Everything you need to know about broaching machines
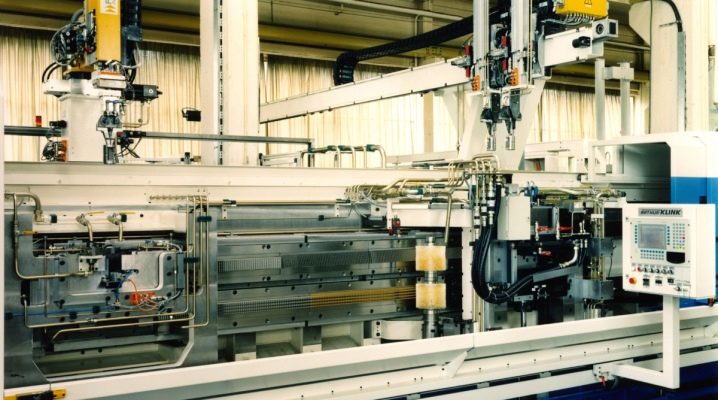
After reading the article, the consumer will find out everything there is to know about broaching machines and how they work. It will be possible to clearly understand the features of horizontal and vertical, the specificity of machines with a broach for the grinder. Also, attention is paid to processing on machines and the selection of specific devices for them.
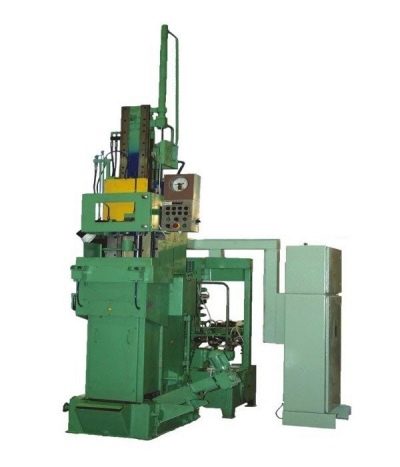
Peculiarities
A large number of metalworking equipment for all kinds of purposes has been created. But even against this general background, broaching machines stand out more than convincingly. They are designed for a particularly clean finish, both inside and out. This technique can work with parts of various geometric configurations. It is worth considering that broaching inside and outside is still performed on different equipment, with its own special features.
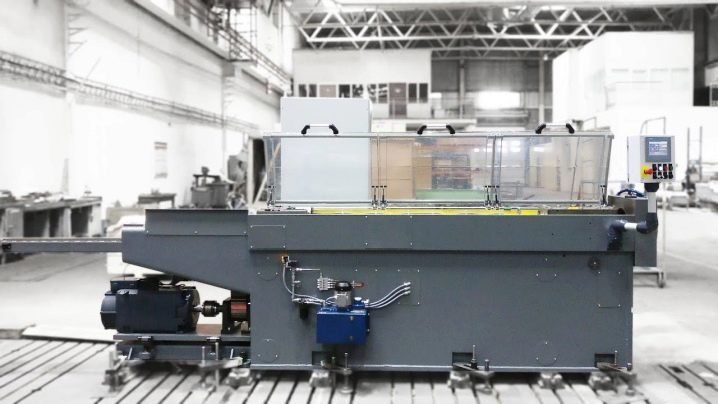
The main functional movement is the movement of the pulling tool. There is no special feed and mechanism for it. The broach teeth are responsible for this function. Most often broaching machines operate semi-automatically, they are equipped for the most part with a hydraulic drive. But the most productive models are designed to use an electromechanical power plant.
When using a hydraulic drive, it is usually equipped with a pair of pumps. They supply oil to the main and auxiliary hydraulic cylinders. The principle of operation involves the support of the broach with a roller and its movement towards the working chuck.
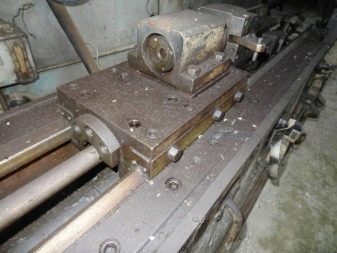
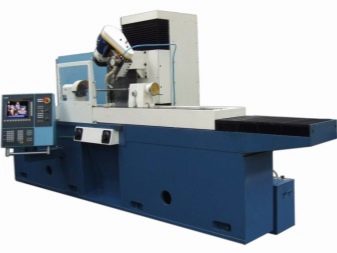
The cartridge grabs the tail of the broach and moves it in the desired direction. The auxiliary chuck is also important: it already clings to the rear shank and returns the broach to its initial position.
Speaking about the device of the main nodes, it must be indicated that structurally, the shanks must correspond to the type of broach and the design of the chuck... It is customary to divide shanks into cylindrical and flat types. Universal chucks for broaches are equipped with a lever-cam clamp; together with them, broaches with a section of 1.6 - 3.2 cm can be used. Some broaching machines can be automatic or semi-automatic.
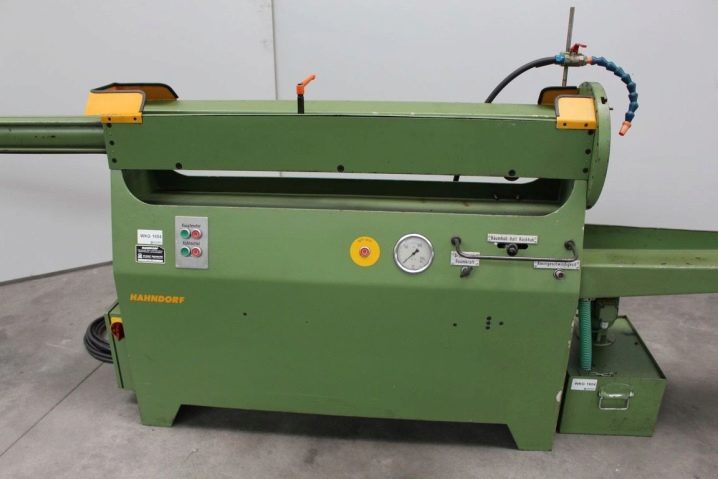
Broaching provides increased productivity. This processing method is quite accurate. After its completion, a clean surface remains. Instead of sequential surface treatments in several passes, a single broach can be dispensed with. It is worth considering the weaknesses of this processing method:
-
deformation during cutting;
-
difficulties with broaching dimensional workpieces;
-
high cost of the tool;
-
difficulties with accurate positioning.
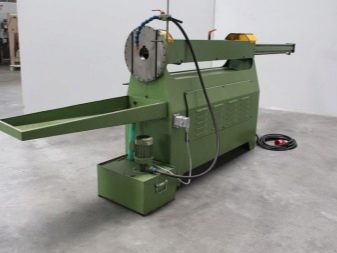
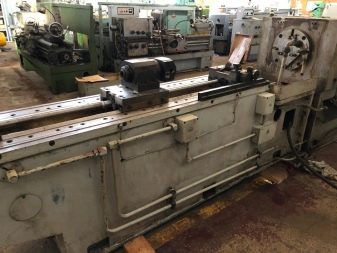
Views
Horizontal
It is the horizontal broaching systems that are considered a universal solution. They are applicable in a wide variety of industries. On such machines, external surfaces are easily processed (stretched). The beds are equipped with a hydraulic cylinder, which, thanks to a special rod, moves the slider. A pressure gauge helps to monitor the pressure in the cylinder.
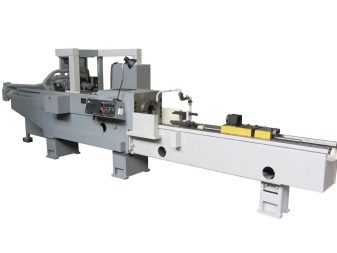
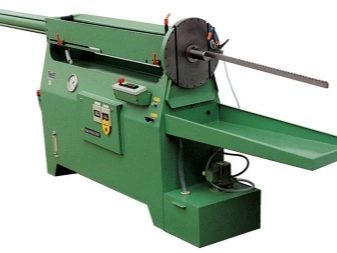
A certain subgroup can be considered a horizontal broaching technique with a revolving design. In this scheme, it is assumed that the broaches from the turntable will be pushed into the part one by one. With such a movement, they automatically join the slider, dock with it.
When the slider moves back, the broach moves back to the original cell.When she enters the same place, the table also moves to its original position; then the drum turns to a new position, and the next broach takes over.
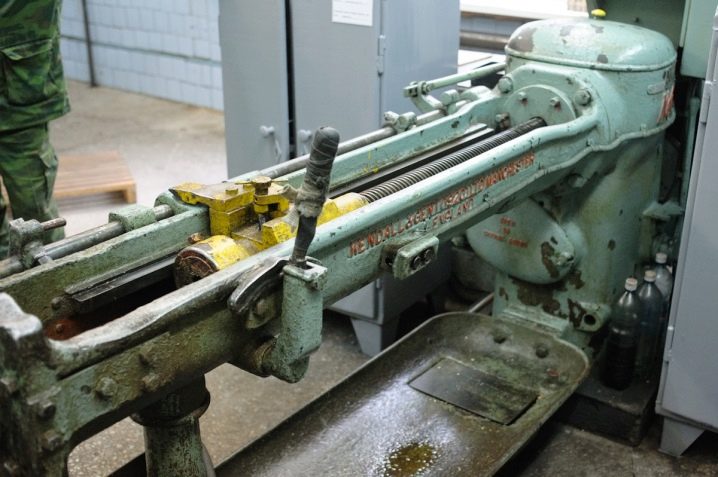
Vertical
It is believed that the main purpose of such machines is the processing of external surfaces with a broach. They are especially stable when working. The slides rest on the bed and therefore do not tip over. It becomes possible to remove allowances up to 0.4 - 0.5 cm. In general, vertical broaching equipment operates in a semi-automatic mode; operators only need to set parts in position and remove it after completing metal manipulation.
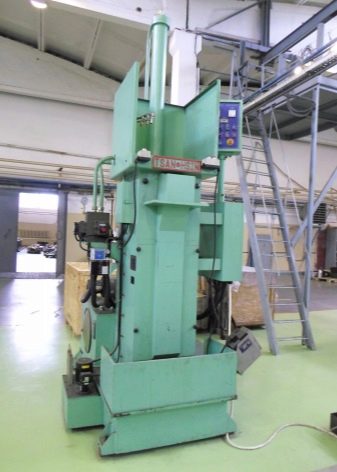
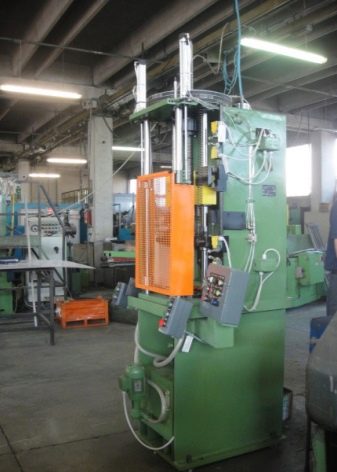
With and without CNC
For mass production of small parts, continuous processing is the best choice. Best of all, it is carried out using carousel broaching or tunnel broaching machines.... Equipment for foam reinforcement is also allocated to a separate group. It is represented by a fairly large number of models. Such machines usually apply an elastic plaster layer; they can feed the workpiece at a variable speed.
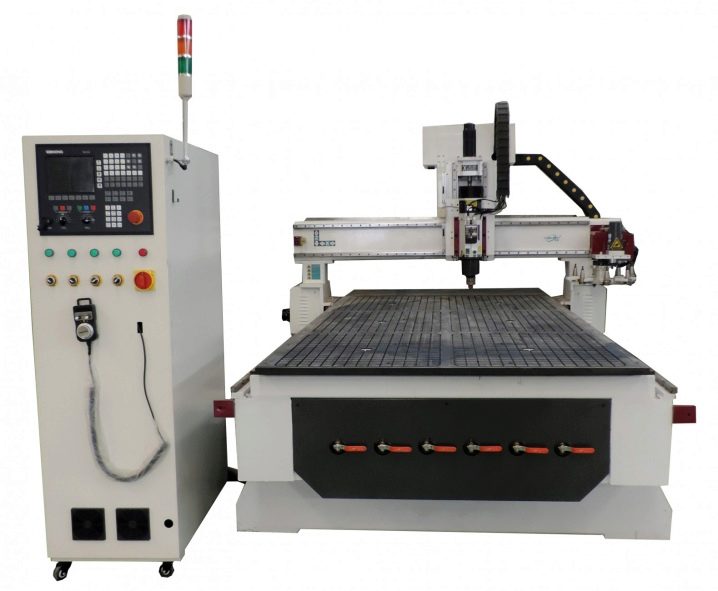
The length of the workpieces to be processed is usually not limited. However, the reservoir capacity for the composition to be applied may be the limiting factor. Other important practical characteristics are:
-
length of workpieces;
-
the size of the conveyor belt;
-
the size of the machine itself;
-
features of the mains power supply;
-
power consumption;
-
possibility or impossibility of continuous operation.
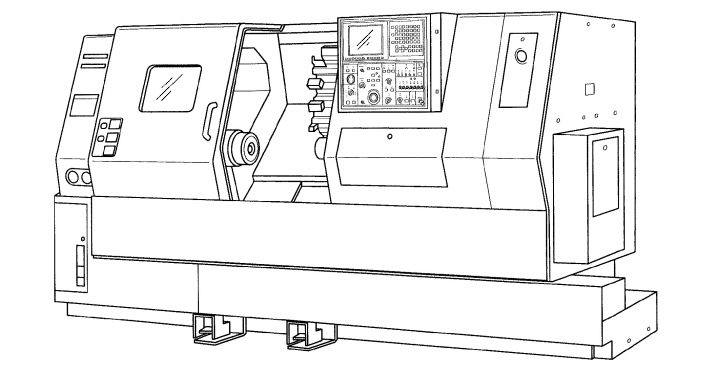
Reinforcement is possible with putties of any composition. But this requires that they have good adhesion to the foam. The design is calculated for the uniformity and uniformity of the applied layer. Similar machines work with platbands, cornices, moldings and so on. A well-designed pusher belt prevents parts from slipping.
Pressure rollers often have inflatable chambers. This minimizes pressure on the surface of the workpiece.
The pressure roller can change the angle at which the pressure is applied, which allows it to adapt to any kind of workpiece relief.
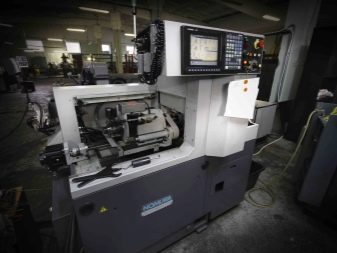
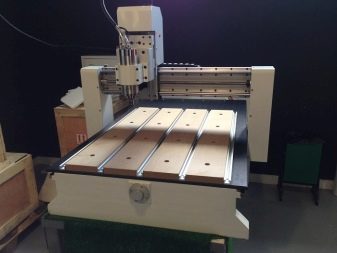
The technical table used for loading and pulling is a product based on a metal frame with a pair of shafts. It is on these shafts that the studded tape is pulled. A gear motor is placed in the side part. A frequency converter is provided that affects the rate of movement and its direction. The receiving tables are created from a base and a pair of pipes with adjustable mounting width.
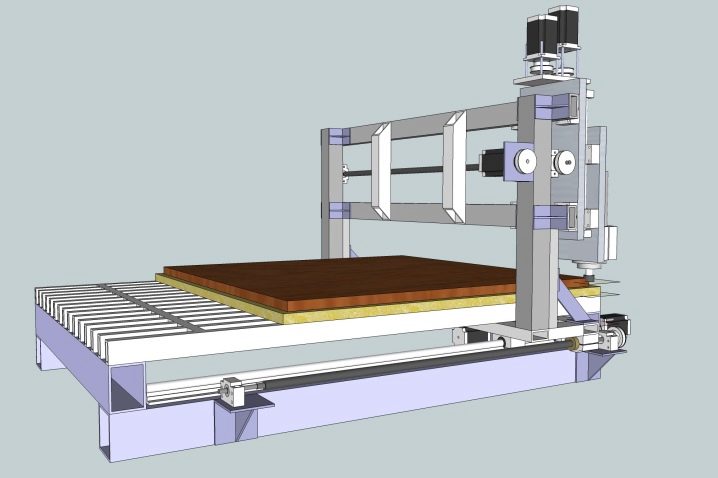
CNC systems are mainly equipped with high-performance vertical broaching machines. Usually, it is possible to replace standard controllers with those that are needed on an individual order. Some CNC systems are optimized for the production of internal splines and keyways. Designers make sure that the programming interface allows manipulation of both the tools used and the workpiece.
As for the grinder machines with a broach, this is almost always home-made equipment - but in a number of situations, however, not particularly inferior to the factory versions.
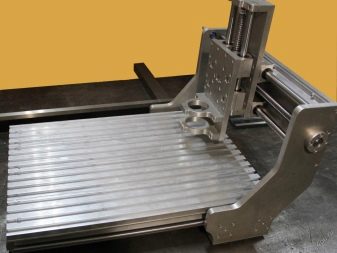
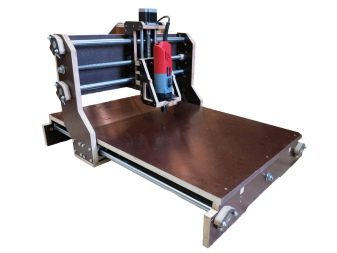
Popular models
However, in most cases it is preferable to use a factory broaching machine. It will be designed by professional engineers taking into account a large number of subtleties and nuances. Among the horizontal apparatuses, the model 7B55 produced in Minsk deserves attention. It is suitable for manipulating interior surfaces of various shapes and sizes. By default, this is a semi-automatic, but if necessary, you can add a CNC for maximum automation.
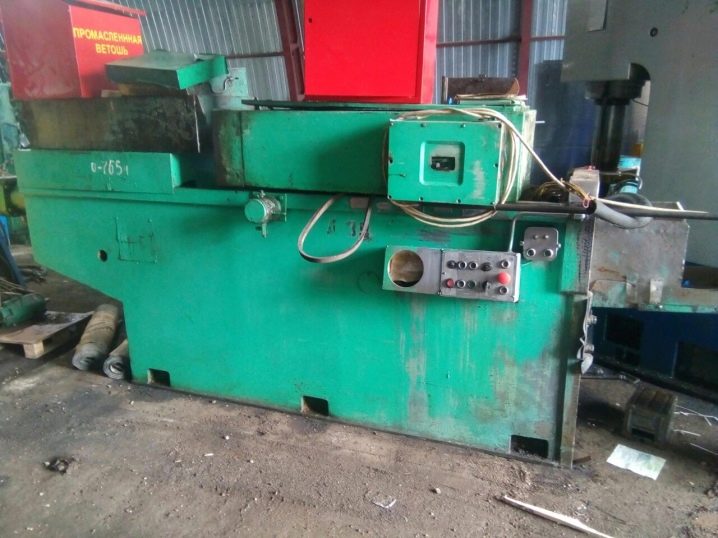
The hydraulic unit is equipped with a pair of high pressure pumps. The functional stroke of the machine reaches 160 cm. It is capable of pulling workpieces at a speed of at least 1.5 and no more than 11.5 m in 60 seconds. In reverse motion, these speeds will be 20 and 25 m, respectively.The electrical circuit has been optimized for maximum reliability and the oil in the hydraulic system is filtered.
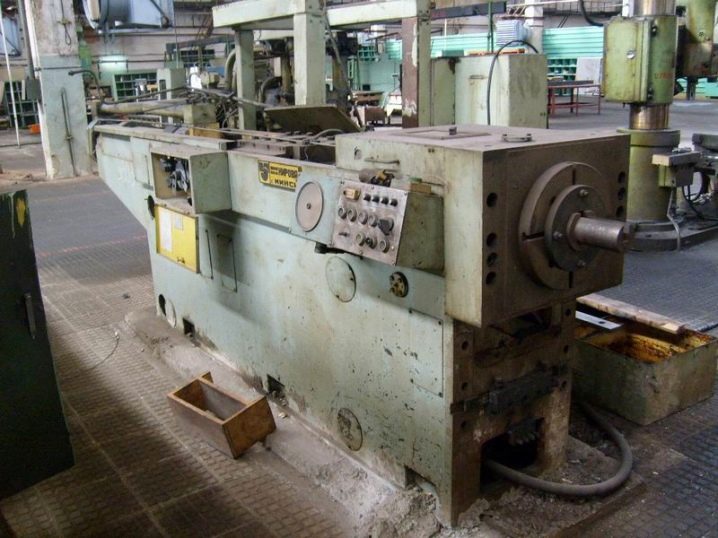
The same Minsk machine-tool company supplies model 7523. It differs in:
-
axial piston pumps in the hydraulic system;
-
semi-automatic execution scheme;
-
cycle counter;
-
double filtration of working fluids;
-
renewal of the electrical part;
-
placing drives inside metal boxes.
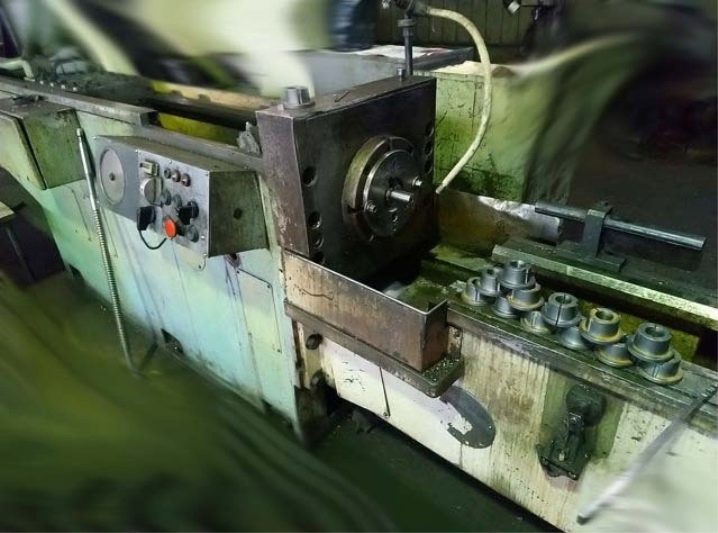
From foreign firms it is worth taking a closer look at HOFFMANN Raumtechnik. This company produces, along with traditional vertical, horizontal - also specialized machines. RAWX-M ruler optimized for final machining of grooves and serrated joints. RASA-M series suitable for handling ball grooves of all couplings. Other firms are unlikely to offer products comparable to those of the market leaders.
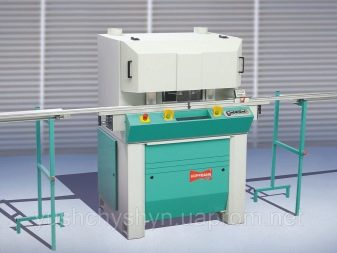
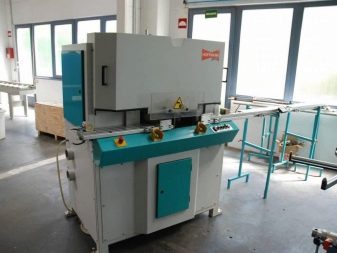
Components
Broaching machines require a variety of attachments. Along with the already mentioned CNC complexes and rotary tables, measuring devices deserve attention. They allow you to guarantee the accuracy of the maintained dimensions. Additionally, you may need:
-
drive equipment devices;
-
turrets;
-
backup power supplies;
-
complexes for supplying lubricating and cooling liquid;
-
air filtration units;
-
devices for the removal of shavings;
-
feed systems for bars and sheets;
-
pumps;
-
specialized software (in CNC systems).
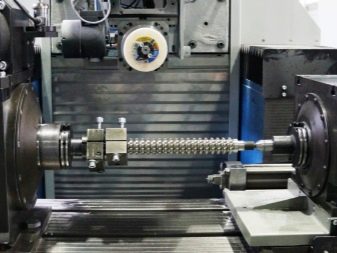
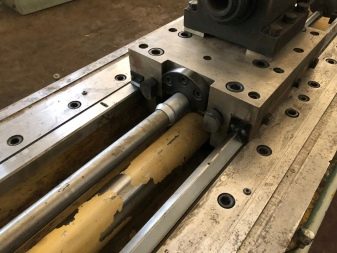
Exploitation
For any work performed, it is required to comply with safety measures. All machines may only be operated with protective covers that are in good working order and comply with the standards. Vertical devices can only be used with brackets. Such guards will allow you to catch the broach if it falls out of the chuck. Parts are introduced into the processing area and removed from there only when the device is turned off, when all the working parts are in their original position.
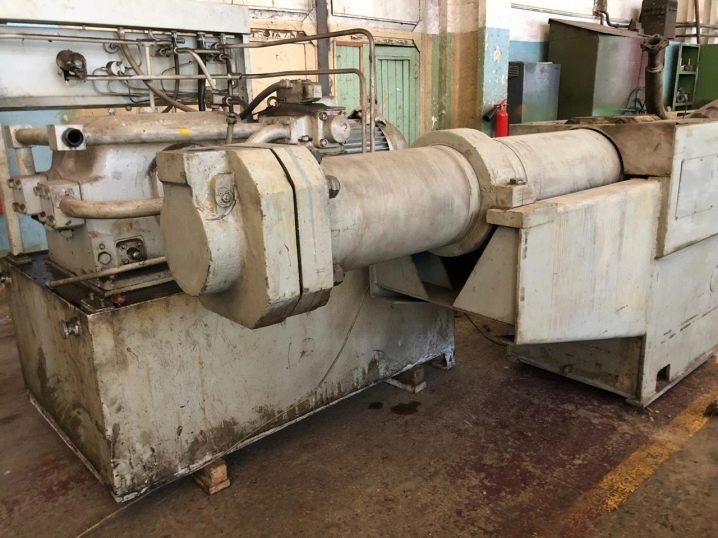
Likewise, do not clean tools that are not de-energized or reset. Working with long broaches on a horizontal broaching machine requires the use of a movable steady rest. In the event of a malfunction of the machine as a whole or any part of it, the device is immediately stopped and reported to the foremen or the technical assistance service.... When processing flat surfaces and other manipulations, it is necessary to carefully monitor whether the functioning of the hydraulic drive is not disturbed.
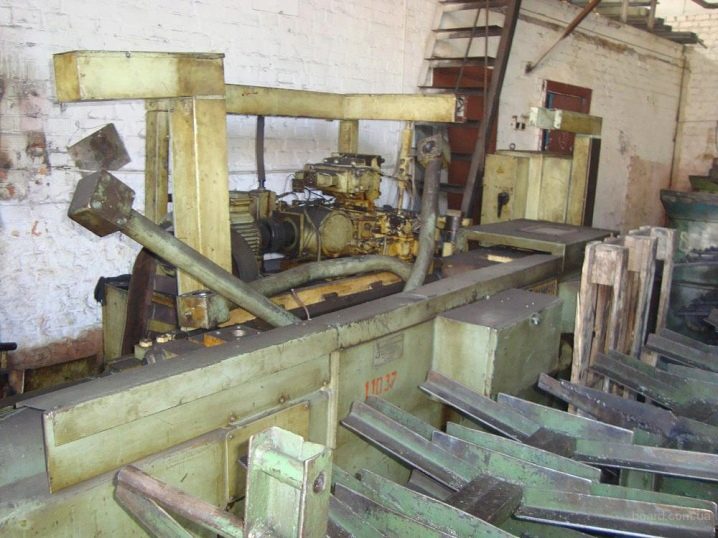
Problems with it can be caused by air ingress and oil clogging. The amount of broaching used is determined by the length of the workpieces and the allowance. It is also influenced by the chosen cutting pattern and the method of surface preparation. The workpiece, which is placed on a support in the form of a sphere, is itself positioned along the broach axis. However, it is necessary to additionally check whether the end part is perpendicular to the axis of the hole; if this condition is not met, the butt end should be modified in an additional operation.
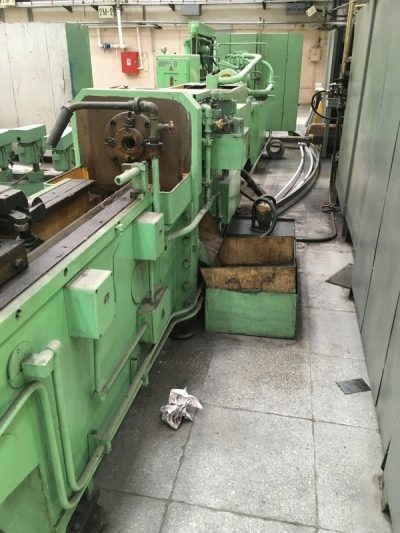
This is not a problem with flat stands. But on the other hand, the difference in diameter allowances can lead to breakage of the broach. For multi-faceted holes, multi-faceted holes are needed, and for complex shaped surfaces, circular broaches. The stock cutting scheme is selected taking into account its value.
If straight splines are to be cut, a major linear motion is required; helical splines are formed with additional movement, otherwise the process will go wrong.
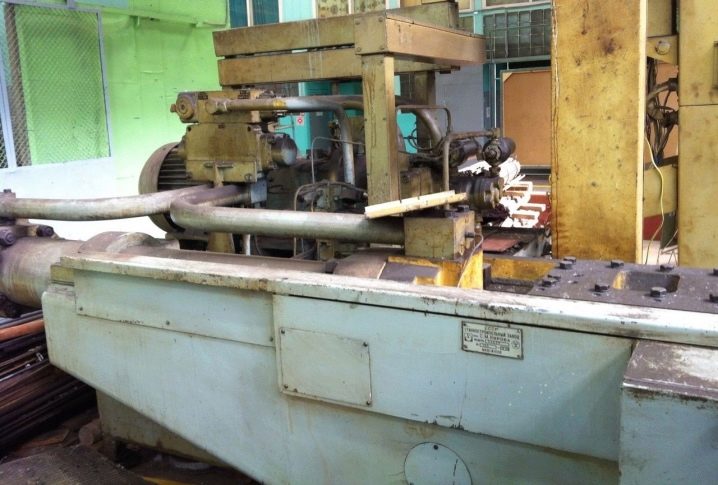
The comment was sent successfully.