All about screw-cutting lathes
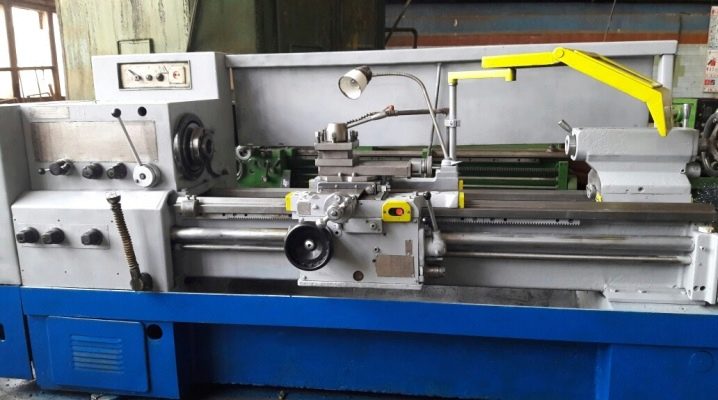
Knowing everything about screw-cutting lathes is quite useful for organizing a home workshop or a small business. It is necessary to understand the features of the device, with the main units and the purpose of machines with and without CNC. In addition to what it is in general, you will have to study universal desktop models and other options, the peculiarities of working with them.
What it is?
Any screw-cutting lathe is designed for processing steel, cast iron and other workpieces. This procedure is called cutting by specialists. Such devices allow you to grind and grind parts. They successfully form the grooves and work out the ends. Also, the purpose of the screw-cutting lathe includes:
- drilling;
- countersinking;
- deployment of openings and walkways;
- performing a number of other manipulations.
The general principle of the device is extremely simple. The workpiece to be processed is clamped horizontally. It starts spinning at a given moment. With this movement, the cutter removes unnecessary material. But the apparent simplicity of the description does not allow one to ignore the rather great complexity of execution.
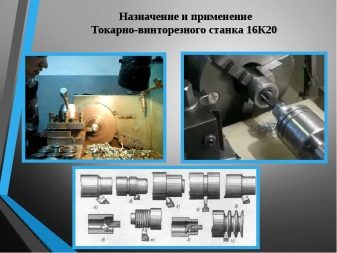
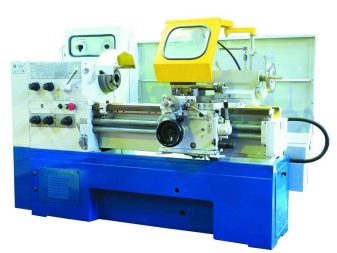
A screw-cutting lathe can work with confidence only if it is assembled very carefully from well-joined elements. The main nodes in the scheme of such an apparatus are:
- support;
- stubborn grandmother;
- bed;
- spindle head;
- electrical part;
- running shaft;
- gear guitars;
- the box responsible for filing;
- lead screw.
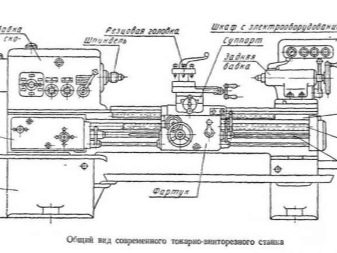
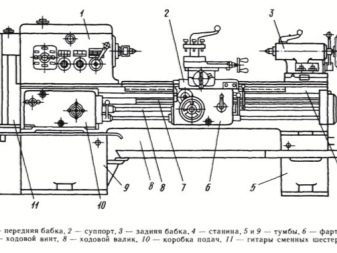
Despite the rather calibrated structure based on typical parts, specific machines can vary greatly. A lot depends on the accuracy during operation. The spindle (aka frontal) headstock prevents the movement of the workpiece being processed. It also transmits a rotational impulse from the electric drive. It is in the inner part that the spindle assembly is hidden - why, in fact, it is so named.
A persistent, it is also a back, headstock allows you to fix the workpiece. The role of the support is to move the tool holder (together with the working tool itself) in the longitudinal and transverse planes relative to the machine axis. The caliper block is always larger than the rest of the parts. The cutter holder is selected according to the category of the device.
The gearbox affects the transmission of impulse to all parts, and therefore the functioning of the system in general.
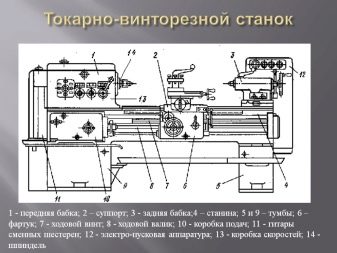
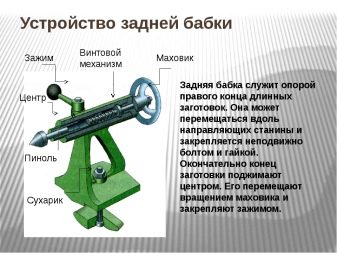
Such boxes can be built into the headstock bodies or be located in separate parts of the body. The tempo is adjusted step by step or in a continuous mode, which is predetermined by the nuances of the design. The main acting link of the box is the gears. It also includes a V-belt transmission and an electric motor with a reverse. In addition, it is worth mentioning the clutch and the handle for changing the speed.
The spindle can be considered an extremely important element. It is a part with a technical shaft configuration and has a tapered channel to hold the parts. It is certainly strong and durable, because it is made from a selected variety of steel alloy. The traditionalist approach implies the use of highly accurate rolling bearings in the design of the spindle element. A conical cavity at the end is needed to place a bar, which sometimes provides a knockout of the central part.
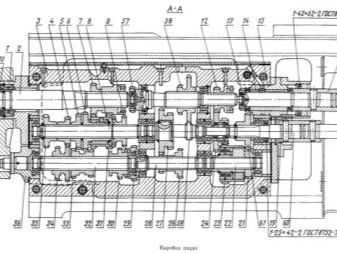
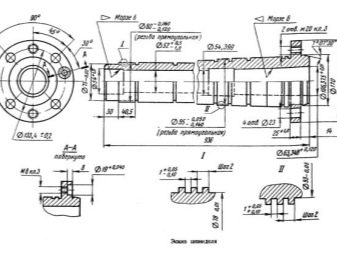
The bed of a screw-cutting lathe is obtained by casting from cast iron. To work out the grooves, as needed, use a marking tool, dies, cutting and other devices. Control units contain a variety of keys and handles, including those that allow you to adjust the caliper. Models with CNC are more complicated than classic ones, but they can perform manipulations unattainable for those and act in some cases without the help of an operator. It is worth emphasizing the role of the apron - inside it there are mechanisms that convert the rotation of the screw assembly and the technical shaft into the forward motion of the support apparatus.
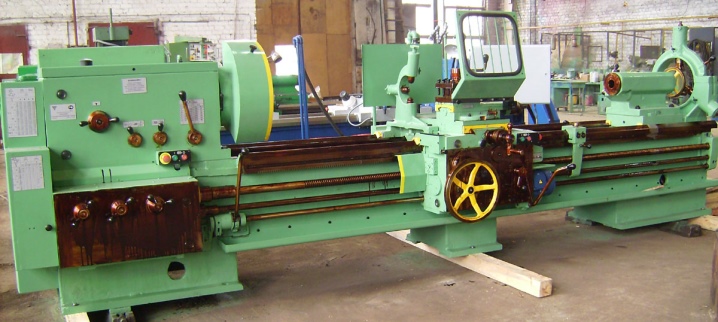
Species overview
By mass
The screw lathe can be used in local private enterprises, for household needs. Such models are usually relatively lightweight. Large and heavy vehicles are designed mainly for industrial production. Devices not heavier than 500 kg are considered light.
Medium-sized equipment plays an important role in the industry. It weighs up to 15,000 kg. The largest industrial designs weigh between 15 and 400 tons. In this case, a high level of accuracy is usually not encountered because the tolerances are no longer so significant.
Very powerful equipment is installed in large factories and factories, but it is not used in the household segment.
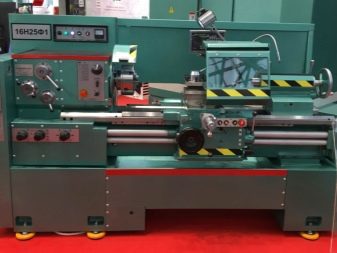
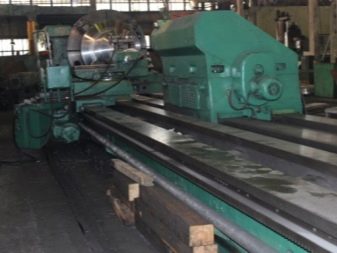
By the maximum length of the part
Basically, lightweight machines interact with parts no more than 50 cm in diameter. Medium-level equipment can handle workpieces up to 125 cm long. The longest part length is predetermined by the distance between the center points of the machine. With the same cross-section, the machines are able to work both long and relatively short structures. The spread over the largest diameter of parts is especially large - from 10 to 400 cm, therefore there are no universal machines working with workpieces of any section.
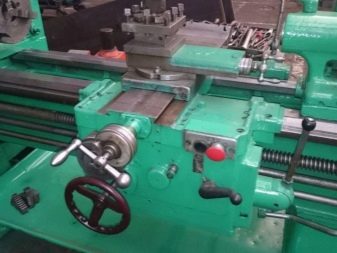
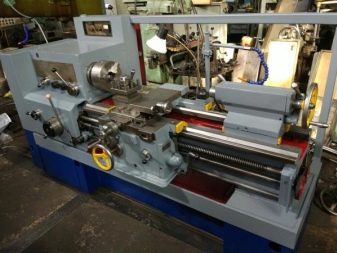
By performance
An important point in the classification of screw-cutting equipment is its technical productivity. It is customary to allocate devices for:
-
small-scale production;
-
medium-scale series;
-
large-scale conveyor production.
The brands of screw-cutting lathes are quite diverse. They are produced in many countries. Moreover, some of the equipment has been actively used since the period of the USSR and has not yet lost its relevance. When familiarizing yourself with the description of the technique, it is important to find out whether it is designed for desktop or floor mounting, what are the features of the installation in general. As for CNC machines, this is practically no alternative solution - even for home use, "purely manual" equipment is used extremely rarely.
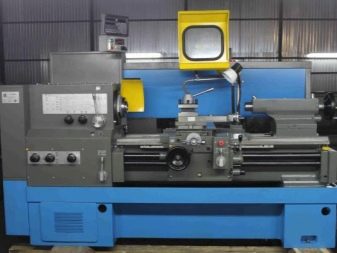
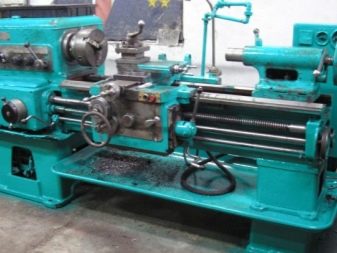
Top Models
It is appropriate to start the review with "Caliber STMN-550/350"... Although such a device is lightweight, there are quite serious possibilities in its compact body. By collecting and configuring it in accordance with the instructions, you can guarantee the accuracy of the work. Technical service is required after every 50 hours of operation. Key Features:
- distance between centers 35 cm;
- section of the workpiece over the bed up to 18 cm;
- total weight 40 kg;
- the number of revolutions - 2500 per minute;
- rubber feet in the basic set;
- plastic handles;
- Morse taper No. 2.

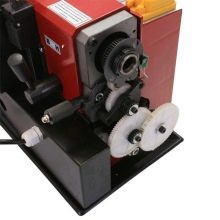
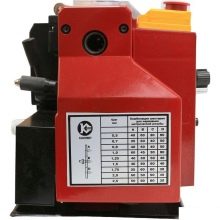
For simple metalwork, you can also use the Kraton MML 01 machine. This device is highly maintainable. The problem is the use of plastic gears. Replacing them with cast iron, you can not be afraid of the consequences of careless use. There will be a distance of 30 cm between the centers, and the mass of the device is 38 kg; it develops from 50 to 2500 rpm in 60 seconds.
In addition to metal, the Kraton product is suitable for plastic and wood. The designers have provided backlighting. A set of interchangeable gears allows you to cut metric threads. Thanks to the swivel slide, conical sharpening of parts is available.
The cross slide travel is 6.5 cm.
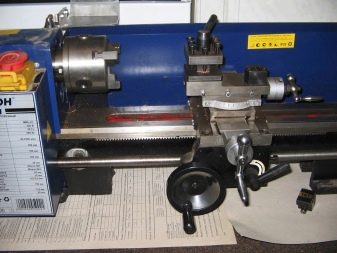
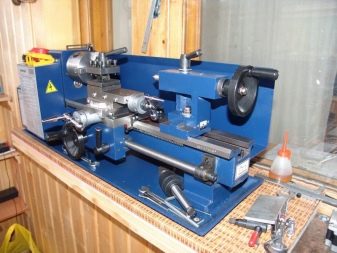
An alternative can be considered "Corvette 402". This is a decent lightweight lathe with particularly high quality components. The single-phase motor has a power of 750 W. The gap between the centers is 50 cm. The section of the workpiece above the bed is 22 cm, and the mass of the device is 105 kg; it can develop from 100 to 1800 turns per minute in 6 different speed modes.
Peculiarities:
- the electric motor is made according to an asynchronous scheme;
- the reverse of the spindle torsion is provided;
- thanks to the magnetic starter, spontaneous switching on after a power outage is excluded;
- the device is equipped with a pallet;
- the spindle taper is made according to the Morse-3 scheme;
- in 1 pass, you can grind up to 0.03 cm;
- cross and swivel calipers moves - 11 and 5.5 cm, respectively;
- spindle radial runout 0.001 cm.
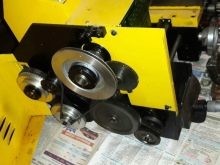
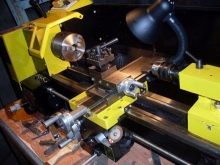
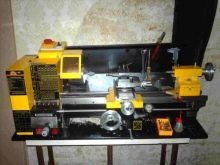
Proma SKF-800 can also be considered a decent solution for organizing a workshop at home. The model is designed to work with very large parts. A pair of three-phase motors provide powerful torque. Main parameters:
- turning length 75 cm;
- workpiece diameter above the bed - 42 cm;
- total weight 230 kg;
- spindle with a 2.8 cm through hole;
- inch thread from 4 to 120 threads;
- obtaining a metric thread from 0.02 to 0.6 cm;
- quill stroke - 7 cm;
- current consumption - 0.55 kW;
- operating voltage - 400 V.
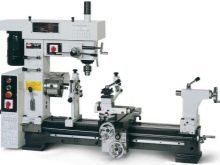
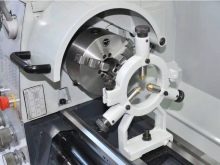
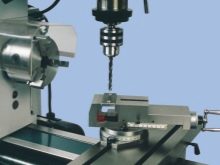
The MetalMaster X32100 is also worth taking a closer look at. This is a universal screw-cutting lathe with digital display. A thread indicator is also provided. The device works well with ferrous and non-ferrous alloys. Quill outreach - 10 cm, 18 working speeds are provided.
Other parameters:
- the cross slide runs 13 cm;
- the coolant pump consumes 0.04 kW and operates from a household network;
- the machine itself operates at a voltage of 380 V and consumes 1.5 kW of current;
- net weight is 620 kg;
- automatic feed in the longitudinal and transverse planes is provided.
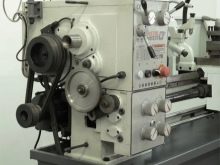
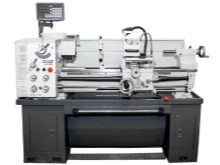
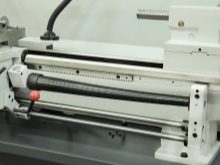
In industrial production deserves attention Stalex GH-1430B... This machine has a center-to-center distance of 75 cm. It weighs 510 kg and is capable of speeds from 70 to 2000 revolutions. The basic delivery includes a pair of steady rests and a pair of non-rotating centers.
The gears are made of superior hardened steel.
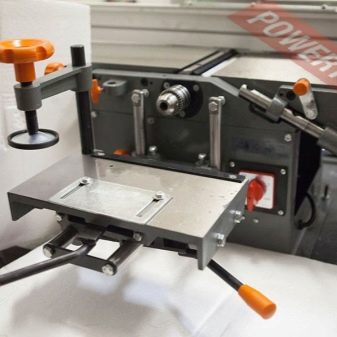
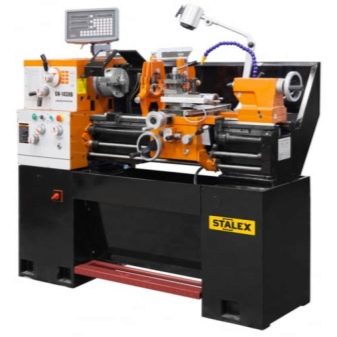
Completing the review is appropriate on the Jet GH-2040 ZH DRO RFS model. This machine is equipped with a 12 kW motor. The through hole in the spindle is 8 cm. Torsion is maintained at very different speeds (24 positions from 9 to 1600 rpm). The manufacturer himself emphasizes the compliance with the special requirements for the accuracy and speed of material processing.

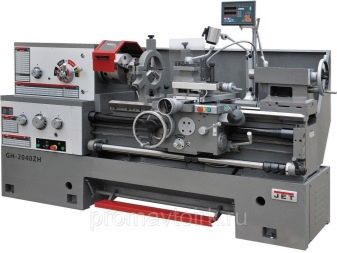
What to consider when choosing?
In the vast majority of cases, the choice for a home workshop is made in favor of universal models. They do not differ in high technical characteristics, however, they are simple in design and can process 1 - 2 parts on a non-serial basis. Any manipulations are done manually. The quality of processing and its accuracy will not be very high.
It should be borne in mind that more and more often, under the name "universal machine" they sell simple equipment with CNC and direct execution of the bed. They allow you to apply control programs. CNC systems are actively replacing the old universal models. But even among the outdated samples there is a division. Thus, copy machines and semiautomatic machines are able to cope with complex-shaped parts; modern examples of this kind have a control system.
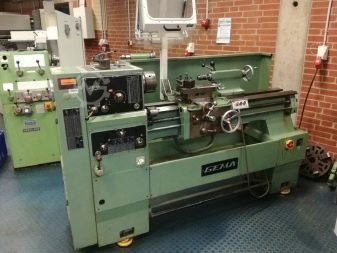
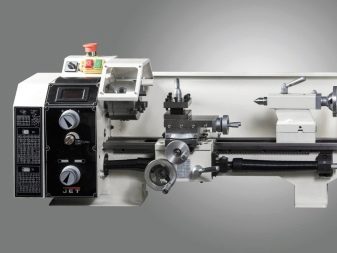
The more incisors, the more productive the apparatus. CNC multi-cutter turning technology is suitable for specific operations. It is mainly used for production lines of various sizes. In any case, you should pay attention to:
- dimensions of the processed parts;
- level of accuracy;
- processing tolerances;
- types of processed metals;
- height of work centers
- chuck diameter;
- type of bed (straight or inclined);
- type of cartridge;
- complete set;
- reviews about the model.
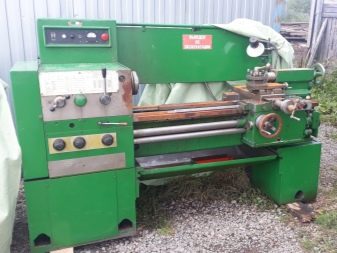
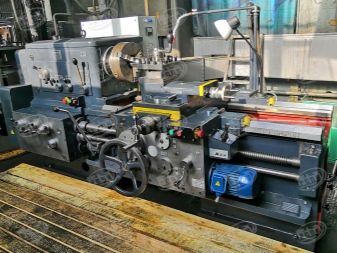
When using a number of modern lubricating and cooling fluids, protection against them is imperative. Any responsible manufacturer provides for it. Screw-cutting machines are selected taking into account the number of working manipulations and their type. We must not forget about the length and diameter of the workpieces. The stronger the machine bed, the more reliable it is; however, a device that is too heavy to use at home is not worth it. Welding connection is preferred over bolting.
Additionally, they pay attention to:
- connection methods;
- power supply parameters;
- the level of backlash (or lack thereof);
reviews of specialists.
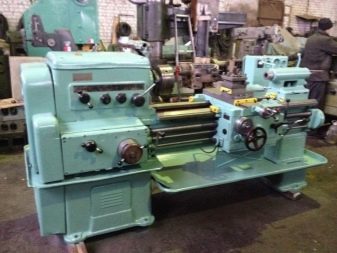
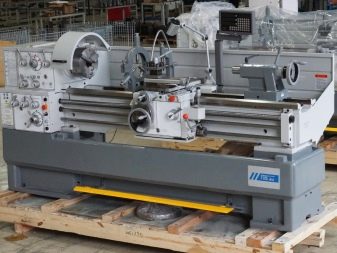
How to work
Often a screw-cutting lathe is used to machine the outer cylindrical surfaces. Similar work is carried out with passing cutters. The workpiece is fixed with the expectation of a sufficiently large overhang. It is believed that the overhang of 7 - 12 mm over the length of the part is enough to process the ends and cut the part. How fast the spindle should rotate, how deeply the workpiece will have to be cut, is prescribed in the flow chart.
The depth of the cut is adjusted using the cross feed dial. After turning, in many cases, the end of the workpiece is trimmed with various cutters. It is necessary to lead the passing or scoring cutter until it touches the end. Then it is taken away and the carriage is moved a few millimeters to the left. Moving the tool transversely, a layer of metal is removed from the end.
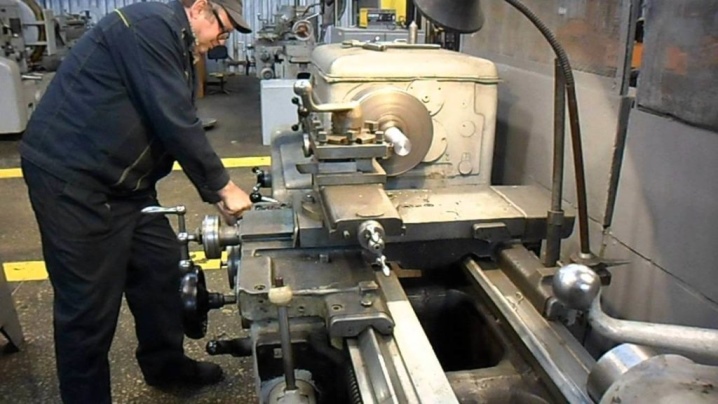
On small ledges, you can grind and cut metal with one persistent cutter. The outer grooves are made using slotted cutters. Work at this moment should be 4 - 5 times slower than when trimming the ends. The incisor is guided neatly, without much effort, always in the transverse plane. The lateral dial helps to set the depth of the groove.
Workpieces are cut using the same method as when grooving. The work is completed as soon as the lintel thickness is reduced to 2 - 3 mm. Further, turning off the machine, break off the part freed from the cutter.

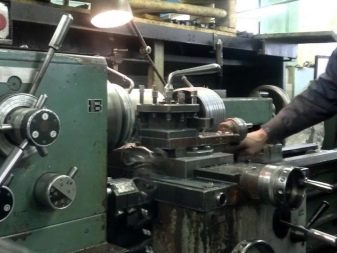
Setup features
Correct commissioning and adjustment is carried out taking into account the nuances of the technological process. When the machine is set up, 2 or 3 parts are machined. According to them, they check how the parameters specified in the drawing are observed. If there is a mismatch, re-adjustment is carried out. An important part of the setup process is to determine the features of the installation and fastening of workpieces in machine tools.
If the vertices of the centers are not aligned, alignment is ensured by moving the tailstock. Next, a driver cartridge is placed. Then the cutter is selected and set exactly along the axis height. The pads should have parallel surfaces with decent workmanship.
You cannot use more than two pads.
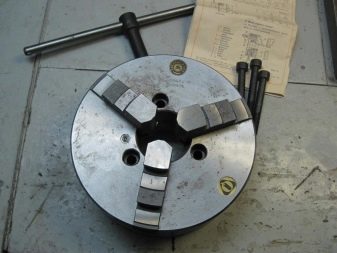
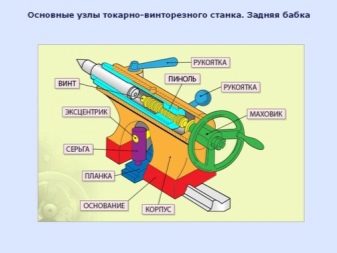
The placement of the cutter tip in the center height is checked specially. For checking, the cutter is brought to the center previously checked for height. The center itself must be installed in the tailstock quill. The protruding section should be shorter - maximum 1.5 times the height of the rod. Too significant overhang of the cutter provokes vibration and does not allow working efficiently; the tool must be firmly fixed in the tool holder with at least a couple of well-tightened bolts.
Round workpieces need to be clamped in a self-centering three-jaw chuck. But if the length of the part is more than 4 times the diameter, you need to take a chuck with a clamping center or use machining machines with a drive chuck. Short non-circular workpieces are mounted using a faceplate or a four-jaw chuck. Bars and other long, small-diameter parts are passed through through passages in the spindle. When adjusting the cutting mode, the main attention is paid to the speed of the main movement and the depth of the cut; you will also need to adjust the feed.
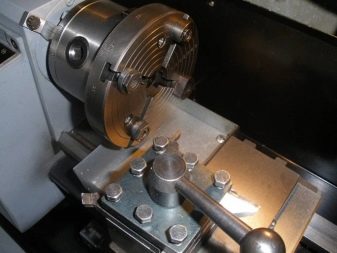
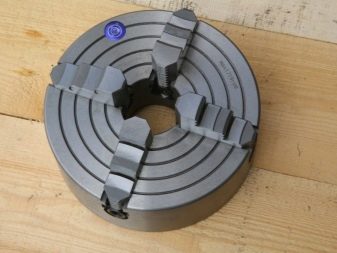
Safety at work
When connecting even the simplest machine, you will have to use devices to protect electrical equipment. The scheme is selected taking into account the basic engineering points. Independent operation of the screw-cutting lathe is allowed only at the age of 17 years. Before admission, you will need to be instructed on labor protection. Additionally, you should be tested for contraindications; during the work itself, the mode of work and rest, the schedule of breaks must be strictly observed.
You need to work on a screw-cutting lathe in a cotton suit or semi-overalls. Additionally, you will need leather boots and special glasses. Even the most careful and orderly workers should keep a first aid kit ready to deal with the consequences of injury. Primary extinguishing media should be kept in workshops.
If any accident occurs, management and emergency services are immediately notified of this.
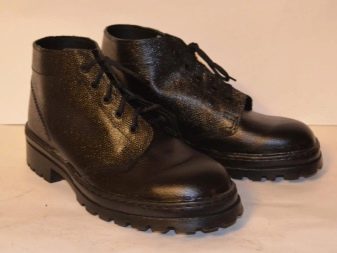
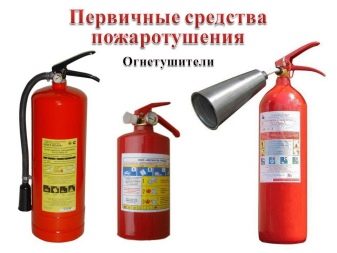
The workplace is supposed to be kept clean. Strictly prohibited:
- turn on the machine in case of ground breakage, in case of malfunction of barriers and interlocks;
- enter the limits outlined by the fence;
- remove this fence (except for repair by competent services);
- start work without checking the serviceability of the machine;
- use unregulated lighting of the work area;
- run the machine without lubrication;
- work without a headdress;
- touch moving parts during work;
- rely on the machine (this applies not only to workers);
- continue to work if vibration occurs;
- allow winding of chips on workpieces or cutters.
All the resulting shavings must be directed strictly away from yourself. Even during the shortest interruption in work, the machine must be stopped and de-energized. Disconnection from the mains will also be required in the event of power failures. In a de-energized state, the machine is removed, cleaned and lubricated. In the same way, disconnection is made before tightening any fasteners.
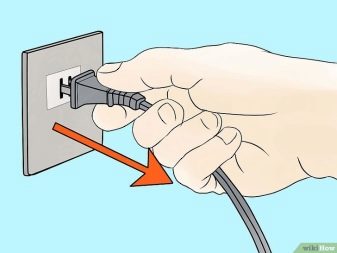
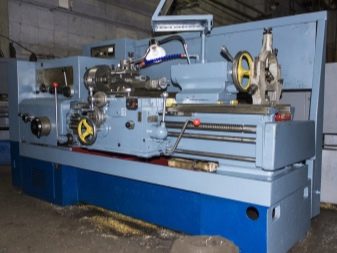
It is not allowed to work on screw-cutting equipment in gloves or mittens. If your fingers are bandaged, you will have to use rubber fingertips. The workpieces to be processed must not be blown with compressed air. Hand braking of parts of the equipment is not allowed. Also, you cannot measure anything along the way of the machine, check cleanliness, grind parts.
When the work is completed, the machines and electric motors are turned off, the workplaces are put in order. All workpieces and tools used are put in certain places. The rubbing parts are lubricated with the frequency prescribed in the instructions. All problems are reported to the management immediately, in extreme cases - after the end of the shift. Otherwise, it is enough to follow the instructions of the technical data sheet and the manufacturer's recommendations.
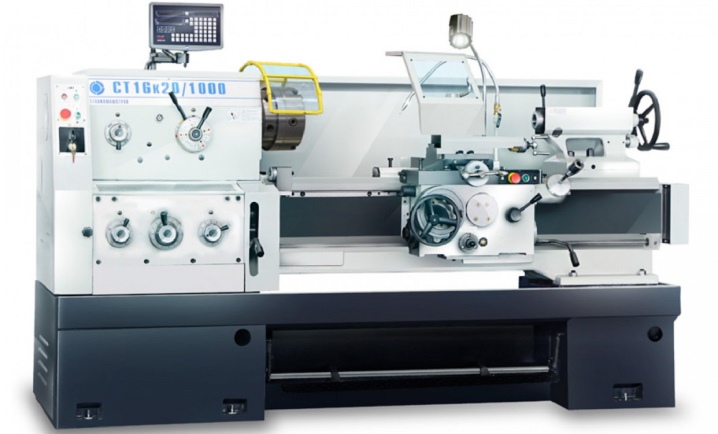
The comment was sent successfully.