Candy washing machine malfunctions
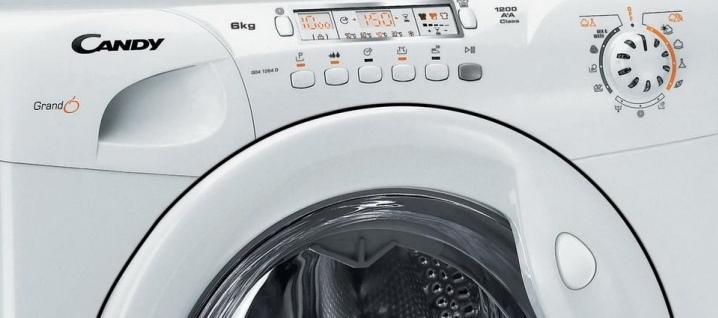
Candy washing machines from the Italian company are in demand among consumers. The main advantage of the technology is an excellent combination of price and quality. But after the expiration of the warranty period, the cars begin to break down. If you have knowledge in electronics and household appliances, then the breakdown can be eliminated on your own.
Frequent breakdowns
Like all other models of washing machines, Candy is short-lived, some part wears out or breaks. Very often the device breaks down due to non-observance of the operating rules. The machine stops turning on or the water does not heat up.
You can do it yourself if the breakdown is minor, for example, you need to replace the drain hose or clean the filter. But if the engine or control system is out of order, then you will have to take the equipment to a service.

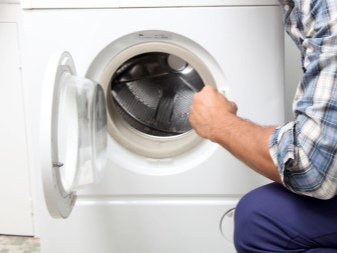
Does not turn on
This is the most common failure in Candy washing machines. It is not necessary to immediately take the electrical appliance to the workshop, you must first find out the cause of the malfunction. The following steps are taken.
- The equipment is disconnected from the mains. The presence of electricity in the apartment or house is checked. If everything is in order, the flap is examined to see if the machine gun was knocked out. The drive plug is inserted back into the socket. One of the washing programs is switched on.
- If the device does not start, then the serviceability of the outlet is checked... This is done using another serviceable technique or a special screwdriver. There is no contact - it means that the socket is not working properly. The cause of the breakdown is burnout or oxidation of the contacts. The old device is replaced with a new one and the operation of the washing machine is checked.
- If the device still does not erase, then it is checked the integrity of the electrical cable. If there is damage, then the wire is replaced with a new one.
- The program does not work, the equipment does not turn on due to control system malfunctions - in this case, you will have to call the master at home to fix the breakdown.



Does not drain water
There are several reasons for the breakdown:
- there is a blockage in the system:
- the hose is broken.
If you do not follow the instructions for operating the equipment, then sooner or later it will fail. Due to a blockage, every second device stops functioning. Very often, equipment owners forget to check their pockets before washing - paper napkins, money, small items can block access to the water drain. The clogging often occurs due to the decoration on the clothes. At high temperatures, the latter can peel off from clothing and enter the system.
You should always clean things of sand and dirt, otherwise they can lead to a blockage.


To fix the breakdown, you need:
- manually drain the water from the tank;
- find the location of the filter using the instruction manual;
- remove the cover, unscrew the part clockwise;
- wait until the remaining liquid is drained (a rag is preliminarily placed);
- pull out the filter and clean from small objects.


The second reason for the breakdown is malfunction of the drain hose. It is necessary to check whether it is twisted, whether there are holes. A blockage in the drain also arises due to the carelessness of the hostess. If, for example, a diaper gets into the drum when putting things into the drum, then during washing the product breaks and the drain hose becomes clogged. It will not be possible to clean, the part is changed to a new one.
The third reason for the malfunction is pump impeller. A working part should rotate. There are situations when the device works, but the pump hums when the water is drained.In this case, the impeller does not stand in its place, it can jam at any time. The pump will have to be changed.
If the drain in the machine does not work well, then perhaps there was a failure in the sensor (pressure switch). The part is under the top cover. If the pipe that connects to the device becomes clogged with dirt, the drain will not work. To check the operation of the sensor, you need to blow into the tube. You will hear a click in response.



The door does not open after washing
Error code 01 - this is how a breakdown is indicated in the operating instructions. There are several reasons for the malfunction:
- the door is not tightly closed;
- the door lock or electronic controller is out of order;
- several things prevent the hatch from closing;
- the water inlet valve has broken.
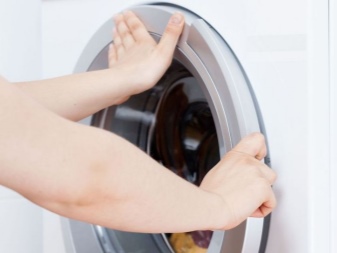

Examine the washing machine door carefully. If it is not tightly closed or things have got in, then the problem can be fixed on your own. But if the electronic controller breaks down, it is better to call the master at home, and it will hardly be possible to unlock the device. But you can take the following actions:
- the washing machine must be disconnected from the mains, wait 15–20 minutes and then turned on again;
- clean the filter;
- activate the mode of rinsing or spinning the laundry;
- after completing the procedure, unscrew the plastic cover and pull on the emergency opening cable.
If it was still not possible to unlock the device, then you will have to call a specialist.
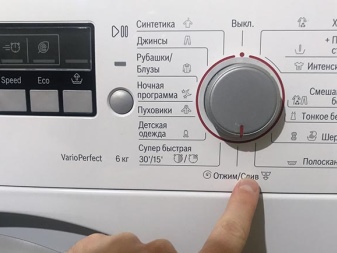

A jammed lock may also be the cause of the malfunction. The part can be changed by yourself:
- the machine is disconnected from the network;
- the hatch opens and the seal is removed;
- two screws holding the lock are unscrewed;
- a new part is installed;
- then the steps are performed in the reverse order.

Rinsing problems
It will not be possible to immediately determine the malfunction after switching on. One of the wash cycles starts first. If the equipment stops working in rinsing mode, then there are several reasons for the breakdown:
- there was a failure in the system;
- the machine has stopped squeezing or draining water;
- there was a blockage in the sewer;
- the water level sensor is out of order;
- the control board is broken.
The drain hose is checked. If it is twisted or crushed by a heavy object, the malfunction is rectified.
The next step is to check if there is a blockage in the sewer. The drain hose is disconnected from the appliance. If water poured out, then you will have to change the siphon or drain pipe.

If problems arise with the electronics, you must take the washing machine to a service center.
Other problems
Error code E02 means that the device does not draw water. She either does not enter or does not reach the required level. Reasons for the malfunction:
- the door lock has not worked;
- the intake filter is clogged;
- an error has occurred in the control system;
- the water supply valve is closed.
The condition of the inlet hose is checked and the mesh filter is rinsed. The valve for the water supply is examined. If closed, it opens.


Other problems may arise.
- The drum is not spinning - the power supply of the equipment is turned off. The water is drained through the filter. The linen is being taken out. The drum is scrolled manually. If it fails, then the cause of the breakdown is a foreign object or a broken part. If the drum rotates, the fault lies in the control system. Do not overload the device - it is better to divide a large amount of laundry into two parts.
- Washing machine jumps when spinning - forgot to remove the shipping bolts during installation. They secure the device during transportation. The second reason is that the technique was not set according to the level. Adjustment is made using feet and a level. Another reason is that the drum is overloaded with laundry. In this case, it is worth removing some of the items and starting the spin again.
- The machine beeps during operation - breakdown occurs most often due to a control failure. In this case, you should call the wizard.
- Water leaks during washing - the supply or drain hose is faulty, the filter is clogged, the dispenser is broken. We need to inspect the equipment. If the hoses are intact, remove the dispenser and rinse.Then reinstall and start the washing process.
- All buttons on the panel lit up at once - there was a failure in the system. You just need to restart the wash cycle.
- Excess foam - a lot of product has been poured into the powder compartment. You need to pause, take out the dispenser and wash.
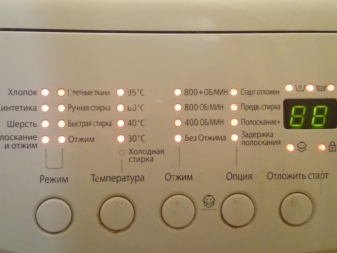

Prophylaxis
To increase the service life of the equipment, preventive actions are carried out:
- you can add special water softeners during washing or install magnetic devices - they will protect the equipment from calcium and magnesium;
- it is worth installing mechanical filters that collect dirt, rust and sand;
- things must be checked for foreign objects;
- the load of linen must correspond to the norm;
- you do not need to use the 95 degree wash cycle often, otherwise the service life will be reduced by several years;
- shoes and items with decorative elements must be placed in special bags before loading;
- you must not leave the device unattended, otherwise there is a risk of flooding of neighbors if a leak occurs;
- the tray after washing is cleaned of detergents;
- the hatch at the end of the cycle must be left open for the equipment to dry;
- once a month it is necessary to clean the filter from small parts;
- be sure to wipe the cuffs of the hatch so that no dirt remains in it after washing.
If suddenly the Candy washing machine is out of order, then you need to find out the cause of the breakdown. If the filter, hose is clogged, or the outlet is faulty, all repair work can be carried out independently. In case of failure of electronics, engine or combustion of heating elements, it is better to call the master at home. He will perform all the work on site or take the electrical appliance for service.

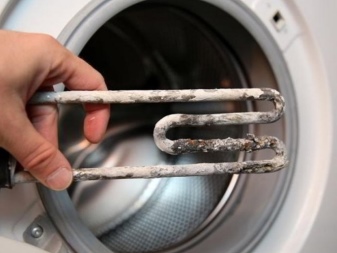
How to repair Candy washing machines, see below.
The comment was sent successfully.