Features of a steady rest for a lathe and its installation
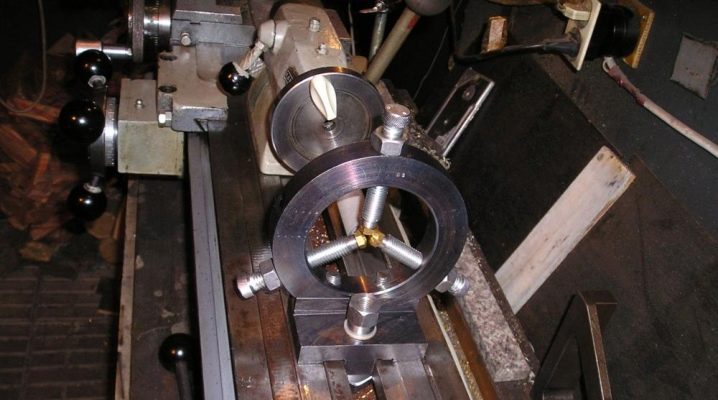
Information about the features of a steady rest for a lathe and its installation will be very interesting to everyone who creates a small-scale lathe. This technique works on metal and wood. Having figured out what it is, what are the requirements of GOST and the subtleties of the device, it will also be necessary to study the features of movable and fixed lunettes.
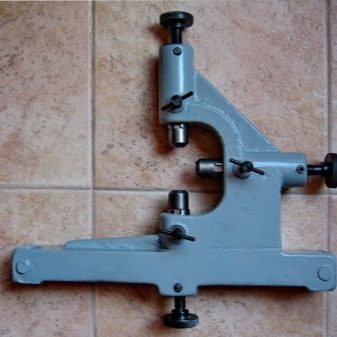
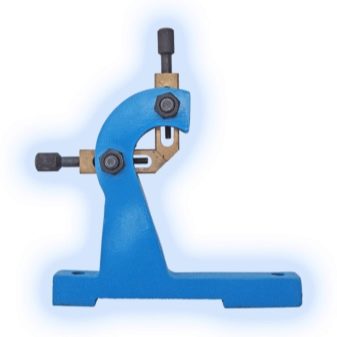
What it is?
Machine tools perform a large number of useful functions and are the true skeleton of the entire modern world, much more important than political institutions, payment systems and religious denominations. However, even these devices "in their pure form" can rarely perform their function most efficiently and with minimal labor costs. A very important role is played by the "external strapping", the presence of various accessories. Even safety and convenience at work depends on them.
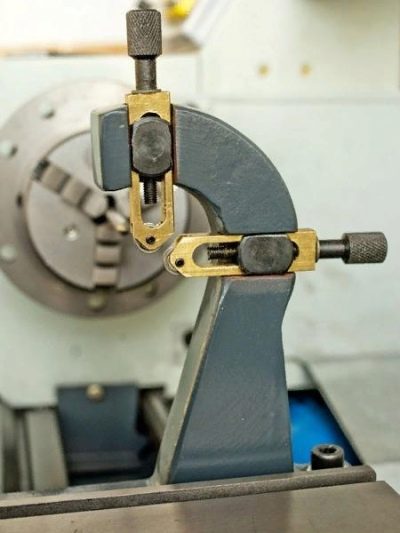
A steady rest for a lathe, and, more importantly, for a lathe both for metal and wood, is responsible for very significant functions. First of all, it acts as an auxiliary support. Without a steady rest, it would be much harder to machine heavy bulky parts. Some of them would have been impossible to work with. Another important point is the elimination of deflection.
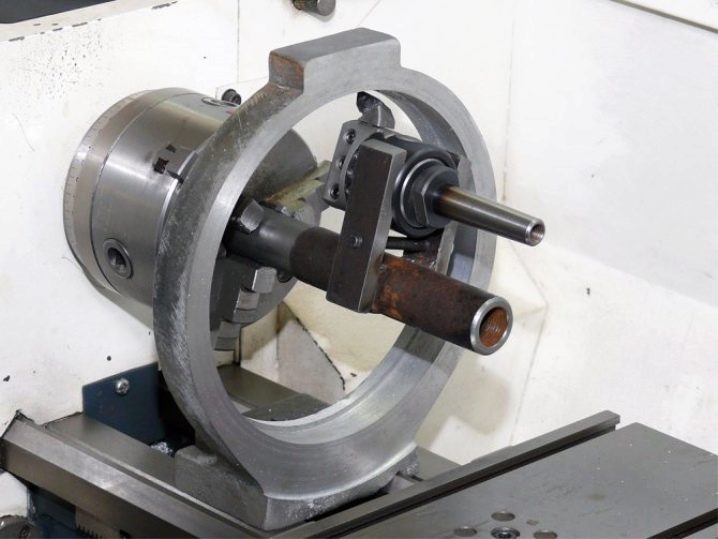
Long workpieces can be bent under their own load. Only additional fixing points allow working correctly, without errors and deviations. By default, the rests are equipped with special rollers, which ensure that they perform their functions in production. A steady rest is especially relevant if the length of the part is 10 times or more greater than its width. Then no natural strength and rigidity of the structure by itself is not enough to prevent deflection.
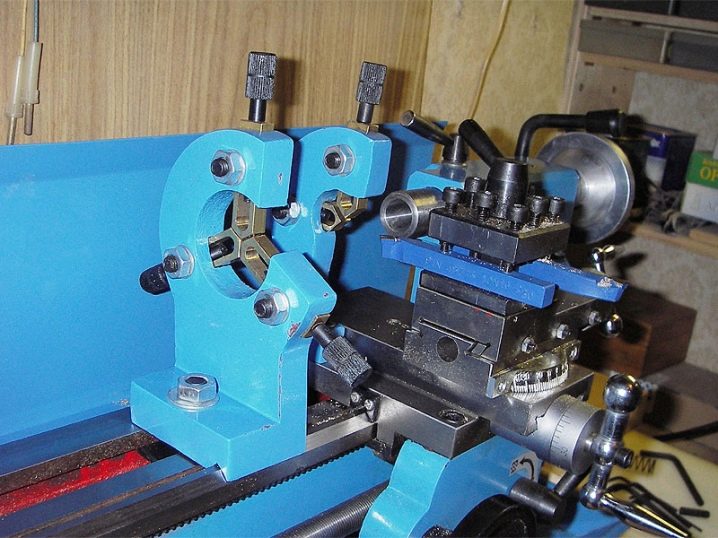
Species overview
It is clear that such an important production tooling could not be ignored by the developers of quality standards. Moreover, 2 different state standards were developed at once. Both were adopted in 1975. GOST 21190 refers to roller rests. GOST 21189 describes prismatic lunettes.
One way or another, both of these device options are placed on automatic turret lathes (the official name of the lathe).
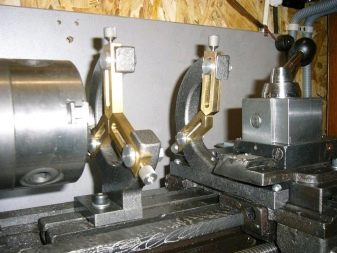
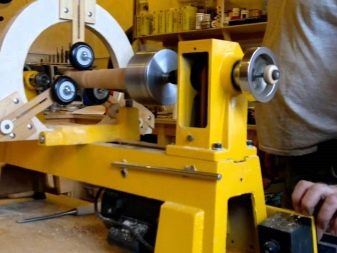
Static
From a practical point of view, however, their other division is more important - into mobile and stationary types. It can be very beneficial to use a steady rest. It provides exceptional manipulation precision. Such equipment dampens all vibrations that occur during normal operation of the machine. The connection to the bed is done by means of a flat plate. The very joining of the parts is performed on bolts.
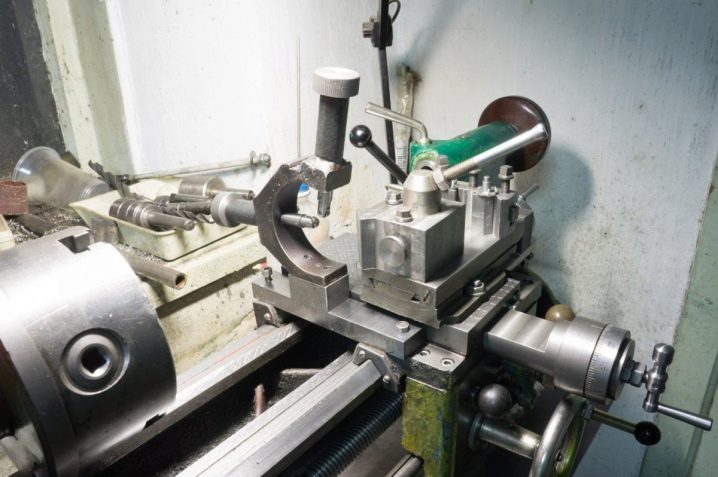
Mostly the stationary unit is equipped with 3 rollers (or 3 cams). One is used as the top stop. The remaining pair serves as side fasteners. This connection is very powerful and reliable. It does not loosen even under an impressive mechanical load.
The composition includes, in addition to the base:
-
hinged bolt;
-
fixing screw;
-
clamp bar;
-
screw control mechanisms;
-
hinge;
-
special nut;
-
hinged cover;
-
special heads.

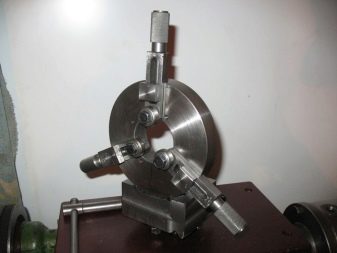
Movable
The mobile rest is also a specific reason. Special fastening channels are formed in it. Such a unit is made in one piece. A fairly complete picture of its form is given by a comparison with a question mark. There are usually two support cams in the movable version - top and side versions; instead of the third support, the cutter itself is used.
It is worth considering other criteria by which lunettes may differ. Basically, such devices are cast from cast iron.
Its use makes it possible to exclude deformation of a brittle and mechanically unstable workpiece. A protective coating is applied over the cams, and its selection is carried out by the manufacturers individually. The cams are made of carbide to avoid premature wear.
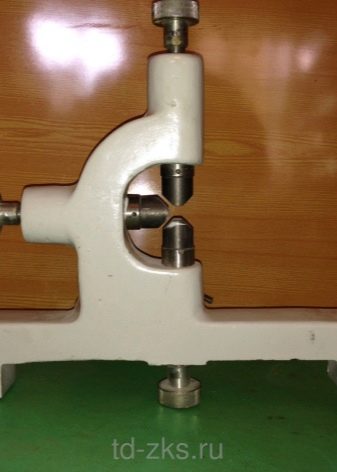
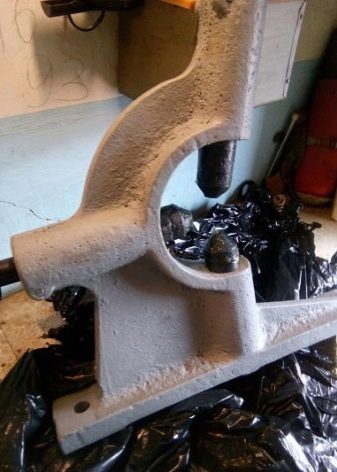
Along with the cam, the already mentioned roller locking system can be used. The cams allow for more efficient control of the placement of the workpiece in the process. But the rollers make it easier to slide (move). It all depends on the priorities of the buyer. Additionally, you need to pay attention to:
-
purpose (turning, metal grinding, bearing production);
-
the number of fixing elements (sometimes there are not 2 or 3, but more, which increases the reliability of fastening, but also complicates the design);
-
method of adjusting the clamps (manual method or a special hydraulic device);
-
inner diameter;
-
dimensions of the workpiece.
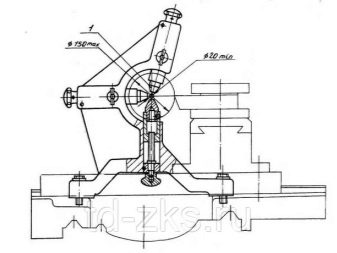

The mobile steady rest is attached to the support carriage. It is used if it is necessary to form grooves on the cams. This machine is also suitable for particularly clean turning. By adjusting the cams, you can then attach parts of different sizes. Their limiting section sometimes reaches 25 cm.
Mobile rests are considered suitable for particularly precise manipulation. Their advantages are also:
-
expanding the functionality of the machine;
-
reduction in the number of defective parts;
-
ease of installation and setting the required parameters;
-
increased in comparison with stationary analogs the degree of safety.
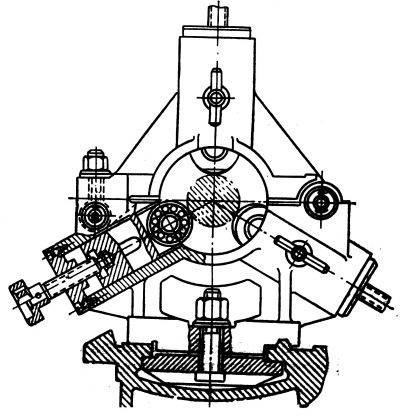
It should be noted that any steady rests reduce the productivity of turning. Quite a lot of time will be wasted on fixing, rearranging and adjusting them.
Sometimes you have to check the fixation accuracy many times. It is even necessary to pre-process the workpiece so that it does not cause problems at the fixing point. The costs of purchasing and using a steady rest depend on many circumstances and cannot be estimated without taking them into account.
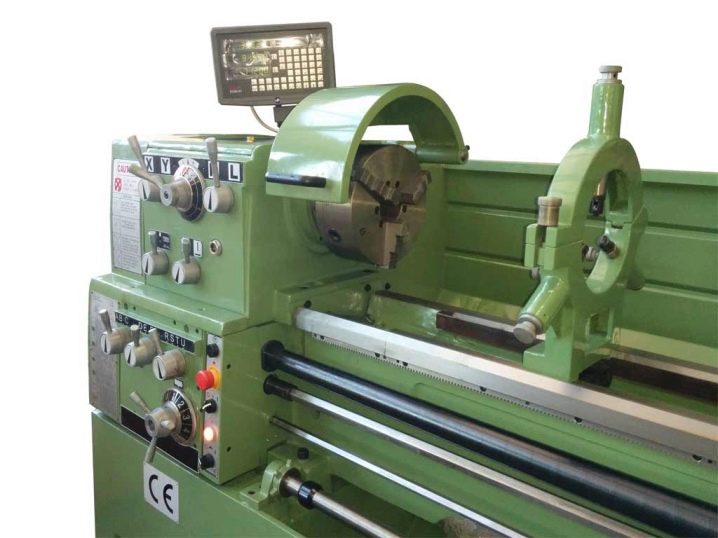
Along with the factory ones, self-made lunettes can also be used. The need for this is due to the high cost of branded models. For each lathe, both a factory and a home-made steady rest must be created individually. The base will be a flange, which is usually intended for connecting pipes. The cams are replaced with studs (3 pieces), the thread of which is 14 mm, and the length is 150 mm.
The studs are placed so that the letter T is obtained. The butt end can be made by a turner on the basis of 3 pointed bronze caps. The internal thread section in this case is 14 mm. A special mechanism assembled from 3 nuts helps to adjust and fix the cams. Each such mechanism must be separate for any cam.
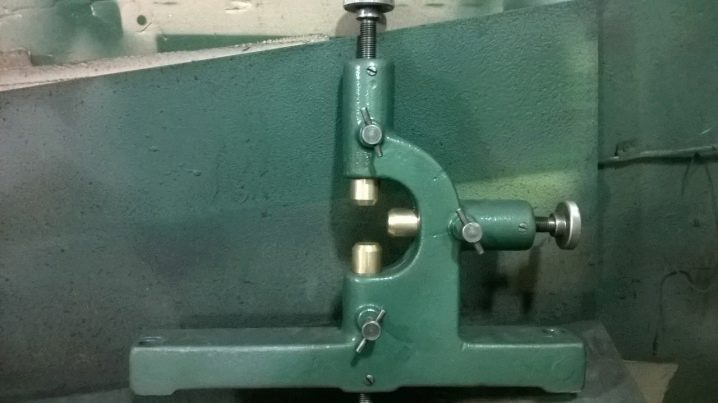
The fixing pad on the bed is created so that it is able to move along the runner. The possibility of fixing it at a certain point is also envisaged. The optimal workpiece for the lining is considered to be a corner, the layer of steel in which is at least 1 cm, and the size of the shelves is 10 cm. The length of the corner blocks is selected equal to the width of the bed runners, which ensures the grip of the guide parts. A nut is screwed onto the cam blocks, and these hardware are screwed by an engraver into other nuts, which are welded in advance (they will serve as clamps).
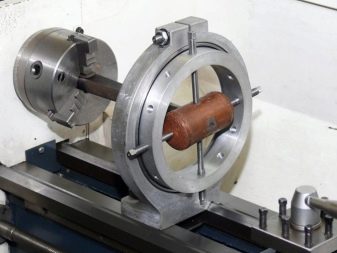
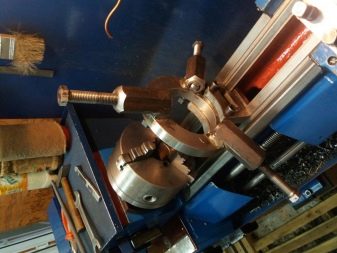
How to install and configure?
These manipulations affect the effectiveness of subsequent actions almost more than the characteristics of the lunette itself. Therefore, such work should be approached with all responsibility. Most often, the rest apparatus is placed at the required point using a bolt.It is important to do this before placing the workpiece in the center. Any stops - both cam and roller types - must be screwed to the limit into the base.
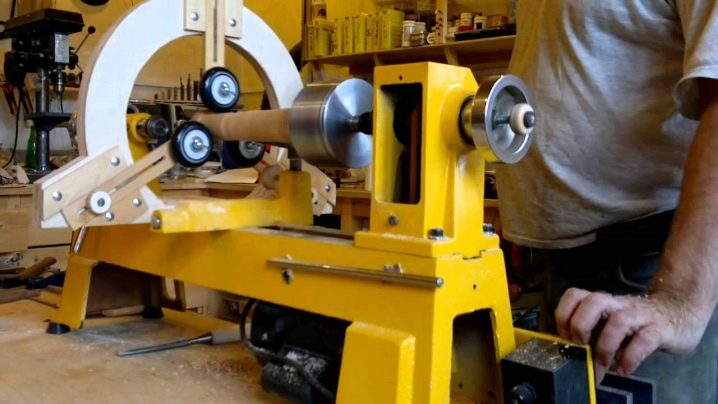
The movable section of the steady rest must then be folded back. A special hinge will help in this. When such a manipulation is made, the part is fixed on the machine. Next, you need to establish its cross-section at the point of the upcoming contact with the steady rest. Then the lid is closed.
So that it does not open arbitrarily, it is pressed to the base with a specially prepared bolt. The next step is cam extension or roller adjustment. It is at this stage that the diameter of the gap and the section of the workpiece are matched. Normally exposed cam pieces rest against the part.
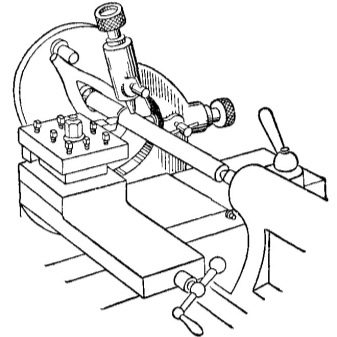
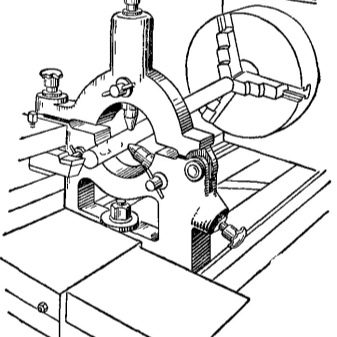
It is imperative to check whether it rotates uniformly when scrolling.
It is possible to expose the rest part on a lathe:
-
using an adjusted workpiece with precisely specified parameters;
-
using steel round timber;
-
with the use of the rack part, into which the micrometer is mounted.
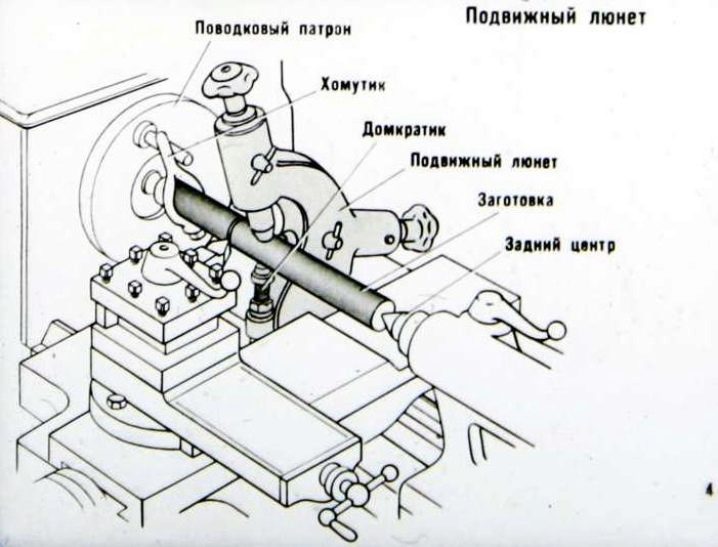
The first way means the need for meticulous fixation of the structure in machining centers. And also the increased accuracy of the circle is important, especially where there will be contact with the steady rest. This means the need for an early recess. Precision gauges are needed if alignment is made to machined blanks before such parts are available to technicians. It is not always advisable to adjust the stops in this way in everyday production practice. Therefore, an alternative way of solving the problem was created - using steel round timber. In this case, they check how well it rotates. The twist should be free. Any unnecessary loads and vibrations during operation should be completely absent.
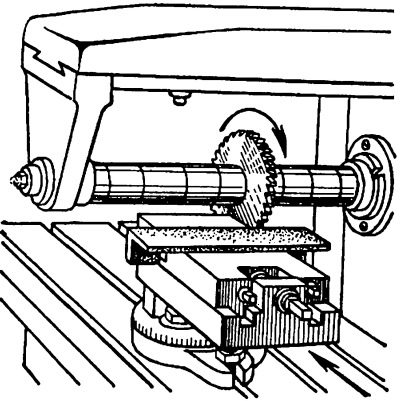
The steady rest can be used only if the workpiece has an ideal geometric characteristics. Processing of blanks with irreparably distorted parameters is not allowed. First of all, the lower cams are brought under the part. The meter determines the distance along the entire length. The distances should be kept as uniform as possible.
If the bezel is placed not for roughing, but for finishing, then the installation goes like this:
-
determine the required point on the part;
-
measure the desired section;
-
fix the mandrel in the headstock;
-
expose the device exactly along it;
-
removing the mandrel, put the necessary part in its place;
-
the steady rest is placed in the same way as before, keeping in mind its strict parallelism with respect to the place where it was adjusted according to the mandrel.
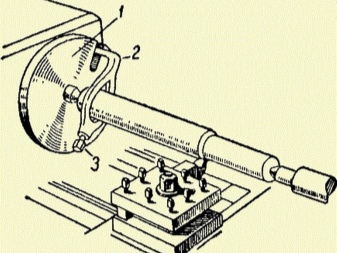
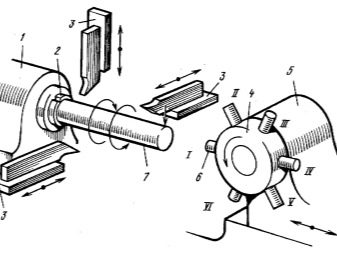
The comment was sent successfully.