Features of lathe calipers
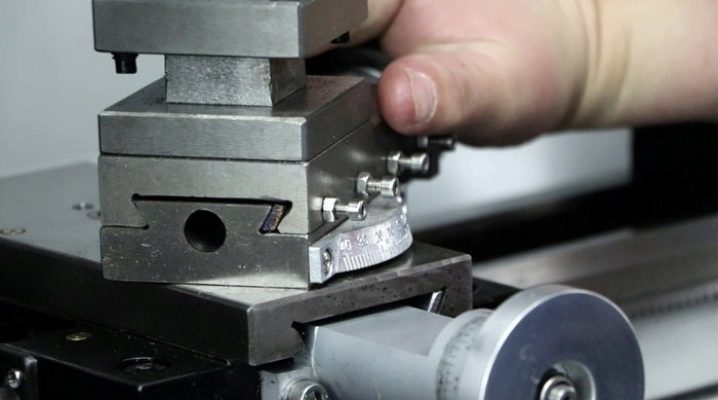
The features of the lathe slides should be studied by everyone who decides to work on such equipment. In addition to the purpose of the caliper, it is worth finding out who first created it. It is also important to find out what parts it consists of. Additionally, you will need to deal with the transverse and longitudinal calipers, with vertical and other types.
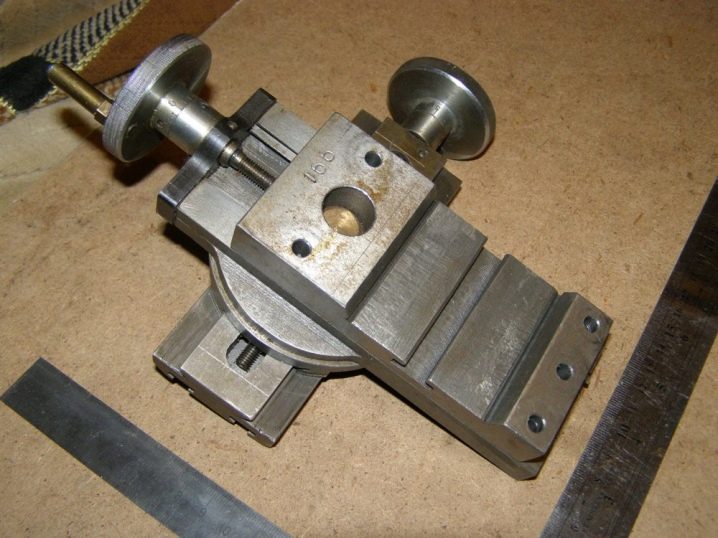
History of creation
The development of mechanical engineering was constrained for a long time not only by the absence of a mechanical engine. An outstanding success was the emergence of a metal-cutting machine with a support, or otherwise - a tool holder. It was his invention that formed the basis of all the successes of turning in the XIX-XX centuries, significantly reduced the cost of technology and simplified the work with it.
Before, since ancient times, lathes changed very little, and the operator always held the cutter.
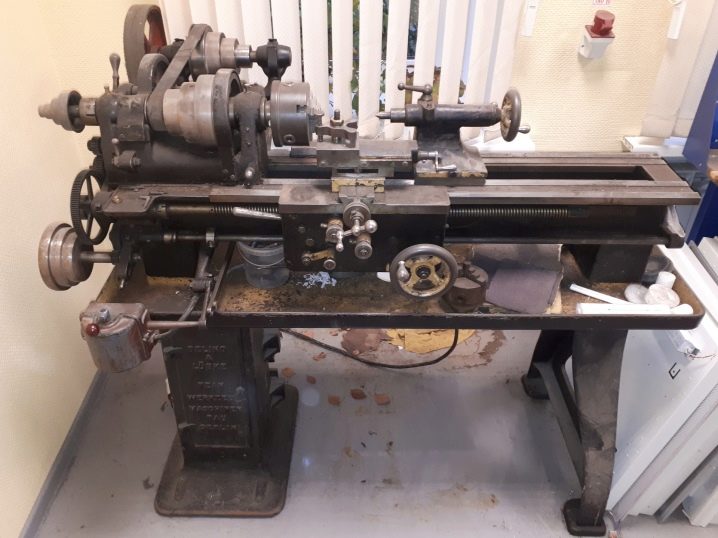
In the 18th century, the early photocopiers with calipers appeared. But it was unique equipment that existed in a single copy. Such equipment could only be purchased by especially wealthy people. The first to create a practical caliper, applicable on mass industrial equipment, by the mechanic from Great Britain Henry Maudsley. This name deserves no less respect than Watt or Fulton. Maudsley significantly improved on an earlier development of the same kind, which was put on a lathe in 1785.
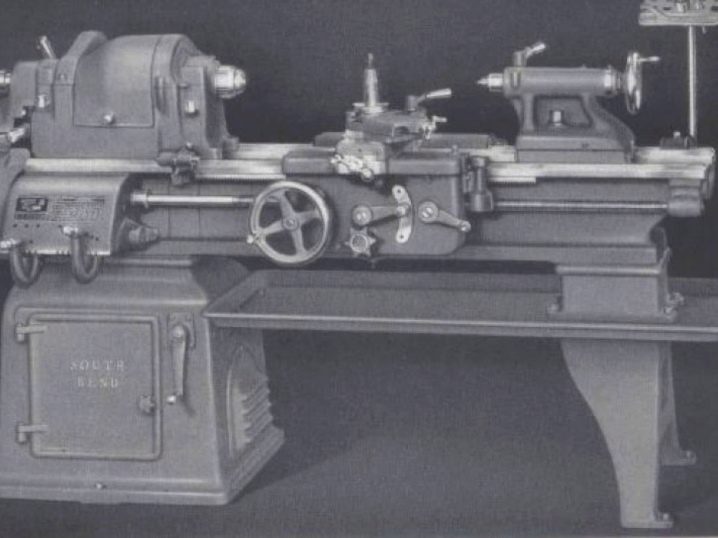
The cross caliper appeared in the mid-1790s. The aim of the invention was to increase the number of manufactured parts, as the traditional manual technique has reached the ceiling of its development. A more advanced design was presented by Maudsley by 1798. It already made it possible to make screws of considerable length; an important feature was the immobility of the workpiece, in relation to which the caliper itself moved. G. Maudsley cannot be considered the sole creator of the holder, but it was his development that turned out to be the most timely.
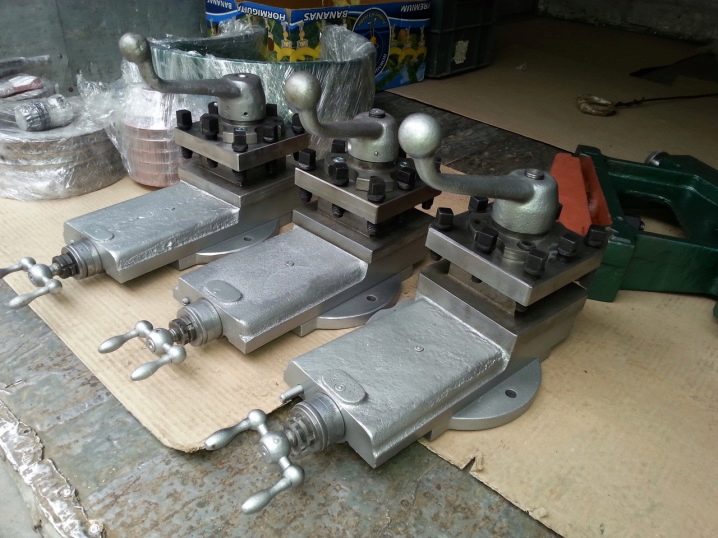
In 1800, he introduced an even more advanced machine. Now it has become possible to form threads with previously unattainable quality and precision. The slide machine concept proved to be so productive that it was taken up by other inventors. For several decades, they used it to create a number of types of machines that are still found in many industries today. So the seemingly modest holder found himself at the origins of all modern industry.
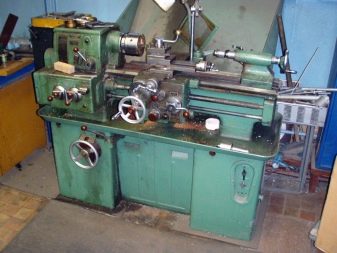
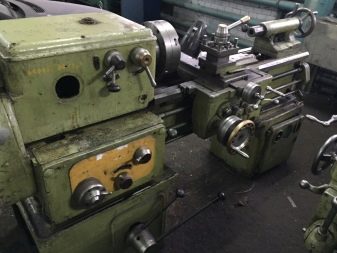
Principle of operation
This principle is precisely the precise movement of the fixed cutting device or other unit used for processing. In some cases, the workpiece is also fixed. The main impulse is torque. It is taken from the lead screw if it is necessary to make grooves or feed in the longitudinal plane.
By feeding the cutting tool, energy is taken from a special shaft.
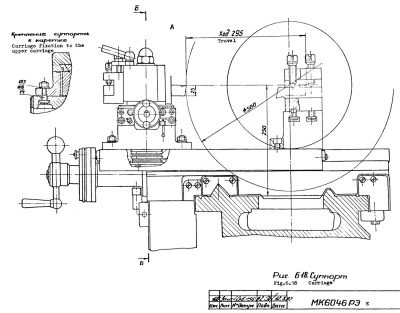
Occasionally a manual drive is used. It is used if both the shaft and the screw are impractical to use. We are talking about such operations as:
- chamfering;
- facing;
- drilling processing;
- cutting the part to be prepared from a larger workpiece.
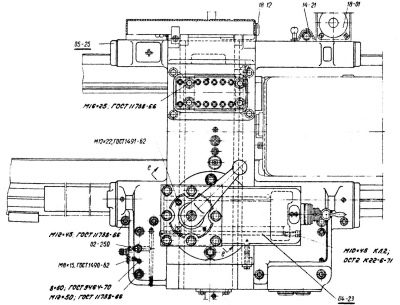
Device and purpose
The role of the lathe support is already clear from its name, which literally translates from Latin as "support". Such a device coordinates the action of the cutting unit. Thanks to him, the feed is performed at a strictly defined amount, within the specified tolerances. A typical caliper consists of different types of parts:
- sled (located at the bottom of the longitudinal and exposed in the transverse plane at the transverse holders);
- a plate that provides a pivot on which the upper type of tool is mounted;
- machine apron.
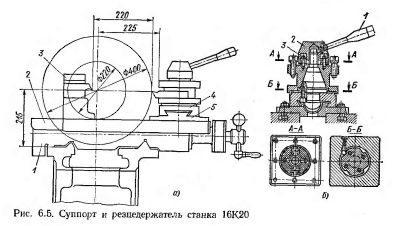
In the longitudinal version, the slide serves as a support and field of movement for all other mechanisms. Inside the apron, there are devices that allow the transmission of a mechanical impulse. During operation, the entire assembly moves. The transverse type implies the extraction of mechanical energy from the carriage screw (although manual operation is also possible).
The device predetermines the course of the rotated plate.
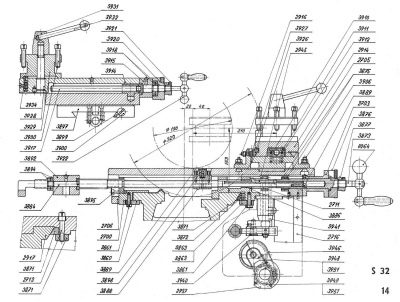
The vertical support moves along the guides installed on the cross member. The designers have foreseen the possibility of his fall. This danger is eliminated thanks to the planks. Facilitation of movement is achieved due to the stop with transverse rollers, on which additional springs are placed. The horizontal movement takes place thanks to a lead screw and a special nut; usually vertical supports can also be deployed in relation to the carriage.
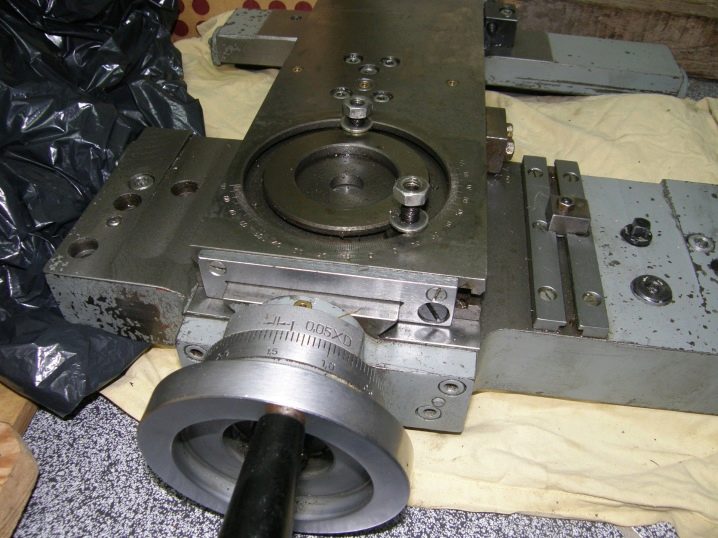
What are they?
Some of the types of calipers have already been said, but this is not worth dwelling on. The way you work is important. Mechanical and automated apparatus is well suited for equipping industrial machine tools. The manual holder is used mainly in personal workshops, where the work does not involve serious effort in operating the equipment.
The longitudinal caliper assembly usually receives impulse from the disk cam via a lever. It also uses a rack and pinion pair and an adjustment bushing.
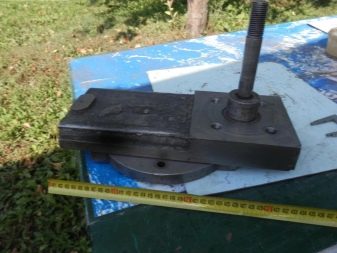
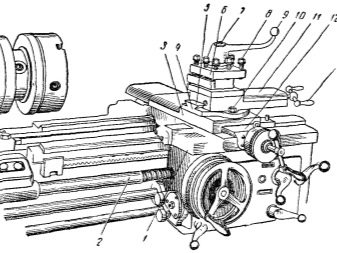
The crank shaft is mounted in journal bearings. The transverse support can be of both horizontal and vertical type; for driving, cams are used that transmit impulse through a set of levers with toothed sectors and a rack and pinion system. Top skids can be found in both conventional lathes and screw-cutting lathes.
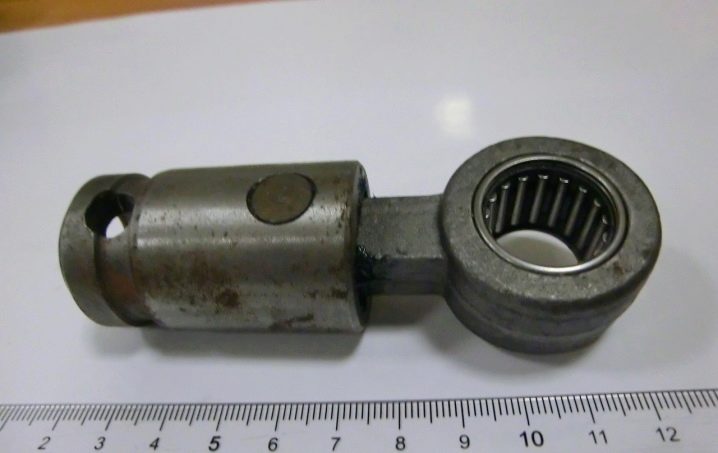
Adjustments
Normal operation of the equipment is possible only with high accuracy of its operation. In particular, the carrier guides are effective only at a certain clearance level. Even minor deviations from this indicator are detrimental. If this value is exceeded, the rigidity of the mates is lost, and errors grow. A screw clamp and a retainer are used to control the clearance.
Sometimes the force provided by the fixing knot is not enough. In this case, there is a risk of fatal deformation under the action of axial or radial loading. The rubbing parts wear out non-uniformly, which does not allow setting identical clearances on each working surface. A pronounced uneven wear is also noted on the drive screws.
Therefore, normal functional travel is maintained by aligning the carriage to the point of least wear.
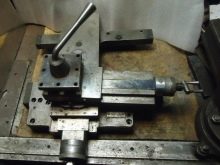
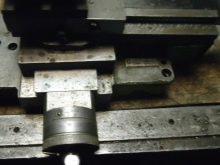
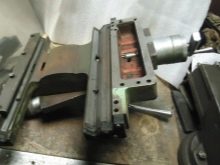
If you do not adjust the caliper, you will not be able to maintain a uniform movement of the slide. They will become locally seized and will stop swaying when force is applied to them from the side. The problem is solved by using wedges. They forcibly set the guides as they should and remove the excess gap. The same wedges will allow the carriage to be pressed against the rails.
It is very important to control the backlash... Its appearance in the helical gear is unacceptable. The problem is solved by manipulating the locking nut. With a long operation of the lathe, the carriage oil seals inevitably become clogged, which manifests itself in the formation of mud strips when the bed shifts. The problem is rectified by washing the felt padding and soaking it with oil; with total wear and tear, it is more correct not to bother with this, but to replace the module with a new unit.
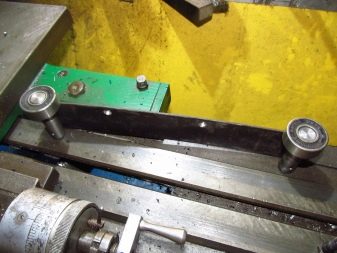
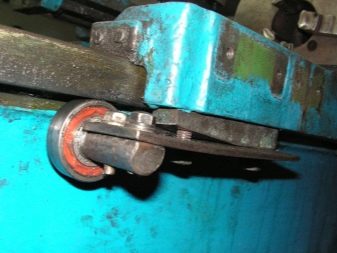
The comment was sent successfully.