Threading on a lathe
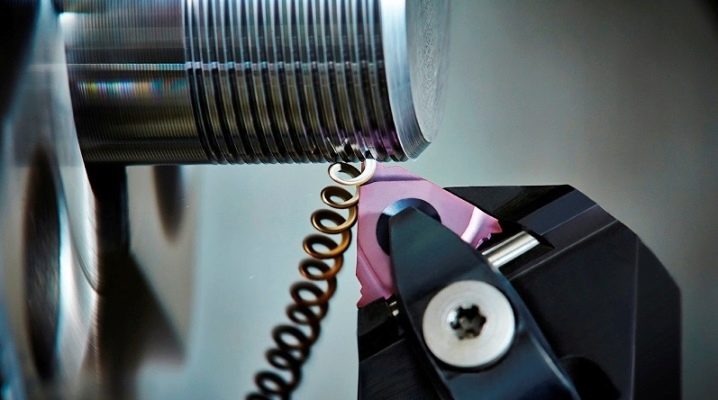
Threading with a lathe has an undeniable advantage: the throughput of the service center where this service is practiced increases 10 times or more. The machine, moreover, makes an order of magnitude fewer errors than the worker.
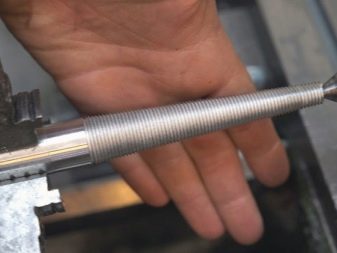
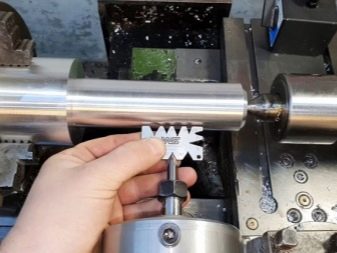
Thread types
Thread blanks are used in the form of cylinders and tapered (tapered) components. In turn, the thread is cut in the form of an external helical (spiral) groove or as an internal one. The structure of a threaded joint is determined by its profile. In practice, several profile types are used:
- triangular;
- rectangular;
- trapezoidal;
- abutting;
- rounded.
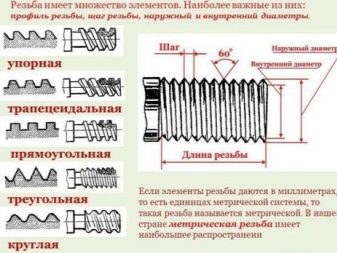
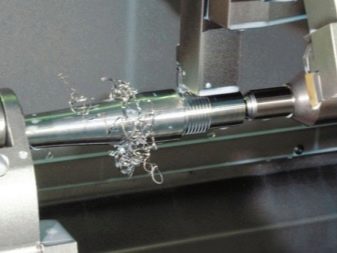
In turn, threaded grooves are made in one or more passes. In the first case, the spiral groove is presented in a single version: only its turns are adjacent to each other, others (accompanying) are not used. The thread pitch is the distance between the central edges (grooves) of the turns adjacent to each other. The path of the thread groove is determined by multiplying the thread pitch by the number of turns or leads of several grooves (if more than one is used).

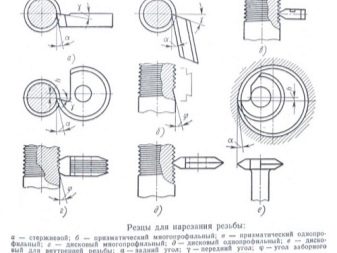
Having decided on the type of threaded connection, the appropriate cutters are selected. Such a tool is a combination of a shank and a working part. The quality level of the screw thread is determined by the performance of these components. The shank has a generally square or regular polyhedral cross-section to ensure centering. It is difficult to secure the cutter in the chuck without a shank. The working part cuts a helical groove. It includes cutting surfaces and sharp edges. The angle of sharpening of the cutter is determined by the alloy from which the part is made. Mainly, steel and non-ferrous metal parts are cut. Having chosen the type of cutter, they begin the technological process.
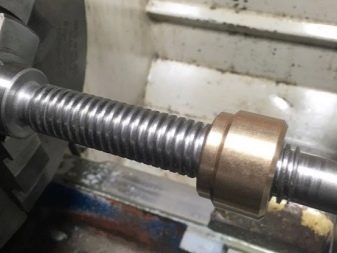
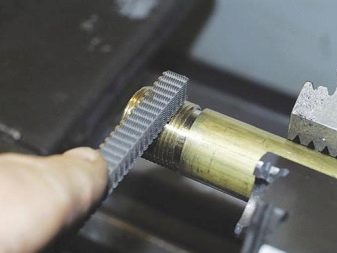
Slicing methods
Moving along the axis of rotation, the cutter leaves a helical groove on the workpiece. One of its main characteristics is the ascent (rise) angle. The angle between the imaginary axis passing through the helical groove and the plane perpendicular to the axis of rotation of the workpiece is calculated in accordance with the value of the torch feed and the speed of the drive (gearbox). The size of the thread pitch is measured while moving along the axis of the workpiece being cut.
As a result, the cutter-performer will receive the cutting that the client ordered. When cutting several grooves (leads), all of them are arranged in the form of uniform spiral grooves. An example of threading a multi-start thread is PET bottles and their corresponding polyethylene caps, for example, for sunflower oil. The difference between bottle caps and studs and nuts is that in the first case the thread is short and does not contain more than one turn.
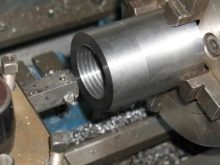
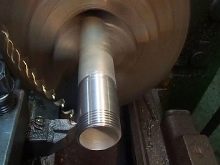
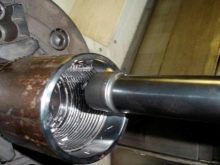
The thread lead for a single-start groove is equivalent to its lead, while for a multi-start thread it depends on the number of coordinated but independent threads. The manufacture of cutters for single and multi-start threads is regulated by the standards of GOST 18876-1973. The same GOST prescribes cutting metric, not inch threads. According to these standards, cutters are produced in the form of prismatic, rod and round cutters.
The outer thread is cut with a bent cutter, and the inner thread is cut with straightened and bent cutters fixed in the working frame. The torch tip is identical to the profile of the helical groove it leaves behind. Prismatic cutters are divided into single and multi-cut.
Disk, in addition to these two varieties, is also produced as a separate tool for an internal threaded groove.
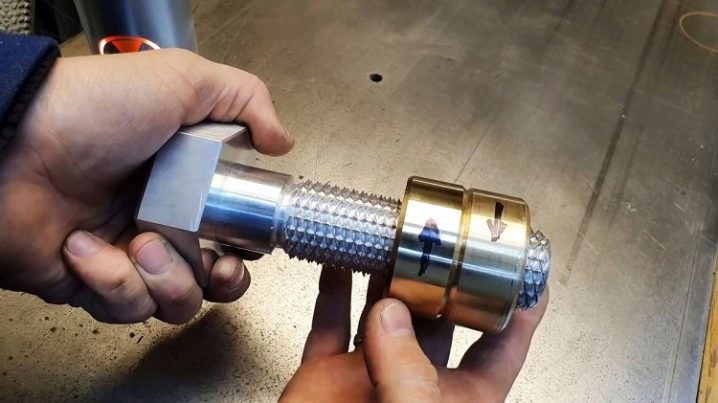
Incisors
This design, in turn, takes into account the following parameters. The rake angle of the cutter is determined by the parameters of the material from which the part is cut. The angle value is between 0 and 250 degrees. When the groove is machined on simple medium or low carbon steel alloy parts, the front angle is zero. The more the steel is saturated with alloying additives, the larger the angle is chosen, but, as a rule, it cannot be more than 100 degrees.
An increase in the impact toughness of a steel alloy forces an increase, an increase in hardness and brittleness, on the contrary, to decrease this value. If you leave the angle for brittle alloys noticeably larger than zero, then chips and cracks will appear on the part. It is unacceptable to use a cutter that is even slightly different in the profile of the cutting edges from the groove that you will need in the future.
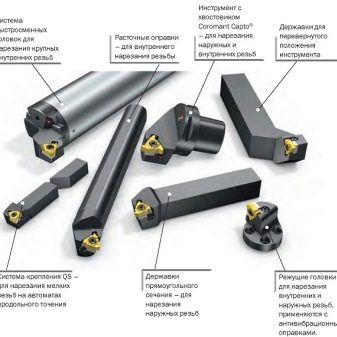
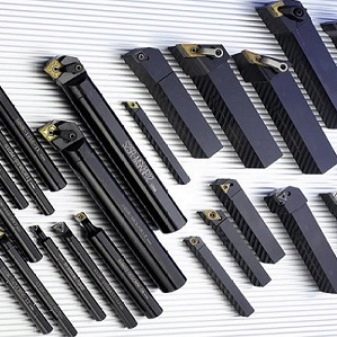
The angles at the back and sides of the cutter are taken such that the cutting teeth and projections do not rub against the inside of the helical groove just obtained. Despite the fact that high-speed steel of special hardness is used as a working material, abrasion of cutting sharp edges will gradually lead to their dullness, and the cutter will be damaged.
The values of these angles are set on both sides at the same value. In the case when the angle of rise, on which the good condition of the thread depends, is selected less than 4 degrees, then the rear-side angles should be set to a value from 3 to 50. At an angle that is more than 4 degrees, the same angles corresponding to it will stop at a value from 6 to 8 degrees.
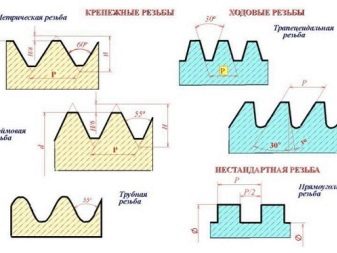
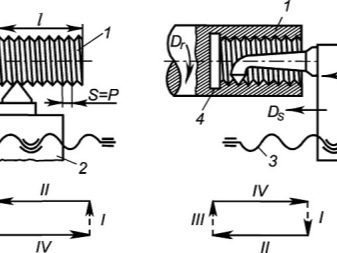
An internal threaded groove is cut in holes pre-drilled through the part. An alternative way of making holes is boring. Parts made of steel are finalized on a machine with carbide inserts made on the basis of T15K6, T14K8, T15K6 or T30K4 steels. In the case of threading on a cast iron workpiece, other carbide cutters are used: from alloys VK4, B2K, VK6M and VK3M.
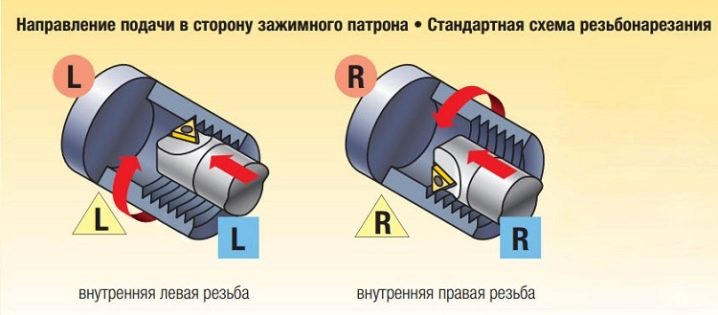
Dies and taps
Taps and dies are wrench and screw-type tools, the inner surface of which is threaded into sectors equidistant from the central axis of the tool. Adjacent sections are spaced at the same distance from each other. The lathe is mainly used for cutting metric threads. The cutters themselves also do not differ in the large value of the diameter of the workpieces for which they are designed. In the case of using cutters designed for machine, rather than manual, cutting, the cutting session is carried out in one step.
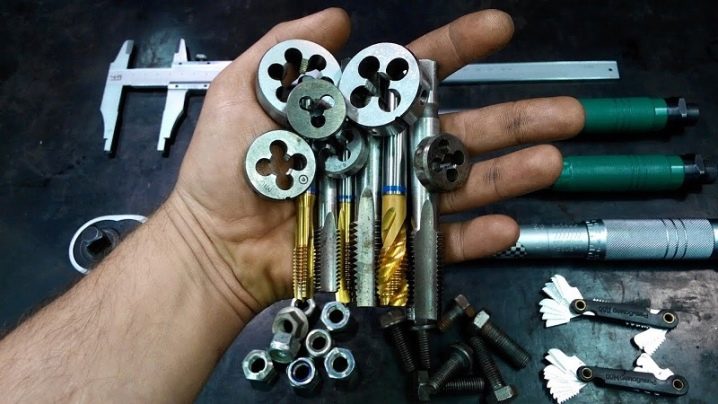
The difference between machine taps and simple manual ones lies in the presence of pick-up and calibration working zones on them. When conventional cutters are used for threading, the craftsman cannot do without the presence of complementary tools. In this case, the first tool cuts the thread roughly, coping with 60 percent of the load, the second brings this performance to 90%, the latter completes the grooving.
This combination can change: rough cutting is carried out for three quarters of the total volume of work (load), and the final cutting is carried out for the last quarter. The pickup zone is noticeably longer on the rough cutter than on the finishing cutter.
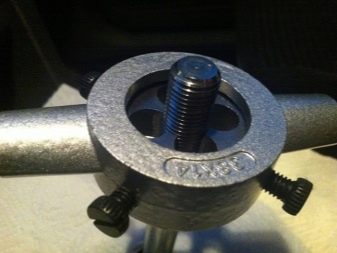
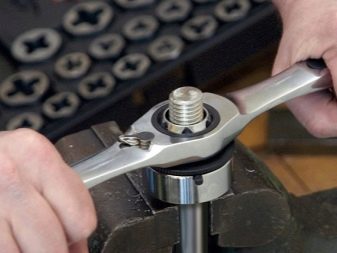
The throughput of the threading machine varies in the following values: up to 12 m of the helical groove (and not the length of the channel or stud to be cut) per minute for steel blanks and up to 25 - for cast iron and all kinds of non-ferrous metal.
For dies, the diameter of the workpiece differs only by small values from the ideal:
- 0.14-0.28 mm - for future threads with a diameter of 20-30 mm;
- 0.12-0.24 mm - for a workpiece diameter with a thread equal to 11-18 mm;
- 0.1-0.2 mm - for workpieces with a diameter of 6-10 mm.
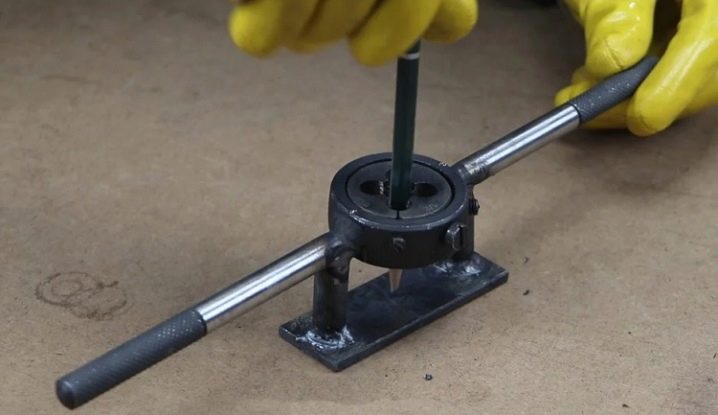
The dies are installed in a special holder located in the chuck of the spindle drive of the unit. In this case, the speed of work will be:
- 10-15 m per minute - for nonferrous metal;
- 2-3 m per minute - for cast iron;
- 3-4 m per minute - for steel parts.
For a smooth fit of the die on the workpiece, the end of the stud to be cut is sharpened to a height of no more than one turn of the future thread. The sharpening should be uniform on all sides, ideally this is also done on a lathe.
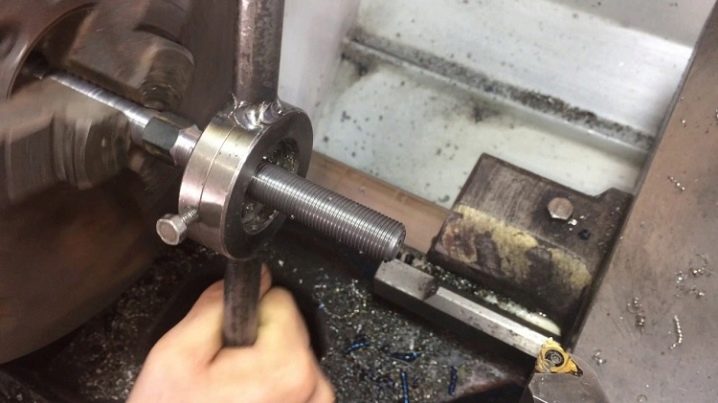
Die head
Tapping with a die head is much less frequent than using dies and taps. The type of thread groove does not matter. The working area of the head is the comb component. Prismatic combs are used primarily for internal threading, while the external groove is cut with a radial, rounded or tangential tool. The principle of operation is based on the divergence of the working components on the return stroke. Thanks to this feature, contact with the cut groove is completely excluded. The combing accessories for internal thread groove cutting are designed as an element containing a taper. When cutting an external thread, comb components of a rounded design are used, which are simple elements in execution.
Rounded combs can be re-machined in order to bring their characteristics to their original values, from which they could deviate during repeated work cycles. When threading with a lathe, using worm or screw elements as blanks that are noticeably longer in length than originally envisaged, the master installs threading accessories on the caliper installation of the turning mechanism, which makes it possible for him to fulfill orders of a larger volume.
Threaded heads are supplemented with simple cutters or cup-shaped elements.
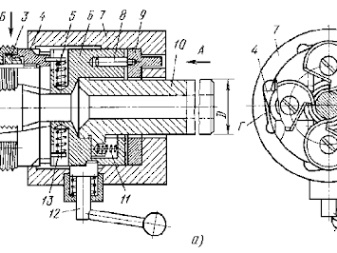
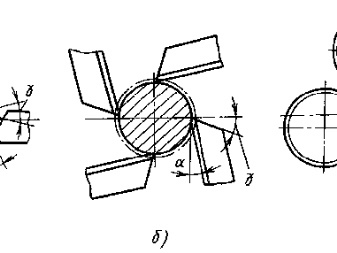
Common mistakes
When rolling a thread on a lathe, regardless of whether it is left-handed or right-handed, as well as when using a CNC machine tool, a template tool is used, thanks to which it is possible to put this process on a wide flow. The planar component of the template component defines the pitch of the thread groove. Calibrated feed-through and non-feed type components are used to gain the most complete control over slicing. The first assumes a profile with a standard length, the second - a shortened one, which allows you to make sure that the average diameter of the workpiece is consistent. If handled carelessly, careless work will lead to the formation of defects on the rough surface.
After the machining session of the part (reinforcement, pipe billet), check the diameter using a threaded micrometer. This instrument should be set up according to a reference pattern to ensure the accuracy of the test. Before checking if the thread matches the stated diameter, clean the flute and dirt you just made with the tool.
Be sure to use industrial or engine oil. Do not use the tool dry; overheating of the die, tap, or thread head will damage the torch being used. Even tools that are victorious and with diamond grit deteriorate when the heat is released from 900 degrees.
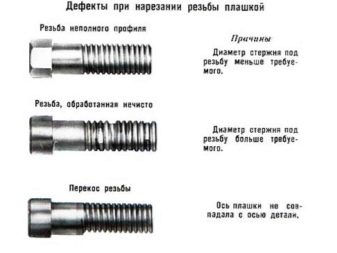
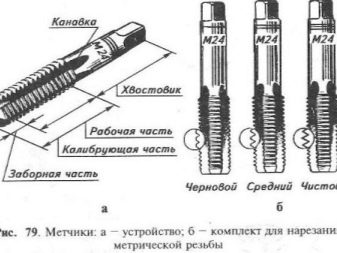
For information on how to cut threads on a lathe, see the next video.
The comment was sent successfully.