Vertical turning lathes
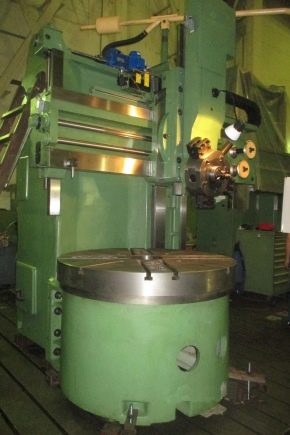
Vertical turning lathes can be very good equipment for many industries. But you need to find out exactly what their purpose and main components are, what the gearbox is equipped with. And you will also have to study other features of the device, cams of CNC machines, get acquainted with the selection criteria.
Device and principle of operation
It is very difficult to say exactly what the general view of turning-boring lathes is. They are represented by a very large number of modifications. And each version is optimized to perform a very specific range of manipulations, which is predictably reflected in its appearance and technical performance. Universal models of vertical lathes are gradually spreading. But there are still very serious differences between them.
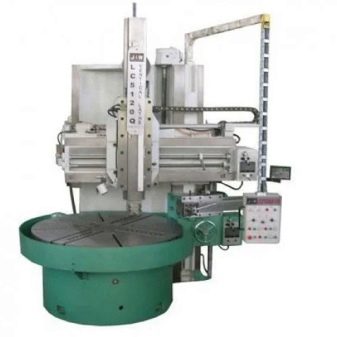
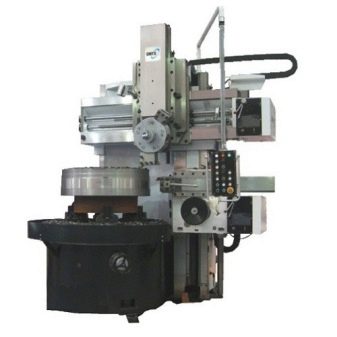
The main nodes in the device diagram are:
- racks;
- a transmission link that provides the connection of the main parts with the drive;
- Checkpoint;
- cantilever assembly, thanks to which the spindle moves;
- calipers (located on the left and right);
- technical cover;
- cradle for faceplate;
- a pair of feed boxes;
- operator control system;
- power control unit;
- electrical panel.
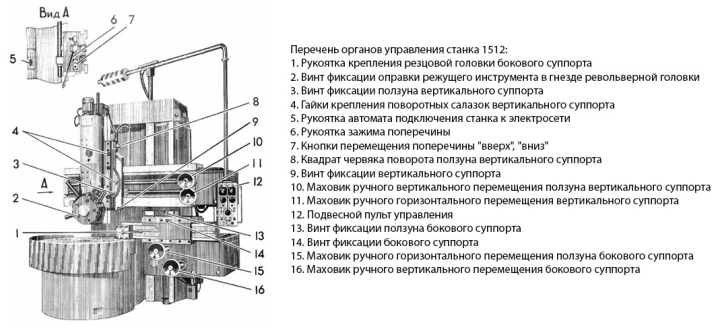
With the help of vertical turning lathes, you can perform a variety of manipulations:
- cut a groove;
- give the required shape to the surfaces of cylindrical or conical parts;
- prepare holes with the required parameters;
- grind flat areas;
- unfold a metal workpiece;
- arrange carving;
- make a shaped surface.
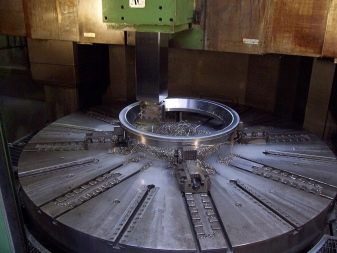
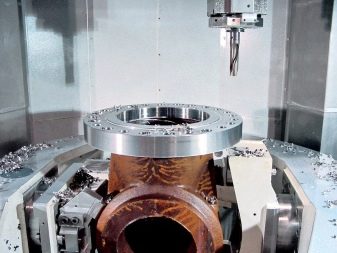
Boring and milling jaws are used on boring lathes.
They can be designed even for models with large faceplates. With their help, the workpiece is attached perfectly, even if it is heavy and large in size. Typically 4 or 8 jaws are included in a typical set. Vertical turning lathes are increasingly software controlled (i.e. numerical control is used).
This approach minimizes the danger associated with the human factor. Thanks to him, the processing accuracy increases significantly. Moreover, such equipment allows you to work at speeds that are completely inaccessible even for the most experienced carousel turners working on simple equipment. Manual versions are used for industries limited to simple turning operations or for rough machining of structures. The workpieces to be processed are mainly fixed in the faceplate holders.
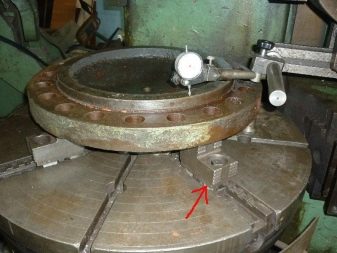
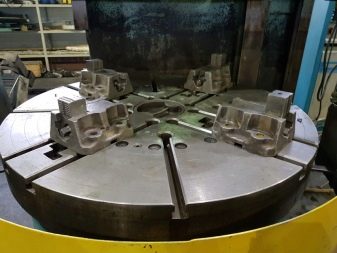
Next, start the rotation at low speeds. This run ensures that the workpiece is centered correctly. Then the spindle head is brought in. It is moved along the traverse. Last of all, the fluid supply is started, which lubricates the machine and removes excess heat.
The regulation of revolutions and processing modes depends on the degree to which the gearbox is equipped, what components are present in it, how they are configured. All this is designed taking into account the selected kinematic scheme.
There are vertical lathes with one or two stands. The two-post version is capable of handling larger workpieces and is very efficient at the same time. The beds of the two-post apparatus contain a cross member with boring and revolving calipers.
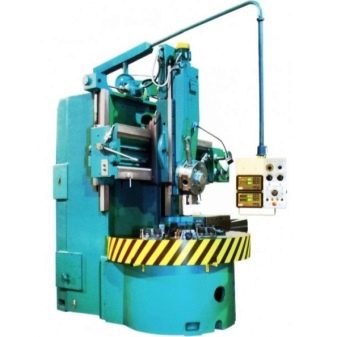
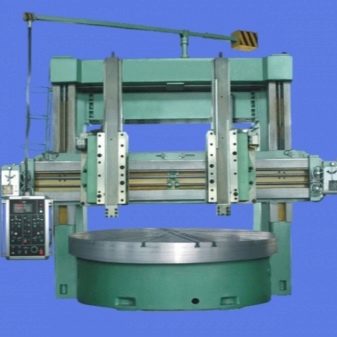
For the movement of these calipers, usually horizontal guides are provided. The boring block has a longitudinal carriage with a turning mechanism. Part of the mechanism is the slider, on which the cutter holder is placed. Correct use of the boring slide and the attachments added to it allows you to:
-
work with tapered surfaces;
-
bore holes;
-
cut through the inner grooves.
Regardless of the specific nuances, such machines are designed for manipulating parts with a section that significantly exceeds the length. Most often, we are talking about sections of more than 50 cm. It is easy to understand that such a technique is in demand in specialized branches of mechanical engineering, where it is required to produce large products.
A mechanism such as a carousel allows you to move the desired items along a completely closed horizontal path.
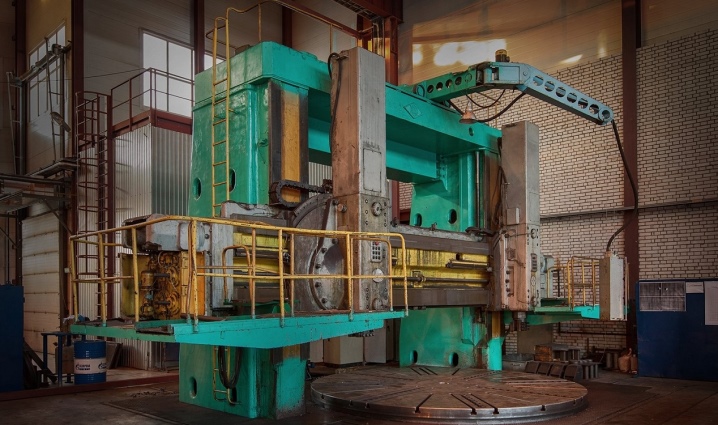
If the cutting element of the boring lathe works with an end face, then annular grooves will form on it. If you move the tool itself in a horizontal plane, then you can no longer grind circular, but spiral grooves. By varying the operating modes and fine settings, it is possible to quite drastically change the pitch of these grooves. The grooves are worked out to an arbitrary depth - it will depend only on how intensively the working block is buried. There are tools that allow you to form grooves also on the sidewalls - it does not matter if these sidewalls are located inside or outside.
Species overview
By appointment
Versatile models are optimized for a wide range of operations. Of course, they lose in the perfection of the production of individual manipulations. Specialized devices are narrowly focused, but specific types of work are performed flawlessly. A universal turning and boring lathe most often has a single stand. The sizes of such devices have their own range of sizes, and the selection of these dimensions is determined by the section of the workpiece.
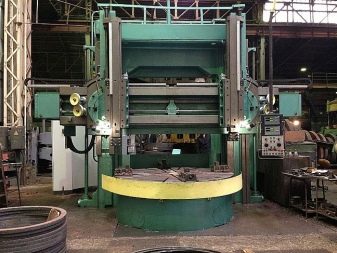
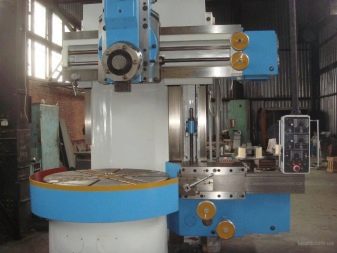
Highly specialized turning and boring machines are usually designed on the basis of universal samples.
Specialization can be achieved:
- an increase or decrease in the height at which processing is carried out;
- changing the number of calipers;
- adjustments to the design of the calipers;
- the introduction of auxiliary drive heads;
- adding to the design of nodes that allow you to perform complex actions.
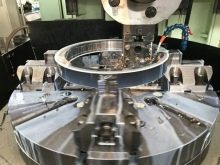
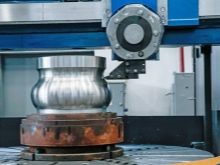
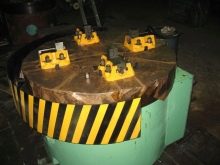
By the number of support points
Single column machines are preferably equipped with a numerical control system. They allow you to handle structures with a cross-section of no higher than 150 cm. An additional area of application is the manipulation of tapered surfaces. Each single column machine contains a side support with a universal holder.
The two-post type of the device is characterized by increased rigidity and reliability, therefore it is used for work with especially large weighty workpieces. The movement of the cross member and supports is achieved with the help of a special unit - "portal".
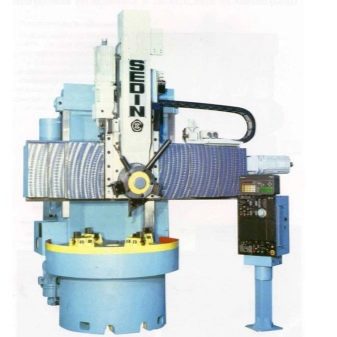
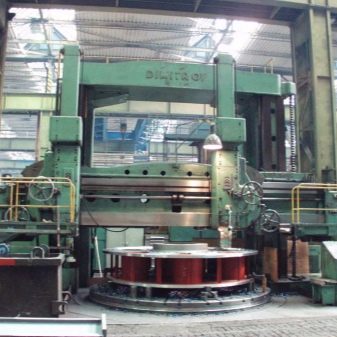
By the number of calipers
There may be one or several of them. Single-support models are distinguished by a relatively narrow field of application.
The more such elements, the wider the scope of application.
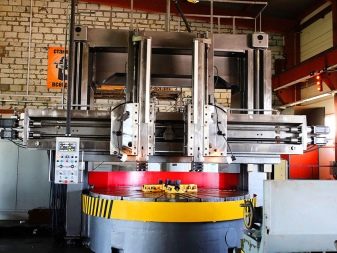
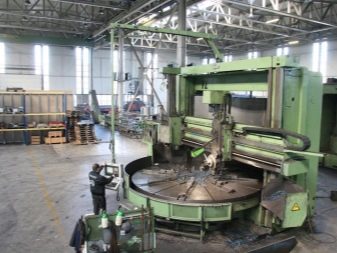
By type of spindle head
The usual design is based on a single cutter. A more modern type is the turret. With it, you can use several cutting parts at once. The movement is oriented both horizontally and vertically according to your choice. The cutters are put into the head one by one, and one by one they get down to business.
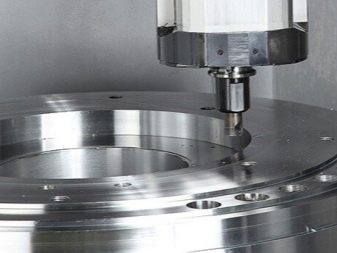
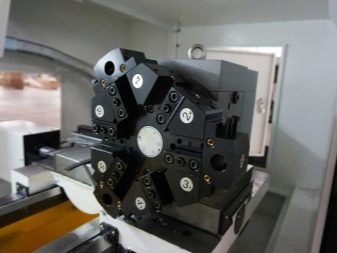
By the type of control of working movements
In ordinary workshops and at home, manual techniques are often used to process metal. Despite the simplicity and lightness, such devices have a minus - you will have to act very carefully. Such a technique can only cope with simple tasks, and even when they are performed, the human factor plays a huge role.Therefore, even in the household segment, CNC machines are becoming more and more convincing leaders, despite their increased price.
It is worth paying attention to the parameters of the equipment. Typical machines, which are supplied in many by the industry, in addition to the main electric motor, have several auxiliary drives. These special units allow more precise control of the individual parts of the production machine. The larger the parts, the more powerful the power plants should be. In the industry, it is not uncommon for turning equipment models that consume 10 kW of electricity or more.
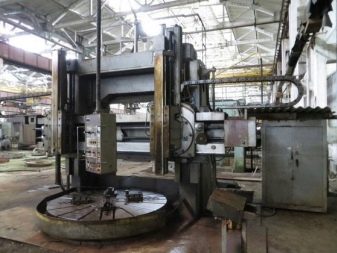
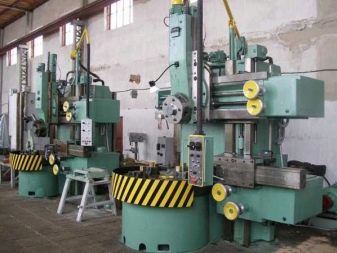
The increased pace of the carousel technology is largely due to the specifics of mounting faceplates. He is also counted on for increased accuracy of manipulations. Therefore, it is possible to perform work that requires strictly limited tolerances. It is worth paying attention to the maximum height and cross-section of the blanks. The height of the structures can vary - in different cases it is 80-500 cm.
The accuracy with which the parts will be processed is determined by the quality of the key block settings. As already mentioned, when using CNC, this figure is maximum. Some high-precision contouring machines can demonstrate even lower error rates.
However, it will not be possible to maintain work at such a high level all the time.
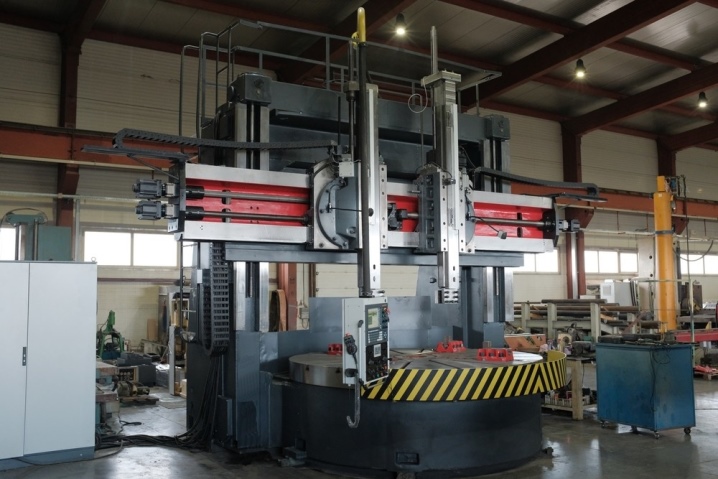
Top Models
The boring lathe market contains a large number of different models. Dalian Guofeng Machine Tools makes a good offer. Its models 5231, 5240, 5250 can compete confidently with the best domestic designs. They are distinguished by increased accuracy and are quite practical. Even blanks with complex geometric shapes can be successfully processed.
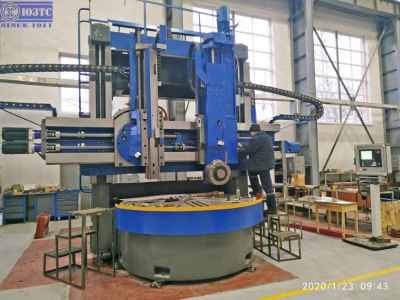
All the models just described have two stands. But there are also single-column versions in the assortment of the Chinese company. Their power is no less than 22,000 watts and no more than 45,000 watts. Modifications from 5110 to 5131 are numerically controlled. Such equipment is quite effective, complemented by special servos.
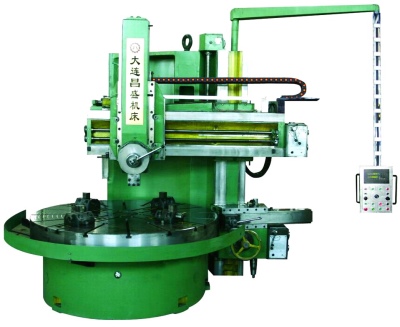
You will have to pay more for the products of the Swiss company ENCE GmbH. However, her quality indicators are also higher. This manufacturer is able to offer several lines at once. So, LEN 3000-5000 are machines without CNC by default, but if necessary, such a control unit can be added. The main power module has a couple of stages. Its electric motor is capable of delivering 16 different speeds.
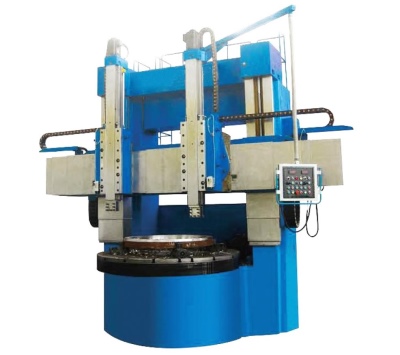
If you need to work with blanks from 125 to 200 cm in size, LEN 1250-2000 series should be preferred... These devices have roller guides. The rollers themselves contain rolling bearings manufactured with very high precision. Error reduction is also achieved with balanced tool holders. To increase the reliability and stability of the equipment, it is equipped with electrical parts from Siemens.
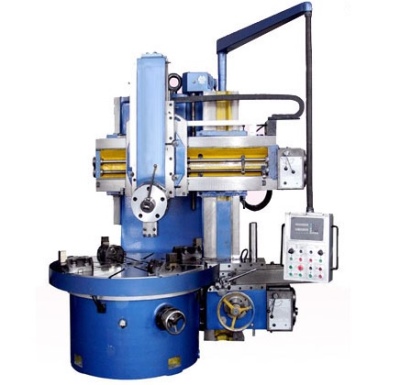
Among domestic firms, the Krasnodar Heavy Machine Tool Plant should be mentioned. He supplies several models of vertical lathes at once. To move the caliper, they are provided with hardened steel guides. The two-column design uses a pair of turret calipers, or a combination of turret and boring units. Some models allow the use of high pressure liquid cooling.
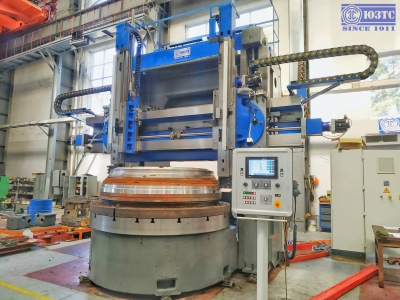
The version 1A516MF3 from the Stankonov enterprise also deserves attention. Its stand is attached to the table with bolts (the spacer acts as an intermediary). The cast iron cross member is produced by casting. The device can handle workpieces weighing up to 10,000 kg.
Caliper feed adjustment is stepless.
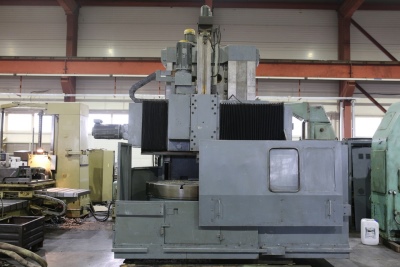
An alternative is the products of the "TBS" company. More specifically, the single-column versions 1512 / 1516F11 and 1512 / 1516F3. They use feeds with separate drives. By default, turret calipers are used; at the request of customers, it is provided to equip with special clamps that simplify the processing of wheels.High reliability is maintained thanks to centralized lubrication.
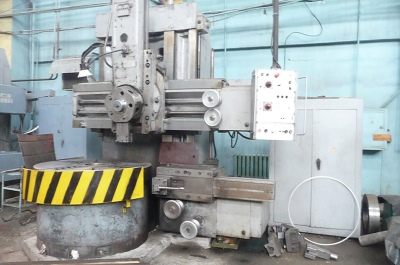
Criterias of choice
Vertical turning lathes can have large diameter faceplates. It determines how large the equipment will be and the size of the workpieces. In turn, the rate at which the faceplate is rotated determines how efficient the system will be. Single leg models are needed to produce tapered parts. Two-post versions are more popular when working with workpieces with a cross section of 160 cm or more.
In a number of cases, the choice of metalworking methods plays an important role. And their feasibility on a specific machine depends on how far the working units move vertically and horizontally. By varying the angle of inclination of the caliper, it is possible to influence the geometry of the manufactured products. It is the more sophisticated and varied, the larger the angle of deflection is provided by the designers. There are other parameters that are also important to consider.
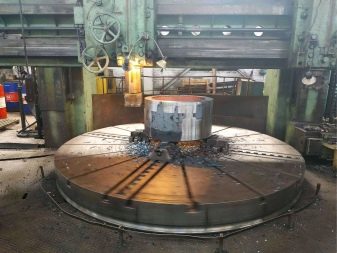
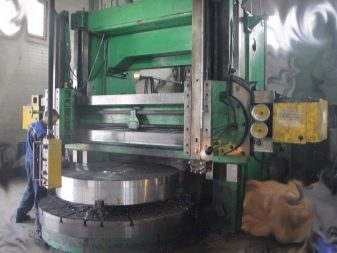
So, in addition to the highest and lowest speeds of the faceplate, you should pay attention to the number of gradations. The larger it is, the more accurately you can adjust the operating mode. But the flip side of this advantage is the complication of the kinematics. It is more difficult to calculate it, and the likelihood of some kind of failure during work increases. It is useful to pay attention to the capacity of the tool magazine.
If it is large enough, the metal processing process is simplified. Ideally, you can concentrate the entire production chain on one or more machines of the same type. When choosing a CNC device, you should think about the accuracy of the action of the executive units. The critical point is the accuracy with which the rotated faceplate is fixed; any yaw of it from a given angle is unacceptable. For the efficiency of tool change, machines with turrets are distinguished.
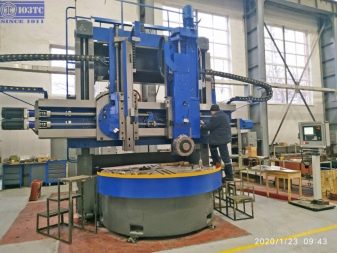
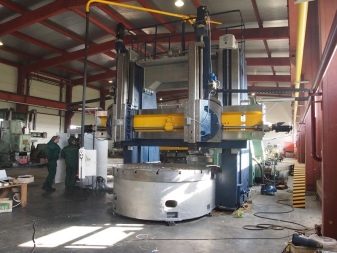
The comment was sent successfully.