How and with what can you cut glass?
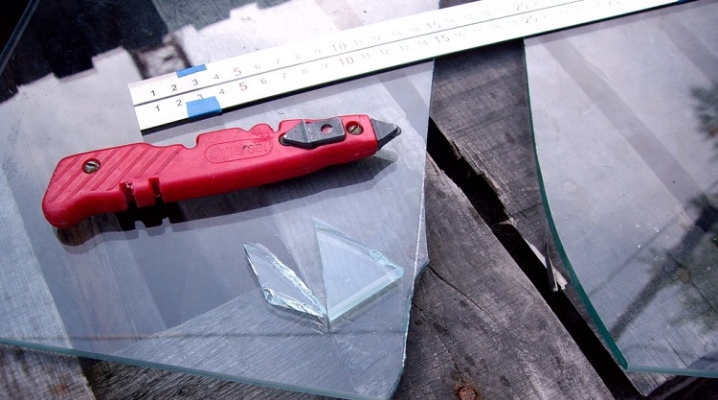
No house can do without glass, and therefore the question of cutting it arises in almost every renovation. There are many ways to solve this problem.
Basic ways
Glass cutting is the most important step in the processing process. As a result, the product acquires the specified dimensions and shapes, as well as the possibility of artistic finishing that improves its appearance. These actions, depending on the desired result, can be performed in various ways and methods on specialized machines.
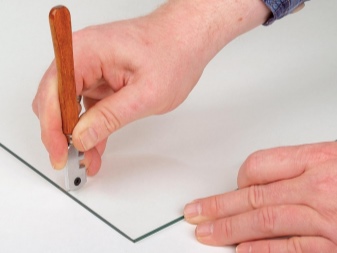
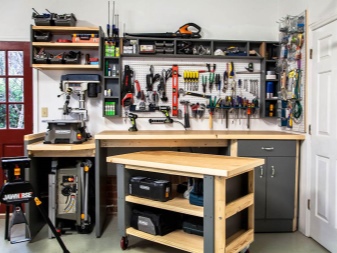
Mechanical
Manual cutting exists and is quite common, but it is usually only used for small repairs, otherwise it is impractical. The oldest and most widespread method of processing and cutting glass is the mechanical method. This is currently the most suitable processing method. This method involves the use of special wedge-shaped cutting rollers, made mainly of tungsten.
Cutting in this way involves two operations. First, the roller makes a groove (at risk) in the glass of the desired path, after which an attempt is made to break it off.
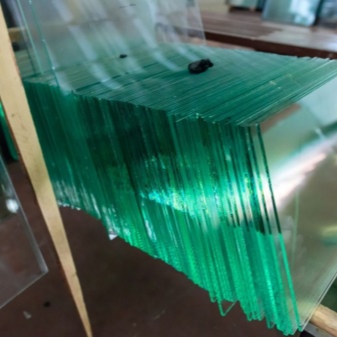

Despite the outdated mechanical cutting technology, it still has significant advantages:
- the highest cutting speed - up to 120 m / min;
- low cost of equipment and ease of maintenance;
- the workpieces can be of various sizes and shapes.
The most common disadvantages of mechanical cutting are:
- chips and roughness of the cut due to mechanical defects in the material;
- the need for subsequent processing and finishing of the cut edge;
- when cutting it is necessary to use special fluids.
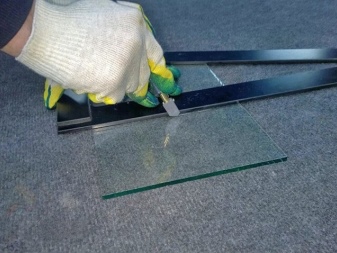

Laser
Laser cutting was initially tested on thin metal. More recently, the same method has begun to be used to cut glass using special devices.... There are two types of laser cutting. The first is an original technology called thermal evaporation laser cutting. This process is currently practically not used, since it is the slowest and consumes a large amount of energy. The method itself consists in evaporating the glass to the end. The main disadvantage of this option is the presence of residual stress in the material due to heating, which can lead to breakage of the product along the edges of the cut.
The second method, which is currently used, has been developed as a result of the improvement of thermal evaporation. It was found that it is not at all necessary to completely vaporize the glass with a laser; low thermal conductivity and heat resistance allow the use of the thermal cleavage method. The principle of this method is discrete heating of glass along the entire cut line. This is followed by a sharp cooling, and a tensile stress is formed in this area, breaking the glass clearly along the drawn line.
This method is faster and less energy intensive, so it is now actively used and gaining momentum.


Laser cutting has several advantages:
- high-quality cut with a flawless edge;
- curly cutting is simplified;
- it is possible to cut glass with a large thickness;
- no mechanical impact is exerted on the product;
- ease of regulation and control of the cutting process.
The glass laser cutting process is currently under development. Therefore, like all new technologies, this method has its drawbacks:
- low emission material (reflective infrared radiation) is not suitable for laser processing;
- expensive machines requiring careful use;
- low processing speed - from 5 to 10 m / min.

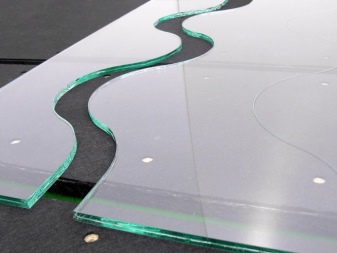
Waterjet
Waterjet cutting was made possible in the 1980s by the use of powerful hydraulic pumps that allowed the fine, sharpened granules of shredded materials to be mixed with water. The technology is designed for cutting a wider range of materials. Glass is very suitable for this method, which leaves a matte edge that is easy to polish.
The advantages of this cutting:
- excellent edge quality, which makes sanding unnecessary;
- no chemical and thermal effects on the material, slight mechanical stress, no cracks;
- the ability to cut very thick and laminated glass.
Despite the advantages, there are also disadvantages:
- very low cutting speed (0.5-1.5 m / min) depending on glass and equipment;
- high operating costs of equipment;
- the need to prepare a large amount of water.

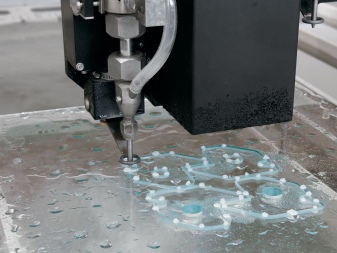
How to cut glass at home?
Before cutting glass at home, you first need to determine the tool that is applicable for this method. In most cases, a glass cutter is used to cut glass. There are the following types of glass cutters:
- oil;
- roller;
- diamond.
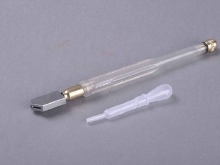
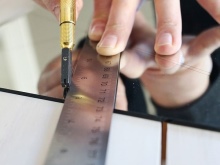

This process can also be done with a soldering iron, angle grinder or circular saw, nichrome wire, and even regular scissors.
- Soldering iron. First of all, risks are applied on both sides of the cut line with a rasp. Then the entire cut line is heated with a well-heated soldering iron. Due to the temperature difference on the surface, the glass breaks, after which it remains only to gently break it off.

- Grinder or circular saw. To cut glass with a grinder, you must use a diamond disc. First, apply a small groove along the cut line with a diamond disc. In the process of work, make sure that the glass surface does not get very hot. To do this, water the surface with ordinary water. The tool used in this method must be in good working order and free from any defects. Otherwise, the glass will simply crack.
When working with a grinder, it is necessary to use personal protective equipment for the respiratory and vision organs.

- Use of heating and cooling. Place the thread impregnated with a combustible substance along the cut line and set it on fire. After the thread has completely burned out, cool the surface sharply with cold water. From such a temperature drop, the glass will collapse along the cut line. Another option is to heat the material using a nichrome wire connected to an electric current. This method does not use water for cooling. The temperature difference between the filament and the glass is enough to chip in the intended place.
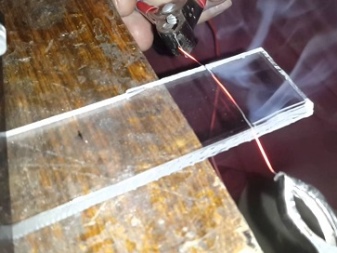
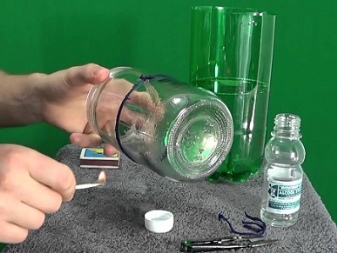
- Scissors. Thin glass of small thickness is cut with simple scissors, if this is done by immersing the scissors and glass under hot water. It is similar to the process of cutting thick cardboard with a knife.
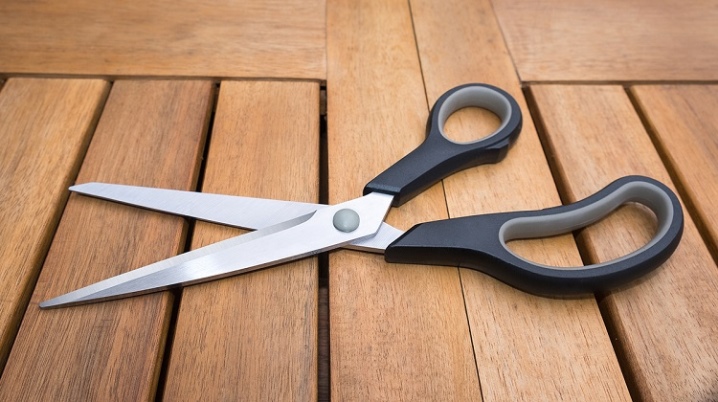
- For drilling round holes in glass, drills for ceramic surfaces are used, as well as diamond core bits of various diameters.
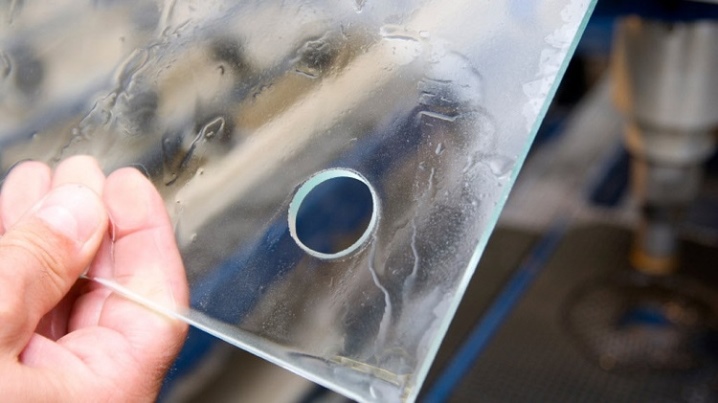
Preparation
Preparation for the glass cutting process should never be neglected. This operation is impossible without preliminary preparation. It is necessary to wipe the surface with a damp cloth to remove all unnecessary inclusions. After the glass is dry, dry with a dry cloth.
Many experts advise using old paper rather than rags. It does not leave fibers on the surface that interfere with the cutting process. Glasses that have already been used are much more difficult to cut and therefore take longer to prepare. In addition to cleaning and drying, such material must be degreased with kerosene.

Features of cutting different types
Tempered glass, also known as tempered glass, is made by heating it in an oven to a temperature of 680 degrees and then rapidly cooling it with uniform air currents. Such a product is used as a windshield and window glass in cars, as well as a heat-resistant and fire-resistant ceiling. As a rule, glass cutting and processing is done just before annealing, which eliminates other problems. Processing such a material by conventional methods is impossible due to its mechanical properties.
There are different cutting methods available for tempered glass. The first is laser cutting of glass. Due to the fact that the laser cuts the material by heating at a certain point, the internal stresses at this point are reduced and prevent cracking of the glass, producing a smooth and high-quality cut. The second and more complex method involves preliminary annealing. The main goal of this method is to completely remove residual stresses over the entire area of the material and thus transform it into ordinary sheet quartz glass. Annealing is carried out by soaking the material in water to the temperature index of the viscosity of solidification in an oven. This is followed by slow cooling to a temperature below deformation. As a result of these actions, the glass loses its tempered properties and can be mechanically cut.
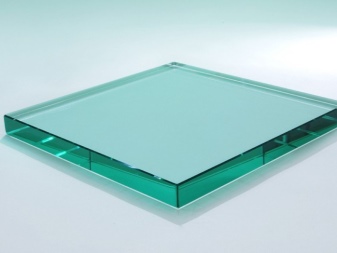
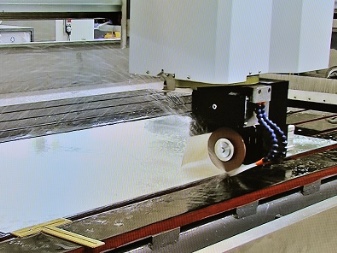
Acrylic glass, also known as organic, is a synthetic polymer of methyl methacrylate, a transparent thermoplastic plastic. It is called glass only formally because of its transparency. The rest of the properties are significantly different and have nothing to do with real glass, which allows you to apply completely different processing methods to it. In this regard, one of the most popular cutting methods is dissection using a milling machine, when specialized equipment is not required, but the same equipment is used as for processing wood and metals.
Other methods used for disassembling the glass also apply to the acrylic version. Waterjet and laser cutting work with organic glass with great efficiency and provide a faster cutting speed than when using the same equipment for processing conventional glass. Cutting thick reinforced glass is difficult due to the presence of a metal mesh in it.
However, all the cutting methods discussed above are applicable to this kind of processing. The only difference is that in some cases, on the cut line, you will have to bite the metal wire with wire cutters.


detailed instructions
Before starting cutting any kind of glass, first of all, you need to check the health of the glass cutter and its sharpening. It is necessary to try to cut out an unnecessary piece of the sheet. A working glass cutter moves without effort and squeak, the cut line is thin and continuous. All other results will indicate that the cutting element is defective or that there was a mistake in cutting technique.
It is also worth choosing a flat support with dimensions larger than the dimensions of the sheet being processed. Any straight surface will do. For safety, it is worth laying a thick cloth on it. Glass marking tools are a bright marker, iron ruler, tape measure.
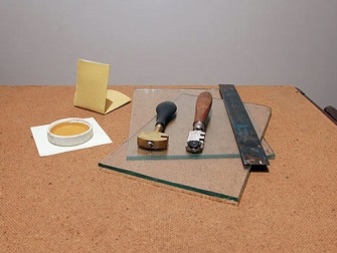

For high-quality cutting, it is necessary to follow the technology and sequence of operations.
- On the surface, mark the start and end points of the cut.
- The glass cutter is at the top and has a ruler attached to it.
- Cutting is performed smoothly from top to bottom, with constant force and in one direction. It is not necessary to carry out the glass cutter several times in one place. The glass may crack.
- Break off a piece, aligning the cutting line with the edge of the table. Create a crack by gently tapping the cut with a glass cutter and then chipping in one sharp motion.
- If the chip is uneven, you can correct it with pliers or use the special cutouts in the handle of the glass cutter.To avoid cracks, the cut line must be moistened with turpentine.
- At the final stage, sand the cutting line with sandpaper, a velvet file or a sharpening stone.
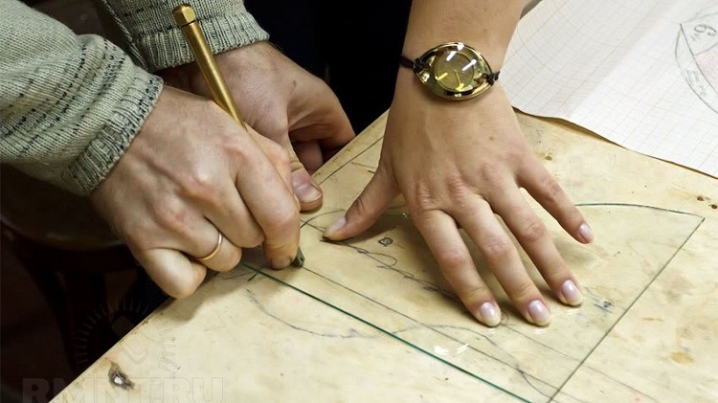
Precautionary measures
It is important to observe safety precautions when working with glass.
- Never cut glass on your knees or random objects. Do not brush along the cut line with your unprotected finger.
- The product should be broken correctly, only in the opposite direction to the cut. The lips of the ticks should be protected with rubber tips or wrapped in cloth or tape.
- Sort and stack sheets with gloves rather than bare hands.
- Be careful when using electric glass cutters to avoid electric shock and possible burns.
- Before starting work, check all tools and accessories, and replace defective ones.
- Work clothes must be cleaned of glass dust and particles after each working day.
- Wear safety glasses.
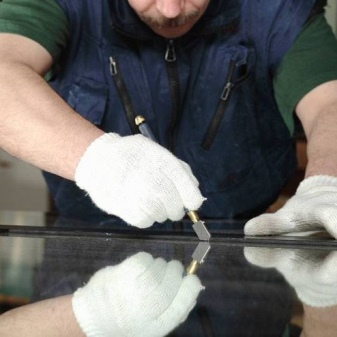
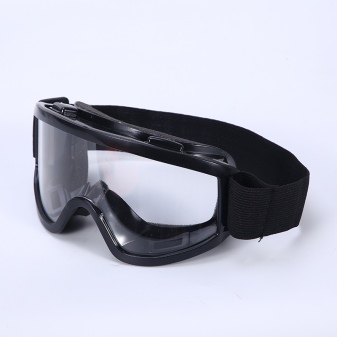
For information on how to cut glass correctly, see the next video.
The comment was sent successfully.