How to check the washing machine motor?

Often the cause of a washing machine breakdown is engine problems. Without giving out the declared drum revolutions or having failed altogether, the washing machine is subject to a reassembly of the engine or drive by means of which the drum rotates.
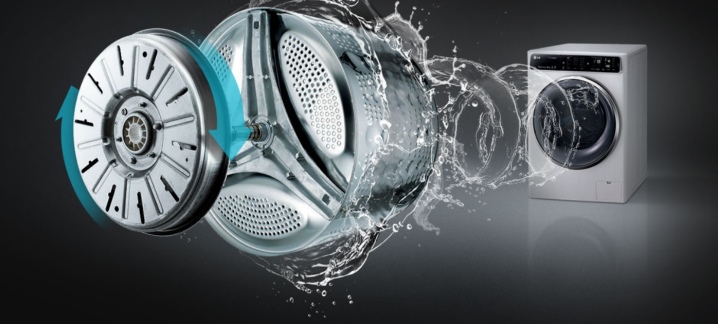
Types of devices to check
In addition to the standard set of tools (pliers, a set of screwdrivers and wrenches), you will need an electrical device that performs a "continuity" of the motor.
Multimeter
Previously, a multimeter was called an avometer - it was a dial gauge that measures resistance, voltage and current. Today dial gauges are almost completely gone from the market - with the exception of miniature, modern versions, which are problematic to find. They gave way to digital counterparts, which allow you to check diodes, capacitors, inductors and windings, and even the health of transistors.
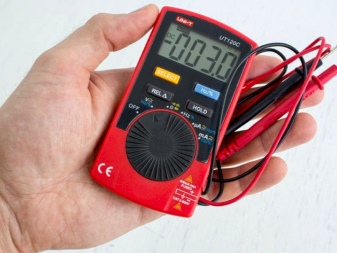
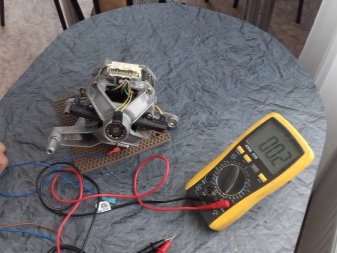
Tester
The same as a multimeter, but it can be made independently - from any pointer galvanometer. To carry out measurements, the tester switches to the resistance measurement mode (values in the sector with the designations Ohm and kOhm).
The device received the name "dialing" - for the buzzer mode: when the resistance is below 200 Ohm, the buzzer is triggered.
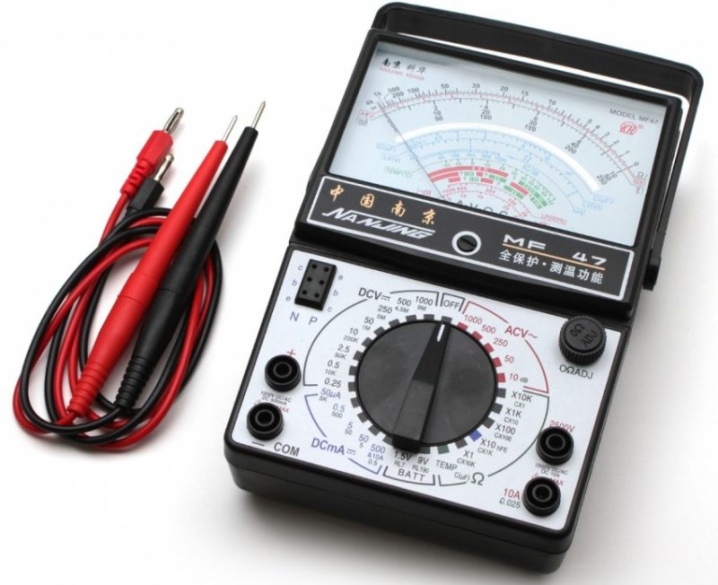
Troubleshooting
Before repairing an engine at home, check which of the three types of motors is used in your washing machine.
Asynchronous
Obsolete type. Despite its simplicity, magnets on the rotor and stator windings, without rings and brushes, are ousted from the market of modern household appliances for their low power output and impressive dimensions. He found application only among users as a generator - the assembled installation can operate for 30 years or more without repair. As a consumer, he is useless: he gives out half as much energy as he takes from the power grid, the rest is spent on losses in work.
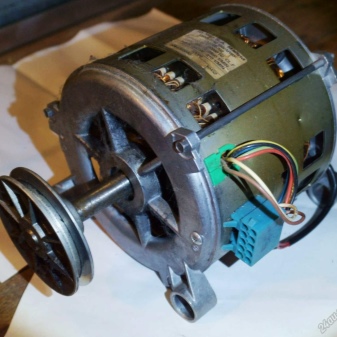
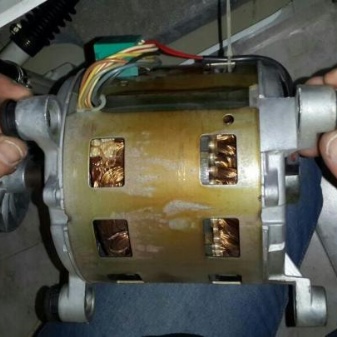
Its improved version is a ten-winding stepper motor, which requires a pulse driver board. Low efficiency has been eliminated in the stepper motor - the "shagovik" has a very strong thrust (moments of the torque generated by the sequential supply of current pulses to different coils).
But such a scheme is not used in automatic washing machines - the revolutions are too high, a powerful high-frequency driver for tens of kilohertz clock frequency would be required.
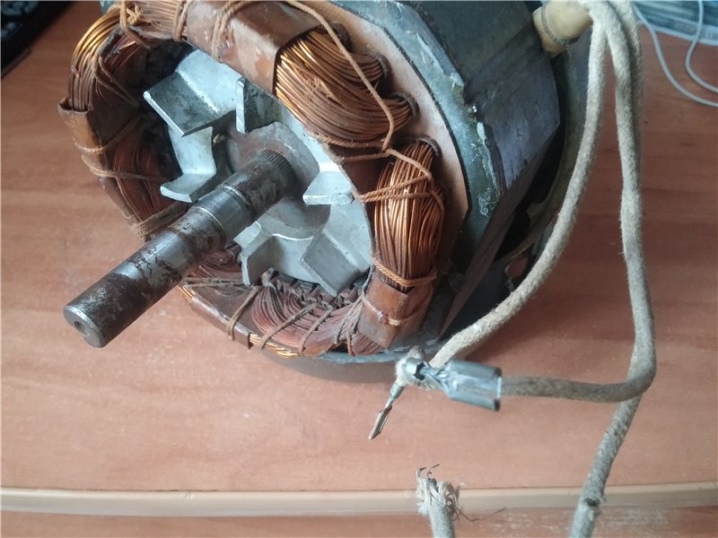
Collector
Has a significantly higher efficiency. The rotor and stator are a set of independent windings connected in series. The rotor circuit is divided into a dozen winding sectors, for each of which there is a pair of lamellas - sliding copper or copper-plated contacts fixed on the shaft. The number of lamellas can reach 20 or more - according to the number of windings.
So that the lamellas do not wear out, graphite brushes are used instead of copper contacts. The brush looks like a parallelepiped, a kind of "brick" up to a couple of centimeters long, connected by means of a bronze or brass contact pressed into it, to the end of which a copper stranded conductor is soldered.
Graphite has a resistivity hundreds of times greater than a copper conductor, but its conductivity is sufficient to power the rotor windings with the required amount of current - those have a resistance of 1-4 ohms.
The rotor assembly is connected in series with the stator, whose windings, like the primary coil of a transformer, have a resistance of up to 200 ohms.
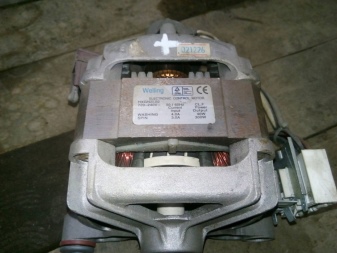
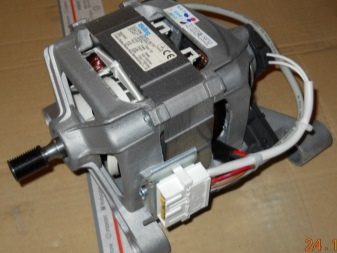
Direct drive
It has increased efficiency due to additional magnetization from permanent neodymium magnets. Such an engine is much more expensive than the others, but it produces, like a stepping motor, high efficiency - about 90-95%. Does not require belts or gears through which torque is transmitted to the drum.
If the engine does not spin or runs intermittently, then at the collector, the first thing to check is the serviceability of the brushes. Pull them out - worn brushes become several times shorter than new ones: graphite belongs to soft materials and wears out quickly during intensive, many hours of work. This is the main disadvantage of the brushed motor.
If the brushes are intact, then check the integrity of the lamellas. Blackened lamellas can be cleaned with fine sandpaper or in a workshop on a lathe. After cleaning, traces of the scraped off material are removed from the lamellas.
If the lamellas are completely worn out, replace the entire rotor, since these contacts cannot be replaced. It's good if there is exactly the same or a similar motor nearby with a working and fully working rotor. With the integrity of the brushes and lamellas, it remains to check the rotor and stator windings.
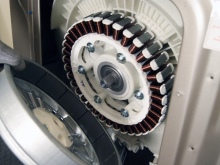
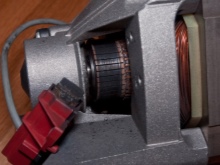
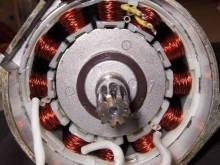
In a direct drive motor, check the integrity of the magnets. If one of them crumbles or flew off, you can order exactly the same or similar neodymium magnets from China and paste in new ones to replace the destroyed ones. If the magnets are intact, check the health of the windings.
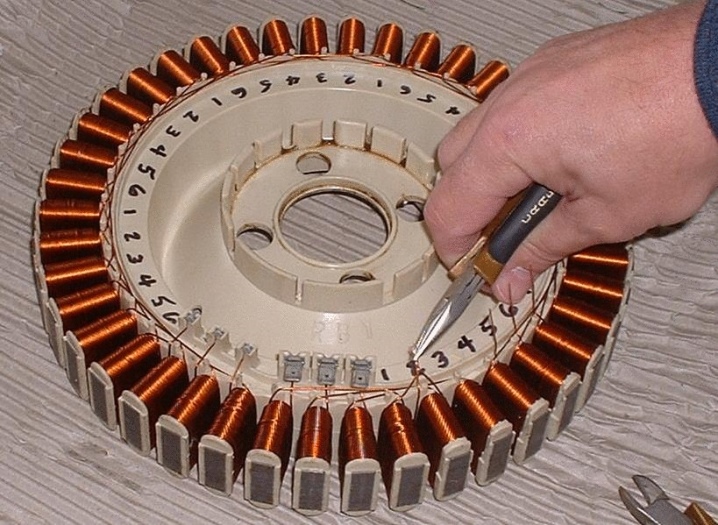
In a collector motor, one by one "ring" the windings on the rotor by connecting the tester with the help of its probes to the corresponding "paired" lamellas. Infinite resistance indicates an open circuit, and almost zero - an inter-turn circuit. A short circuit most often occurs from constant overheating, due to which the epoxy glue with which the winding is poured and the varnish covering the winding wire with a thin layer peel off.
The alternating magnetic field induced by the stator winding does its dirty work - the closed loops literally heat up due to the release of too much induction current and their own low resistance, and this part of the winding simply burns out. Then the section of the wire loses contact, and the multimeter indicates an open circuit. The rotor windings must not short-circuit to the housing (breakdown of the coils to the shaft).
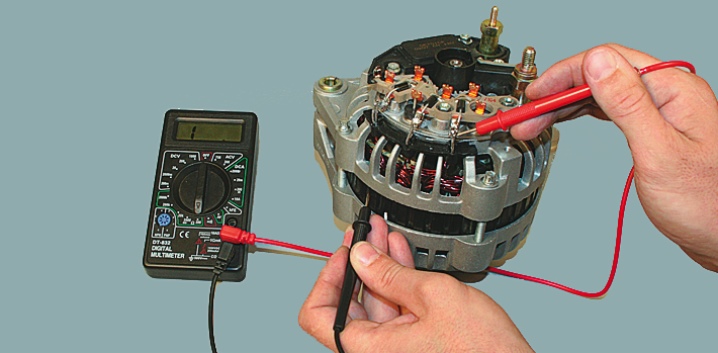
Turn-to-turn closure occurs both in the rotor and in the stator. The stator winding with short-circuited one or several turns cannot provide the power requested by the consumer, while it overheats. If the washing machine did not have a thermistor on the motor, then it would become a fire hazardous device: smoke will go out of the engine, and the mains fuse on the electrical panel will be “knocked out”.
The thermistor turns off the power supply to the motor if it warms up to 90 degrees: a normally working motor, even with a daily wash of several hours, will not heat up over 80 degrees.
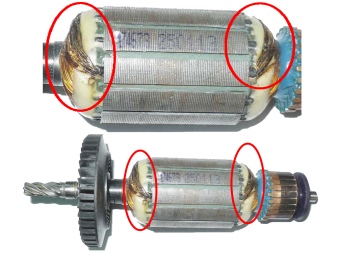
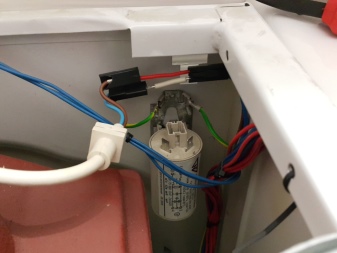
In stator electric motors there are 3 windings: when one of them fails, the remaining 2 do not “pull” well. The motor acquires a "dead point": when the shaft stops, it may not start. One winding is the same as a completely faulty motor. The motor is designed in such a way that all 3 stator windings "push" the rotor in concert - with the interaction of stator and rotor magnetic fields.
This problem is corrected by rewinding the engine: the old enamel wire is removed, and a new one is wound up instead. An advanced user will order the required wire from Russian or Chinese suppliers and rewind the stator by himself. Beginner - will use the services of the service center. It is ten times more difficult to rewind the rotor “filled” by the manufacturer - it will be replaced.
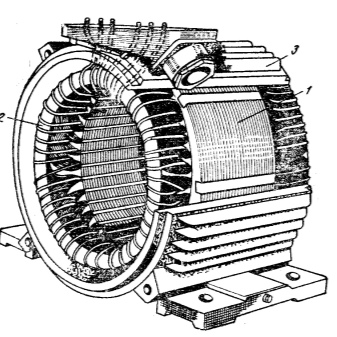
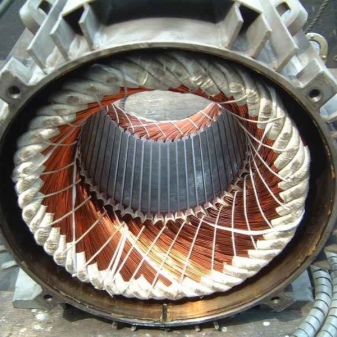
Finally, bearings in the motor may wear out... The manufacturer uses a sufficient amount of lubricant so that the engine can run for several months without additional lubrication.But the temperature of the shaft and stator ends rises from the heating of the windings to several tens of degrees, from the sparking of the brushes (if any), which is why the lubricant gradually evaporates. Ideally, it is necessary to lubricate the engine with lithol or grease at least once every six months when washing clothes every day.
No matter how high-quality the shaft, stator plates and bearings are, oil "hunger" is the way to friction, ten times greater than with a timely lubricated mechanism.
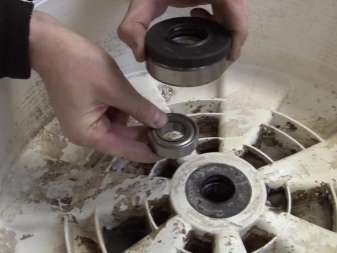
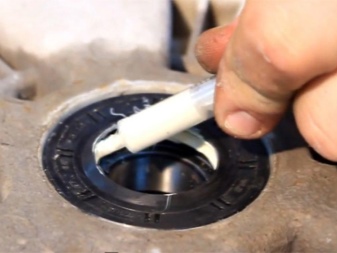
Balls and bearing cages wear out and parasitic play forms. The separator and balls are broken, the shaft "walks" and the engine vibrates at high revs. There is a rubbing sound, the shaft is jammed and the engine runs extremely unstable. The gap between the rotor and the stator (less than 1 mm) on one side is violated when the shaft wobbles. The stator and rotor blades are ground to center the perfectly wound motor. In turn, misalignment leads to additional vibration. Having disassembled the motor, be sure to check the condition of the bearings.
With direct drive motors, the part of the shaft that is in contact with the motor wears out. This is a wheel rigidly connected to the motor shaft. It is smaller in diameter than the drum. The pad on this wheel also wears out.
Whether it is made of rubber or resembles a cog in a helical gear, the worn out element needs to be replaced.
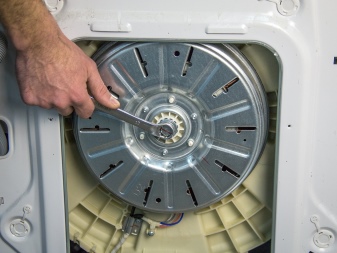
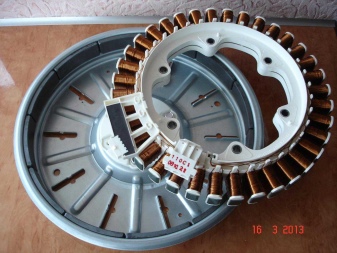
Advice
- Check the lubrication condition of the motor bearings every six months or a year. If it is running out, clean the shaft from the remnants of the old grease and add a new one. Do not use industrial oil - it dries quickly at 50-80 degrees.
- Do not overload the car by "driving" it to the limit. If the model has 7 kg of laundry, load 5-6 kg.
- Reduce the spinning speed, especially when there is a lot of laundry (near weight limit). Instead of 1000 rpm, it is better to use 400-600.
- Lightweight items require a refreshing wash - one main cycle, one rinse, one spin. Do not prolong the wash for 3 hours when the laundry is lightly soiled. If you have a dryer and an iron, you can skip the drying and light ironing mode.
- Fix the machine by placing it in a small recess, "sinking" the feet into the floor by a centimeter. At high revs, it will not budge.
- Do not hang the AGR on brackets above the floor, even if the wall is made of reinforced concrete. Having caught the resonance when shaking during the spinning of the laundry, you can fill up the house.
- If your mains voltage fluctuates frequently, use a high-power regulator or UPS that provides stable 220 volts.
- When checking the engine for operability, turn it on in series through the heating element of the machine - the faulty windings will be saved, since in the case of their low resistance, short circuits, the spiral of the heating element will quickly heat up.
- In the wiring (line) of the socket into which the CMA is connected, an additional difavtomat must be used.
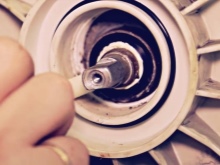
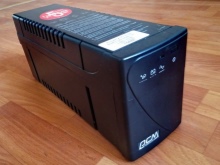
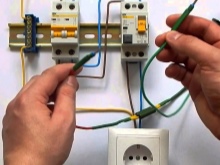
A washing machine, like any device, needs careful handling and timely care. Then it will work for 10-20 years without any problems.
How to check the washing machine motor, see below.
The comment was sent successfully.