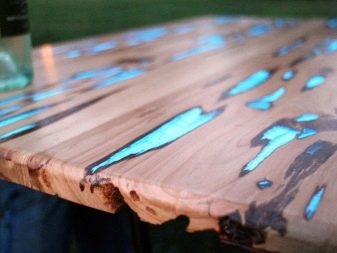
A tree eaten by bark beetles or damaged by damp looks very unusual in resin. Natural damage, filled with epoxy with the addition of dye or luminous paint, can create unrealistically beautiful cosmic patterns on the countertop. All kinds of holes, cracks and paths in the wood can be created artificially, creating your own pattern. All small holes are filled with the prepared mortar using a construction trowel. After hardening, remove excess resin using a sander.
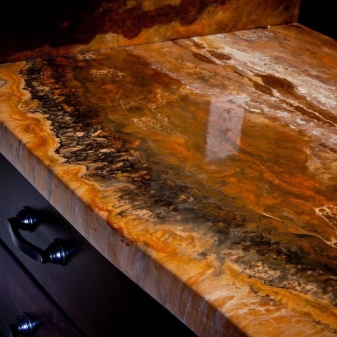
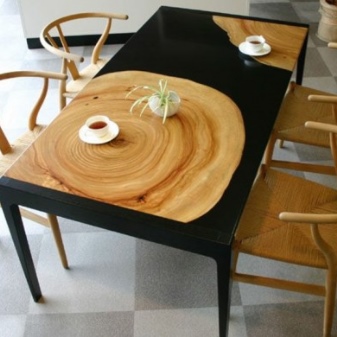
The process of making a tabletop using the pouring method is the most expensive and time consuming, and also requires special care in work. It is used in the manufacture of countertops with attachments, as well as to create original designs with fantastic ideas and unusual solutions. For example, a famous American designer Greg Klassen, which creates original models of tables with "natural landscapes". The "river" or "lake" frozen in the tabletops of his amazing tables amaze with their grandeur and incredible beauty.
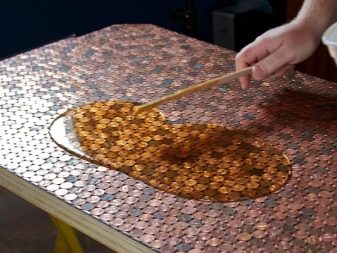
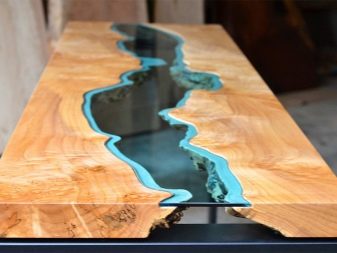
For information on how to make a wooden table with a river from epoxy resin with your own hands, see the next video.
The comment was sent successfully.