Features of woodworking machines and their choice
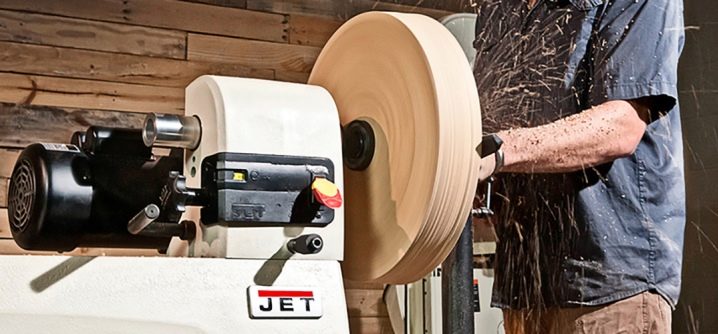
The woodworking machine is used for the machining of wood and sawn timber based on it. It is used for sawing, planing, drilling, using cutters or high pressure.
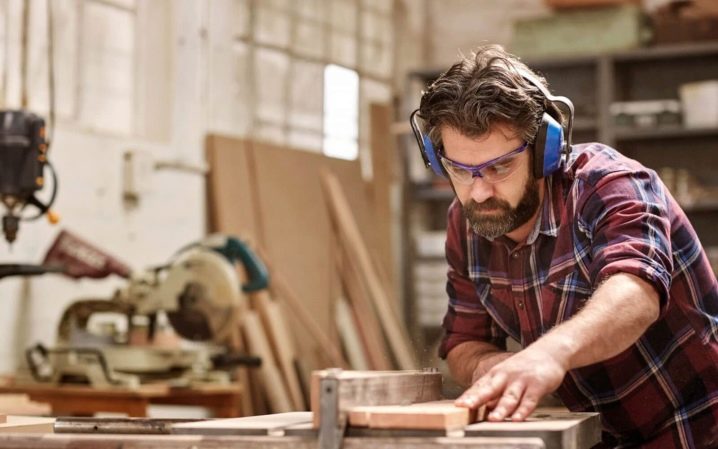
Views
The woodworking machine allows you to get lumber and parts for furniture and other structures from wood that are often used in everyday life and at work. An example of a blank - pieces of timber, board, plywood. It becomes possible to get even veneer and shavings. As finished products - parquet sections, skis, pencils and much more.
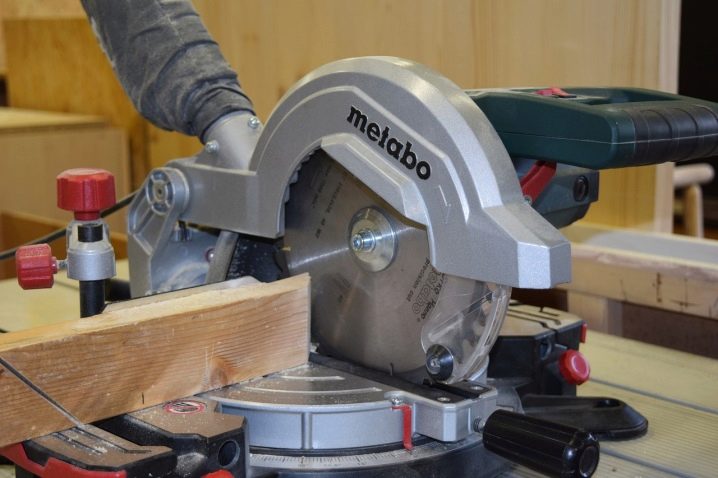
Woodworking machines for wood, producing the processing of parts and workpieces for them by exposure to high pressure, belong to pressing machines. As auxiliary machines and mechanisms, installations are used that carry out preliminary sorting of wood elements by size and shape, packaging and delivery, refer to machines, not producing wood processing and processing.
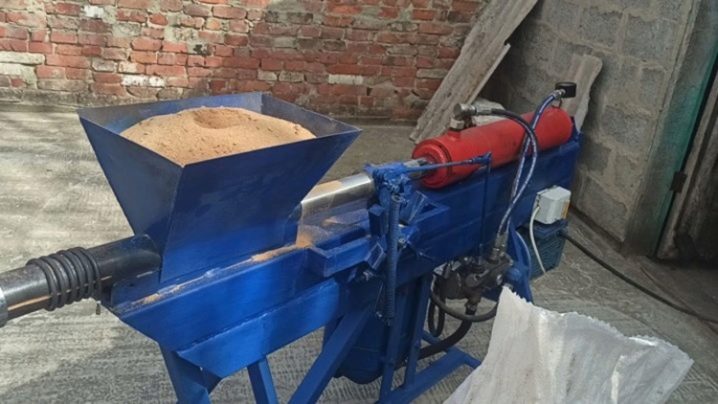
Universal
Universal machines include devices that perform, in addition to cutting, for example, punching pins and grooves. This machine is precisely wood-cutting, spikes and grooves can be carried out using relief cutting. Stamping is easier not so much solid wood as materials based on it - a composite, for example, MDF. The wood dividing machine can also be equipped with a laser controlled by a CNC module.
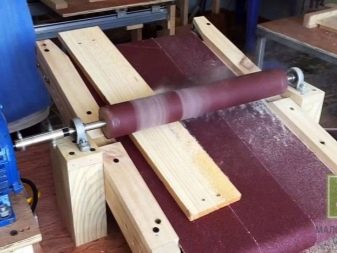
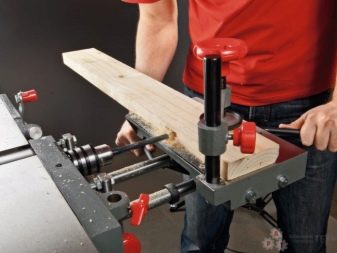
These machines can perform both cutting and sanding of wood to the desired level of roughness or smoothness. They are able to give both the shape and dimensions of the part, perform turning and milling of the future product from a previously formed workpiece. In addition to drilling, sawing and milling, these machines are able to process wood by peeling, chiselling, turning and sanding.
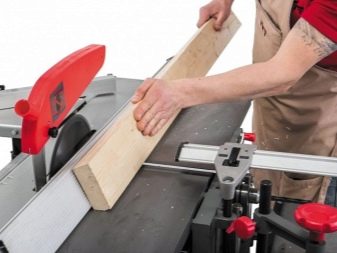
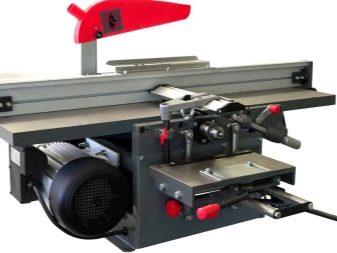
Cutting without the formation of shavings is carried out using special shears, a wood splitter, a stamping machine, a chopping or crushing machine. The structure of the universal machine includes improved shock and vibration tools, each of which operates on a separate spindle drive. More often, two or three instruments are combined in one.
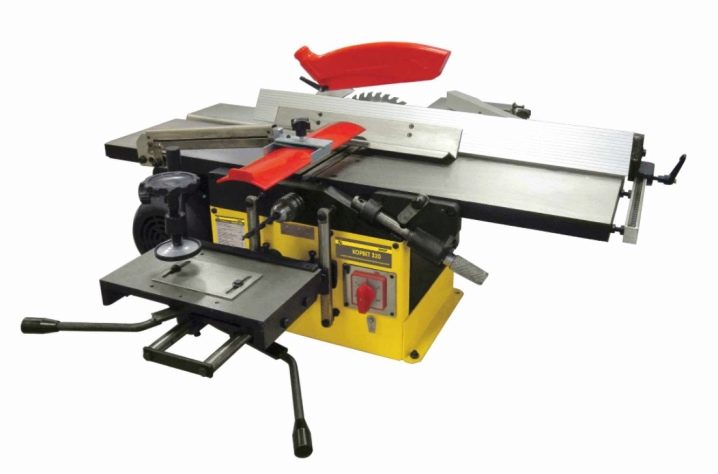
Sawing
The sawing machine produces chip-forming wood cutting. A byproduct of sawing is a variety of shavings that are formed when a saw blade or circular saw passes through an uncalibrated log of freshly felled trees devoid of bark and branches. The largest machine of this kind is the sawmill working with logs.
Sawmills work both vertically and horizontally. The first method is suitable for cutting a log into sections - the saw runs vertically in relation to the laid tree trunk from which the bark and branches were removed, while division into sections is facilitated by stack sawing of workpieces lying on top of each other. The second method is used to cut logs into slabs and boards, then unedged boards are cut along the longitudinal edges and become edged.
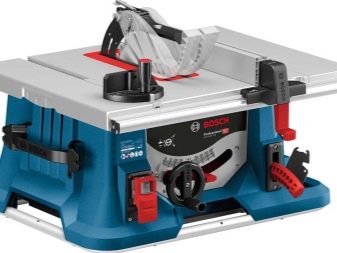
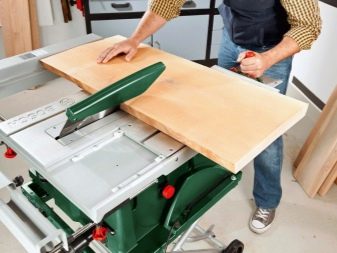
Milling
Having received the blanks, the craftsmen send them to the production of specific products. Most of the needs in woodworking are solved by the router. Woodworking milling machines produce relief and surface processing of products with high precision, which is possible due to the high speed of the machine - about 15.30 thousand revolutions per minute. The more power and the higher the speed, the more highly professional, smoother processing you can get.
In 99% of cases, for the manufacture of specific products, machines with a numerical control module (CNC) are serially used. Milling machines are equipped with cutters-cutters of a special shape, capable of producing a perfectly even notch, undercut, sharpening or smoothing of specific edges. An example of such a blank is an insert panel for classic wooden doors, carved frame parts for purely wooden or wood-composite windows.
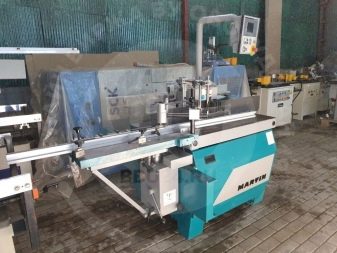
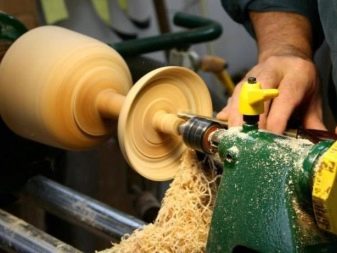
Jointing
A jointer is a long plane. Compared to a short plane, it is more convenient in manual use, with its help you can easily trim an uneven floor from boards that have a factory defect (low-grade edged wood). Manual planers have been supplanted by a jointer. In fact, manual planing machine - an electric drive with a special cutter, which at a speed of at least 3000 rpm cuts off the unevenness of the wood layer by layer, which have gross defects on the surface.
A roughly sawn board made with a low-speed sawmill or circular saw is leveled over the entire surface using a planer.
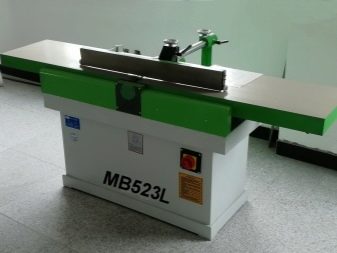
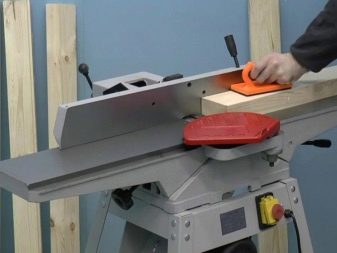
Automatic planing machines are equipped with a carriage-through mechanism, which, by placing boards, beams or slats between two side guides, grinds the layers to the required depth so that the flywheel knife does not touch these setting strips with its tip (they are made, as a rule, of steel ). The planing machine is also replaced by a milling machine, while unevenness when grinding wood layers is not important. No matter how skewed the piece of wood turns out to be, the universal planer-milling machine will turn it into a flat board, stick or bar.
Universal and purely planing machines are controlled using the same CNC unit: the worker sets the depth of the groove (the edge along which the electric planer or motorized cutter will pass) in each specific case, while the original workpiece is securely fixed along the guides. With the help of an electrofugan, after processing one of the surfaces, turning the processed piece of wood on the other side, a perfectly flat workpiece is obtained for performing other tasks.
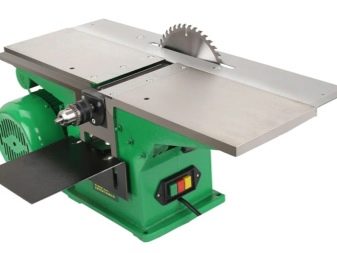
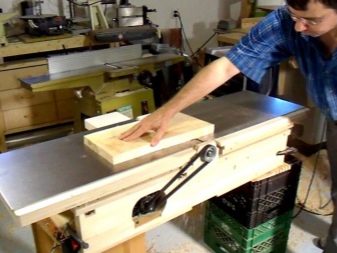
Thicknesser
A thickness gauge is a device that sets an ideally strict projection for planing a board. The thicknessing machine contains this mechanism... The thickness gauge itself is not complete without roller-wheel elements with a bearing stroke. The thicknessing device contains a shaft with cutting elements that remove the top layer of wood during operation. This flattens the top surface of the workpiece so that it becomes strictly parallel to the bottom. The latest models of thicknessing machines are equipped with a uniform feed, which makes it possible to remove a layer of wood of the same thickness along the entire length of the surface.
The thicknessing machine differs from some other devices in that the board, timber or rail is moved with the help of shafts, and the knife mechanism is fixed on a stationary axis.
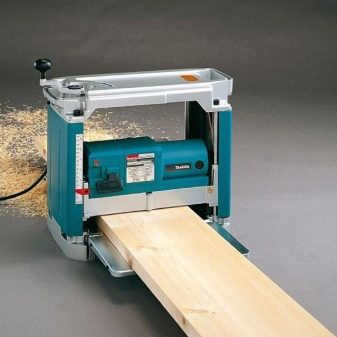
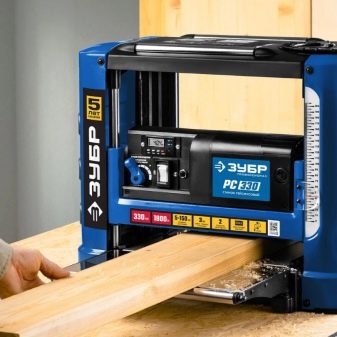
Planer-thicknessing
The planer and thickness planer are combined into one, more versatile unit. Planing (planing), carried out in a given size, is carried out due to the guiding effect of the thicknesser. Applications - for example, furniture blanks where perfect smoothness and thickness are required. In a similar way, for example, grooved euro-board for flooring of the highest grade is produced, where the absence of knots and the homogeneity of the wood motivate the finishing masters to handle such building material with extreme caution. Thicknessing with simultaneous jointing is an expensive operation, but perfectly sawn, planed and additionally processed (edges, spikes and grooves) boards and beams are considered an attribute of luxury interior.
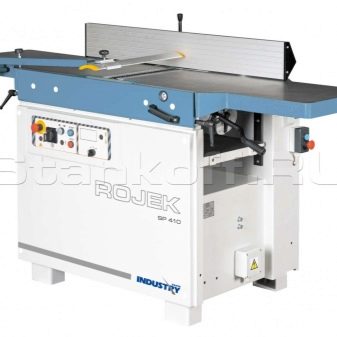
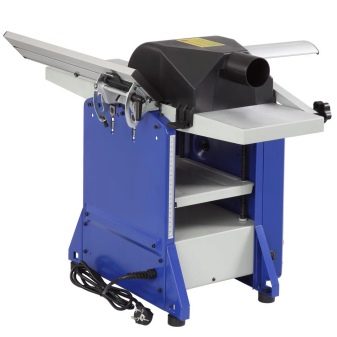
Top manufacturers
Among the Russian machines, the most popular is the Muravei brand of Yaroslavl production.... The power consumed from the network is from 2.7 kW, the unit is universal, with the functionality of planing and thicknessing, sawing and drilling, milling turning. Planing width - 25 cm, cutting depth - 8.5. Planing is carried out in layers up to 3 mm thick. The device operates from 220 or 380 volts, engine speed - up to 4200 per minute. In addition to prefabricated components, the kit includes a clamping clamp for fixing the guides.
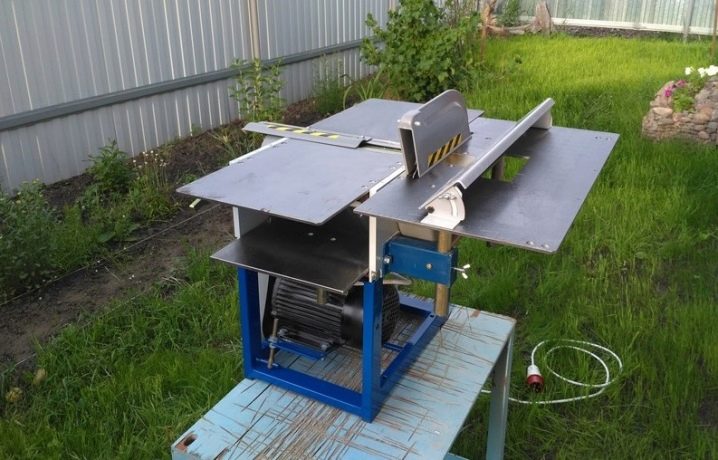
Among the foreign models, one of the best is the machine JET JWL-1015... The length of the processed components reaches 0.9 m, which was made possible by the elongated frame made of cast iron. The transmission is carried out on the basis of belts, the belt is installed and removed quickly enough.

Swedish equipment from the company Logosol for more than 50 years it has been in high demand. The price and quality of these devices are in an optimal combination. The company produces universal machines with the functions of large-circulation copying of single-type parts. The demand for these models is formed by factories, factories and well-known craftsmen on the local market, whose products are in high demand.
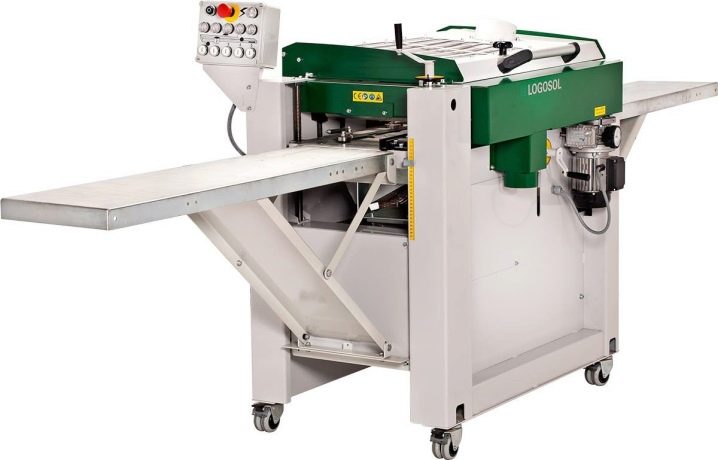
Belarusian (Mogilev) product on the machine tool market - manufacturer's machines. The quality is noticeably above average, the machines of this plant compete with their Swedish counterparts. Specialization - desktop production, as well as household machines for performing operations of a decent range of complexity.
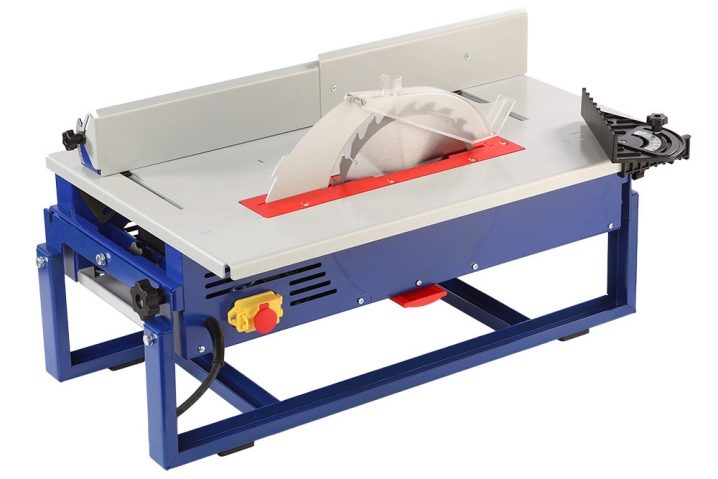
Metabo TS 254 - German quality and ease of customization, high quality and durable assembly. The power consumption of the motor from the mains is 2 kW, it is possible to install large-diameter discs up to 254 mm. Cutting width - 63 cm, depth - 8.7 cm. The saw blade rotates to an angle of 47 degrees relative to the original cutting plane. The machine has the functionality of smooth start and emergency stop of the drive. The device is easy to carry and transported to a new workplace if necessary.
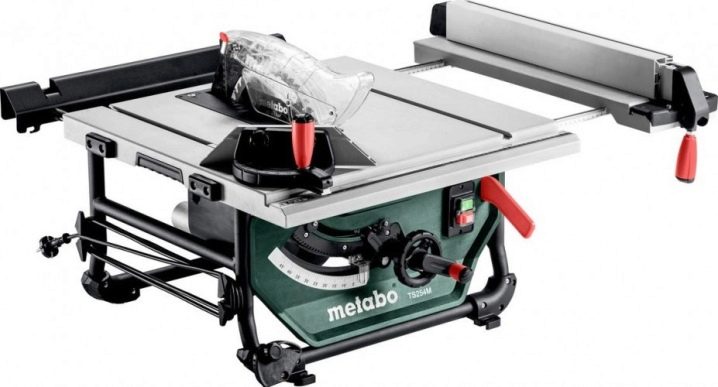
DeWALT DW745 has a relatively small - no more than 22 kg - in weight. Made in the USA, rated for 1850 watts. The saw blade rotates 45 degrees. The diameter of the saw blade is limited by a mark of 25 cm. The cutting depth is 7.7 cm. The set includes a well-oiled table and a parallel stop. The unit has a frame welded from steel pipes.
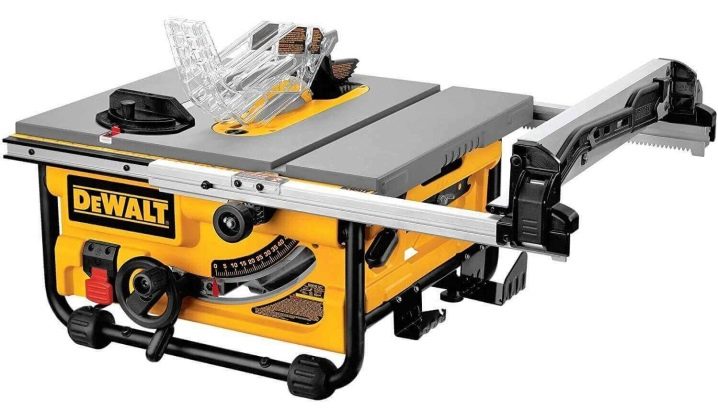
Makita 2704 cuts 9.1 cm deep, the engine accelerates to 4800 rpm. Uses 25.5 cm circular saw blades. The unit is configured by the user himself.
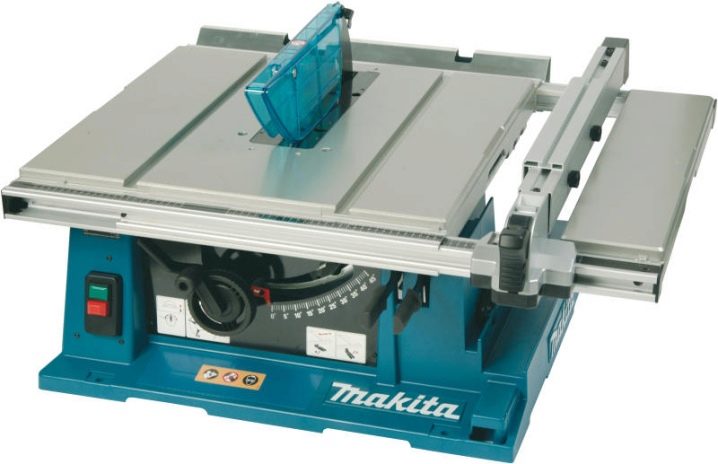
BOSCH PTS-10 saws 7.5 cm deep, there is a 1.4-kilowatt motor, weight - 26 kg. Connects to a construction vacuum cleaner to remove shavings and sawdust.
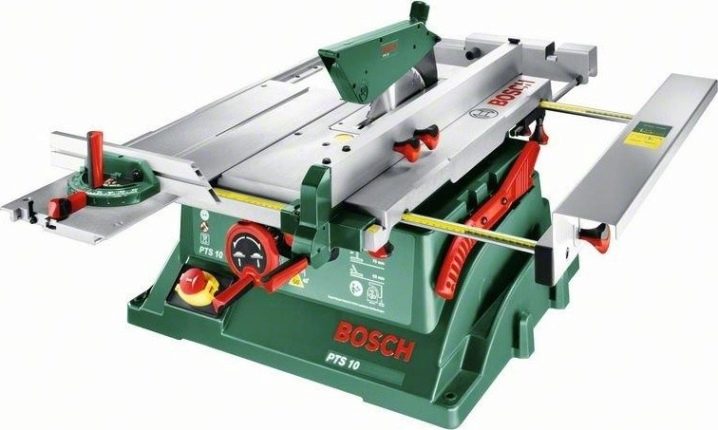
How to choose a machine for your home?
Woodworking mini-machines for joinery and locksmiths for a home or garage workshop do not have a capacity of more than a few kilowatts. In everyday life, consumption is limited to 3.3 kW - standard circuit breakers and an electric meter would not withstand a greater load. Large power, exceeding several kilowatts, is useless at home - it is used in production, where a more powerful three-phase line designed for 10 kW or more is connected to the workshop. For example, sizing machines, grooving machines and end machines do not require an upper power limit.
A weight of more than 30 kg is an obstacle to quickly transferring the machine to another room during a major overhaul. One person will not be able to carry a device weighing more than 20 kg - here you cannot do without helpers.
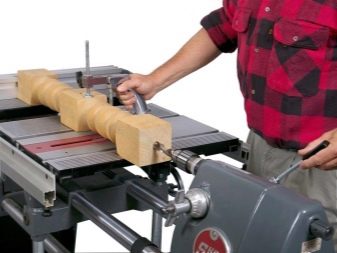
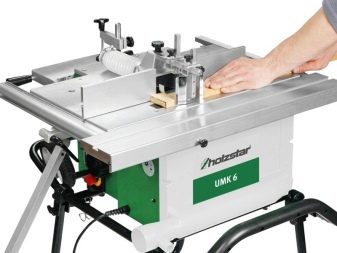
Functionality can play a decisive role in the choice. For example, when a master is engaged in the production of furniture and art products, then one cannot do without milling, thicknessing, planing.In this case, a universal product will be the best solution. The equipment of universal machines, like that of milling machines, is quite diverse.
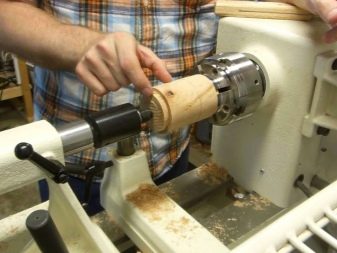
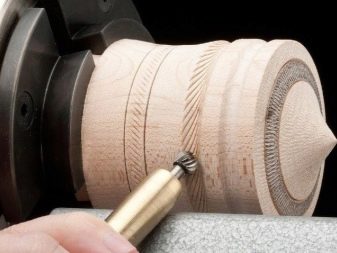
Engine speed determines how high-quality the primary cut of workpieces and parts is. A machine with 3000 engine revolutions per minute (50 - per second) is the minimum requirement. Less resourcefulness will not allow you to plan and grind parts perfectly and smoothly. The best choice is a machine with a speed of 10 thousand revolutions per minute or more. Tapping does not require too high revolutions.
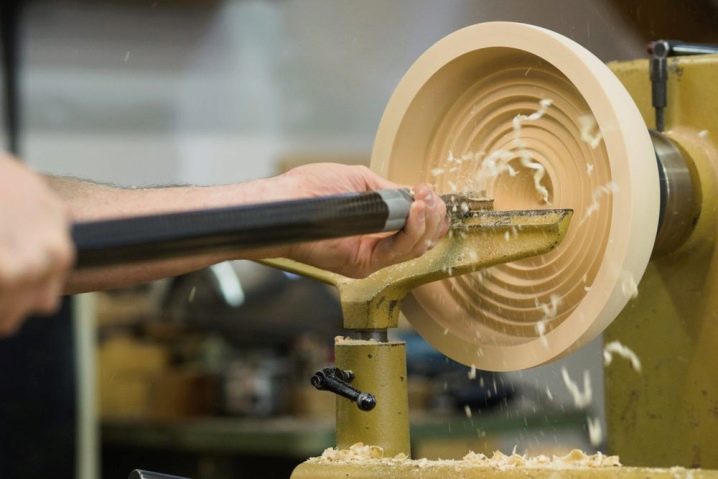
In 99.9% of cases, there is no access to a three-phase 380 V network. This allows you to focus the choice on machines operating precisely from a single-phase 220 V. The power of the machine can be significantly reduced - three-phase electricity transmission is considered economically more profitable, as is its use at the place of work.
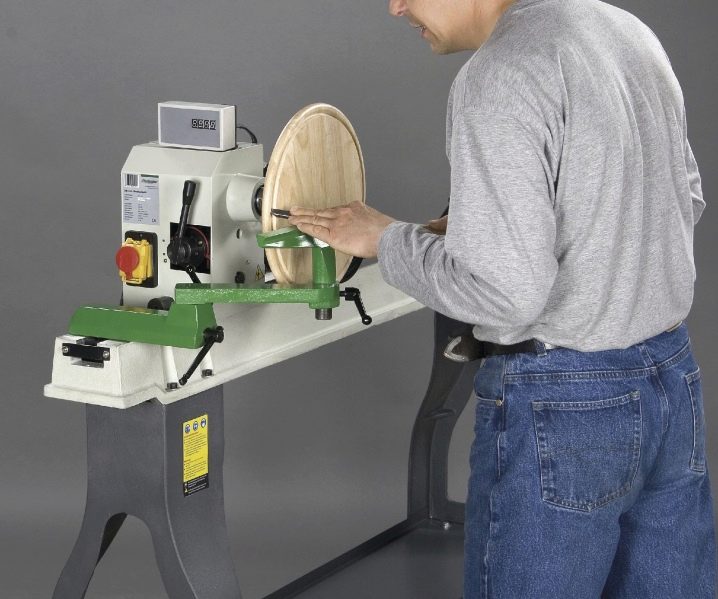
Safe use makes you pay attention to protective components and emergency shutdown, for example, when a saw blade or planer cutter, cutter, drill or other tools that are processing parts get stuck.
Safety for the master is above any functionality: they often choose a less functional, but safer machine for woodworking.
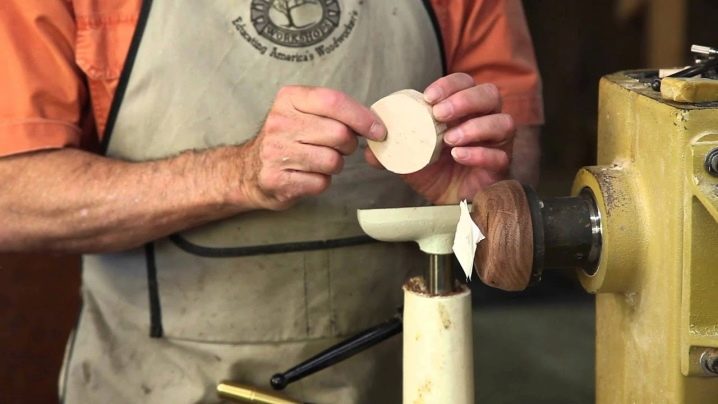
Safety at work
The protective equipment of any modern machine, before which serious tasks are set, allows in general to work safely. For example, a visor-visor and a vacuum cleaner connected to the working chamber prevent by at least 80% the scattering of wood dust, shavings and sawdust around the room where work is being done.
However, a certain amount of wood particles still ends up in the air, in connection with which it is necessary to work with goggles and a respirator.
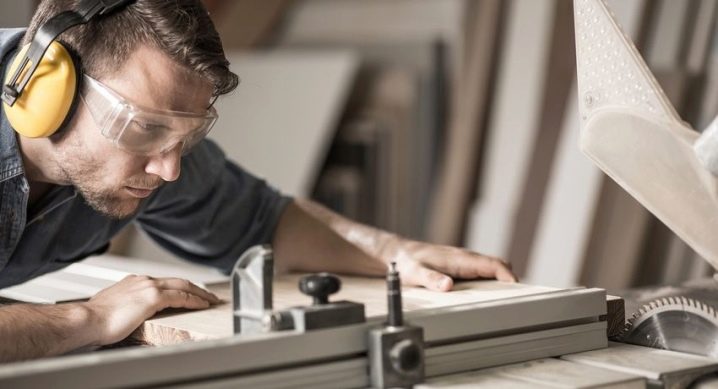
The use of overalls, for example, a general protective overalls, enables the craftsman to protect the skin from the ingress and adhesion of the same wood dust.... This is especially true in cases when there is no well-equipped shower room in the work area. If the protective visor of the visor type is shortened on the machine, that is, it does not fully allow the high-speed particles flying off to linger inside before they are sucked in by a construction vacuum cleaner connected to such a machine, the presence of overalls, a respirator and glasses is not just desirable, but necessary.
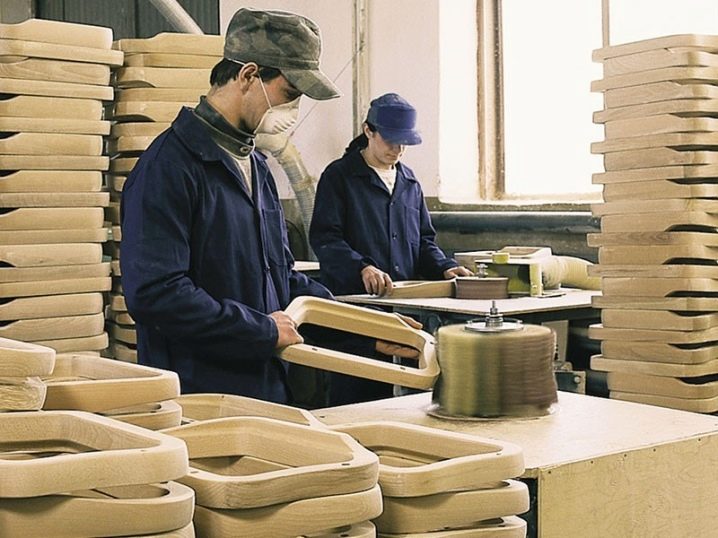
Work clothes are made of thick and rough natural (or not fully synthetic) fabric. In the simplest case, it can be a tarpaulin, which is not easy to ignite with an abundance of red-hot sparks.
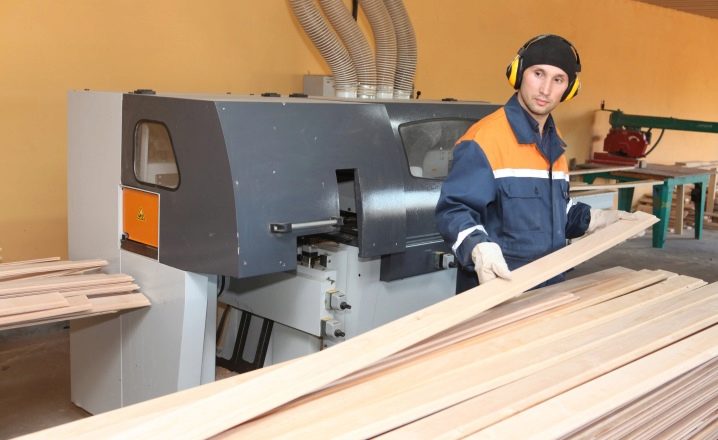
The room where woodworking is carried out should be ventilated with an exhaust hood, and there should be intake ventilation from the side of windows or doors. The easiest way is to open the windows in micro-ventilation mode to provide fresh air. This is also due to the fact that overheated wood evaporates tree resin - and is even capable of emitting not steam, but smoke.
This is especially true for machines supplemented with a laser-plasma cutter: wood that is scorched along the cut line smokes when it is cut with a laser.
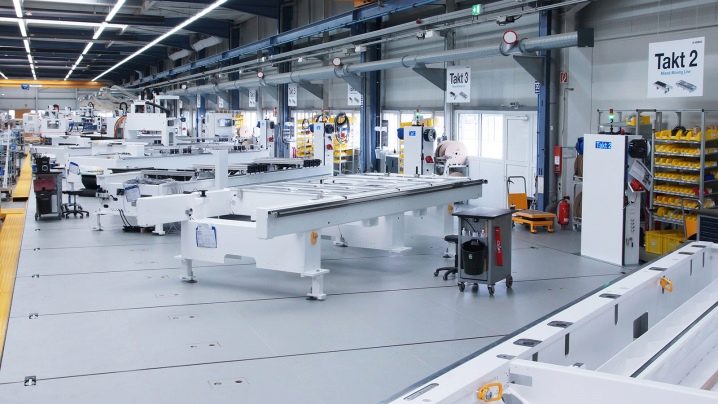
The comment was sent successfully.