Overview of laser machines for cutting metal and their selection
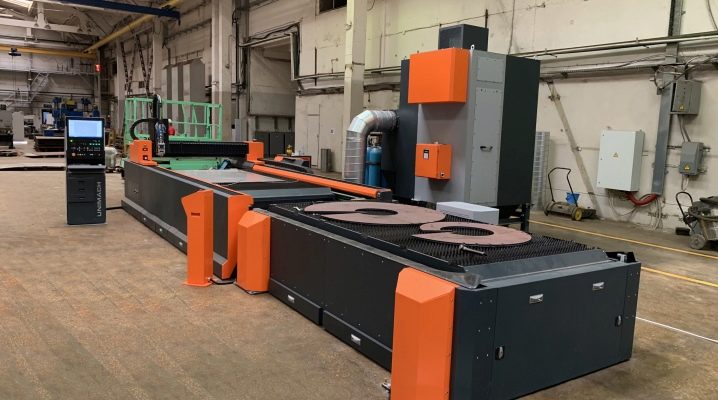
Laser equipment for metal cutting is used in a wide variety of industries: mechanical engineering, metallurgy and furniture manufacturing. This popularity is due to the fact that it allows you to create parts of a complex shape with an increased level of accuracy. Such equipment will be discussed in our article.
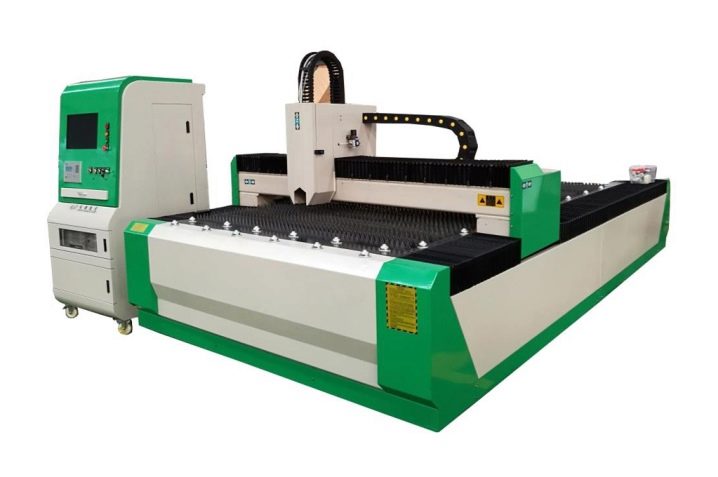
Design and principle of operation
Metal laser cutters have three main functions:
- engraving: drawing a picture, text and even a photograph on a metal surface;
- laser cutting;
- curvilinear cutting.
In all cases, a template is formed according to which the numerical control module sets the cutting parameters. The result is a perfectly accurate product.
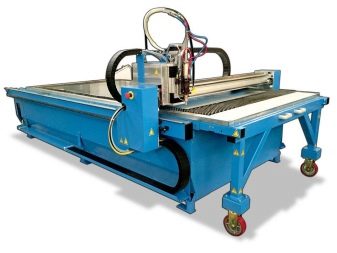
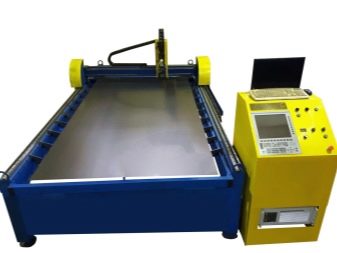
The main advantage of laser machines is their high productivity: a large number of products can be processed in a relatively short period of time.
The design of any laser cutter includes several blocks:
- emitter - responsible for generating a stream of photons or a narrowly focused laser pulse;
- gas movement unit - designed for blowing hot metal out of the working area and cooling the radiator;
- drive - used to move the emitter along the surface to be treated;
- working cutting table - it is on it that the workpiece is placed, while the table can be replaceable;
- CNC / ACS module.
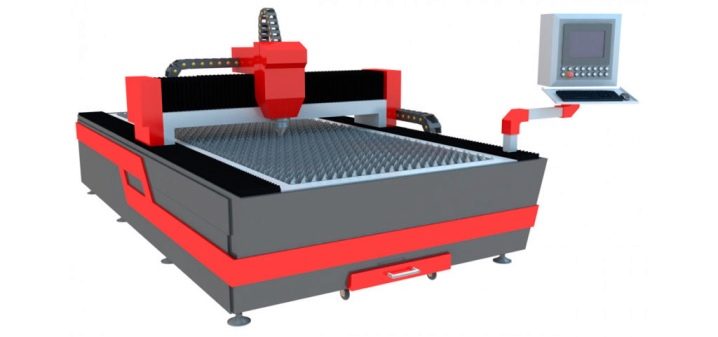
The principle of operation of such machines is based on the generation of a narrow beam by a laser tube that performs metal processing. As a result of the contact of the beam with the surface of the material being processed, a high-temperature effect occurs, and it allows engraving or cutting metal. In this case, the flow of the gas mixture blows out the layer of molten material, which ensures a high quality cut. These machines can be used to work with all types of sheet steel, as well as non-ferrous metals and their alloys.
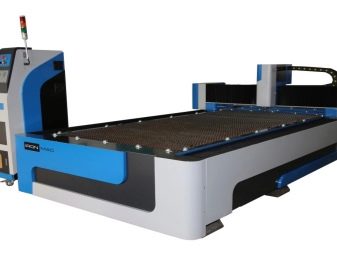
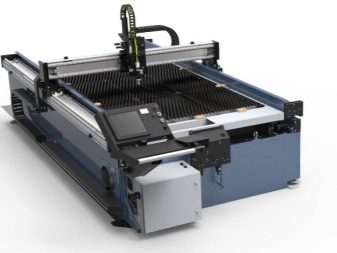
Description of species
The essence of the work of any laser cutter consists in focusing a narrowly directed beam, as a result of which the energy is concentrated on the surface of the processed material. The diameter of such a beam does not exceed tenths of a millimeter, which ensures the minimum cutting thickness. The course of melting and the subsequent transformation of the metal structure occur as a result of bringing the power characteristics of the laser beam to certain parameters. Depending on the mechanism of operation, there are four main types of such machines.
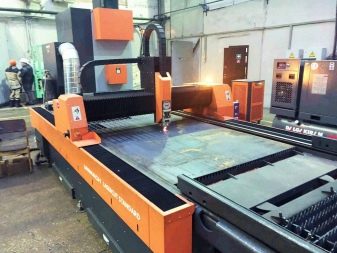
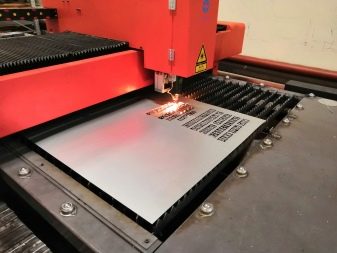
Gas
Laser cutting of metal can be carried out in an oxygen or nitrogen environment, the choice depends on the characteristics of the metal to be processed. So, as a result of oxygen exposure, exothermic reactions are triggered, the thermal energy of which makes it possible to cut fairly thick sheets of low-alloy and carbon steel.
It is not recommended to cut galvanized or galvanized surfaces in oxygen. In this case, the cut is uneven, in addition, the risk of dross formation increases. When cutting stainless or high alloy steel, it is undesirable to allow oxidation of the cut point. That is why, when working with such metals, inert gases, most often nitrogen, are in demand.
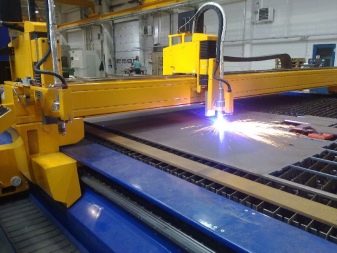
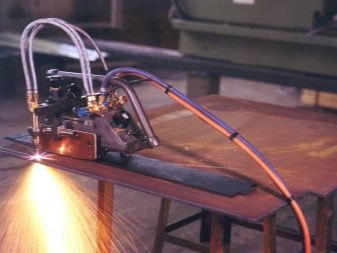
Also, nitrogen is used in cases where the sections will subsequently be stained.If oxygen is used, the oxidation of the metal will lead to a decrease in the quality of the tinting.
Any gas medium can be used for cutting aluminum. But for working with titanium alloys, neither one nor the other can be used, since both gases begin to be absorbed by the metal surface and form a brittle layer. For this material, preference should be given to laser devices operating in helium or highly purified argon.
In general, any gas laser cutters give the maximum radiation wave, so they are in demand when processing sheet metal of maximum thickness.
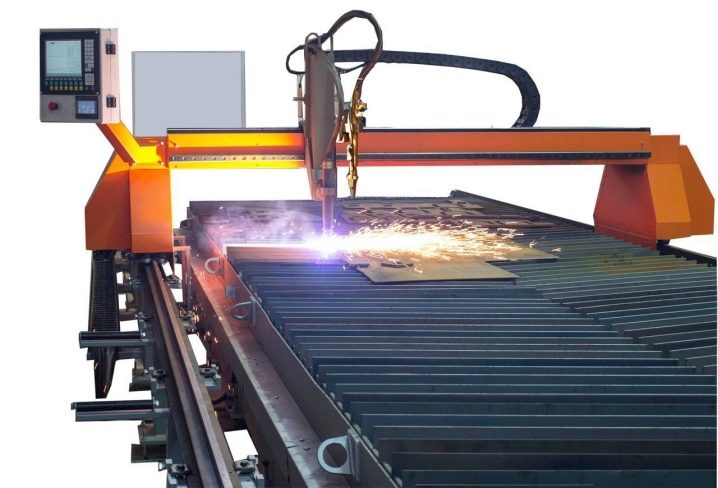
Fiber optic
High efficiency and productivity of the equipment is provided by fiber-optic laser devices, they are often implemented in the form of mini-machines. They have the following advantages.
- High beam quality. The cutting line is thinner and the spot is smaller, which generally improves work efficiency.
- High cutting speed. In comparison with gas, it is twice as much.
- Durability. The use of a professional fiber-optic laser ensures stable performance up to 100 thousand hours of equipment operation.
- Increased efficiency. The efficiency of photoelectric conversion in fiber optic cutting corresponds to 30%, which is 2-3 times more than when laser cutting in a gas environment.
- Low cost of use. The power consumption of fiber optic installations does not exceed 30% of laser cutting in a gas atmosphere.
- Minimum maintenance costs. The absence of the need for reflective lenses saves a lot of money on machine maintenance.
- The operation of such equipment is not particularly difficult. Due to the transmission of the optical fiber, there is no need to adjust the parameters of the optical path.
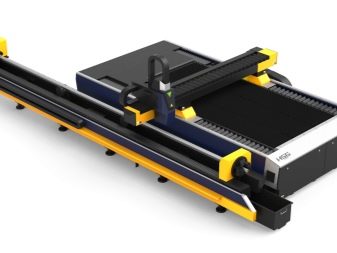
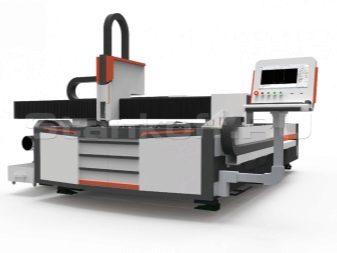
Diode
The main working element of a diode laser cutter is an emitter in the form of a semiconductor crystal formed as an optical resonator. In addition to the diode, such a laser includes a specialized device for powering from an alternating current network. This allows you to vary the parameters of the output radiation.
Also, the design provides for a temperature control sensor and an optical device, which can greatly increase the monochromaticity of the beam.
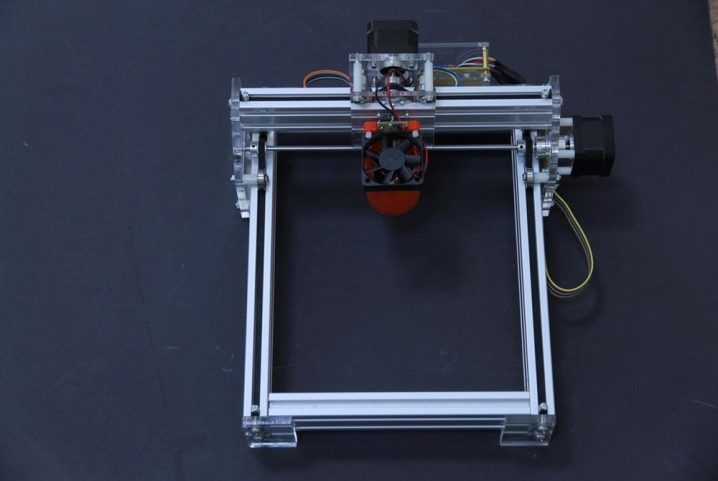
However, a diode-type laser is significantly inferior to gas and fiber-optic ones in terms of coherence parameters. Focusing gives a large divergence, so it is impossible to concentrate energy in the maximum volume. The only advantage of such equipment is its relative cheapness relative to all other models.
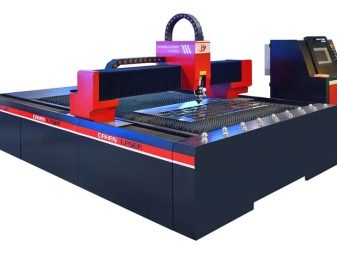
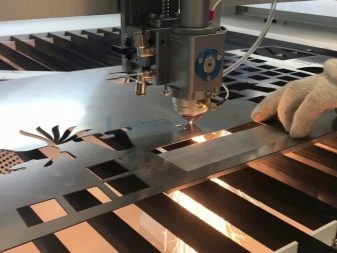
Solid state
The principle of operation of a solid-state laser is similar to a gas one. But it also has its own characteristics. In contrast to the gaseous medium, an active medium of solid forms is used here. As a rule, these are crystals and various glasses that are activated upon contact with rare earth elements. Such lasers are characterized by increased efficiency, while a number of models are quite compact in size. These torches produce beams with wavelengths that can handle a wide variety of metals and thicknesses.
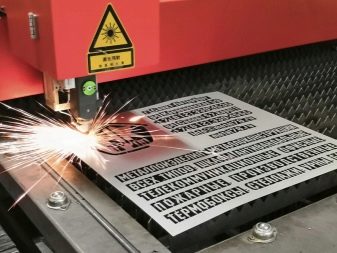
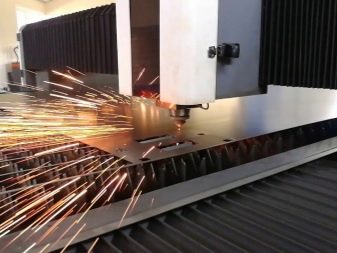
Popular manufacturers
Today on the market there are laser cutters for metal from a variety of manufacturers. Among foreign companies in the domestic market, the products of factories located in European countries, the USA, as well as in Japan and Taiwan are very popular:
- Trumpf (Germany);
- Schuler (Germany);
- Trotec (Austria);
- Farley Laserlab (Australia);
- GCC (Taiwan).
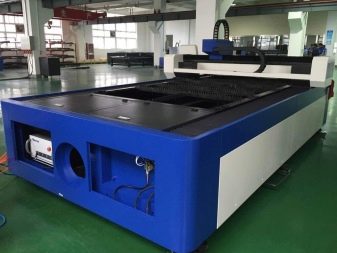

In addition, Chinese-made products occupy a large market share. The opinion about it is ambiguous, many doubt its quality.However, some brands with production facilities in China operate using Swiss technology and under strict control from the customer. They produce laser cutting machines with extremely high technical and operational characteristics. These companies include:
- Rabbit;
- Wattsan;
- Bodor.
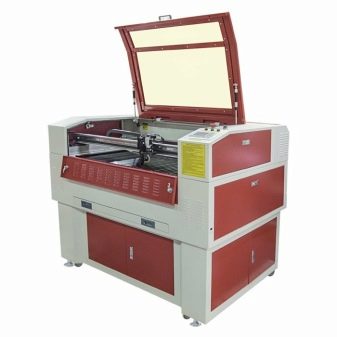
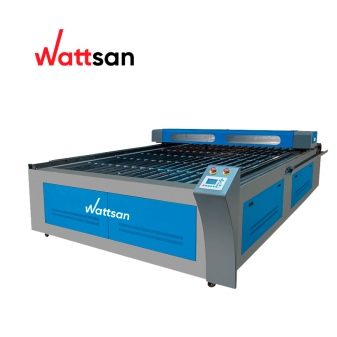
In Russia, laser cutters are produced by the industrial enterprises Semiconductor Devices, LOMO, Plasma and Inversion. Each of them offers certain types of laser systems. There are no enterprises in our country engaged in the production of all types of laser machines at the same time.
As practice shows, the quality of Russian cutters leaves much to be desired and falls short of the machines of foreign companies. However, this is fully offset by their low price.
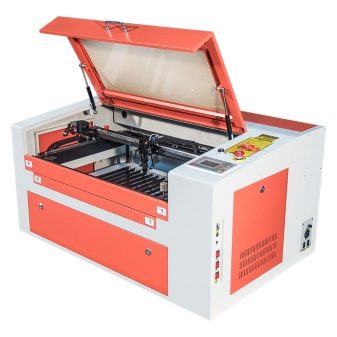
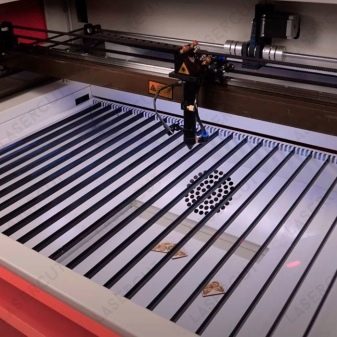
Nuances of choice
When choosing a laser cutter for metal, you should pay attention to the following characteristics.
- Assortment of materials. First of all, it is necessary to take into account the specifics of the enterprise. It is important to clarify what the parts to be cut are made of and what their thickness is. These factors should be compared with the technical data of the machine, the size of the working area and the operating parameters of the equipment.
- Power. The average power of all laser machines today ranges from 500 to 6000 watts. If you plan to cut metal sheets less than 6mm thick, a 500-700W laser cutter will suffice. To work with thicker material, you need to select the machines with the maximum power.
- Rigging. When it comes to fiber optic machines, you need to pay attention to consumables: servomotors, guides, cutting heads, chimeras and others. The quality and functionality of these components affects the precision and speed of laser cutting. Some unscrupulous manufacturers complete equipment not with original components, but with their counterparts in order to reduce costs. This can be confusing for the buyer. Therefore, information on the origin of consumables must be clarified in advance.
- The quality of the equipment. In recent years, there has been a tendency to reduce the production cycle at most enterprises. Many firms, especially those that have recently entered the market, do not pay sufficient attention to testing their laser cutters before delivery to the client and do not perform quality control of the equipment. Therefore, when choosing a machine, it is very important to pay attention to the availability of testing services and pre-sale preparation at the manufacturer.
- Service maintenance. When selecting equipment, it is better to give preference to the machines of those manufacturers whose service services are represented in the region of use. Otherwise, any flaws in the course of operation will lead to long-term repairs and, accordingly, production downtime.
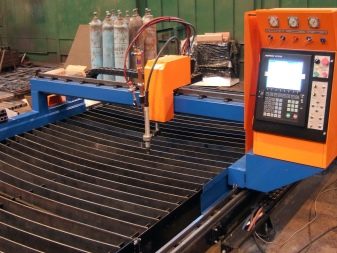
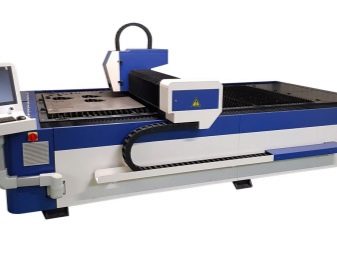
Application
Metal laser cutting machines are versatile. And this applies to both the materials used and the breadth of production possibilities. In particular, they can be used for cutting and engraving metals.
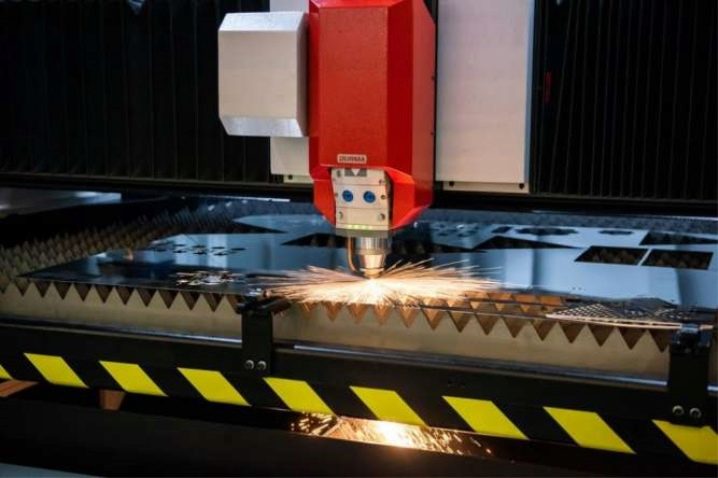
The most common use of laser equipment is material cutting. Machine tools in which the main cutting tool is a laser are widespread in metalworking. They allow you to make:
- individual elements of indoor and outdoor advertising structures;
- metal constructors and puzzles;
- decor items;
- parts for auto and aircraft modeling;
- souvenirs.
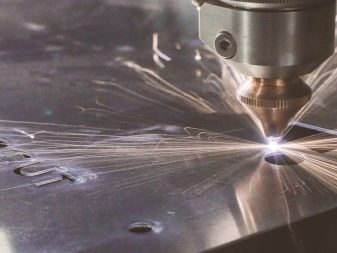

Laser engraving of metal products can turn the simplest thing into a priceless gift. The most clear engraving is obtained using a laser beam. The images applied in this technique have an unlimited shelf life, they are not afraid of abrasion, the effects of acid-alkaline solutions, water, ultraviolet radiation and temperature extremes.
With the help of a computer-controlled laser, you can get an image with maximum detail. Often, intricate patterns are created on metal surfaces and even reproduce photographs.
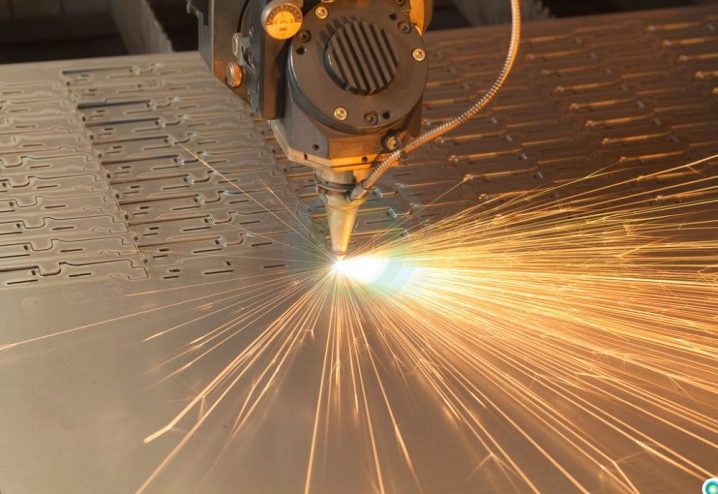
Most often, a laser cutter is used for engraving lighters, cigarette cases, jewelry, cold and small arms, as well as decorative items.
With the laser beam, not only flat but also convex surfaces can be engraved. In this case, a specialized workpiece fixation mechanism is connected to the machine engine. The rotation of the motor is transferred to the workpiece, it begins to move at a given speed and the laser beam applies an image from all sides.
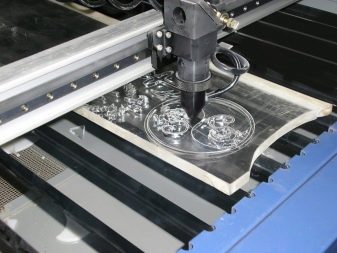
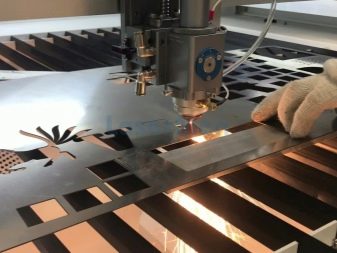
The comment was sent successfully.