What are wood planers and how to choose them?
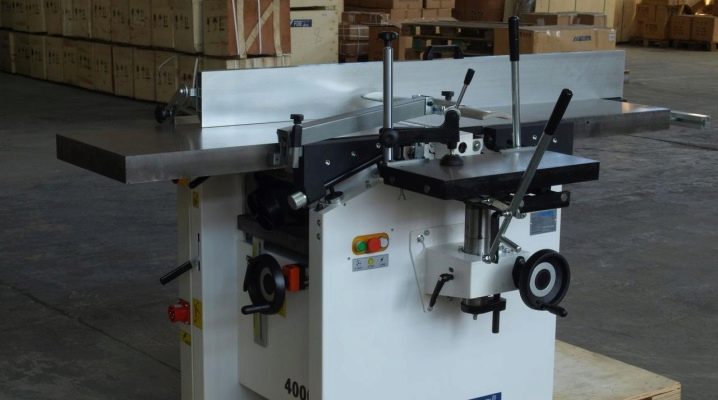
Planing machines are devices with the help of which various processing of wooden materials is carried out, from creating the shape of an object to grinding it. The modern assortment of woodworking machines from various manufacturers allows anyone, be it a professional or a home craftsman, to choose the necessary tool. However, in order to do this, it is necessary to clearly understand what task the master sets for himself, the work of what complexity is ahead. This article will help you navigate the current market for wood planing machines, so that any buyer can choose the model you need.
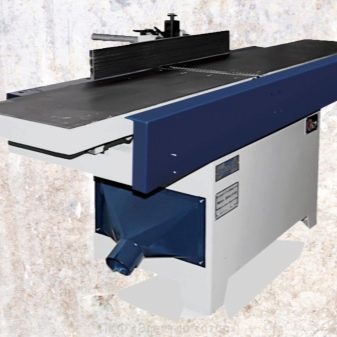
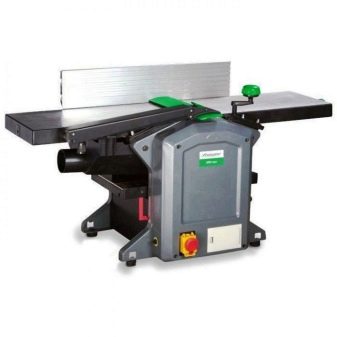
Species overview
Planing machines for wood, depending on the purpose, are divided into several types.
According to the principle of operation, they can be transverse and longitudinal planing.
Cross planing - when working on this device, a piece of wood is placed on the table. The planer head moves, due to which the working movement occurs, and the movement of the table ensures the feeding of the part.
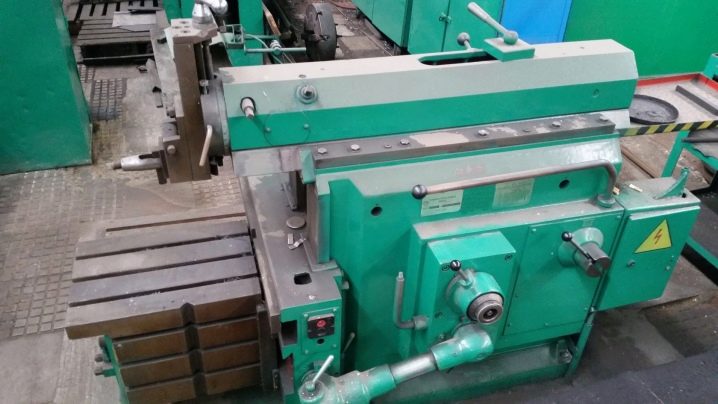
Longitudinal planing - on a machine with this configuration, the working movement occurs due to the movement of the workpiece on the table. And the planer head, in turn, feeds the part.
According to the working conditions, woodworking devices are divided into stationary and desktop.
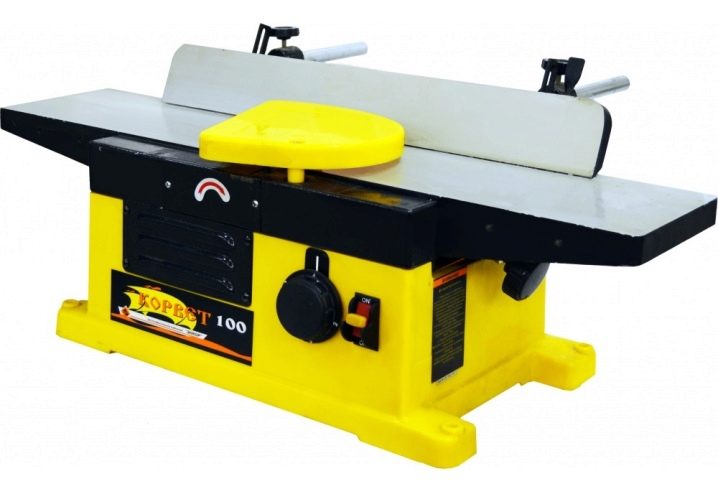
Stationary - used in profile factories for industrial purposes (large in size and weight, require voltage from 380 V to operate, differ in increased cost).
Tabletop - suitable for work at home for household purposes (small in size, light, required voltage - 220 V, low-cost).
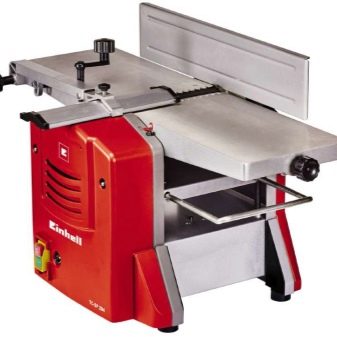
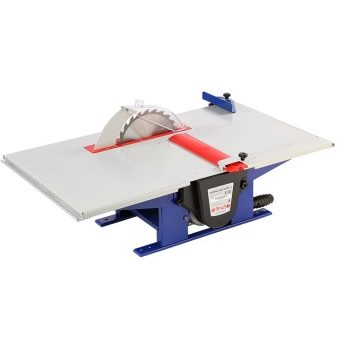
One of the basic stages of wood processing is the planing of workpieces. It consists in removing the upper layer of material, removing significant irregularities, due to which it is possible to form a bar of the required size.
Of course, this operation can be done manually using a plane, but the use of an automated device will make this work more efficient and faster.
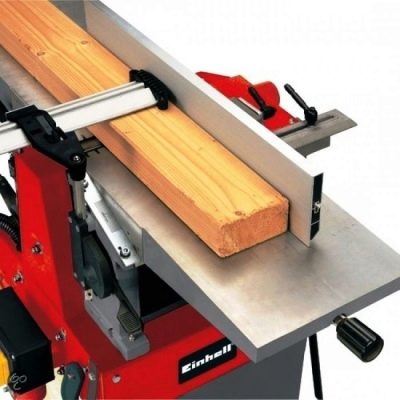
With the help of a planer, you can produce interior details, furniture, as well as restore aged wooden objects - in general, process any flat surface (vertical, horizontal, inclined, at different angles). Four-sided woodworking machines are very popular. With their help you can:
-
fugue;
-
thicknessing;
-
mill;
-
profile.
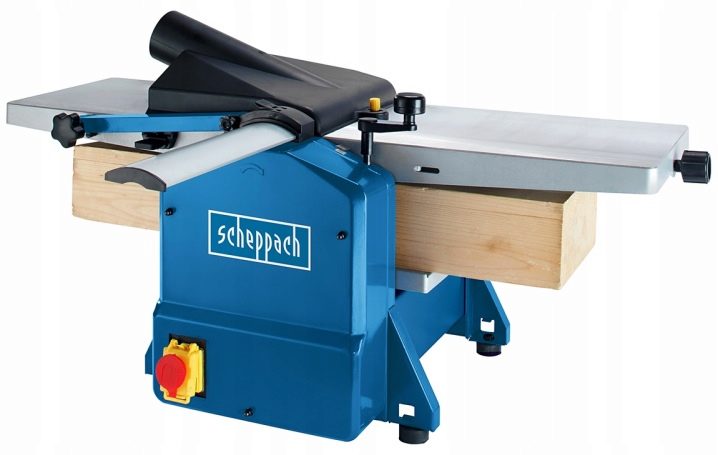
The advantage of the unit with such a configuration is the ability to simultaneously perform several operations. This machine can be used to produce skirting boards, parquet boards, window parts and much more.
In general, woodworking machines are divided into planing, thicknessing, combined, circular and universal.
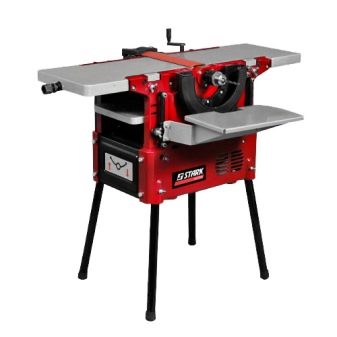
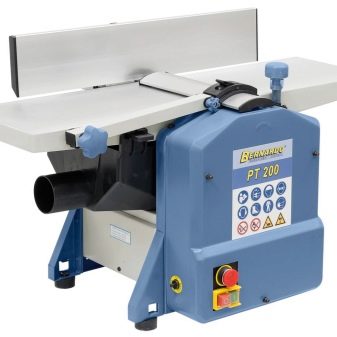
Jointing
Jointing machines are used to pre-process the raw material (boards, bars) of various sizes intended for the manufacture of furniture. This unit allows you to plan the workpiece, removing various protrusions and roughness. The basic elements of the device itself are the bed and two tables made of cast iron (one at the level of the cutting shaft, the other along the thickness of the removed chips). The process of work looks like this: a blank block is manually moved along the table, which is pressed against the knives.
As a rule, for high-quality processing, rolling is required in several passes, due to which all the edges of the workpiece are leveled, and an equal thickness is formed.
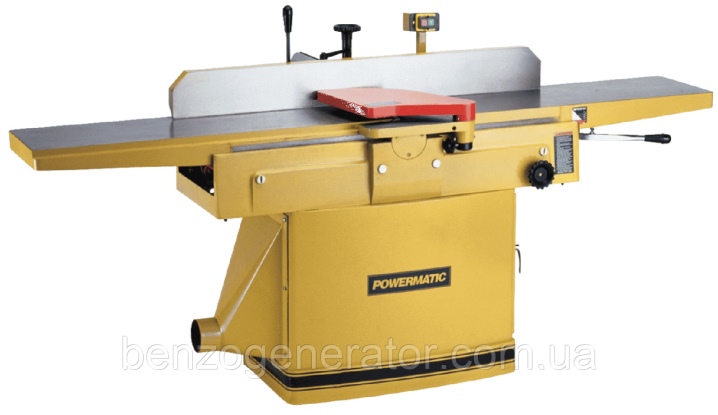
Thicknesser
The second step after planing is finishing - it is done with a thicknessing machine. With its help, it is possible to achieve an absolutely smooth surface of the bar and high accuracy in the formation of its dimensions, which are necessary in the manufacture of furniture or connecting fasteners. The thicknessing machine allows you to remove roughness with a thickness of 1-5 mm. This unit is of two types:
-
one-sided (the bar is processed from one side);
-
double-sided (simultaneous processing on both sides).
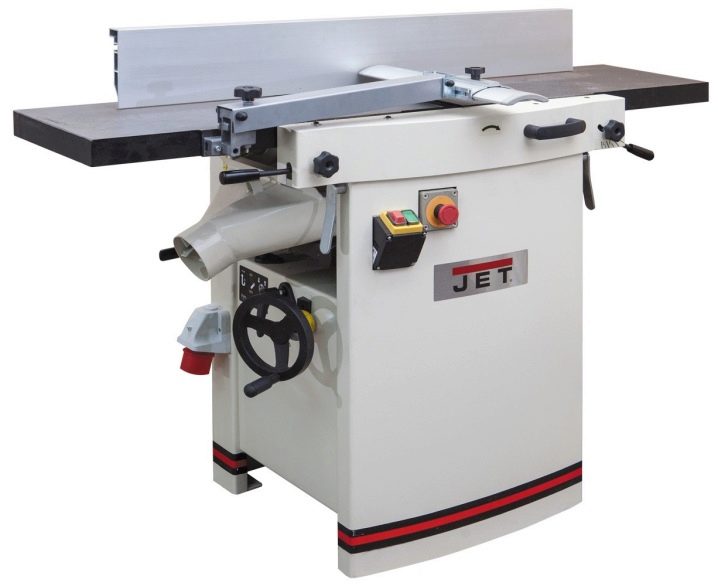
As a rule, on such machines, workpieces are fed automatically.
Combined
Combined units include planer-thicknessing machines having two components - a planer (upper) and a thicknessing (lower). The advantages of such a machine are its compactness and budget price; it is perfect for amateur activities.
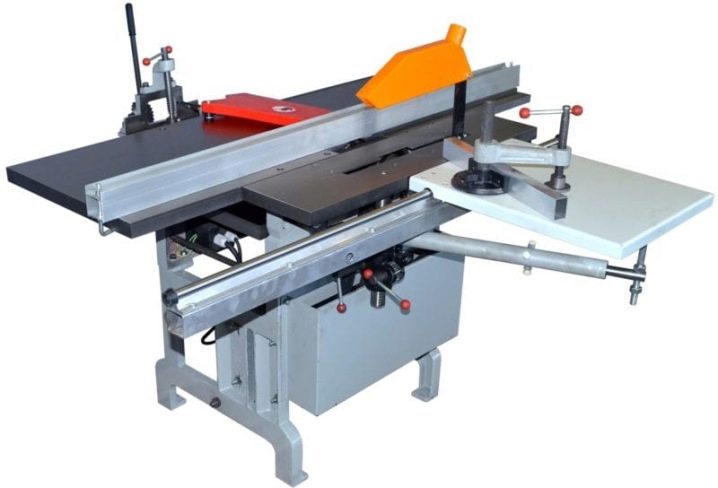
Jointing-circular
This type of machine is used for sawing bars and forming milling blanks.

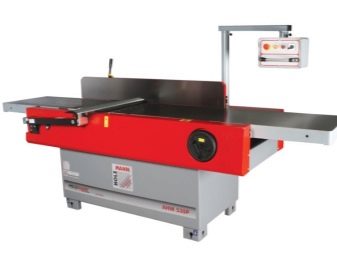
Universal
Universal machines are used to perform the following work:
-
jointing;
-
cutting;
-
calibration and others.
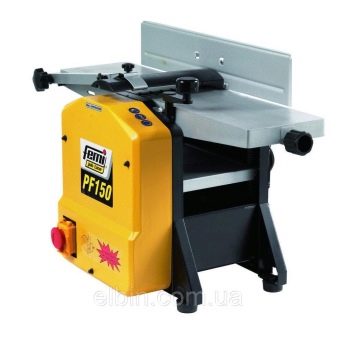
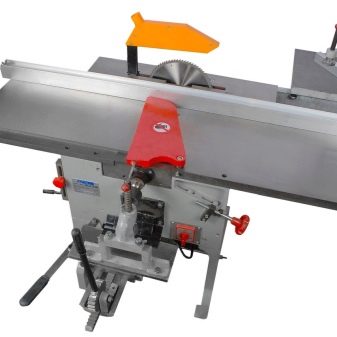
The main disadvantage of such a unit is its high cost, so it is usually used in mass production.
Rigging
Modern machines for wood processing have the following elements:
-
Desktop;
-
metal bed;
-
guiding device;
-
knife shaft;
-
feeder;
-
clamping, clamping, lubricating elements;
-
fences;
-
drive unit;
-
starting parts;
-
Electrical engine.
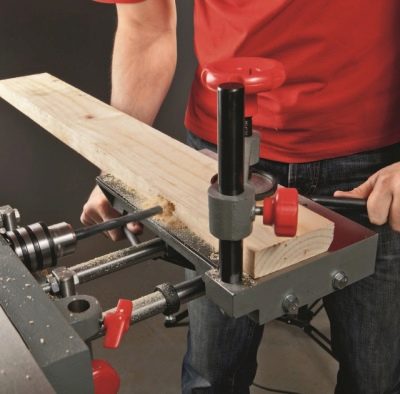
One of the key roles in the operation of the device is played by the knife shaft. Therefore, knives for woodworking units are made of durable steel, which, depending on the type of equipment, have the appropriate dimensions and are sharpened for certain types of wood.
Popular manufacturers
Today the market of woodworking equipment pleases the buyer with its species and price variety. According to a number of sources, the top five include the following manufacturers:
-
MAKITA;
-
BOSCH;
-
"STAVR";
-
PROXXON;
-
JET.
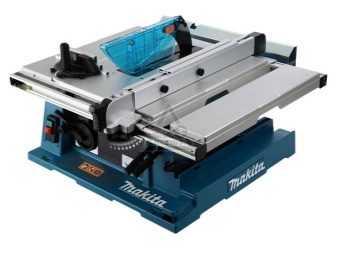
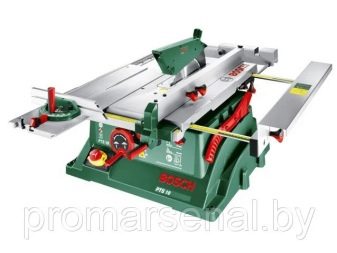
The table shows the main characteristics of woodworking machines from various brands that are in the highest demand.
Model Properties |
MAKITA RT0700CX2 |
DeWALT DCS7485N |
Einhell TC-US 400 375 W |
JET JRT-1 |
View |
Edge router (trimmer) |
A circular saw |
Grinder (stationary) |
Milling table |
Dignity |
1) compact dimensions; 2) the ability to carry; 3) multifunctionality; 4) extended complete set. |
1) compact dimensions; 2) extended complete set; 3) dust removal function; 4) a clear cut line; 5) high-quality assembly. |
1) low noise level; 2) budget price; 3) high-quality assembly; 4) compact dimensions; 5) dust removal function; 6) ergonomic design. |
1) budget price; 2) high-quality assembly; 3) multifunctionality 4) ergonomic design. |
disadvantages |
High probability of early breakdown |
High price |
Refinement with a file is required |
The main parts are made of plastic |
approximate cost |
200 $ |
800 $ |
130 $ |
110 $ |
Criterias of choice
When choosing a woodworking machine for a home workshop, you should be guided by the following parameters:
-
specifications;
-
purpose;
-
price.
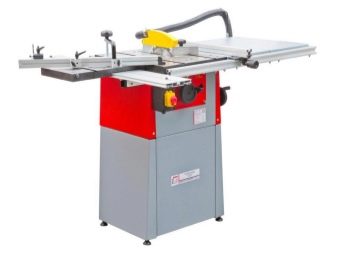
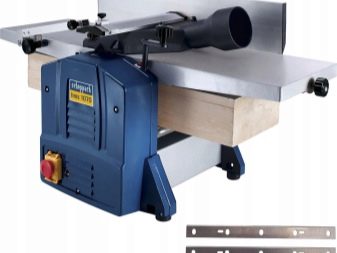
It should be borne in mind that there should be free space around the desktop, so you need to carefully consider the dimensions of the selected device. And also you need to remember: the higher the rotation speed, the more ideal the processing is.
As for the knives, their number should not be large, since they require complex maintenance. The main parameters are also the width and depth of planing - they indicate the dimensions of the bar that can be processed, as well as the width of the layer removed from the part.
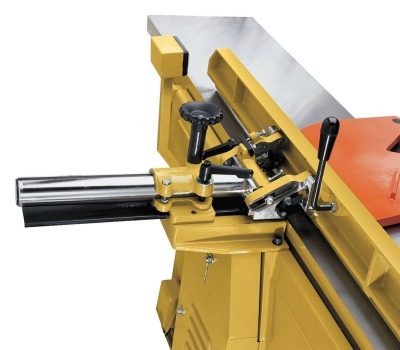
Nuances of operation
Working with a woodworking unit consists of the following points:
-
adjust the height of the back flat tile correctly;
-
installation of a workpiece, which, under the influence of knives, acquires the required dimensions.
When working with long parts, seek the help of a partner.
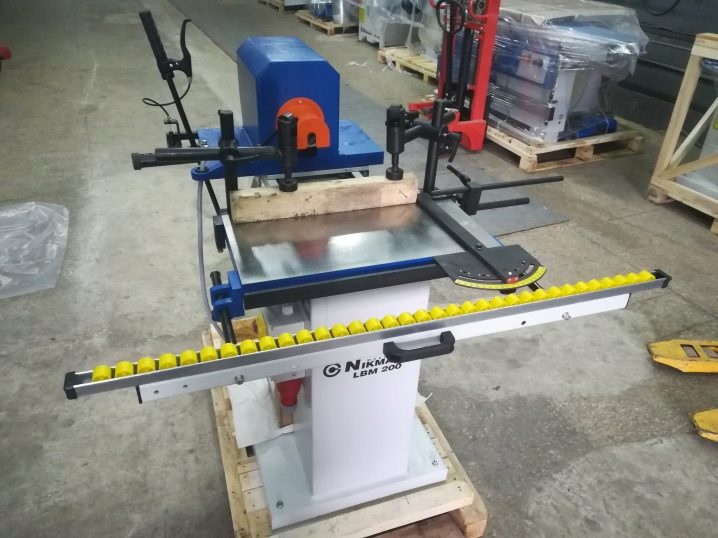
In order for the device to last as long as possible, it is important to adhere to the following rules:
-
regular sharpening of knives;
-
when working with a large volume of material, use a dust extractor;
-
regular cleaning with solvent and silicone spray of the shaft and knives
-
regular wax or paraffin treatment of threaded wheels.
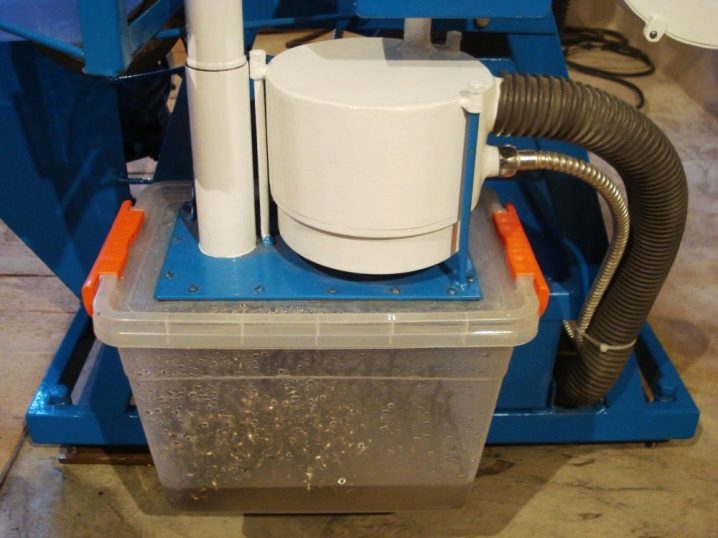
Summing up, a number of advantages of woodworking equipment should be noted over manual processing of materials:
-
high performance;
-
low labor costs on the part of the operator;
-
high quality of the result;
-
increased level of security;
-
great technical capabilities;
-
the possibility of additional equipment.
Thus, a properly selected woodworking machine will facilitate and improve the work of the master with minimal time and labor costs.

The comment was sent successfully.